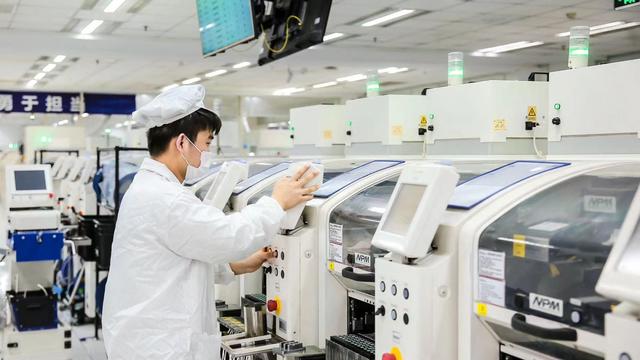
出品|虎嗅科技组
作者|陈伊凡、齐健
头图|联想
40多年前,深圳从香港转移来的“三来一补”加工贸易中,捞取了第一桶金,那是当代“中国制造”的起点。如今,曾经的渔村发展成大都会深圳,这座被制造改变的城市,制造也在这里迭代嬗变。
从深圳市中心福田区出发,向西开行40多公里,就到了联想集团(下称:联想)南方智能制造基地。
基地所在地深圳光明区新划定的科学城,联想建在这里的制造基地被视作智能制造的“母本工厂”,这意味着,这里会率先应用最先进技术,这座工厂将会形成可复制方案进行推广,其也将承载创新理念和产品的孵化。
初建的光明科学城周围还有些破败荒芜,但联想制造基地已经显现出科学城完工后的雏形——从外部看,基地就像是几座6层写字楼,只有走进去,置身嘈杂的产线,才知道这是工厂。
“全自动货架”、“ AGV机器人”等一系列自动化名词从关伟口中蹦出,描绘未来。关伟是联想高级副总裁、全球供应链负责人,在深圳工厂的一间会议室里,他向虎嗅介绍了联想全球智能制造的布局,旁边的厂房中,一半是人工,一半是“智能”。
与此同时,在距离深圳将近一万公里的匈牙利首都布达佩斯,一座以这座“母本工厂”产线为蓝本的厂房正在运转。那里最初的四条产线,由深圳工厂设计、制造,在疫情期间通过中欧班列运往欧洲。
跨国公司的创新扩散与母国创新,在这套智能制造体系上演进循环。
当前,全球供应链正在经历前所未有的动荡,消费电子疲软,库存积压,据第三方咨询机构Gartner最新公布的数据,2023年一季度全球个人电脑(PC)出货量共计5520万台,较2022年一季度减少30%。在变幻莫测的经济形势、购买动力不足、供应过剩和PC需求持续低迷这些不利因素的共同影响下,PC市场连续第二个季度出现历史性同比下降。
很难有制造企业能在行业下行周期中全身而退。
即便是在2023年一季度,以23.3%的市场份额继续保持PC出货量第一的联想,也连续两个季度遭遇了公司历史上最大的年出货量降幅。
当PC市场下行时, “库存”成了很多制造企业的“魔咒”。但关伟说,他们面临最大问题是需求疲软,而不是库存。智能化系统能够让工厂提前4个月-5个月对市场需求作出判断和决策。
在联想刚发布的22/23财年全年及Q4业绩发布沟通会上,联想表示较上个财年,库存同比下降24%。对于一个全球上亿台PC年出货量、上百条产品线的企业来说,这样的库存下降数据着实不容易。联想CEO杨元庆也表示,去库存过程中个季度末基本完成。
走出“库存”魔咒的背后,是供应链的管理,而作为全球PC出货量最大的联想智能工厂,意味着这些工厂需要承担更大数量的订单、多元需求以及更加快速的响应,降库存的难度更大。全球PC生产的两座灯塔工厂,一座是惠普的新加坡工厂,另一座就是联想的合肥产业基地(下称联宝)。根据联想统计的销售数据,全球每销售8台笔记本电脑,就有1台诞生于联宝。
过去三个月,虎嗅走访了联想合肥工厂、深圳工厂、匈牙利工厂,试图还原联想如何利用智能制造预测和管理全球供应链,如何复制智能制造能力的过程。
复制智能制造
2008年,联想刚刚开始讨论是否要投入建设自造基地时,有人主张“要把制造业拿到自己手里”,有人主张“没有自建工厂的压力,品牌能跑得更轻快”,当时的高层会议一度形成4票赞成、4票反对的僵持局面。
