引言
与金属材料相比,树脂基增强复合材料具有较高的刚度、强度,良好的耐热、耐冲击、耐腐蚀性能,因此被广泛应用于航天航空、汽车交通、特种设备等领域。在特种设备领域,国外已经开始V型瓶(全复合材料)的相关研究。碳纤维增强复合材料(CFRP)在制作过程中,由于工艺不成熟或外界因素的干扰,纤维层容易和树脂浸渍不充分导致材料内部留有微气孔。使用过程中,碳纤维增强层合板在厚度方向上没有增强,层间性能较弱,因此层内分层损伤一直是层合结构的主要损伤模式之一。分层损伤的出现会让复合材料的承载能力快速下降,成为复合材料工程应用的重大安全隐患。
近年来,相关学者对复合材料的损伤演化及监测检测进行了深入研究。总体上,关于含分层损伤的碳纤维增强复合材料的结构健康监测的研究已经比较深入,但多数集中在力学性能的比较以及对分层损伤的静态检测。尽管目前已开展含分层缺陷复合材料损伤演化的相关研究,但是定量评价分层缺陷对不同损伤机制的影响研究还存在空白。
本文制备了含不同分层损伤的碳纤维增强复合材料,采用声发射技术实时监测其在弯曲加载下的损伤演化行为。通过分析损伤演化中材料内部的声发射信号揭示复合材料在弯曲破坏过程中的损伤演化规律,为碳纤维增强复合材料的早期损伤预报提供科学有效依据。
1. 实验部分
1.1
/复合材料试件制备/
实验以10层T300-3k碳纤维织物为增强相,3329A环氧树脂和3329B固化剂(质量比为100:40)为基体相,采用真空辅助树脂灌注技术制备所需碳纤维增强复合材料层合板。
制备时,在第2层和第3层之间、第5层和第6层之间分别放入宽度为5mm的聚四氟乙烯薄膜,用来模拟分层损伤(记分层缺陷在第2、第3层的复合材料试件为试件A,分层缺陷在第5、第6层的复合材料试件为试件B)。层合板制备好后需在110℃烘干箱中固化6h、在室温下固化48h。最终切割成60mmx20mm的标准件,标准件厚度为(3.0±0.2)mm(图1)。
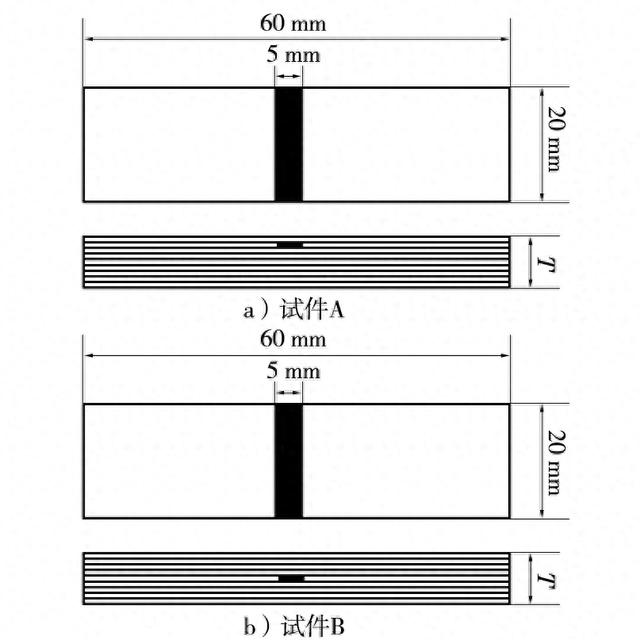
图1. 两类复合材料试件示意
1.2
/实验装置和实验过程/
实验过程按照ASTM D790-2003《未增强和增强塑料及电绝缘材料弯曲性的标准试验方法》,在LD24万能试验机上进行三点弯曲实验。DS2-8A型声发射仪实时监测材料内部的损伤演化,使用的声发射传感器型号为RS-54,内置前置放大器为10mV,频率范围为100~900kHz;采样频率设置为3MHz,门槛值设置为40dB(图2)。弯曲速率依据标准定为1mm/min,跨厚比应为16:1,所以跨距设置为48mm。
