绝缘栅双极晶体管(Insulated Gate Bipolar Transistor,IGBT)是新能源转换系统和高压电源开关装置中的关键部件,也是大功率半导体中具有代表性的平台器件,它能大幅提高电机驱动的效率,目前广泛应用于照明、汽车、高铁等领域。它作为新型功率半导体器件的主流器件,无论在工业、 通信、3C电子等传统领域,还是轨道交通、新能源、智能电网、新能源汽车等战略性新兴产业领域,IGBT都发挥着至关重要的作用。
一、 什么是IGBT
1、IGBT的定义
IGBT 也是一种复合全控型电压驱动式功率半导体器件,与MOSFET (绝缘栅型场效应管)结构功能相似,可控制的电压范围更高。
半导体产业 分成四种类型:集成电路,分立器件,传感器和光电子,其中IGBT属于分立器件的一种。
2、IGBT的特点
IGBT 可以被认为是一个MOSFET 和一个 BJT (双极型三极管)混合形成的器件,但相比于MOSFET制造难度更高、结构更复杂,可承受的电压也更大。一般 MOSFET 器件或模组的可承受电压范围为 20-800V,而IGBT 可承受1000V以上的高电压,因而是电力电子领域较为理想的开关器件。
3、IGBT的主要功能
IGBT通过脉宽调制,可以把输入的直流电变成人们所需要频率的交流电,或者反过来。主要用于变频逆变和其他逆变电路,被称为是电力电子装置的“CPU”。
4、IGBT的主要产品形式
模组和分立器件两种形式,一般通俗的说IGBT指模组,IGBT模块是由IGBT分立器件与快恢复二极管芯片通过特定的电路桥接封装而成的模块化半导体产品。
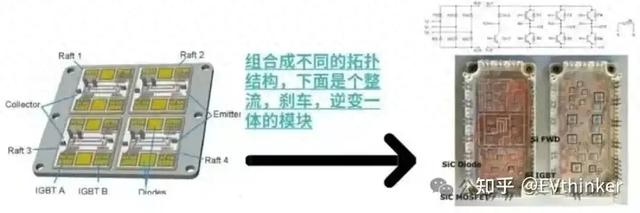
二、IGBT技术及其应用
1、IGBT的技术特点
IGBT生命周期较长,产品迭代速率不追求摩尔定律,使用周期较长,虽然老一代产品损耗较大,但其芯片面积大,稳定性较好,因此部分领域仍会选择使用旧代产品。
各代IGBT的主要发展趋势主要为降低损耗与生产成本,总结来看大致可分为三大主要技术阶段:
第一阶段是:第一、第二代IGBT为代表的平面栅型 IGBT,其中第一代由于工艺复杂且成本高,已基本被淘汰。第二代部分类型产品目前仍有销售。
第二阶段是:以第三代、第四代IGBT为代表的沟槽栅型IGBT,该类型产品通过创新的沟槽设计,大大减小了IGBT的体积和使用功耗,因此被广泛使用。第五代、第六代的IGBT,属于对沟槽栅型的改进,结构并未有很大的变动。此外,该阶段还出现了第三阶段的过渡型产品Trench Stop。