被视为消费电子行业的领头羊苹果,就完全没有制造能力。虽然这种业务模式可以集中资源在产品设计端发力,但这也意味着苹果对代工伙伴严重依赖。
2008年,正是中国大陆手机ODM厂商诞生之际。闻泰在嘉兴建立了自己的制造工厂,从研发设计向生产制造进行垂直整合,成为中国大陆第一家手机ODM企业。此后,龙旗、华勤等纷纷转型ODM。
关伟至今记得,当初是联想CEO杨元庆投下的关键一票。
三年后,关伟来到安徽合肥肥西县宋郢,为联想的“自造”工程打下第一桩。联想合肥产业基地年初获评 “灯塔工厂”,这一称号,代表了智能制造的最高水平。
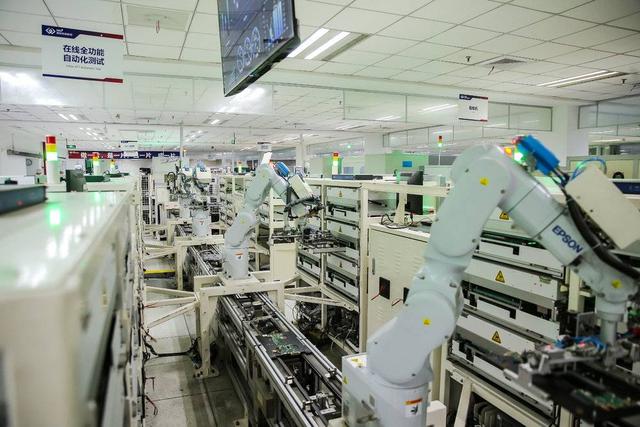
联宝工厂产线 图片来源:联想
如今,这座工厂有32条智能主板、36条整机生产线,面向全球5大区域126个国家和地区的客户提供高科技产品和服务。截至目前,它累计出货近2.5亿台/套(最新数据),平均0.5秒就有1台笔记本电脑下线。
“灯塔工厂的评审标准不是死的,是动态的。”曾参与过灯塔工厂评审咨询工作的李铁军告诉虎嗅,这个“动态”的唯一标准就是——“先进”,也就是在灯塔工厂评选的打分表格中,看看企业到底有多少项技术是行业领先的。
李铁军打了个比方,去年评审的标准可能认为使用了预测性维护的工厂是领先的,但今年预测性维护普及了,可能这个标准就改成5G+柔性制造了。这种动态的评选标准,也就意味着灯塔工厂要有不断迭代技术的能力,这背后则是资金和技术实力的积累。
联宝的特色是自动化和智能化。工厂每天处理约8000笔订单,且80%都是单笔小于5台的定制化需求。其特色产线之一的水星线,可以灵活多变,工作台可以变成不同模块,长线、流水线、Z形线等,最大限度保证柔性。整个电脑的包装环节,皆由机械臂完成。
从生产前的排产规划、到智能产线动态运转、再到供应链协同管理,联宝将数智技术与实体制造深度融合,通过智能排产、联合排产和供应链控制塔等一系列数字化创新应用,实现排产时间缩短67%,结构件库存降低50%,每0.5秒就可以下线一台笔记本电脑。
8年后,智能制造能力不断演进、提升,2019年,关伟和联想的众多高管一起,在深圳光明区制定了一片新的规划,也就是今天的联想南方智能制造基地,联想的智能制造“母本工厂”。
在这座智能制造工厂中,流水线并不紧凑,工厂也不拥挤。原料、货品码放得整整齐齐,一组组机柜上排列着自动进行软件灌装、压力测试的产品。厂房里的上下货由AGV机器人“全权负责”,一切都显得井然有序。
而这些智能产线最让人感到意外的是,线上的工人看起来似乎并不忙碌,但整条产线的产能却可以达到传统产线的十几倍,甚至几十倍。
在联宝工厂的时候,关伟曾去拜访一些ODM厂商,他们给了一组数据令他印象深刻,180米的产线,180多个人,1小时做180台机器,“这是传统的生产制造”。而如今,联想深圳工厂的一条笔记本生产线147米,有72个智能制造工位,生产线人员只有53名。
“未来人会不会更少?一定会,因为我们是做真正的实业,不是做展示,让大家觉得很漂亮,毕竟我们还要跑我们正常的业务,如果成本太高的话,客户、用户是不接受的。”关伟说,三四年前,联想设立生产线自动化,智能率只敢定在40%,因为再往下投资,成本效率不划算。但随着数字化、智能化能力的提升,自动化的水平也在逐步提升,今天的自动化率可以做到60%。也许再过两年自动化率能做到65%、70%。