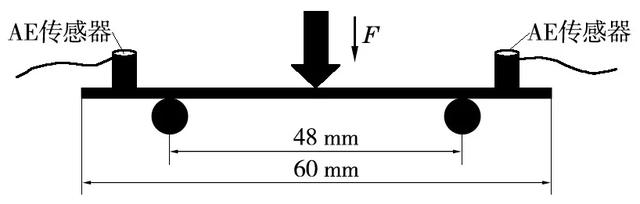
图2. 三点弯曲实验测试示意
2. 结果与讨论
2.1
/宏观力学性能分析/
两试件的破坏载荷和弯曲强度的实验数据可知,
试件A的破坏载荷均值和抗弯强度分别为1.93kN和772MPa,破坏载荷标准差为0.11269kN;
试件B的破坏载荷和抗弯强度分别为2.15kN和860MPa,破坏载荷标准差为0.13317kN(表1)。
分层缺陷越靠近表面,试件的承载能力越差,试件A的抗弯强度比试件B低11.39%。试件B的分层位置位于中性层附近,所以它的承载能力相对于试件A略有提升。

表1. 两类试件破坏载荷与抗弯强度
对复合材料进行宏观力学的分析,可将其视为均匀的各向异性材料,即不考虑环氧基体和增强纤维各自的材料特性,用平均力学性能表示层合板的强度和刚度特性。
两种复合材料试件的载荷—位移曲线和平均破坏载荷曲线如图3所示:
试件A在1.84kN附近有一个明显的波动,代表靠近压头的两层子板可能提前发生了失稳破坏。由于分层缺陷位置靠近表面,在两层子板发生破坏后难以保证载荷向其余子板的传递,所以试件A载荷位移曲线在1.84kN之后有较大波动,直至最后断裂失效。
试件B的破坏载荷比试件A高11.3%,而且两类试件在达到极限载荷后存在稳定的持续加载阶段,表明试件虽然经历了严重的损伤,但仍有一定的承载能力。试件的残余强度允许材料继续吸收能量。

图3. 两类试件载荷-位移曲线
载荷-位移曲线只能反映材料整体的宏观力学性能,因此采用声发射技术同时监测试件的弯曲加载,获取实时声发射信号来描述其损伤演化。
2.2
/声发射响应特征/
声发射信号的特征参数包括频率、幅值、能量、上升时间、撞击数、RA值(上升时间/幅值)等,不同的特征参数包含了信号的不同特性。在复合材料中,常用的特征参数为频率、能量和幅值。幅值是声发射信号波形中的最大振幅,表征声发射源信号的强度;能量则是信号检波包络线下的面积,可以表征声波的振幅,声发射事件的强度和持续时间。本节通过分析两类试件声发射信号的幅值和能量特征,研究损伤演化过程。
图4为两类复合材料试件的幅值-时间-载荷关联图。可以看出,在加载初期,两类试件均没有声发射信号,此时载荷较小,材料内部并无损伤。
在100s前试件A产生的声发射信号多于试件B,且这些信号多是低幅值信号(低于60dB),说明随着载荷的增加,分层缺陷靠近表面的试件出现了较多微损伤。
