
文|大核有料
编辑|大核有料
水陆两栖运动方式兼具水中和陆地的活动能力,因其在滨水环境下独特的机动性能优势,可以迅速完成水陆转换,为现场作业提供了更多便利,具有广泛的应用前景。
传统的水陆两栖运动方式多为轮式车辆与螺旋桨组合或履带式车辆与螺旋桨组合,但是由于水陆介质密度相差过大,尤其在水位不高的浅滩地段,波浪扰动较大,2种运动系统转换过程复杂,导致在该类地段运动性能不高。
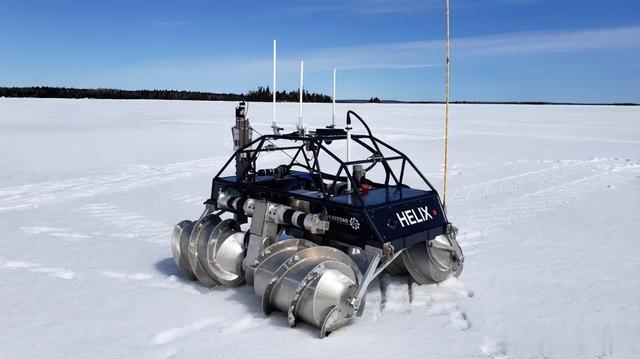
为降低系统复杂性、提高运动效率,近年来对无需进行系统转换的单一系统水陆两栖运动方式的研究逐渐增多。
但螺旋推进运动方式也在沼泽、淤泥、滩涂等半流体环境下表现出良好的适应性,长期受到关注。
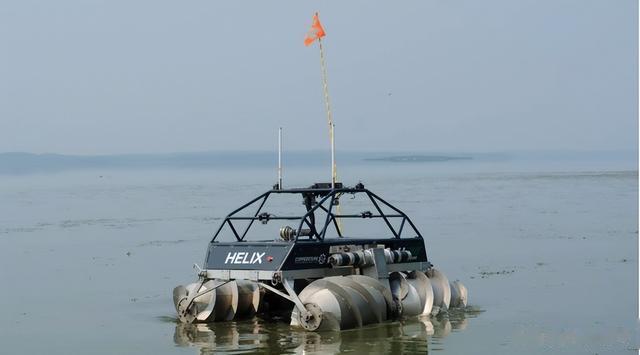
与轮式或履带式车辆相比,螺旋推进的运动原理完全不同,它的支撑作用是通过自身浮力来实现的,而不是通过土壤本身的强度来实现的。
推进能力通过粘性剪切和对介质质量运动的反应来获得,而不是通过与土体的摩擦和黏聚力来实现。
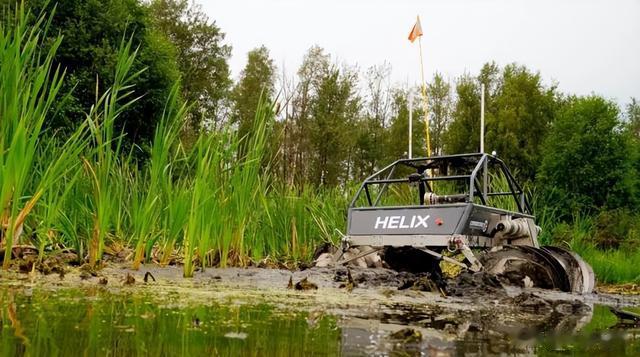
最早使用螺旋推进的载具可以追溯到19世纪。20世纪20年代,螺旋推进被用于陆地上的福特森雪地车,如图1所示,为在冰、雪、泥、沙、沼泽和其他恶劣地形中行驶提供了更多的可能性。
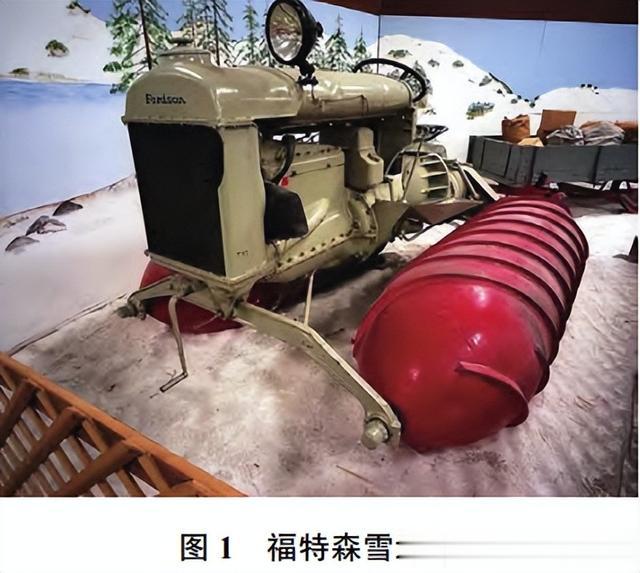
1957年,一家德国公司在汉诺威展览展示了螺旋形水陆两栖车;1965年,美国军方委托克莱斯勒公司开发测试一种用于稻田、沼泽行驶的两栖车辆,如图2所示。
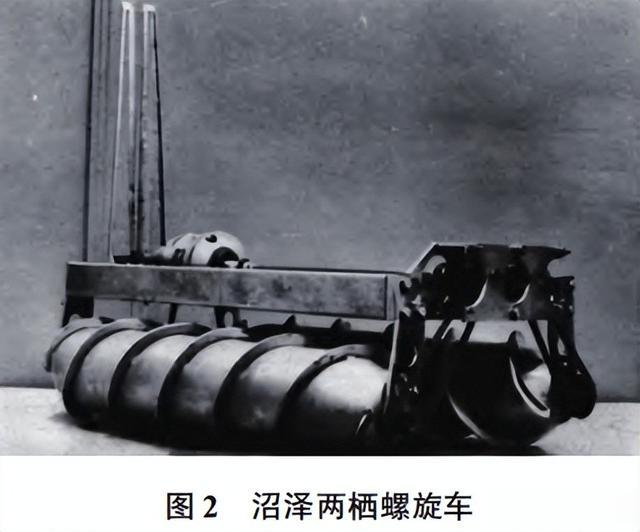
2002年,用于探险的螺旋推进车雪鸟6号被开发并成功穿越白令海峡,如图3所示。
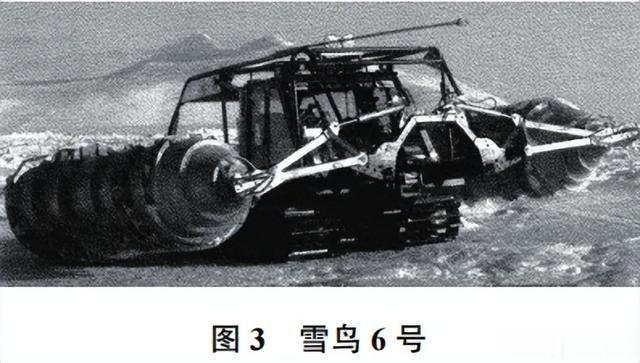
2015年,CopperstoneTechnologiesLtd.开发并使用多种螺旋推进式两栖车辆,配备了一个能携带多个有效载荷的中心控制单元用于岩土工程测量和数据收集,Copperstone的最新设计是HelixNeptune,如图4所示。
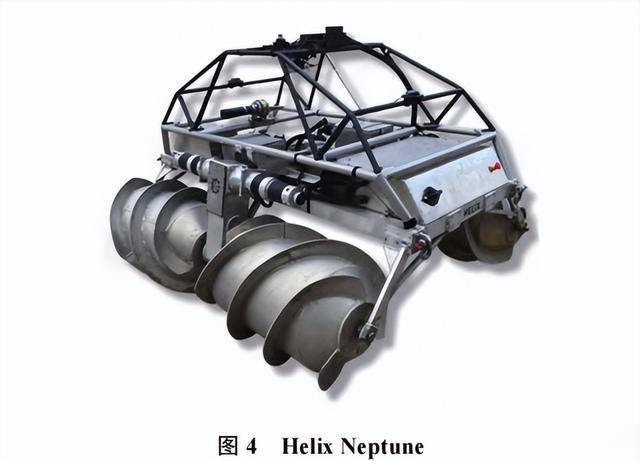
目前为止,螺旋推进在农业、工业和军事等许多领域都有相关的研究设计,但是大多数为载人车型,且几乎都是用于陆地行驶,对其水中性能考虑甚少。
那么水陆两栖机器人,在实际应用中,该怎样优化设计,才能提升其螺旋推进性能呢?
