我用70的厚壁钢管试车成功了,和原先的模具截面形状完全一样。说来惭愧,为了这套模具,我已经折腾了快两个星期了。
期间也断断续续搞点线切割,别的杂件,但是就这套模具令我头痛不已。
下面容我炫耀一番。
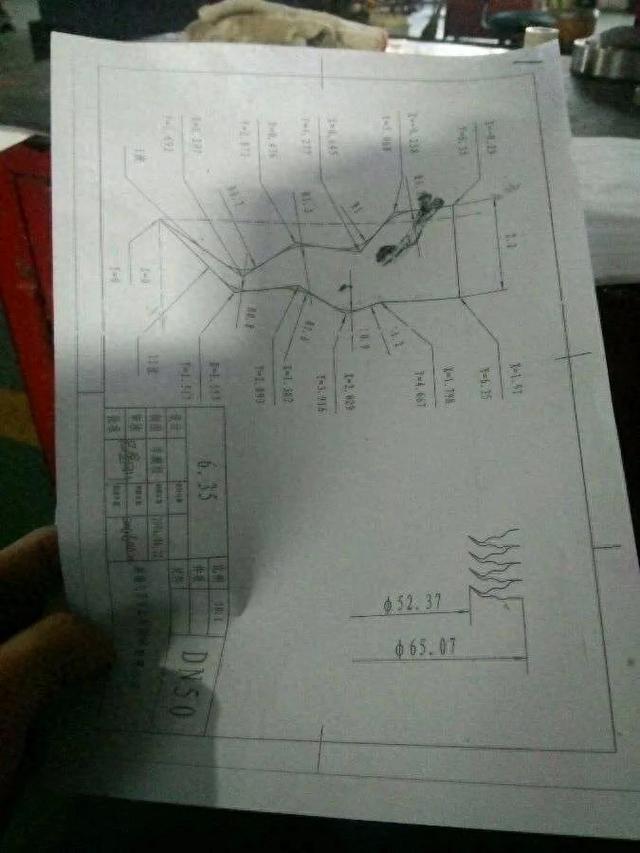
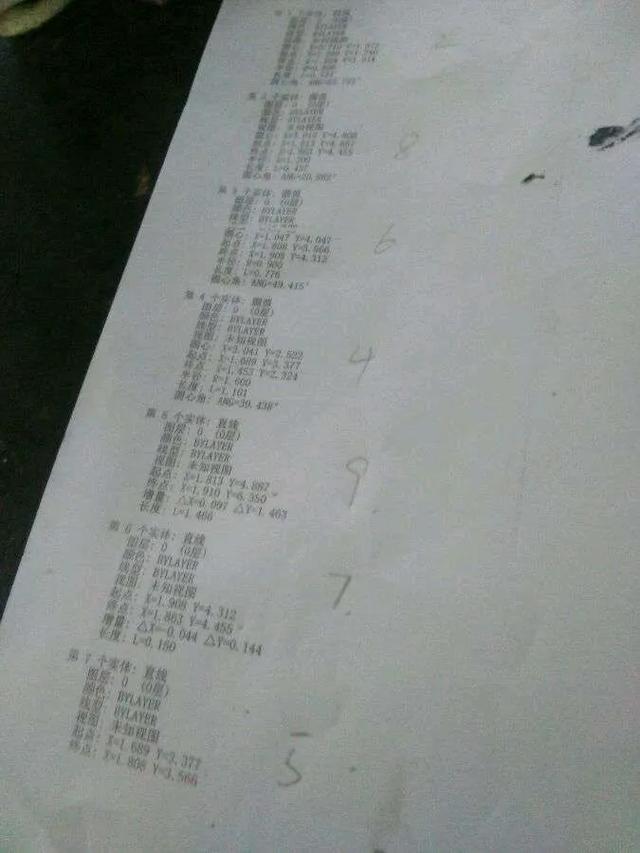
刚开始拿到图纸,一看,一套模具而已嘛!虽然Cr12硬了点,用726刀具还是没什么问题的。
于是,专门做了一把螺纹刀,不过由于是车端面,要横着压。材料到手,图纸到手,刀具是车间领导亲自给我磨的。刀尖角度很小,估计在45到50度之间。
这样的夹角,完全可以避免与模具轮廓干涉。后角也磨的挺大,也是为了避免干涉。为了增加强度,连过度刃都没有磨。拿到领导磨好的刀具,我还仔细用油石研磨了一番。
编程,开车!
