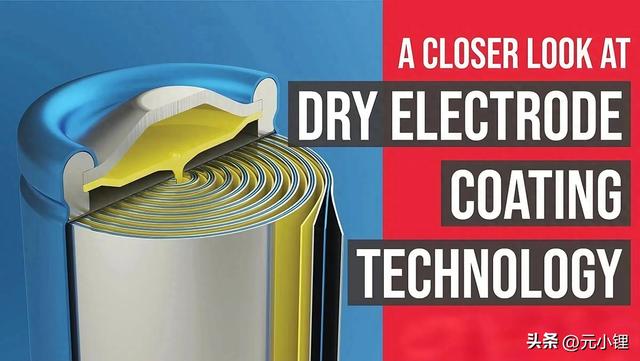
在3月20日举行了一次员工内部吹风会上,特斯拉罕见地公开了许多新的技术内容。身高173cm,体重56.6公斤,手部自由度22个的Optimus人形机器人已经在佛罗蒙德产线上工作了。这条产线正是去年四季度被改造成生产双干法4680 D电芯的全新产线。
Optimus的应用,使得佛罗蒙德的这条生产线成为世界上第一条使用人形机器人代替部分人工的锂电生产线,主要是降低成本。拥有AI学习能力的人形机器人在生产上的威力一旦发挥出来,那中国的人力成本优势将荡然无存。
特斯拉双干法4680电芯的关键技术点双干法指的是干电极工艺和干法涂布,这两个工艺如何结合,解决了比如成本、能量密度、生产效率等。同时特斯拉采用这种技术后的产能提升情况,以及对其他电池生产商的压力。
特斯拉双干法4680电芯:锂电行业的颠覆性革命在全球能源转型的浪潮中,特斯拉双干法4680电芯的即将量产犹如一记惊雷,在锂电行业引发强烈震动。这款采用革命性干电极工艺和干法涂布技术的圆柱电池,不仅标志着特斯拉电池技术路线的重大突破,更预示着整个锂电制造体系将迎来根本性变革。根据特斯拉2023年Q4财报披露,其德州超级工厂的4680电芯周产能已突破100万颗,配套的Cybertruck量产速度正在快速爬升,这标志着历时三年的技术攻关终于进入产业化收获期。
一、双干法工艺的技术突破在传统湿法电极工艺中,活性材料需要与有毒溶剂NMP混合形成浆料,经过涂布、烘干、辊压等多道工序。特斯拉的干电极技术彻底摒弃了这一流程,通过将正负极材料与特制粘结剂PTFE混合,在高压作用下直接形成自支撑电极薄膜。这种工艺创新使得电极制备工序从12道缩减至3道,生产能耗降低70%,车间面积需求减少90%。更关键的是,干法工艺允许使用更高比例的硅基负极(硅含量可达35%),相比传统石墨负极,理论容量提升达10倍。
干法涂布技术的突破同样令人瞩目。传统湿法涂布需要精确控制浆料粘度、固含量等参数,干燥过程容易产生应力裂纹。特斯拉采用静电喷涂技术,使干燥的活性材料粉末在电场作用下定向沉积,形成厚度仅80μm的均匀涂层,较湿法工艺减薄30%。这种超薄电极结构使锂离子扩散路径缩短40%,配合无极耳设计,实现了充电速度提升50%的惊人突破。美国阿贡国家实验室测试数据显示,4680电芯在15分钟内即可完成10-80%SOC快充。
材料体系创新是双干法工艺的另一核心。正极采用高镍NCM 811与单晶化处理技术,搭配LiFSI新型锂盐电解液,循环寿命突破2000次仍保持80%容量。负极方面,特斯拉开发了"核壳结构"硅碳复合材料,通过碳层包覆缓解硅的体积膨胀,膨胀率控制在8%以内。这种材料创新使能量密度达到300Wh/kg,较21700电芯提升16%,且成本下降14%。
二、产业生态的链式反应特斯拉自建电池帝国的战略在4680电芯上体现得淋漓尽致。内华达州的Terafactory规划年产能达100GWh,采用全流程垂直整合模式:从魁北克的锂矿开采,到德克萨斯州的负极石墨纯化,再到自研的4680全自动产线。这种闭环供应链使特斯拉将电芯成本压缩至$70/kWh,较采购第三方电池节省22%成本。更关键的是,产能自主权使其免受2023年锂电池价格暴涨65%的市场冲击。
设备制造领域掀起革新浪潮。德国MANZ公司开发的干法电极设备,采用等离子体表面处理技术,使PTFE纤维化程度提升至95%,薄膜抗拉强度达15MPa。涂布环节的静电喷涂系统由美国Applied Materials定制开发,配备2560个微孔喷嘴,定位精度达到±2μm,生产速度提升至60m/min。这些专用设备的研发投入已超$5亿,构建起特斯拉独有的技术护城河。
供应链重构正在加速。传统隔膜厂商面临颠覆风险,特斯拉的无钴化正极使华友钴业股价单月下挫18%。而在硅基负极领域,中国贝特瑞凭借核壳结构专利,斩获特斯拉三年长单。电解液方面,新宙邦的LiFSI产能被提前锁定至2025年。这种供应链洗牌正在重塑全球锂电产业格局,据彭博新能源财经预测,到2030年干法工艺将占据35%的锂电池产能。