«——【·螺旋推进装置设计·】——»
螺旋运动原理:螺旋筒的运动依靠自身与介质之间的相互作用力来推动自身移动。
如图5所示,在陆地上,螺旋筒旋转时,地面对螺旋叶片产生剪切力,剪切力可分解为一个轴向的牵引力和一个径向的滚动力,从而使螺旋筒移动。
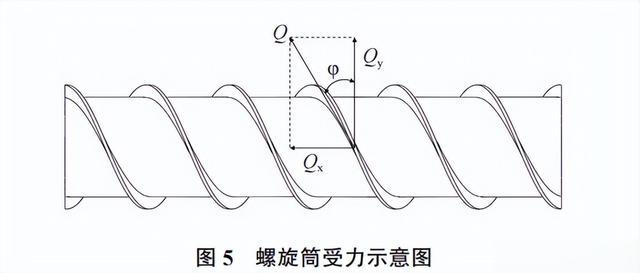
在水中,水对螺旋叶片产生的剪切力小到几乎不计,通过旋转螺旋叶片拨动水流向后,自身受水流的反作用力,从而获得向前的推力。
将两个螺纹相反的螺旋筒组装在一起,将顺时针螺旋筒置于左侧,逆时针螺旋筒置于右侧,通过控制两个螺旋筒的转动方向和转速实现多方向运动。
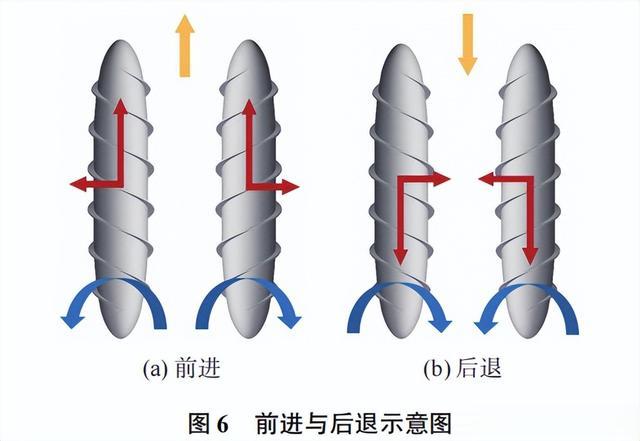
陆地运动:前进与后退,如图6所示,左螺旋筒逆时针旋转,右螺旋筒顺时针旋转,保持两螺旋筒转速相同,二者提供的侧向力相抵消,生成向前的推力,从而形成前进运动。反向旋转即为后退运动。
转向:如图7所示,在陆地上,利用差速转向原理,左螺旋筒逆时针旋转,右螺旋筒停止或顺时针旋转,使左侧转速大于右侧,即可完成向右转弯,反之为向左转弯。
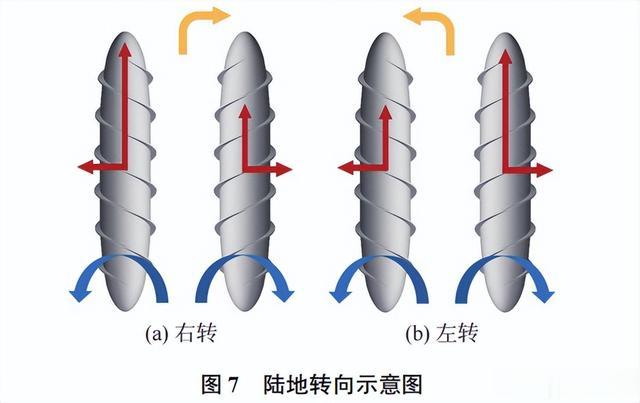
侧向横移:如图8所示,螺旋筒的特性使样机可以侧向移动,使两螺旋筒同时逆时针转动,保持转速相同,即可向左横向移动,反向旋转即为向右横向移动,侧向移动只可在地面实现,在水面无法实现。
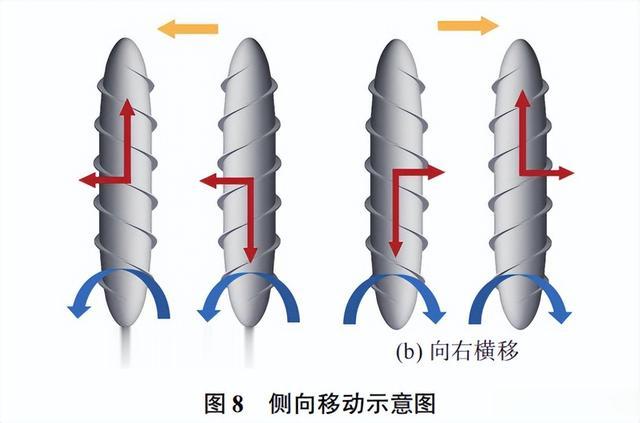
水中运动:前进与后退:螺旋筒旋转方式与陆地前进与后退运动方式相同。
转向:水中同样可利用差速转向原理实现转向。
如图9所示,除差速转向外,使两只螺旋筒同时顺时针或逆时针旋转,即可完成原地转向。
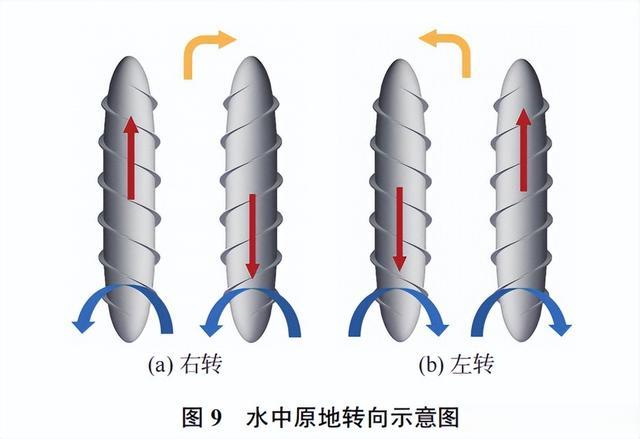
螺旋筒设计:螺旋筒设计参数有螺旋筒直径D、螺旋筒长度L、螺旋线数量a、螺旋叶片高度h、螺旋叶片厚度b、螺旋叶片角度φ、螺距k等,如图10所示为具有参数的螺旋筒示例。