这套模具最先是使用厂里的一台马扎克机床车出来的,但是玩那台马扎克的师傅已经辞职了,而且那台马扎克由于很久没有人使用,已经闲置出问题了。
一开机,就显示刀架报警,只能靠现在还在使用的两台沈阳了,顺便吐槽一下,厂里还有一台闲置的后置刀架斜轨西门子系统的宝鸡,自从买来就一直在那里吃灰。原因是用惯发那科系统的各位师傅玩不来西门子。
接着正题说。到了这层,我才想起来有必要再发一次图纸。
说明一下,图纸两条曲线代表的是两套模具的截面轮廓,而且图纸后面附带了两页纸,给出了所有节点的平面坐标。它给出的坐标是x,y,与我机床用的坐标方向不一样不说,还需要换算。
所以,第一步,就是根据这些节点坐标,算出机床加工用的工件坐标。真麻烦。要不是怕装,我就直接用电子表格代替手算了。
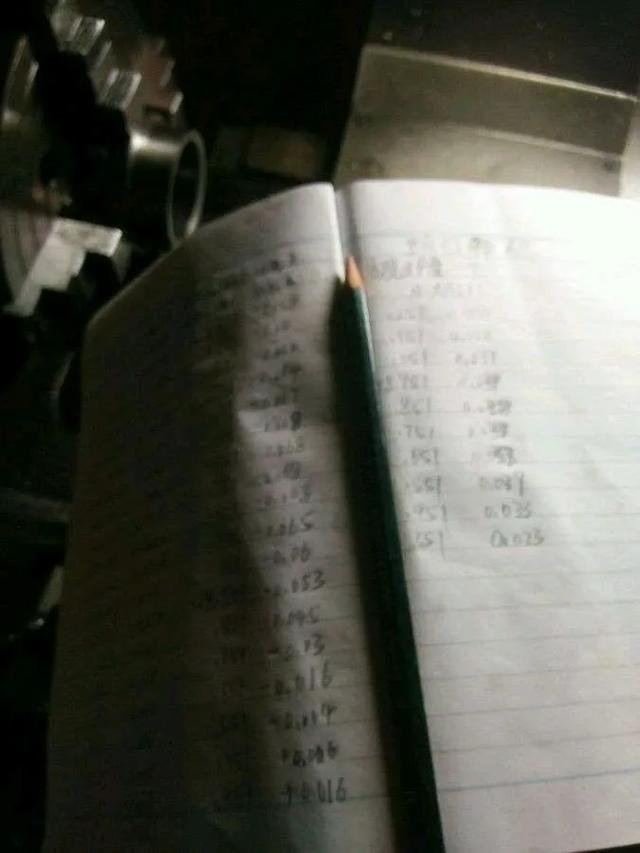
这时候,我用领导计算好的坐标给的开始编制程序,然后领导去帮我磨刀。我程序写完了,他把刀具也磨好了,然后我就开始装刀,对刀,开车。
车完之后,我感觉就不对,和原先的模具对不上。
从内外径看,吻合的挺好,但是送到冲床那里,人家一看,你这个不行。这样冲出来的产品不合格,说形状不对,你的圆弧没挖到位。
领导出主意,说你把圆弧全部分两段,意思就是给机床指定圆弧的最高最低点。我说一样呀,命令里给出了起点,终点,半径,圆弧的形状就完全确定了呀,领导摇摇头,说确定不了,你再把刀子磨利点,然后他又把图纸拿走了,去电脑上拉最高点最低点坐标去了。
我反正也没别的活,就跟着他折腾吧。我就去磨刀子,万一领导的猜测是对的呢?但是经过一上午反复折腾,证明了领导的猜测也不对,下午领导不见,不知道去哪里忙活去了。那时候我也一筹莫展了。于是,又丢下不管了。