第三阶段是:2018年以后出现的第七代微沟槽型 IGBT,该类型产品更大程度地减小了器件的体积和功耗,目前英飞凌等厂商技术已达量产水平。
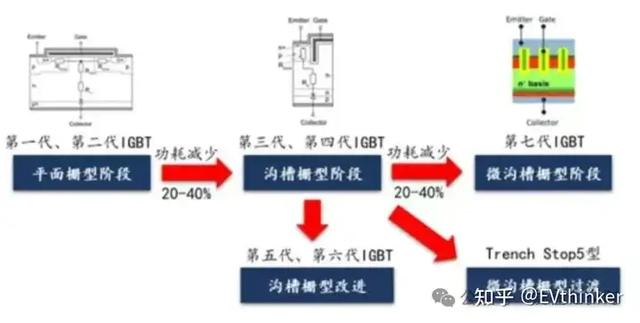
2、IGBT的市场应用
IGBT能够根据工业装置中的信号指令来调节电路中的电压、电流、频率、相位等,实现精准调控的目的,被广泛应用于电机节能、轨道交通、智能电网、航空航天、家用电器、汽车电子、新能源发电、新能源汽车等领域。
按电压分布来看,消费电子领域所用IGBT产品主要集中 在600V以下,新能源汽车常用IGBT产品电压为6001200V,动车组常用的IGBT模块为3300V和6500V,轨 道交通所使用的IGBT 电压在 1700V-6500V之间;智能电 网使用的IGBT通常为3300V。
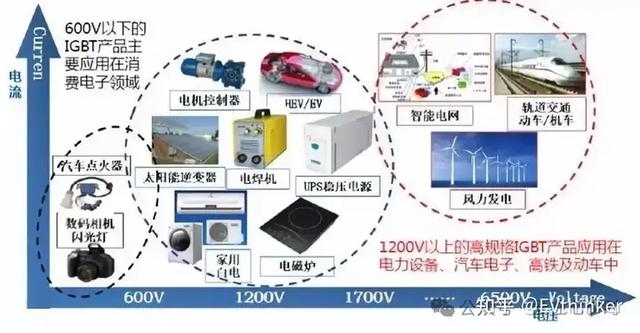
数据显示,从中国市场来看新能源汽车相关领域是IGBT最大应用领域,市场占比达31%,其次为消费电子、工业控制及新能源发电等。
IGBT模块热量主要由导通功耗、开关功耗、断态功耗以及快恢复二极管功耗产生,通常情况下断态功 耗因相对较小可忽略不计。下图为常规IGBT模块结构示意简图,其IGBT热传输路径为:IGBT芯片/二极管→芯片下焊接层→DBC铜层→DBC陶瓷层→DBC铜 层→衬底焊接层→基板→导热硅胶→散热器→外部环境。
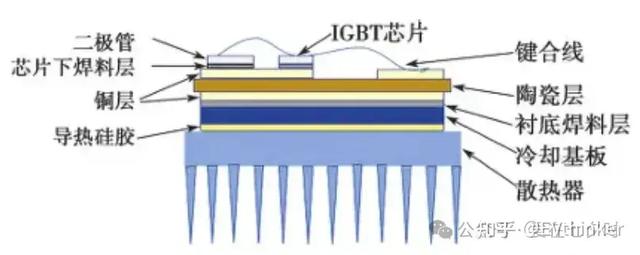
IGBT功率模块的传热热阻主要包括热沉自身的热 阻、各焊接层热阻、陶瓷层热阻、上下铜层热阻,以及各层之间的接触热阻。通过了解IGBT功率模块的热 传输路径和传热热阻的组成,有利于我们更好地理解 IGBT模块冷却系统散热性能的优化过程。
3、风冷式散热
风冷可以分为自然对流(空气冷却)和强制冷却。随着IGBT功率越来越大,普通的自然对流冷却显 然不能够满足高性能高热流密度IGBT模块的散热需 求。强制风冷的散热量比自然风冷散热量高约5~12倍。强制风冷散热系统主要是由电子元器件、散热器和风 扇等组成。电子元器件产生的热量由散热器传导,经 过空气对流带出,当带出的热量等于热源产生的热量 时便达到平衡。