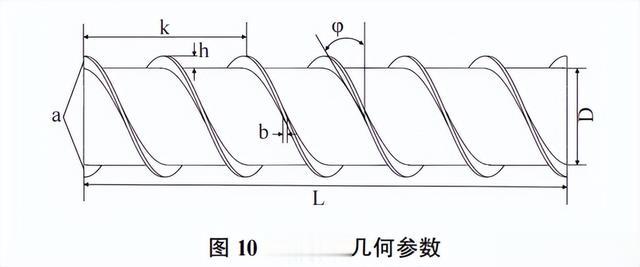
螺旋线采用圆柱螺旋线,圆柱螺旋线可视为一空间点向量绕某一直线进行匀速圆周运动,同时绕该直线进行匀速直线运动的合成结果,其标准方程为:
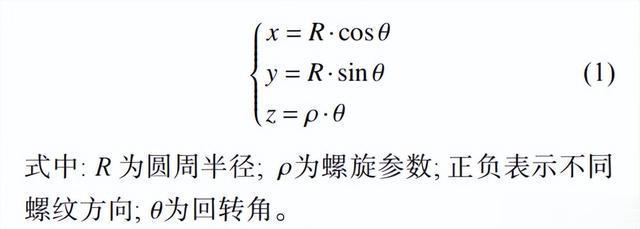
文中所设计螺旋筒长600mm,半径67mm,螺旋叶片高15mm,螺旋叶片厚度10mm,螺距0.2m,螺纹线数量为2。
为减小水中阻力,将螺旋筒主体部分设置为椭球体形,在前后两端设计有端盖,端盖与螺旋筒共形,对螺旋叶片做适当削除处理,在保持叶片高度不变的前提下使其与螺旋筒主体共形,设计如图11所示。
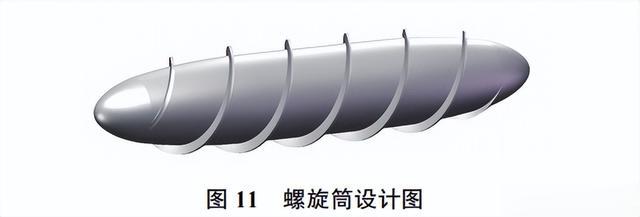
螺旋筒内部设计有中心轴、电池、支撑结构、驱动电机以及齿轮传动机构。其中中心轴从前端盖贯穿至后端盖,两端以插入键的方式固定,在螺旋筒转动过程中始终保持静止;
内置两组电池为驱动电机提供动力,同时平衡单个螺旋筒的重心;
驱动电机与传动机构以齿轮啮合方式连接,带动传动机构旋转从而使螺旋筒旋转,前后端盖保持固定不旋转。
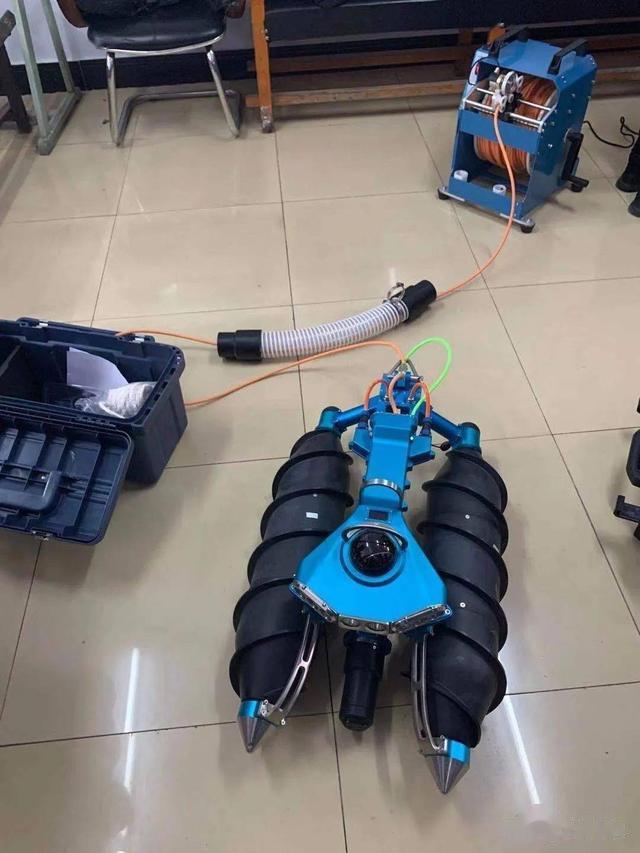
内部结构布置位置通过2种计算确定,一是对螺旋筒开展重浮力计算,确保螺旋筒的重心浮心保持在中心轴对称面中心的铅锤线上;
二是对两螺旋筒以及上部电子舱组成的样机整体开展重浮力计算,确保样机的重心浮心保持在样机对称面中心的铅垂线上。
图12为螺旋筒内部结构图。
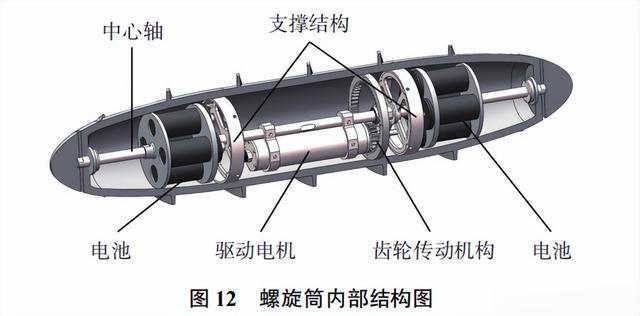
«——【·螺旋筒水动力数值仿真·】——»
数值仿真计算方法:为进一步研究螺旋筒性能,使用计算流体动力学(computationalfluiddynamics,CFD)软件对其展开推力性能计算。
采用雷诺时均纳维-斯托克斯方程作为控制方程,螺旋运动遵守质量守恒方程与动量守恒方程,表示为:
质量守恒方程,流入质量与流出质量之差为控制体流体质量的增量,积分形式为:

在直角坐标系中转化为微分形式:

动量守恒方程,在流体区域内动量的变化率等于作用在该区域的外力总和,表达如下:

螺旋筒的计算域及边界条件如图13所示。
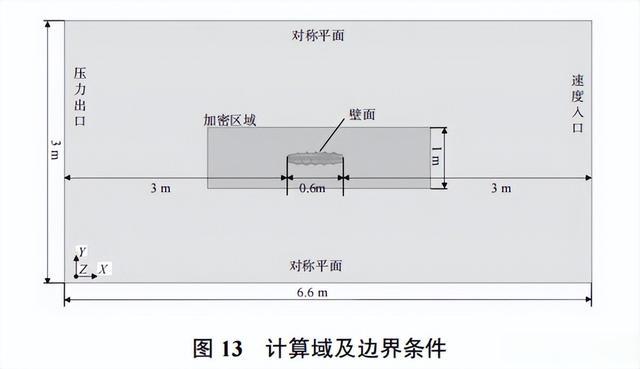
其中:入口边界处和出口边界处各距离螺旋筒5倍自身长度,其他4个面都距离螺旋筒9倍自身最大外径。
右侧面为速度入口,进速为0;左侧面为压力出口,其他面为对称平面,螺旋筒表面为壁面,对螺旋筒周围区域进行加密。
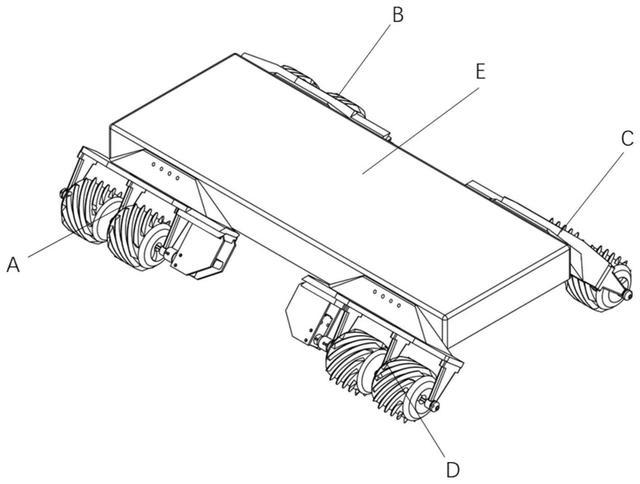
网格划分是水动力计算中比较重要的部分,网格过疏或过密都会影响计算结果,过疏的网格会导致计算结果不准确,过密的网格会使计算量增加,计算难以收敛。
网格划分如图14所示,采用切割体网格进行网格划分,表面网格增长率为1.3,设置全y+壁面处理,壁面表面设4层棱柱层以有效模拟近壁面运动,第1层网格高度0.0025m,棱柱层增长率为1.5,螺旋筒表面y+符合湍流模型的计算要求。
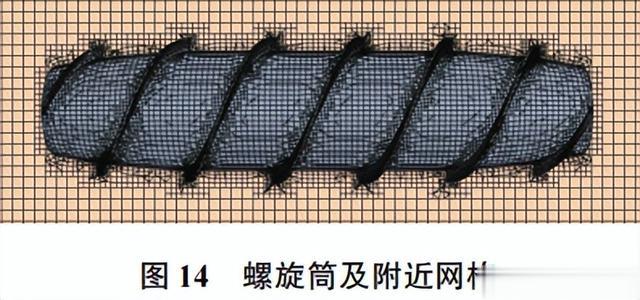
湍流模型使用SST模型,气液交界面求解采用流体体积函数(volumeoffluid,VOF)法,设置螺旋筒绕轴以固定速度400r/min旋转。
进行网格无关性验证,如表1所示。
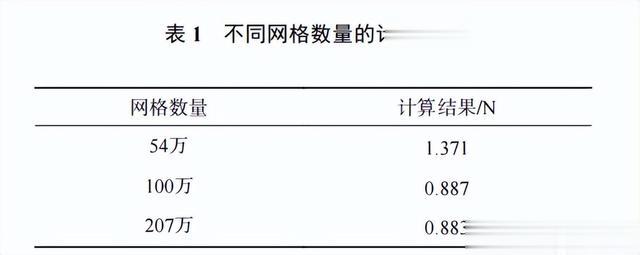
分别设置网格数量为54万、100万、207万,在螺旋筒半浸没状态下计算其推力分别为1.371N、0.887N、0.883N,可以看出当网格数量从100万提升到207万时,对计算结果影响很小,故选择网格数量为100万作为网格划分结果。
分别设置时间步长为0.01s、0.005s、0.001s进行时间步长独立性验证,如图15所示。
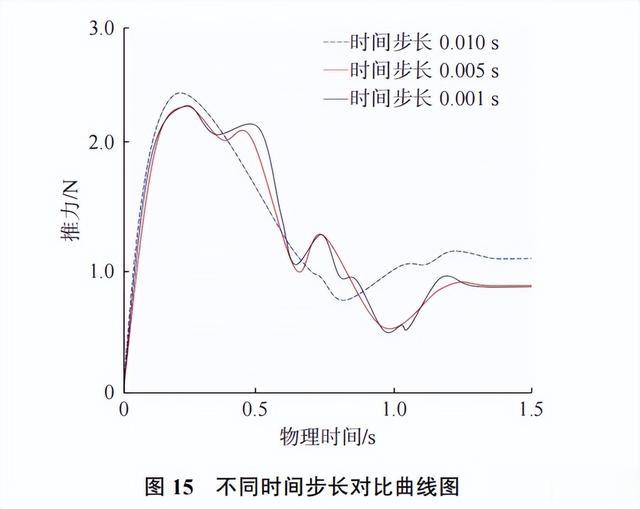
相同物理时间后计算结果分别为1.147N、0.887N、0.881N,可以看出随着时间步长的增加,计算结果逐渐稳定,故选择0.005s作为时间步长,物理时间为1.5s。