完事闲了,领导又催我车那套模具,我说我也没招了啊,程序我仔细检查过,刀子你也磨了好几次,但是车出来的东西就是不合格,怎么办?我也没招啊。(吐槽一下,我学数控才一个月而已,一个月。)领导说那也得车啊,再把它夹上,再换个程序。 反正我又处于没活状态,领导说怎么办咱就怎么办。这时候,领导问我,你这床子,哪样是03,哪样02?我说顺时针03,逆时针02。他说你把03/02换下。
我抱着反正我自己也折腾不出来的想法,继续折腾,陪着领导折腾一遍,领导说换回来吧。(只能在心底苦笑)。折腾一上午之后,再次证明这些都没用。
到了隔日,这模具到我手上的第n天,我开始怀疑刀具。
刚开始,我只想着刀子磨的肯定没问题。但是如果改变走刀路线呢?原先我只是按照领导说的角度安装,从内孔车到外圆。我改变了刀具的安装角度,试车一次,发现稍稍有些好转,但是只是看起来而已。和与之配合的模具一匹配,发现还是不行。改变走刀路线,从外圆车到内孔,还是不行!
疯了,真的疯了,那时候我已经是第n次感觉到无力了。但是这东西就是我的,车出来也得车,车不出来,还得车。这哪是赶鸭子上架,明明是赶已经技穷的黔驴上架啊!
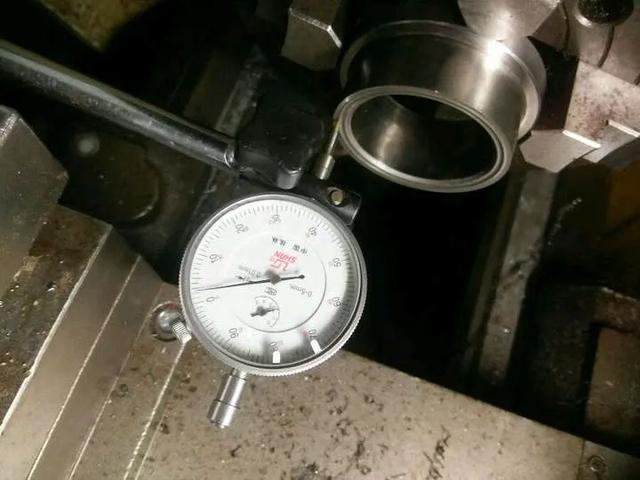
这时,下道工序的师傅也急了,说她领导整天批评她,她告诉她领导,说模具没有修好,可是她领导说你去催呀,不催人家能给你快快修吗?
我对她说,我已经绞尽脑汁的在想办法了,可是就是加工不出来。她说问你领导啊,我说我领导天天在给我出主意,想办法呢。她也一脸无奈,“我要懂就自己车了”我又一脸郁闷,“我教你呗”她说,“你快得了吧,继续想办法车吧”
其实我从一开始就有两个疑点:原先加工出来的模具,真的和图纸完全吻合吗?带着这个疑点,和整天被怀疑的心情,我晚上痛下苦功,用了两个小时测绘出了一大堆坐标。
你们一定想问,坐标哪来的?