三、市场格局的重构风暴成本优势正在改写游戏规则。特斯拉通过干法工艺将每kWh制造成本降至68,比宁德时代CTP3.0电池低68,比宁德时代CTP3.0电池低12。配合一体化压铸车身技术,Model Y的电池包成本占比从30%降至22%。这种成本优势直接转化为产品竞争力,搭载4680电池的Standard Range版Model Y售价有望下探至$35,000,对大众ID.4等竞品形成降维打击。
技术标准之争日趋白热化。特斯拉开放4680设计标准,吸引松下、LG新能源加入生产阵营,但核心的干法工艺设备仍由自研团队掌控。这种"开放架构+核心技术封闭"的策略,与苹果iOS生态异曲同工。反观宁德时代推出的麒麟电池,虽然体积利用率达72%,但依赖传统湿法工艺,在成本迭代空间上已显疲态。韩国SNE Research预测,到2025年4680电池将占据全球动力电池25%的市场份额。
应用场景正在裂变拓展。除电动汽车外,特斯拉将4680电芯导入Powerwall储能系统,循环寿命可达8000次,度电成本降至$0.07。在航空领域,SpaceX正在测试4680电芯驱动的电动涵道风扇,为电动垂直起降飞行器提供动力。更令人瞩目的是,特斯拉机器人Optimus Gen 2已采用4680电芯组,能量密度提升使其连续工作时间延长至8小时。这种多场景渗透正在构建特斯拉的能源生态系统。
站在技术革命的临界点,特斯拉双干法4680电芯带来的不仅是产品迭代,更是整个锂电产业的价值链重构。当传统玩家还在为5%的能量密度提升绞尽脑汁时,特斯拉已经用革命性工艺实现了成本、性能、效率的跃迁。这场变革的涟漪效应正在扩散:材料体系革新催生新的供应巨头,制造设备更替孕育千亿级市场,应用场景拓展打开十倍增长空间。对于锂电开发者而言,这既是颠覆的危机,更是重构游戏规则的机遇。未来五年,能否在干法工艺、硅基负极、固态电解质等关键领域建立技术储备,将决定企业在新能源时代的生死存亡。
一、干法电极制造工艺1. 材料制备体系原料预混系统采用双行星搅拌机(转速800-1200rpm),将正极材料(NCM811/NCA)、导电剂(CNT/VGCF)、粘结剂PTFE按89:5:6比例预混合。PTFE以纤维状形态存在,长度控制在50-100μm,直径0.2-0.5μm。混料温度严格保持在25±2℃,湿度<5%RH,防止PTFE提前纤维化。纤维化处理通过高速剪切设备(转速3000-5000rpm)对混合粉末进行机械活化。剪切过程中PTFE分子链沿剪切方向展开,形成三维网状结构。关键控制参数:剪切时间30-60秒,温度≤40℃,纤维化程度需达到90%以上。纤维化后的混合料呈现蓬松絮状结构,堆积密度从1.2g/cm³降至0.5g/cm³。造粒成型使用对辊压延机(压力10-15MPa)将混合料压制成厚度0.5-1mm的连续带状前驱体。此阶段需精确控制辊间距(±5μm),确保材料内部PTFE纤维均匀分布。压延后的带状材料孔隙率控制在35%-40%,抗拉强度≥8MPa。2. 电极成膜工艺热压延展带状前驱体进入多级热压机,第一级预热至80-100℃使PTFE软化,第二级在120-150℃、压力50-80MPa下进行延展。通过双向拉伸(MD/TD拉伸比1.5:1),形成厚度80-100μm的自支撑电极膜。拉伸后电极孔隙率降至20%-25%,面密度波动≤±3%。等离子体表面处理采用大气压等离子体(氩气/氧气混合气体)对电极表面进行活化处理。处理功率2-5kW,处理时间30-60秒,使电极表面氧含量从0.5%提升至8%-10%,改善电解液浸润性。处理后接触角从110°降至15°,电解液渗透时间缩短至5秒以内。二、干法涂布与集流体复合1. 静电喷涂技术粉末带电处理活性材料粉末(如硅碳复合材料)通过电晕放电装置(电压30-50kV)带电,使颗粒表面电荷密度达到10-15μC/g。带电粉末在电场中沿电力线定向运动,沉积精度±2μm。图案化沉积采用2560孔静电喷头阵列,通过掩膜板控制沉积区域。喷涂速度60m/min,涂层厚度50-80μm,面密度偏差≤±1.5%。特斯拉专利显示,该技术可将边缘过渡区宽度从传统湿法的3mm压缩至0.5mm,材料利用率提升至98%。