不同浸没深度计算结果:由于螺旋筒同时提供浮力与推力,在水中的不同的浸没深度对其性能有显著影响。
为使螺旋筒推进效率最大化,对其不同浸没深度的水动力性能展开计算,表2为计算结果。
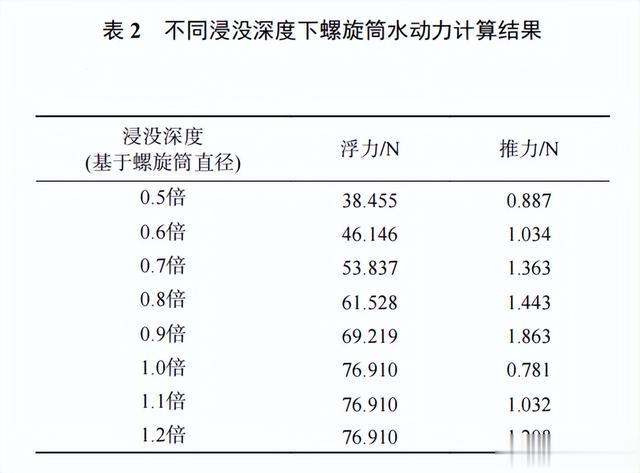
由表可知,在相同转速条件下,螺旋筒产生的推力随浸没深度变化有明显变化。
当螺旋筒未完全浸没状态下推力随浸没深度增加而增加,在0.9倍深度处推力达到最大,故通过更改配重使其保持螺旋筒浸没深度为自身0.9倍处。
«——【·样机水面测试·】——»
样机介绍:自主研制的螺旋推进水陆两栖机器人样机主要由主体电子舱以及左右螺旋筒组成,其中所有电子元件均安装在主体电子舱内进行统一密封,包括全球导航卫星系统(globalnavigationsatellitesystem,GNSS)、惯性测量单元(inertialmeasurementunit,IMU)、电源、控制板、电压转换模块、摄像头、激光器及网络交换机等。
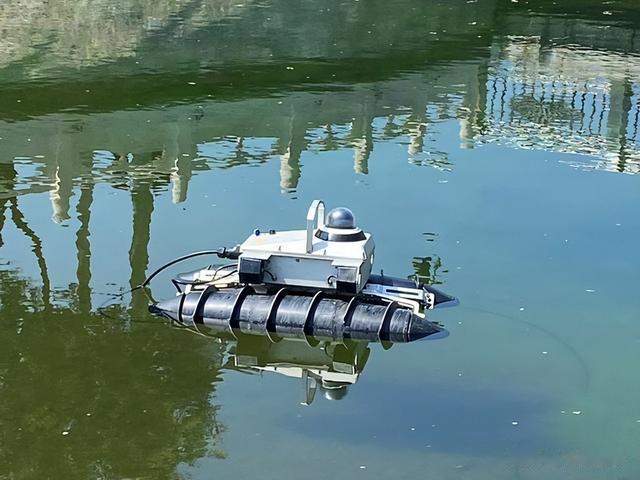
电子舱内部设计从多方面进行考虑,电器方面,基于STM32核心板,开发了小型低功耗通用控制板,作为核心控制模块。
配电系统采用磁开关,可在水下上电,提高了任务适应性。
优化散热设计和大电流供电能力,提升长时间大负载工作状态下的稳定性。同时,优化了元器件排布和整体尺寸,适合狭小的水密舱内部使用。
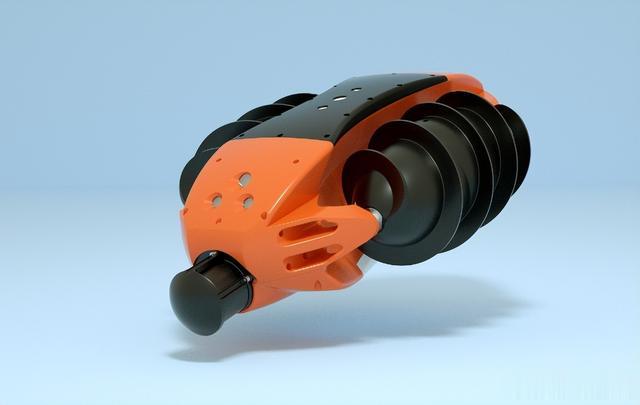
控制系统包括平台上的底层控制系统以及远程的遥测系统两部分,具备遥控和自主2种工作模式。底层控制系统采用vxWorks,通过同步处理机制保证了系统的可靠性。
远端遥测软件主要显示主视角的视频、地图、遥控指令和状态显示。螺旋筒控制系统原理图如图16所示。
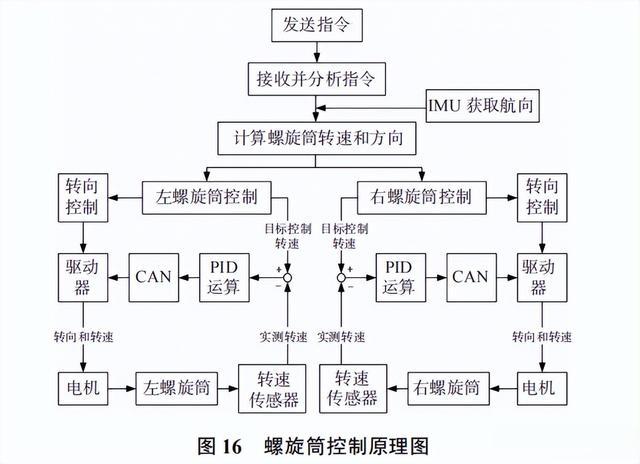
电子舱做水密处理,舱体与舱盖之间为法兰密封。在主体电子舱两侧平行布置2个螺旋筒,为样机提供浮力与推力。