如上的图,我把百分表固定在刀架上,使百分表与模具端面完全重合,然后手摇进刀,每次只进10个丝,也就是刀架每次只移动5个丝,然后记录下机床x坐标和百分表读数,估读到0.1丝。
就这样,模具单边厚度6.35毫米,也记录下了100多组坐标,经过电脑处理之后,得到了实际测绘出的模具图纸。经过比对,发现给我的图纸没有问题,实际测绘得到的图,和用图纸画出的图,惊人的吻合。
那么图纸没问题,问题只能出在加工环节。
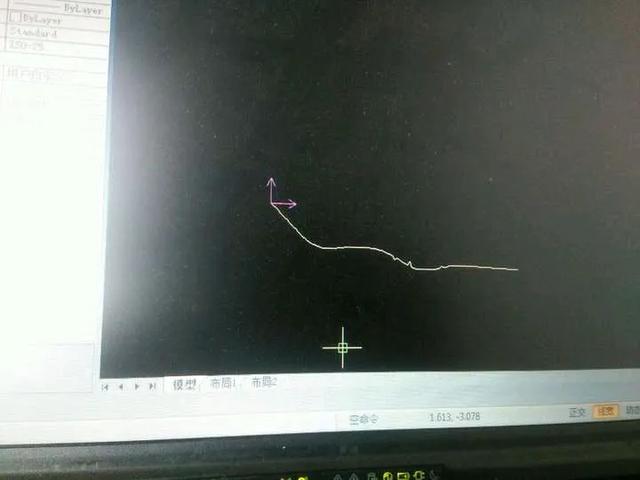
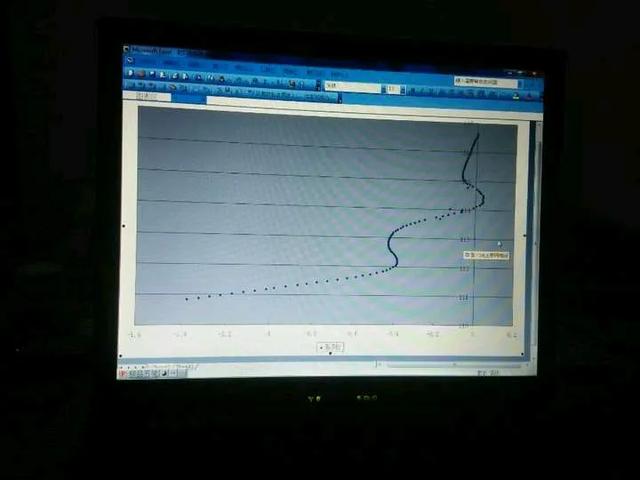
加工环节,程序本身的问题是不可能的。而刀具,更不可能。我干数控之前的工作,就是专业挖薄板,3个厚的薄板,最小我挖过内孔37的。
刀具后面有一点点干涉都不可能挖进去。那么问题只能出在工艺安排上。
我突然想到一种可能,就是丝杠的间隙。由于刀子要沿着z向反复移动,所以,丝杠间隙的影响不可忽略,想到这一点,我顿时兴奋起来了。
还是用一把刀加工。但是,建立两组刀补,刀补的z向值相同,而分别建立两个不同的x刀补参数。
一个是由外圆向内孔车削之后,量取外圆确定。而另一个x向刀补是由内孔向外圆车削端面,量取留下的内孔台阶来确定。工艺安排是,永远让刀具向着z值减小的方向移动。
也就是说,刀具定位到某段的最高点,然后向着最低点车,到达最低之后,快速定位到下一个最高点,再向着最低点车。从内孔开始,这样单段车出来,换刀补不换刀,再从外圆车到内孔。顺着这个思路重新编制了程序,然后再次开车了。
经过俩小时奋战,不断调整刀补,成了!哈哈哈。
最终的结论就是,问题正是出在丝杠间隙上面。干普车的都知道,如果对刀时摇过了头,那么只有反转摇过间隙之后,才能重新进刀。
有些床子,甚至重复定位精度都不够,只能向着一个方向进刀,试车,测量,再进刀。如果你摇过头,那你只有重新试车,再测量了。