3.1、翅片形状优化。
通过改变翅片形状结构,可减 少对流环境下流动阻力的影响,提高散热器散热性能。半圆形和等腰三角形形状的翅片结构, 在与常用矩形翅片散热性能的对比分析中可发现,流 动阻力对散热性能有一定影响,但阻力并非唯一决定 性因素,数值模拟结果表明:在矩形、半圆形和等腰 三角形结构翅片中,半圆形结构流动阻力最小、等腰 三角形次之,等腰三角形结构翅片具有更高的换热系 数,但半圆形和等腰三角形的翅片结构散热性能均优 于矩形结构散热器。
3.2、流道结构优化。
通过调整散热器部件的位置、 在合适位置加入挡板,降低风道分压不均匀性,减少 负压区的产生。借助Icepak热分析软件, 对变频一体机(YJVFT-315S1-4(55/1140))内部风道 结构进行优化,优化前发现在风扇上游和安装支架下 部区域存在较大的回流、压力分布不均等突出问题;通过改变基板纵向尺寸、翅片数量和翅片间距等变量, 避免了主要回流区域的产生,减少进风口进风量损失, 相对于优化前内部分压更均匀。
3.3、考虑更换散热器材料,使用比表面积更大的材 料。
泡沫铜翅片散热器,该型材具有比 表面积大、质量密度更低等特点;通过试验比对,证 实了具有更大比表面积结构的材料更有利于热量向外 部环境的扩散,散热效果更佳。填充石蜡、石墨纳米片的直翅片散热器,发现石墨纳米片可 以有效地增强导热,其中搭载15%的石墨纳米片散热 器的热导率增加了近5倍。
4、液冷式散热
水冷散热系统通常包括冷却模块、液冷泵、 水箱、“水-空气”热交换器和管路,如图2和图3所 示。冷却模块负责接收热源产生的热量,在泵的作用下 管路中水能够快速流动,从而实现冷热液体频繁交替, 吸收大量热量的液体在流经“水-空气”热交换器时将 吸收的热量转移到外部环境中,这样保证了热源温度处 于一个相对稳定的环境下。
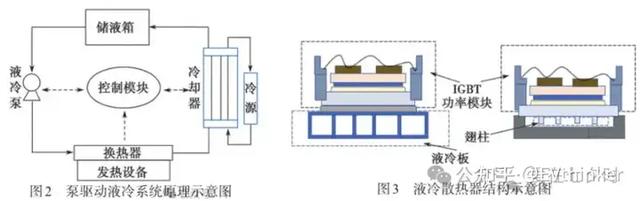
与风冷散热器相同,合理改变原有结构内部翅柱 的形状也可以提高散热器整体散热效果,进而实现冷 却系统优化的目的。
5、热管相变散热
5.1、常规热虹吸管散热
热管按照工作液体回流动力区可分为:有芯热管、 两相闭式热虹吸管(又称重力热管,如图4所示)、重 力辅助热管、旋转热管、电流体动力热管、磁流体动 力热管、渗透热管等。重力热管只需满足加热段位于冷凝段下方,就可以 实现内部工质的循环,不需要吸液芯、吸液槽等结构, 结构最为简单,应用也最为广泛。早期应用在IGBT模 块散热的热管以重力热管居多。