联想的每个工厂都有侧重,例如,武汉重点是手机和平板电脑产品;合肥主要是笔记本电脑和服务器产品;天津未来是智能制造的展示中心,天津重点服务的是中国的客户,未来用天津的制造基地辐射东北亚市场,比如日韩市场;南方基地是全球智能制造“母本工厂”。这也决定了不同工厂的智能化程度,而不是一味复制。
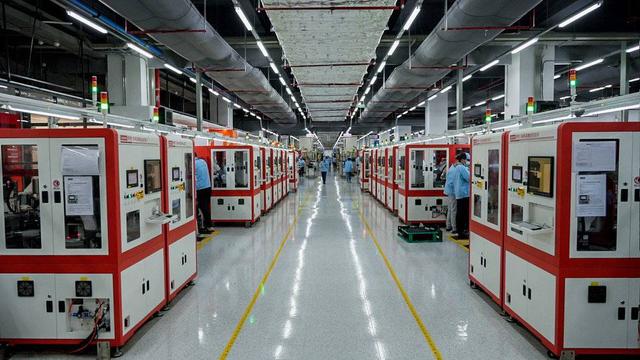
联想南方基地工厂 图片来源:联想
关伟说,尽管产能不如合肥工厂,但南方基地的生产复杂度比合肥工厂高,最著名的、最稳定的商用电脑ThinkPad生产地是在深圳,特别是联想的S系列和T系列。而联想的高性能计算服务器整个成品都是在南方基地生产制造。后来,南方基地的这套工厂,被复制到了匈牙利,在那里生产的高性能计算服务器,被运往欧洲的算力中心。
细数下来,全球PC生产商自建工厂的并不多,而将自己智能制造的能力对外赋能的,则更少。
桐昆,是一家化工企业,主营PAT、纤维和长丝,这家企业有21个车间,791条生产线,分布在多个厂区,过去,这些厂区都是一个个信息孤岛。联想在各个工厂直接搭建了统一标准,通过在生产线附近放上传感器,随时收集模拟信号,再将这些模拟信号转为数字信号,通过Leap数据库归纳整理,再上传到云端,这样这些原本孤岛般的厂区信息就集合到了一个管理系统。
原材料从生产到发货,两端都是物流,中间是制造,智能制造中,物流的智能化尤为关键。举个例子,在联想的系统里,有上百万的物料编码、一台笔记本电脑的主机板上大概有1500个元器件、再加上其他组装的元器件,一台笔记本上,大概有3500个-4000个元器件。这些元器件怎么去储存、捡料,没有自动化、智能化的解决方案,难以想象。关伟解释,以前是一个一个货架,用二维码一扫,再去拿。这样备料方式,生产100台电脑,备料可能超过六个小时,甚至八个小时。但通过智能化的方案两个小时可能就会备好(料),这是完全不一样的。关伟说,在紧挨着园区的地方,会建立通道,与生产线进行直接的连接来提升生产效率。
智能制造的关键不是“智能”
与许多人设想的智能制造不同,其关键可能不是智能,而是产能。盲目上系统,产能跟不上,可能造成不必要的浪费。
“多数情况智能工厂的产能都是开不满的。”联想某智能工厂负责人告诉虎嗅。
而另一边,则是PC需求的下降,行业周期的下行,作为全球PC出货量最大的联想,自然无法独善其身。
“低迷的经济市场将在整个2023年继续抑制设备需求。”Gartner高级研究总监Ranjit Atwal表示,他预计2023年终端用户在设备上的支出将下降5.1%。
当去库存成为供应链企业今年主基调时,关伟并不担心这个,他更多的判断来自数字化系统,多年的供应链管理经验,使他对数字和趋势极为敏感。2020年初,市场需求非常紧张,订单雪片般涌入,那个时候如何分货?是以利润优先还是市场份额优先,还是以营业额为优先?关伟他们依靠智能化系统,从不同的维度进行模拟,制定了分货的原则。
因此,关伟基于智能化决策,判断在2023年年底,市场需求就上来,因此反而需要加大库存。在分析市场的时候,采购团队、计划团队不仅要关注自己的库存是多少、市场份额有多少,还要看其他企业在哪里投产了,工厂产能是多少,是几寸的工厂,是什么样的工艺……
