锂离子电池作为新能源领域的核心组件,其封装工艺直接影响电池的安全性、能量密度及使用寿命。U型包膜与回型包膜是方形动力电池主流的两种封装方式,本文从技术原理、工艺流程、性能对比及发展趋势等方面系统分析两种技术的特点,并结合铝塑复合膜材料创新与设备兼容性优化,探讨未来发展方向。
一、引言
锂离子电池封装膜的主要功能包括绝缘保护、防尘防水及机械防护。根据市场统计,软包电池中铝塑复合膜(铝塑膜)的应用占比超过60%。方形硬壳电池则多采用PET绝缘膜或蓝膜,其封装方式以U型与回型为主。两者在工艺复杂性、材料利用率及良品率方面存在显著差异,直接影响生产效率和成本控制。本文结合专利技术与行业实践,对两种封装模式进行深度解析。
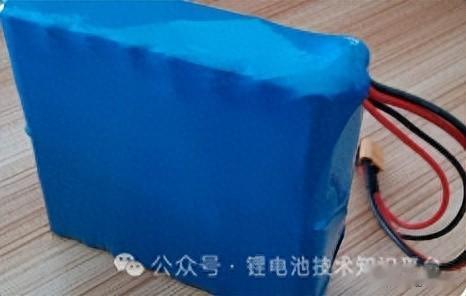
二、技术原理与工艺流程
1. U型包膜
定义:从电池底部开始包裹绝缘膜,依次覆盖底部、两个大面,最后通过侧面折边完成封装。
核心步骤:
1. 底部贴膜:贴膜胶辊将绝缘膜贴敷于电池底部,确保无气泡;
2. 大面包覆:上下胶辊同步动作,将膜延展至电池上下表面;
3. 侧面折边:通过导向斜面或辊压结构对侧边进行45°折角处理,再完成90°弯折贴合,减少褶皱。
技术难点:侧边折角处易因膜层重叠导致厚度增加(可达3层以上),影响电池能量密度;若折角精度不足,易出现气泡或撕裂,良品率通常低于80%。
2. 回型包膜
定义:以环形路径包裹电池,依次覆盖两个大面、两侧面及底部,最后通过顶部折边收口。
核心步骤:
1. 大面与侧面包膜:绝缘膜一次性覆盖电池四个侧面;
2. 底部折边:通过短边辊压组件对底部边缘进行精密折弯;
3. 顶部封口:利用热压或结构胶固定顶部边缘,确保密封性。
技术难点:底部裸露区域需额外贴附绝缘片,存在脱落风险,可能引发短路;对设备定位精度要求极高,否则易出现折边错位。
三、性能对比与适用场景
1. 结构特性对比
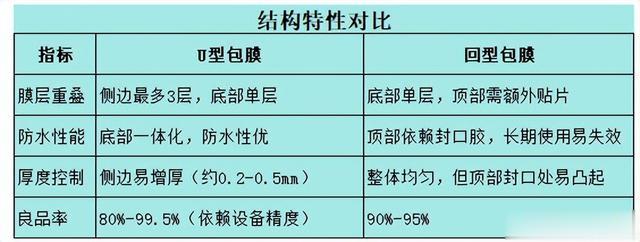
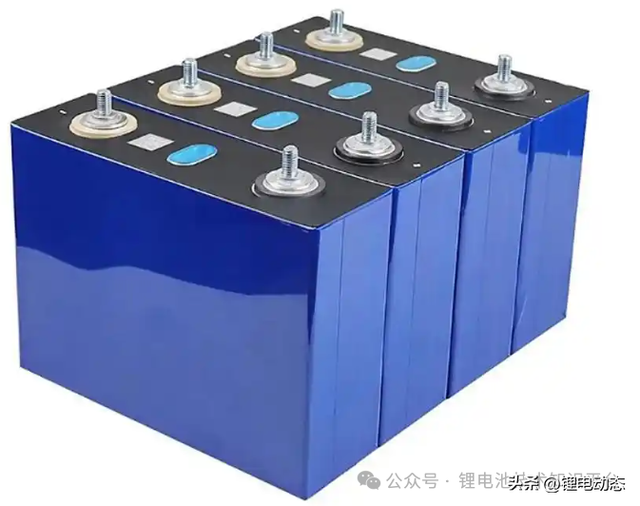
2. 应用场景
U型包膜:适用于对底部防水要求高的场景(如新能源汽车电池模组),通过改良折边工艺(如45°导引斜面设计)可将良品率提升至99.5%。
回型包膜:多用于3C领域,因其工艺简单且成本较低,但对环境密封性要求不高的场景。
四、技术挑战与创新方向
1. 材料创新
铝塑复合膜:主流厚度为86-153μm,由尼龙层、铝层及CPP树脂层复合而成。国产化率从2016年的不足5%提升至目前的30%,但仍需突破耐电解液腐蚀技术。
高粘接性蓝膜:通过优化胶层配方(如添加硅酮改性材料),可减少折边时的膜层剥离风险。
2. 设备兼容性优化
专利技术显示,兼容U型与回型包膜的设备可通过模块化设计实现快速切换:
关键组件:包括可移动式辊压模块(如右/左辊侧胶组件)、自适应定位夹具(电池定位夹紧组件)及智能切膜系统(右/左切胶装配体);
切换逻辑:通过伺服模组调整工位路径,U型模式下跳过底部短边包覆步骤,直接进入侧边同步辊压。
3. 工艺改进
动态折边技术:采用电池移动与折边同步进行的伺服模组,避免静态折边导致的膜张力不均问题;
激光辅助贴合:在折边区域预涂热熔胶,通过激光局部加热提升贴合强度,减少气泡。
五、发展趋势
1. 高精度一体化设备:通过集成视觉检测与AI算法,实现包膜厚度在线监测与工艺参数自适应调整,目标将综合良品率提升至99.9%。
2. 轻量化膜材料:开发超薄(≤80μm)铝塑膜,在保持阻隔性能的同时降低电池重量,助力能量密度突破300Wh/kg。
3. 固态电池适配封装:针对全固态电池无电解液的特点,开发无需防腐蚀层的简化包膜工艺,进一步降低成本。
六、结论
U型与回型包膜各有其技术优势与局限性,未来发展方向将聚焦于材料性能优化、设备智能化及工艺标准化。通过兼容性设计(如专利CN112208830A所述装置),企业可灵活应对多元化需求,同时降低设备投入与维护成本。随着铝塑膜国产化进程加速及固态电池技术成熟,锂离子电池封装技术将向高效、高可靠性与低成本方向持续演进。
文章来源:锂电池技术知识平台
注:本站转载的文章大部分收集于互联网,文章版权归原作者及原出处所有。文中观点仅供分享交流,不代表本站立场以及对其内容负责,如涉及版权等问题,请您告知,我将及时处理。