螺旋筒外壳采用3D打印方法,材料为POM,内部支撑结构、中心轴材料为不锈钢。
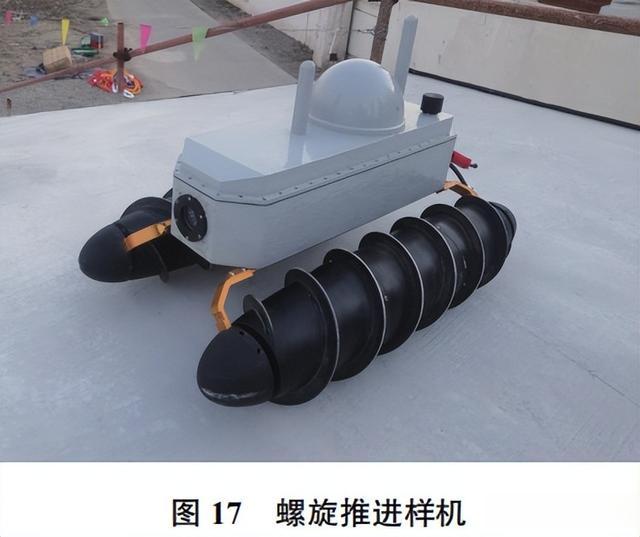
研制样机如图17所示,相关参数见表3,电子舱硬件仪器型号见表4。
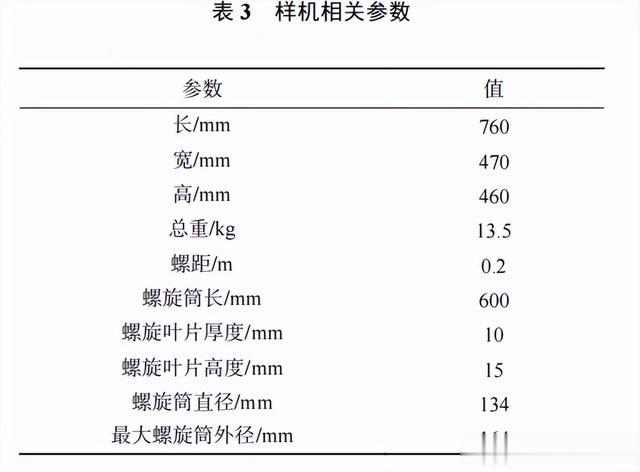
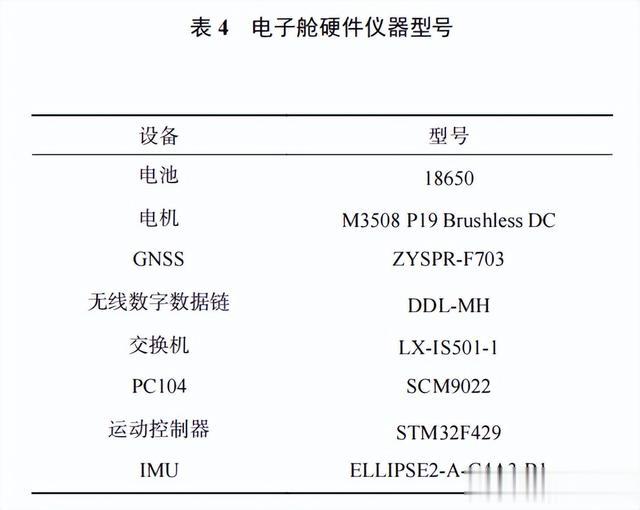
水中测试:在南京的大堰水库对样机开展水上行驶测试,包括直线往返测试以及定向自主导航测试等。在直线往返测试中,样机以1kn的平均速度行驶了2.5km,最大航速可达2kn。
在自主导航测试中,在上位机软件内规划目标点,使样机绕目标点进行自主避碰导航,航行轨迹如图18中黄色部分所示。
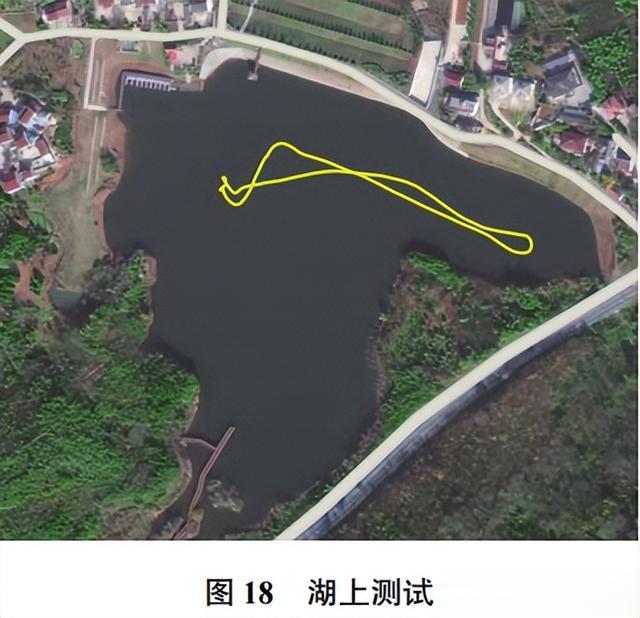
测试结果表明该装备在水上行驶时具备良好稳定的行进姿态,如图19所示。
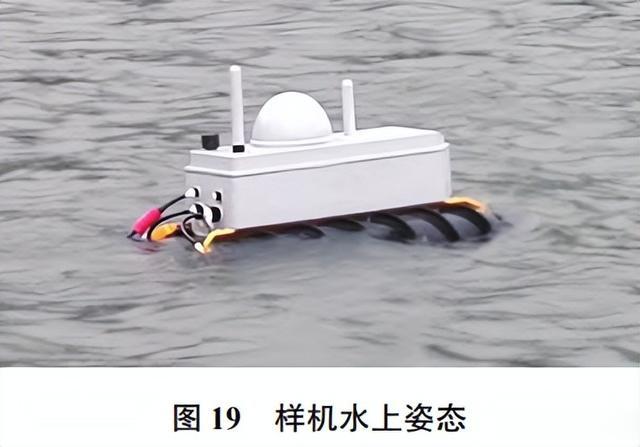
«——【·螺旋推进性能优化设计·】——»
根据样机测试结果,发现该尺寸下的螺旋筒推进能力较弱,在较为平静的水域可以自由行驶,但是在较大风浪环境下难以克服波浪实现自由运动。
为提高螺旋筒推进能力,提升推进效率,对螺旋筒开展优化设计工作。

除螺旋筒基本设计参数以外,影响其推进效率η的因素还有转速n、外部介质等,综合考虑上述因素对推进效率的影响,将螺旋叶片高度h以及螺距k作为变量,保持螺旋筒其他基础参数不变,设转速n=400r/min,选取水为介质,根据水动力仿真计算结果推力F和扭矩T,寻找最大推进效率。
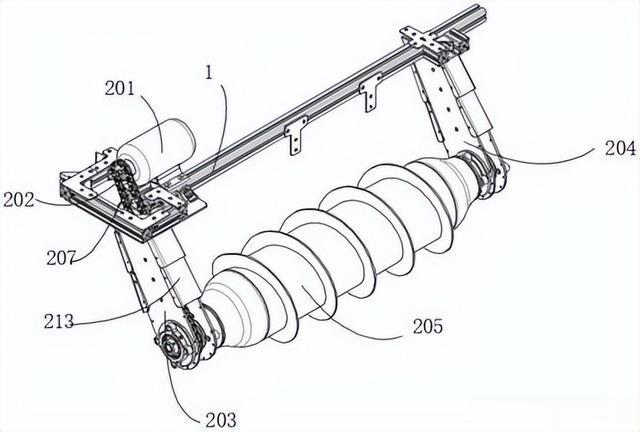
响应面法是通过多元线性回归的方法,对设计样本进行试验设计,拟合出响应值与多个相关因素之间的函数关系,进而可以直观的寻求最优的设计参数。是一种能够解决多变量问题的综合了试验设计和数学建模的优化方法。
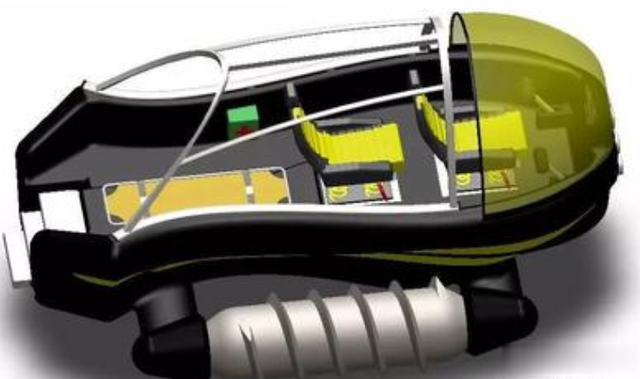