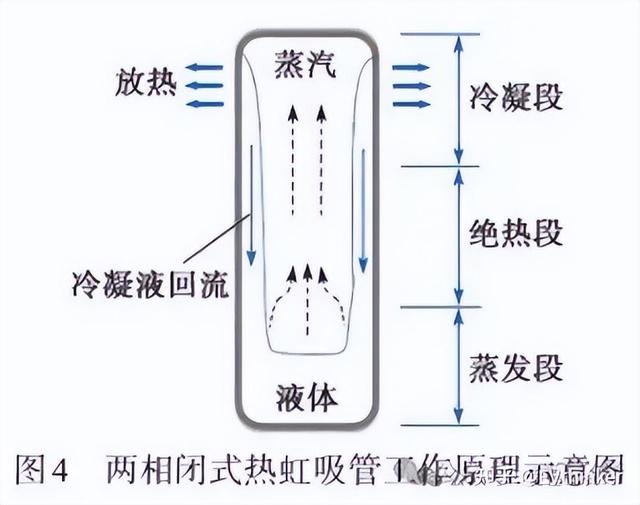
5.2、两相闭式热虹吸管优化
早期应用于IGBT模块散热的热管冷却系统是在冷 却基板钻取一定尺度的孔洞,然后将重力热管竖直嵌 入在基板上,在远离基板的热管表面装配散热翅片, 即通过“热管散热器+空气对流”方式实现散热要求。在上述2个热管散 热模型中,空腔内部用蒸馏水作为热管的工作介质, 不具有导电性,充分地考虑到介质泄漏可能会带来的 问题。散热器原理图见图5~图7。
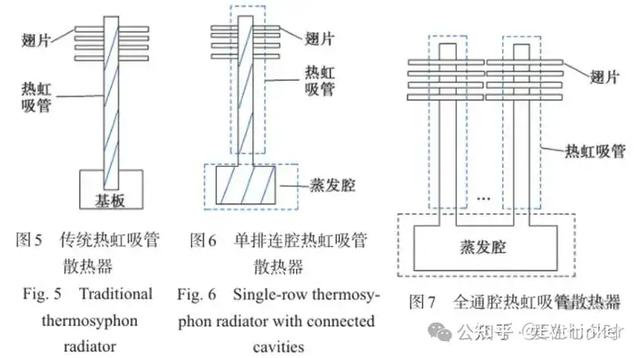
5.3、平板热管
这是一种采用多个平板微热管构成平板微热管阵列,配合翅片的使用,该散热系统可以保证IGBT模块在 自然冷却条件下结温约为110 ℃,基板最高温度为 70.3 ℃,可以满足其正常工作的要求。
5.4、环路热管
这是一种带有毛细芯的环路热管,其独 到之处在于蒸发器的嵌入式工艺处理,将多组环路热 管均匀埋藏在冷却基板内部,环路热管均匀布置到整 块基板内部,同一层面的热管蒸发器受热均匀,使得散热器占用IGBT模块的整体尺寸很小。
5.5、埋入式热管散热器
下面展示了9种不同的埋入式热管散热器。
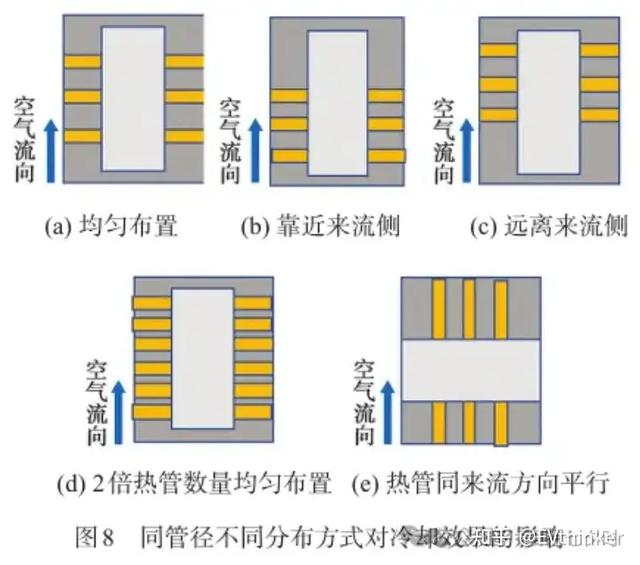
图9显示,当热管的分布位置一致时,改 变热管的直径尺寸,其散热效果随管径直径的增大而提高。

图10中“U”型和“O”型嵌入式模型增加了翅片中下 部分的热流密度,翅片潜能充分发挥,“O”型表现出 更好的均温性,散热表现也最好,该热管散热器性能 优于传统热管散热器,能降低散热器底板温度20 ℃。
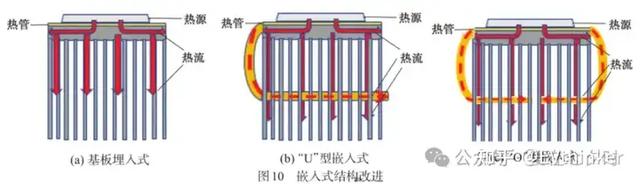
目前针对IGBT模块的热管理,各种不同的散热手 段层出不穷,除了空气冷却、液体冷却和热管相变冷却外,两相强制对流冷却技术(如喷雾冷却、射流冷却等)也得到了发展。
用于维持IGBT功率模块正常工作温度的各种冷却 技术,既有主动式冷却,又涉及到被动式冷却。通常, 通过优化散热器传统结构、选用新型导热材料都可以 提高整体散热性能,若考虑进一步地提升散热效果,减小接触热阻是一种很好的选择。此外,还可以通过增大散热面积,引入冷却性能更好的石墨烯薄膜。