在100s之后,两类试件均出现大量高幅值(高于80dB)声发射信号,高幅值信号是多种损伤模式共同出现的结果,说明此时两类试件均已经出现了严重的损伤。在达到极限载荷之后,两类试件承载能力突降,之后的每一次载荷突降,均伴随着90dB以上的信号出现,这一点在试件B中表现尤为明显。
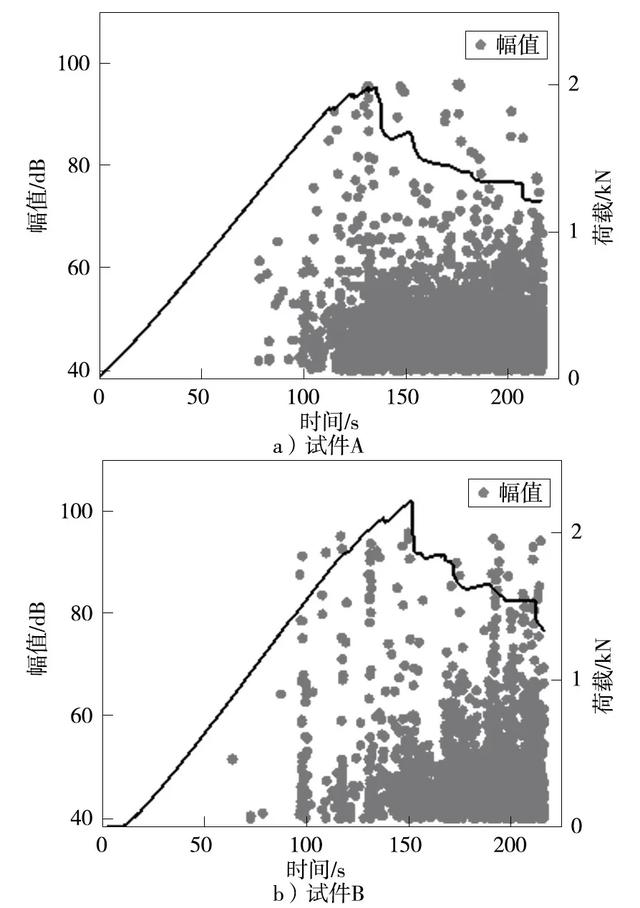
图4. 声发射幅度-时间-载荷关联图
图5为两类复合材料试件的声发射能量、累积撞击数和载荷随时间变化历程。结合图4,100s前的声发射信号同时具有低能量和低幅值的特征,这些损伤应该是复合材料内部的加工缺陷或微小裂纹在小载荷的作用下形成的损伤。
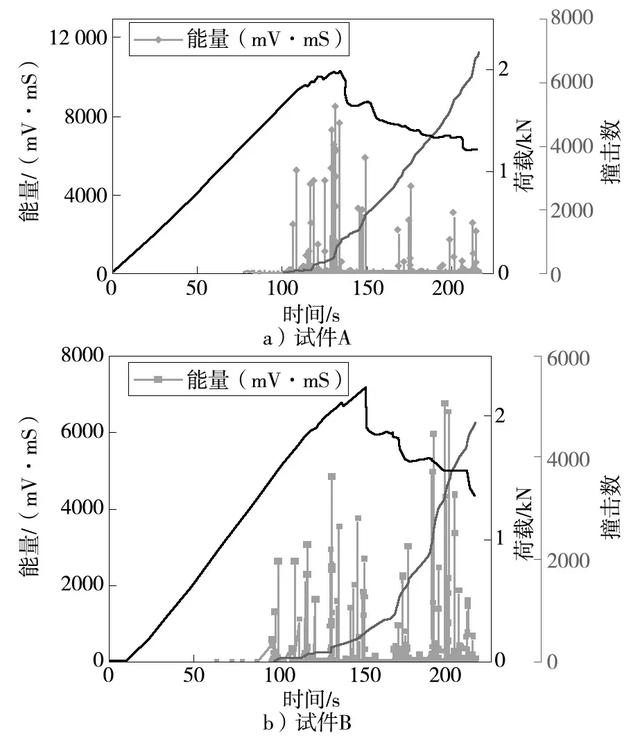
图5. 复合材料试件的能量、撞击数和载荷时间历程
试件A在106s时出现了能量为2 540.43 mV·ms的声发射信号,之后一直有高能量的声发射信号产生。直至加载至破坏载荷附近,高能量信号激增,最高达8 544.49 mV·ms。在达到破坏载荷后,试件承载能力下降,且每一个平台期之后载荷的突降都带来了高能声发射信号的产生和累计撞击数的增加,说明撞击数和能量可以用于描述试件的损伤过程,并且与载荷位移曲线有较好的对应性。
试件B出现高能声发射信号的时间早于试件A,从信号分布来看,试件B的高能信号集中在200s左右,且总体的加载过程中4 000 mV·ms以上的信号少于试件A,最高能量为6 764.37 mV·ms。
撞击数为材料在加载过程中发生损伤的次数,声发射源每发出一次弹性波都对应着一个撞击数。试件A的累计撞击数为6811个,试件B为4686个。
2.3
/声发射信号的聚类分析/
选取峰值频率、幅度和RA值,使用IBM SPSS执行的k-means算法进行声发射信号的聚类分析统计,建立不同损伤信号和损伤模式间的相关性。两类复合材料试件的峰值频率和弯曲载荷随时间的变化历程如图6所示。

图6. 试件峰值频率和荷载随时间变化历程
根据峰值频率大小,声发射信号被分为三类:基体开裂代表的声发射信号峰值频率最低,一般为十几到几十;纤维/基体脱粘次之;纤维断裂的声发射信号频率最高。两类试件不同损伤模式的频率范围见表2,声发射信号在不同损伤模式的边界处没有重叠,说明聚类效果良好。

表2. 两类试件不同损伤机制的频率范围(kHz)
由表2还可以看出,两类复合材料试件的不同损伤模式几乎是同时发生的。试件A加载至1.26kN附近产生了连续的基体开裂和纤维/基体损伤,而试件B在1.50kN附近才有大量的基体开裂和纤维/基体脱粘损伤出现。