在工程优化设计过程中,使用响应面法除了可以获得响应目标和参数变量之间的不同变化关系,而且无需完整运行所有求解过程就可以获得近似结果,获得最优计算结果,在过去的十几年中,响应面法在结构优化设计等方面已有了迅速的发展的应用。
建立优化模型如下:

式中,电机最大持续扭矩T=2.8N·m。
由于还没有明确的表达螺旋筒推进效率的公式,将螺旋筒的推进效率计算方法近似为螺旋桨的推进效率计算方法,推动螺旋筒旋转所需功率为:

螺旋筒产生的有效功率为:

式中:T为螺旋筒扭矩;ω为角速度;F为螺旋筒推力;v为螺旋筒前进速度,则螺旋筒推进效率:

使用CFD软件对螺旋筒进行优化分析主要分为两个部分。
在软件内绘制螺旋筒的几何模型,输入模型后对其开展预处理,设置好物理模型、边界条件等,对模型进行网格化处理,随后开展水动力仿真计算;
根据仿真计算结果建立螺旋筒优化目标,输入响应值和变化参数形成系列设计研究算例,通过对计算结果进行后处理与分析,拟合构造3D响应曲面,随后寻得最优解。
整体优化流程如图20所示。
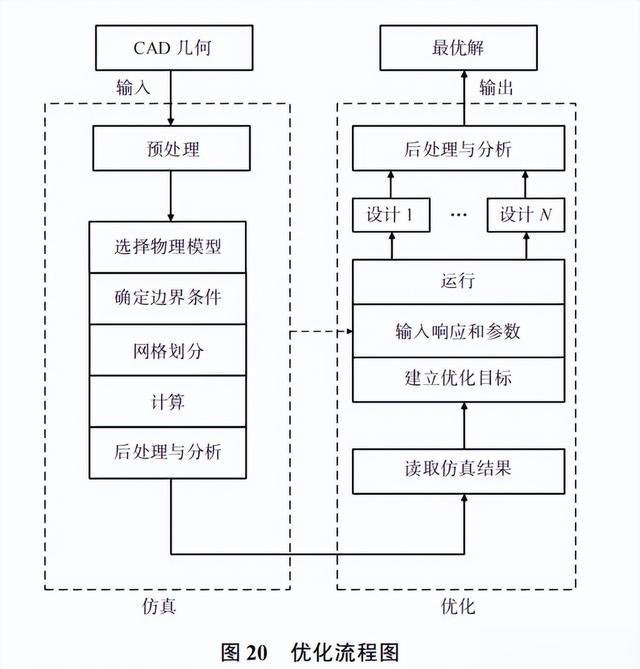
为方便调整参数进行计算,以圆柱形螺旋筒为基础构型。
在CFD软件内绘制模型并对其进行预处理,设置计算域、边界条件和湍流模型等与上述相同,使用重叠网格方法计算螺旋筒速度,将整体划分为背景区域和重叠区域并分别进行网格划分。
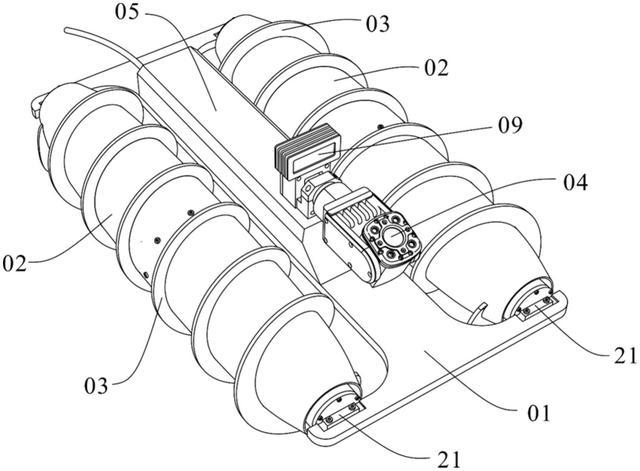
因本次优化目标为提高推进效率,为提高计算精度,减少时间成本,故不作两相流处理,流体介质只设水。
给定螺旋叶片高度参数变化区间为[15mm,25mm],参数间隔2mm;给定螺距参数变化区间为[200mm,300mm],参数间隔20mm,计算结果见表5。
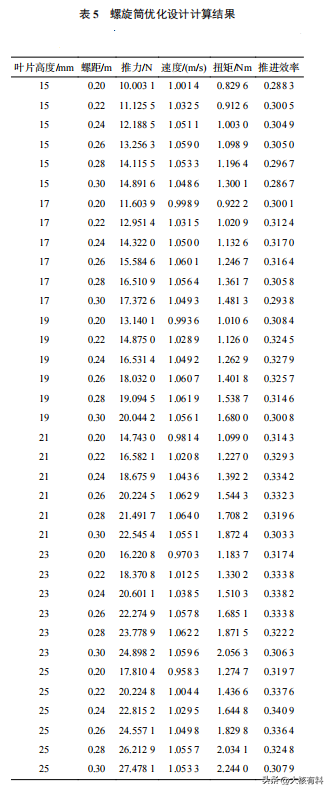
图21~图23为不同目标参数随基本因素变化的响应曲面,由响应曲面结果可以得知,螺旋筒推力F随螺距k和螺旋叶片高度h增大而增大;