2. 集流体复合工艺超声波焊接铝箔(正极)/铜箔(负极)与干法电极通过超声波焊接复合。焊接频率20kHz,振幅30-50μm,焊接时间0.1-0.3秒。界面结合力≥1.5N/mm,较传统涂布工艺提升50%。原位固化复合后的电极在120-150℃、氮气环境下进行热固化,使PTFE纤维网络与集流体形成化学键合。固化后电极剥离强度≥0.8N/mm,卷曲半径可达到3mm(传统工艺需≥8mm)。三、电芯组装核心技术1. 无极耳(Tabless)设计激光刻蚀导电路径采用皮秒激光(波长355nm)在集流体边缘刻蚀出宽度0.2mm、深度15μm的微槽,形成连续导电通道。导电路径密度达120条/cm,使电子传输距离从传统极耳的150mm缩短至0.5mm。三维集流结构通过磁控溅射在电极两端沉积5-8μm厚的铜/铝镀层,构建三维集流网络。该结构使内阻从传统电芯的2.5mΩ降至0.8mΩ,热扩散系数提升3倍。2. 全极耳卷绕工艺张力精准控制卷绕过程中采用磁悬浮张力控制系统,将箔材张力波动控制在±0.05N以内。卷绕速度提升至15m/s,较传统工艺快3倍,同时对齐精度达±0.1mm。原位固化电解液注入含1% AIBN引发剂的凝胶电解液(LiFSI基),在80℃下引发原位聚合,形成三维交联网络。固化后电解液离子电导率达8mS/cm,机械强度提升至5MPa,有效抑制硅负极膨胀。四、关键工艺设备创新干法电极生产线德国KraussMaffei定制化双螺杆挤出机:产能500kg/h,能耗仅传统搅拌机的30%美国3M等离子体处理系统:处理宽度达800mm,功率波动≤±1%静电喷涂系统瑞士ABB高精度机械臂:重复定位精度±2μm,配合2560孔喷头实现多材料共沉积在线厚度检测仪:采用β射线+激光干涉双重测量,分辨率达0.1μm全自动卷绕机日本平田机工磁悬浮卷绕头:转速3000rpm,动态平衡精度G0.4级红外热成像系统:实时监控卷芯温度场,温差控制≤±1℃五、工艺难点与突破PTFE纤维化控制突破点:开发剪切应力-温度耦合模型,实现纤维长度CV值<5%难点:过度剪切会导致PTFE分子链断裂,丧失粘结性能干法涂布均匀性突破点:引入电场-气流协同控制算法,面密度波动≤±1.5%难点:粉末团聚导致局部厚度异常硅负极膨胀抑制突破点:核壳结构设计(碳包覆层厚度10-20nm)+ 三维铜集流网络难点:循环过程中界面应力累积导致结构坍塌六、与传统工艺对比工艺环节
传统湿法工艺
特斯拉双干法工艺
优势提升
电极制备
12道工序,使用NMP溶剂
3道工序,零溶剂
能耗↓70%,车间面积↓90%
涂布速度
20-30m/min
60m/min
效率提升3倍
干燥能耗
需120℃×100m烘箱
无需干燥
节省100%干燥能耗
材料利用率
85%-90%
98%
成本降低$5/kWh
电极厚度
120-150μm
80-100μm
能量密度↑16%
环境排放
VOC排放>5000ppm
零VOC排放
环保合规成本降为0
七、产业化挑战设备投资强度高干法电极生产线单GWh投资达$1.2亿,是湿法工艺的2.5倍,投资回收期需5-7年。工艺窗口狭窄PTFE纤维化温度需控制在±2℃,湿度波动容差<±3%RH,对车间环境控制提出极高要求。材料体系重构传统LCO、LFP正极与干法工艺兼容性差,需开发专用高镍单晶材料,研发周期长达3-5年。八、技术演进方向全固态电池集成干法工艺与硫化物固态电解质天然兼容,特斯拉已申请"干法固态电极"专利(US20230378563),目标2030年实现500Wh/kg能量密度。AI工艺优化采用数字孪生技术,通过10万组工艺参数训练神经网络模型,实现电极缺陷率从0.1%降至0.01%。连续化生产开发从原料到电芯的"One-Pass"生产线,目标将生产周期从72小时压缩至8小时。特斯拉双干法4680电芯的工艺革新,本质上是将锂电池制造从"湿化学"时代推进到"干物理"时代。这种变革不仅需要突破材料科学极限,更需重构整个制造体系。对于锂电开发者而言,掌握干法工艺的核心在于理解"材料-设备-工艺"三位一体的协同创新逻辑,这将是未来十年行业竞争的主战场。