三、 IGBT的产业链及工艺流程
1、IGBT产业链
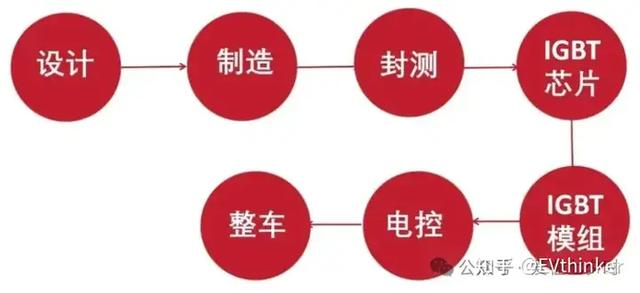
2、IGBT的加工流程

3、IGBT的生产流程
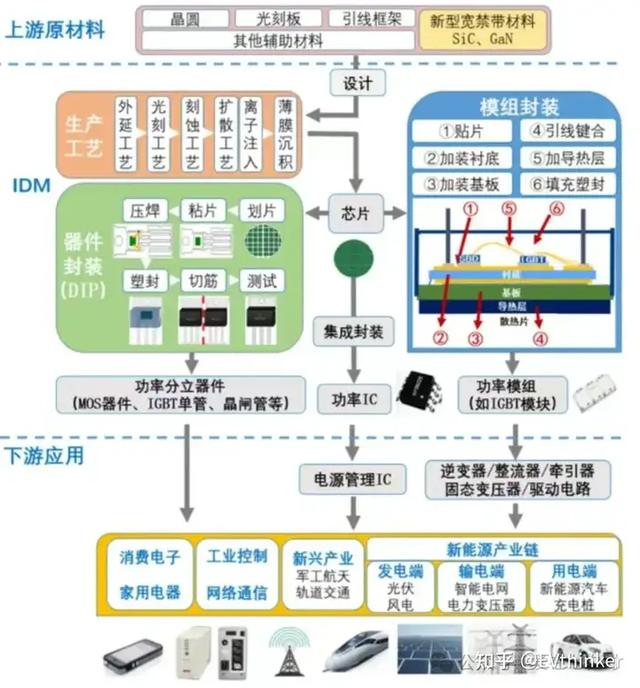
4、IGBT制造的三大难点
IGBT制造的三大难点:背板减薄、激光退火、离子注入。
IGBT的正面工艺和标准BCD的LDMOS区别不大,但背面工艺要求严苛(为了实现大功率化)。具体来说,背面工艺是在基于已完成正面Device和金属AI层的基础上,将硅片通过机械减薄或特殊减薄工艺(如Taiko、 Temporary Bonding技术)进行减薄处理,然后对减薄硅片进行背面离子注入,在此过程中还引入了激光退火技术来精确控制硅片面的能量密度。
特定耐压指标的IGBT器件,芯片厚度需要减薄到100-200μm, 对于要求较高的器件,甚至需要减薄到60~80μm。当硅片厚度 减到100-200μm的量级,后续的加工处理非常困难,硅片极易 破碎和翘曲。
从8寸到12寸有两个关键门槛:芯片厚度从120微米降低到80微米,翘曲现象更严重;背面高能离子注入(氢离子注入),容易导致裂片,对设备和工艺要求更高。
5、IGBT模块的封装难点
IGBT模块重视散热及可靠性,封装环节附加值高,设计优化、材料升级是封装技术进化的两个维度。
设计升级方面主要是:
5.1、采用聚对二甲苯进行封装。
聚对二甲苯具有极其优良的导电性能、耐热性、耐候性和化学稳定性。
5.2、采用低温银烧结和瞬态液相扩散焊接。
在焊接工艺方面,低温银烧结技术、瞬态液相扩散焊接与传统的锡铅合金焊接相比,导热性、耐热性更好,可靠性更高。
材料升级方面主要是:
5.1、通过使用新的焊材,例如薄膜烧结、金烧结、胶水或甚至草酸银,来提升散热性能;
5.2、通过使用陶瓷散热片来增加散热性能;
5.3、通过使用球形键合来提升散热性能。
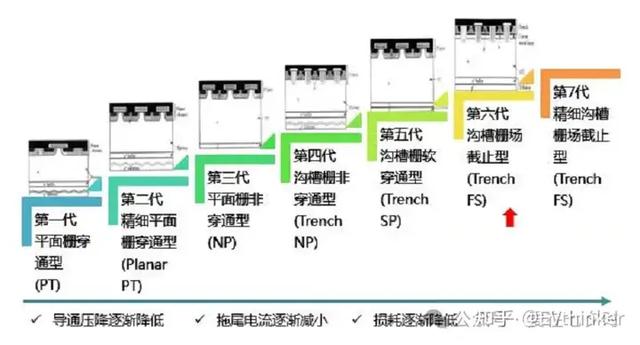
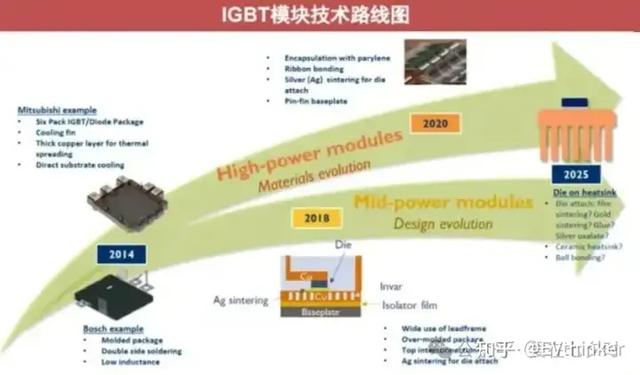
珠海富士智能股份有限公司专注于IGBT散热铜底板研发与制造!http://www.fujichinon.com/