因为分类只有3种,所以中频声发射信号除了代表纤维/基体开裂,也可代表分层损伤。随着载荷的持续增加,试件A在1.56kN出现大量的纤维断裂损伤,这可能是因为靠近表面的聚四氟乙烯薄膜影响了层合结构的完整性,从而影响弯曲应力从第3层子板向第4层子板的传递,所以第1、第2层子板率先出现大量的纤维断裂损伤。试件B在1.6kN出现了纤维断裂损伤,但与试件A不同,其纤维断裂损伤明显较少。
为了研究不同损伤机制对复合材料试件整体损伤的影响,采用累计声发射能量来表征材料的整体状态和完整性。图7为复合材料试件不同损伤机制的累计声发射能量。
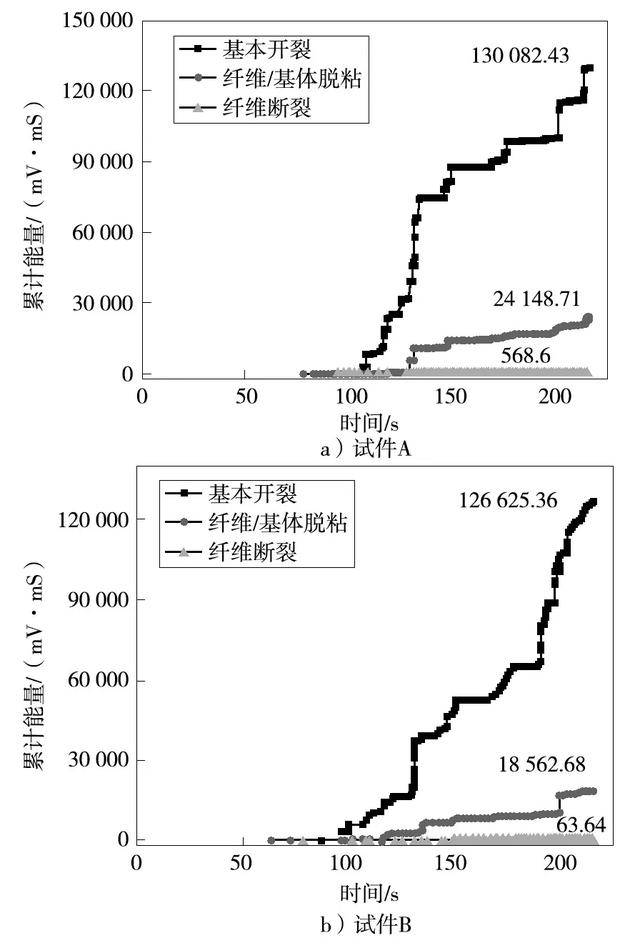
图7. 试件不同损伤机制的累计声发射能量
加载初期产生的基体开裂和纤维/基体脱粘信号能量较小,所以此阶段基体开裂和纤维/基体脱粘的累计声能曲线不好区分。
在100s以后,基体开裂和纤维/基体脱粘的累计声能曲线开始快速增长。不同的是,分层缺陷靠近表面的试件其失效主要集中在前半阶段,最终试件A基体开裂、纤维/基体脱粘和纤维断裂的累计声能分别为130 082.43 mV·ms、24 148.71 mV·ms和568.6 mV·ms。
而分层缺陷位于中性层的试件B,则是在加载的后一阶段累计声能曲线变化率最大,最终试件的3种损伤机制的累计声能分别为126 625.36 mV·ms、18 562.68 mV·ms和63.64 mV·ms。弯曲加载全过程试件A释放的累计声能比试件B高6.1%。
结语
本文基于声发射技术,研究了含不同分层缺陷的碳纤维增强复合材料层合板在弯曲加载下的损伤演化行为。结果表明:
(1)相对于材料中间位置的分层缺陷,位于近表面的分层对试件的承载能力影响更大,含近表面分层缺陷的试件抗弯强度比含中间位置分层缺陷的试件低11.39%。
(2)分层缺陷不会改变试件的损伤机制,对损伤信号进行聚类分析,明确信号代表的损伤模式,并采用累计能量参量实现分层缺陷对损伤机制影响的定量表征。
(3)含近表面分层的试件其累计声能在峰值载荷附近增长最快。声发射技术可以实现复合材料损伤的定性和量化评估,为复合材料结构健康监测提供依据。
END
来源:《设备管理与维修》(作者:赵惠;杨飒;于璇;王璇;牛卫飞)
文章来源:恒润集团
注:本站转载的文章大部分收集于互联网,文章版权归原作者及原出处所有。文中观点仅供分享交流,如涉及版权等问题,请您告知,我将及时处理!