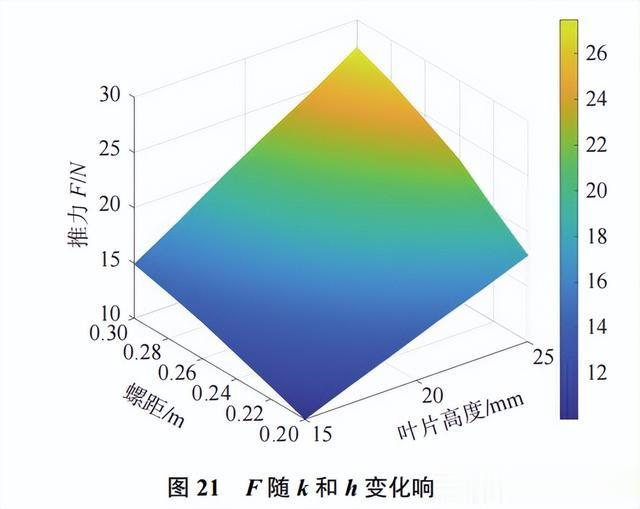
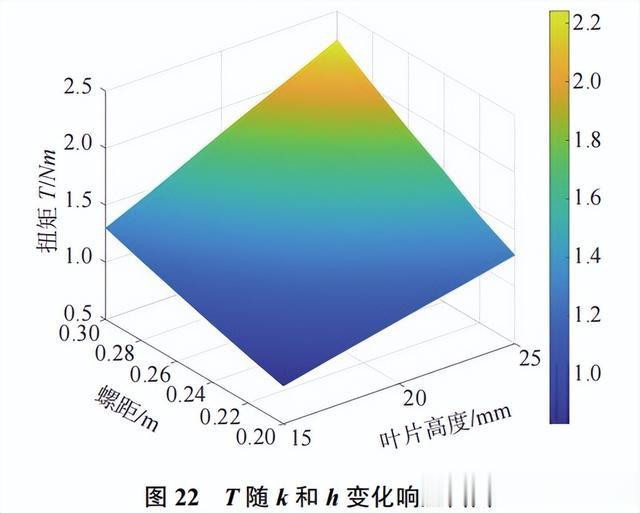
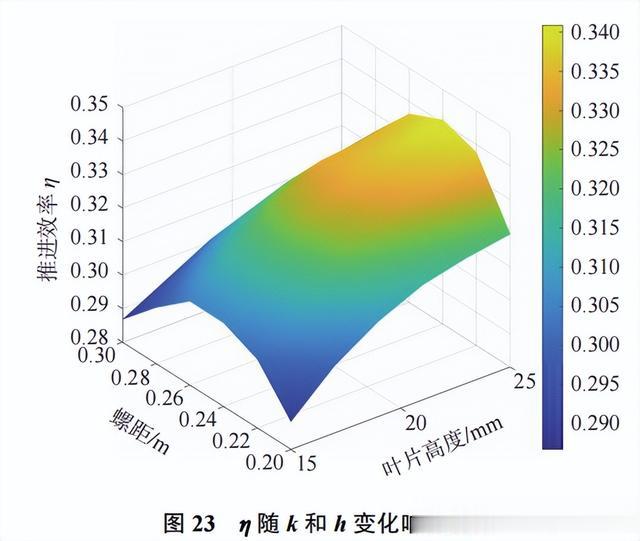
螺旋筒扭矩T随螺距k和螺旋叶片高度h增大而增大;在螺距k和螺旋叶片高度h变化区间内,螺旋叶片高度25mm,螺距0.24m时,推进效率η达到极大值,该组参数即为参数区间内最优结果。
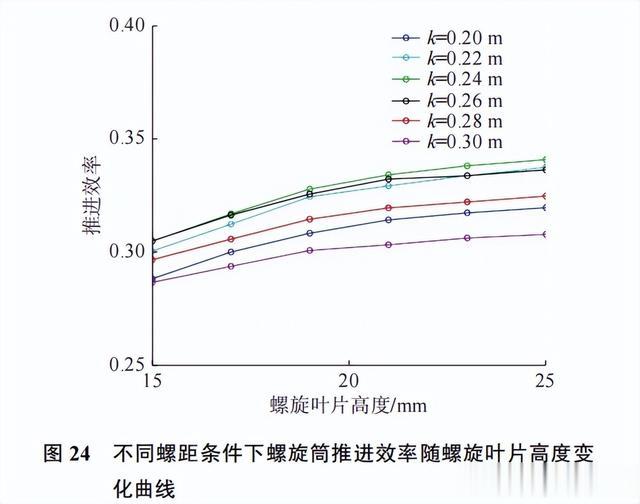
图24、图25为螺旋筒推进效率η随单一参数变化曲线。由图24可知,保持螺距不变,推进效率η随螺旋叶片高度增大而增大,且近似为二次函数关系;在螺距为0.24m时推进效率优于参数区间内其他值。
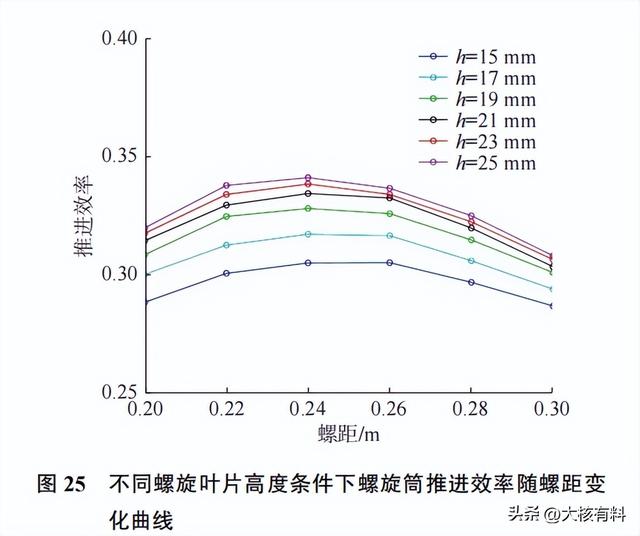
由图25可知,保持螺旋叶片高度不变,推进效率随螺距的增大先增大再减小;螺旋叶片高度越大,推进效率越高。
根据优化目标,选择具有最大推进效率的参数作为优化结果。
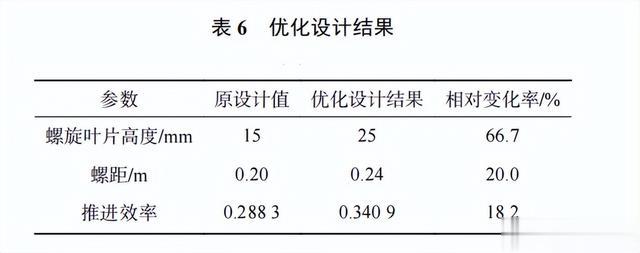
表6为螺旋筒参数的设计优化结果。与原设计方案对比,新的优化方案将推进效率提升了18.2%。
«——【·结语·】——»
该款水陆两栖螺旋推进机器人,掌握了螺旋推进的原理和螺旋筒的设计方法,发现了螺旋筒在0.9倍浸没深度时具有最大的推力。
通过水中测验验证了螺旋筒在水中行驶时具有良好的行驶姿态以及实际工程应用价值。
从提高螺旋筒水中推进效率角度看,存在一组设计参数可使得推进效率最佳。
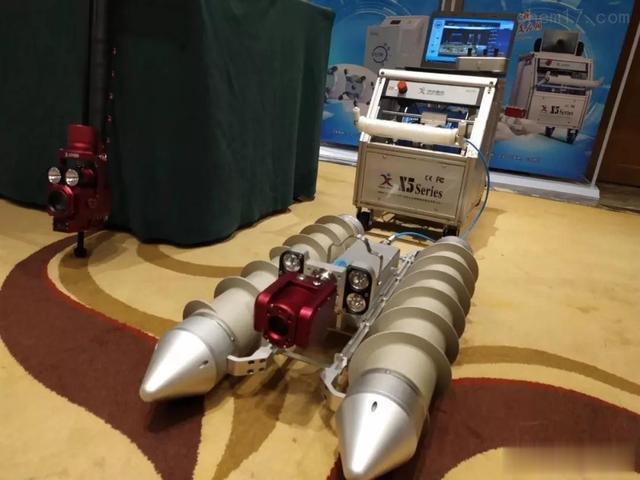
在一定区间范围内螺旋叶片高度越大,推进效率越高;螺距对推进效率的影响较为复杂,需通过数据仿真确定其最佳数值。
螺旋筒其他因素对水中螺旋推进性能的影响仍需进一步的研究,水中环境仅是对螺旋推进性能研究的一部分,后续需要在湿地、滩涂、沼泽等水陆两栖环境开展试验,对螺旋筒推进性能进行进一步研究分析。