每周,关伟都会拿到一叠堆积数字的材料,上面是锂、钢、碳市场价格的走势。“那些原材料跟我六个月以后的价格是有关系的。通过这些我们就有系统性控制,因此,过去几年我们的库存压力都不大。”关伟说。
但产能,却是关伟最担心的问题之一。
需求上不来,产能自然开不满,智能化产线的价值也就难以体现。前述工厂负责人告诉虎嗅,过去的产线都是由人组成的,不怎么需要维护。停掉的产线没有成本,但智能工厂可不一样。
智能工厂的产线上都是智能化、自动化设备,不管设备开不开,产线跑不跑,机器买回来,就需要维护保养。虽然产线不开,维护保养费用会低一些,但总归是有费用,而且维护产线的技术人员也不像过去招的临时工,召之即来挥之即去,他们的工资更高,这些都是成本。为了维护智能化产线,联想专门针对不同设备组建了技术团队,即便是停工的产线,每年维护的成本也要十几万元。
关伟在谈到产能时,提到了一个重要的评估机器或系统效率与生产能力的参数——稼动率,这是衡量机器设备实际运转时间与理论可运转最大时间比的指标。
高稼动率表示机器设备的实际运转时间,接近理论可运转的最大时间,利用效率高,生产能力得到较好发挥。相反,稼动率低则说明机器设备闲置时间过长,实际产出低于理论最大产出,生产效率较低。
无论是在工业生产还是信息技术与人工智能领域,稼动率的提高都能够带来更高的生产力和系统性能,是实现成本节约与能力提升的有效手段。
综合来看,一个制造型的企业稼动率一般是50%,优秀的企业稼动率可以做到75%-80%,如再通过自动化手段,这个数字可以提升到85%-86%。在关伟看来,这是投资智能制造和自动化的依据之一。
“我们的策略一定是超前的,会对未来五年、十年进行规划,包括产能在内。”关伟说,今天产能开不满不意味着明天开不满。“也许2023年整个市场都不会特别好,这正是我们休养生息不断提升自己基础的时候,我相信2024年、2025年市场一定会快速发展,但我们坚决不能等到那个时候再去投资,因为投资是有周期的,一个工厂即使深圳速度要想建成、成熟化至少需要两年到三年的时间,所以现在我们就开始做。”
出海办厂
相比于维持母国区域创新系统所需的低廉边际成本,跨国办厂,可能又是另外一个故事。
将中国制造能力整体向外输出,联想是其中一个样本。
坐落于匈牙利布达佩斯的联想匈牙利工厂,建于2020年,这片场地,是从当地的物流公司手中租来的,占地近5万平方米,面积相当于7个足球场。
索博尔奇·佐约米(Szabolcs Zolyomi )是联想匈牙利工厂的一号员工,虽然加入联想不到三年,但在此之前,他在供应链上已与联想有许多合作。这所工厂建设耗资82亿匈牙利福林(约合16728 万元),其中匈牙利政府提供了20亿福林拨款。这里主要生产提供给算力中心的高性能计算服务器,其中就有发至全球第九大高性能计算中心的德国莱布尼茨高性能计算中心。
索博尔奇·佐约米告诉虎嗅,如今,这座匈牙利工厂的产能一天是1000台服务器和存储设备,4000台工作站和商用台式机。在这些产能之外,还有每天20个到30个相对比较复杂的机架解决方案的设计与完成。
进入工厂,不同颜色制服的工作人员被分配不同的工作,白衣服是标准操作员、深蓝色是产线的管理者,红色是监管员,而参访人员则是绿色制服。每条产线大概有20名-30名标准操作员,红色的监管员正在电脑前指导。
这座工厂的产线,正是从深圳的南方基地复制过来的。
但所谓的“复制”,并不容易。
由于考虑订单数量、产能等原因,这座匈牙利工厂并没有想象中高度智能,没有穿梭其中的自动化机器人,也没有联宝工厂那般有条不紊运行的机械臂。但整座工厂的IT管理做到了智能化。
联想计划在匈牙利建设整整4条生产线,预期该厂每天生产至少1000个定制服务器,4000个定制工作站,平均下来,也就是每分钟生产1台服务器,每15秒下线一台工作站。在匈牙利建厂时,正是2021年,世界疫情进入爆发期时,为了最大限度保证工厂完工进度,联想的员工在国内把生产线完整组装一遍,再拆下来打包运送,以防止一切可能的遗漏和疏忽,为了提高施工效率,他们甚至把在国内具体施工组装生产线的26名工人也一起带走。到了欧洲,还需要适应当地的接口标准。
疫情期间,海运货柜紧张,他们最后将设备打包成30个集装箱,通过中欧班列和海运运往匈牙利。
联想集团的匈牙利工厂建设用时不到10个月,索博尔奇·佐约米眼看着平地起了厂房,空地上的生产线被一条条组装、搭建完成,这座工厂将会响应EMEA(欧洲、中东和非洲)的市场需求。
每个产线工人面前都被安置了一个大屏幕,当产线工人不知道如何装配物品的时候,就可以把物料扫描一下,大屏幕上的模型就会点亮对应的位置,提示工人物料应该装配在对应的地方。
还有一块主控屏幕会显示哪条产线的效率是有问题的,主管会立即对这条产线进行调整。而如果操作员不小心拿错零件,系统将无法进行下一步提醒。
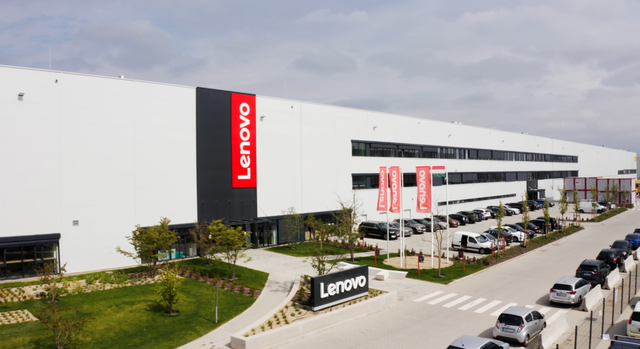
联想匈牙利工厂 图片来源:联想
在匈牙利工厂建成之前,联想集团的中国工厂每次向欧洲发货,都需要经过超远距离的长途运输,漫长的旅途,面临诸多变数,国际局势变化、气候海相的异常,还有许多无法预料的事件,都会导致产品到货延迟。在超远距离运输过程中,无数的小概率事件汇集在一起,就必然导致产品交付给客户的时间根本无法控制。很多客户因为担心延迟,就会选择另择供应商。加上服务器有定制化和及时性的要求,并且运输成本过高。
匈牙利工厂正好弥补了这一不足,靠近高速公路,地处欧洲腹地,提供了便利的交通。
索博尔奇·佐约米说,现在联想集团EMEA 区域(欧洲、中东与非洲)90%的服务器都是采用匈牙利工厂本地部件生产交付的,匈牙利工厂里,有15个国家的员工,其中70%是本地的匈牙利人。“如果我们跟客户签完一个合同,那时候才开始找供货商去供货,那要等6到7周的时间。对于客户来说,如果有一个急速的生产需求就没有办法满足。我们现在的做法是,所有的部件都是已经提前存在本地,已经在欧洲。一旦我们接到了客户的定制化需求,我们就可以马上拿到原材料为客户定制、生产,很快交付到客户手上。”
“全球化不简单的。”关伟直言,过去20年里,联想进行了多次兼并收购,包括日本NEC,将那里的工厂收购过来,整合组织架构、系统和流程,等到系统整合好,员工培训好后,仍会面临执行的问题。但关伟看来,数字化是解决这个问题的办法,他们将深圳做的智能生产系统LeMES推广到全球,标准和数字是统一的,智能排产系统也是在深圳做好,运行好,再当作一个个模块推向全球。
一折卖到国外,九折内销。
去库存还不简单?计划性报废呀,过保必坏[得瑟]
联想不是美国企业吗怎么在中国投资那么多工厂[得瑟]
去库存得心中有美!美帝良心想[点赞]