

摩擦是在两个实体相对运动时产生的力的阻碍。摩擦会导致机械设备的磨损和故障,因此有效减少摩擦和控制磨损,对于机械设备性能和国民经济的改善至关重要。
润滑剂是一种有效的方法来控制机械设备的摩擦和磨损。传统方法是添加液体润滑油作为润滑剂,以达到抗磨损和抗摩擦的效果。然而,在微尺度摩擦条件下,传统润滑剂已经显示出一些局限性。
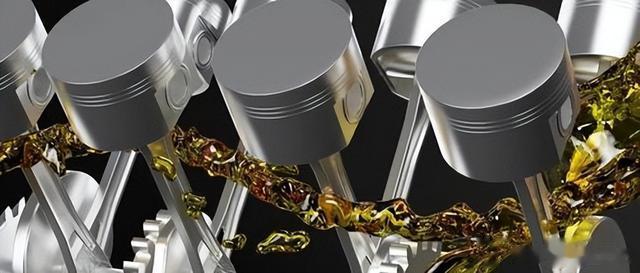
研究和应用二维材料和纳米摩擦学等新技术,在摩擦控制领域具有重要意义,有望为常规技术和工程领域带来更好的性能和效果。
我们主要研究基于物理和化学方法的石墨烯在500N基础润滑剂(粘度指数为99 mm2 s−1)中的分散稳定性、抗磨和抗摩擦性能。
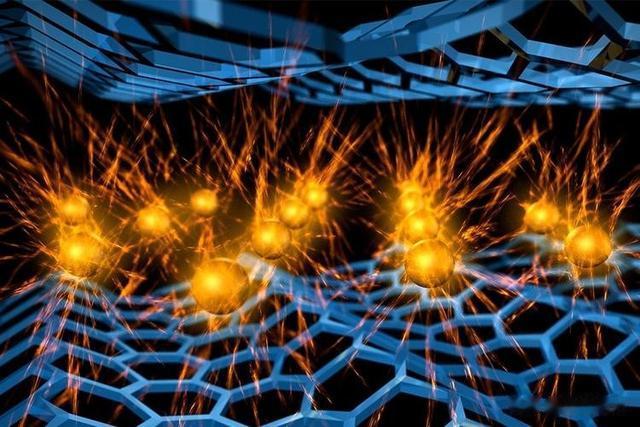
尽管石墨烯能有效减少摩擦和磨损,但其在介质中的不溶性和聚集倾向是处理石墨烯作为纳米填料时遇到的两个主要问题,这将导致石墨烯与聚合物界面之间的相互作用减弱。目前,改性石墨烯表面是提高分散稳定性的一种更有效的方法。
因此,我们采用油酸和硬脂酸对石墨烯表面进行改性,将改性后的石墨烯分散在润滑油中作为溶剂,以测试其分散性和摩擦学性能。
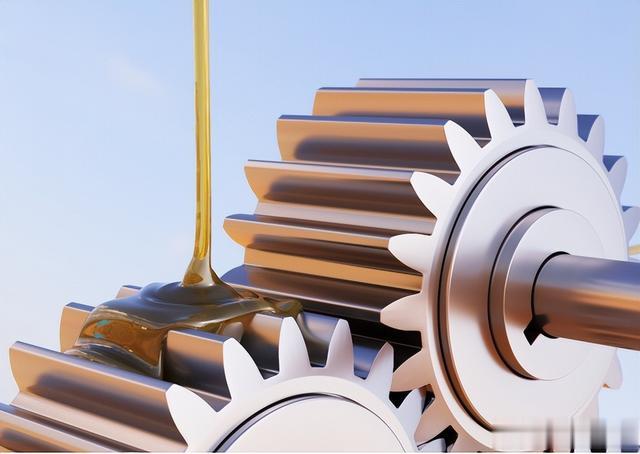
1.分散稳定性评价方法
分散性是指石墨烯添加剂在一定的分散条件下,能够均匀地分散在润滑油中的特性。稳定性是指在一定粒径下,石墨烯添加剂能够在润滑油中形成稳定的悬浮液,并且在长时间内保持悬浮稳定的特性。
通过对比分析(参见下图),对于化学方法制备的石墨烯,当沉降时间为6天时,分散体开始出现分层现象,润滑油的颜色发生明显变化,并且出现明显的白色浮冰。

随着沉降时间的延长,化学石墨烯分散体的表观析出现象变得更加严重。而采用物理方法制备的石墨烯分散体的颜色基本保持稳定,在静置20天后仍然保持黑色。
紫外-可见光谱如下图所示,显示了两种石墨烯分散体在300–800 nm吸光度范围内的变化情况。可以观察到不同分散体的吸光度曲线呈现一致的变化趋势,即随着沉降时间的增加,吸光度逐渐降低。
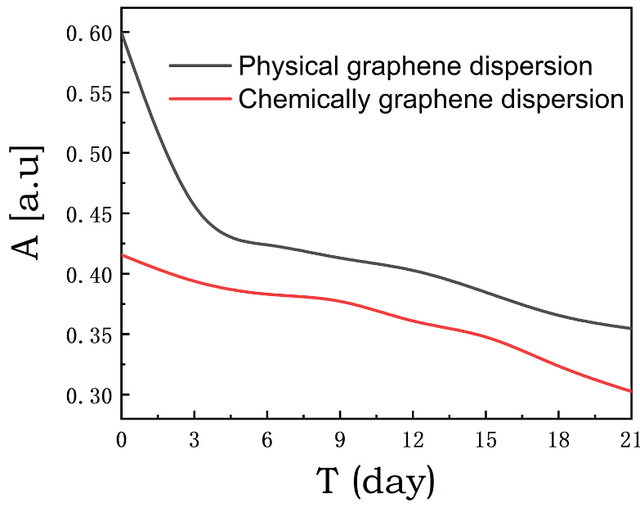
物理法石墨烯分散体的吸收值高于化学石墨烯,这表明物理法石墨烯更容易分散在润滑油中,其分散稳定性更高。这可能是由于化学石墨烯在制备过程中的结构受损,导致其分散性较差。
在本实验中,还研究了石墨烯色散吸收值随波长的变化。从下图中可以观察到,石墨烯色散的吸收值随着波长的增加逐渐稳定。
对于物理法石墨烯分散体,吸收值趋于稳定在400nm的波长,特别是从第三天开始。第一天的吸收值高于波长范围内的其他几天。
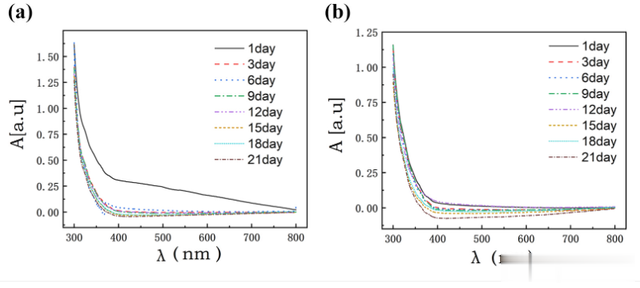
化学石墨烯分散体每天的变化曲线在400nm处接近,吸收值趋于稳定。
2.摩擦学测试结果分析
石墨烯材料的润滑机理一直是积极研究的热点。理论研究表明,石墨烯纳米片在铁表面的化学吸附与润滑膜的形成有关。
当上下摩擦副相互运动时,层状纳米片之间发生滑移。石墨烯直接作用于基体表面,然后与金属基体发生摩擦化学反应,形成碳质材料的润滑膜,从而防止摩擦副直接接触,减少材料的摩擦和磨损。
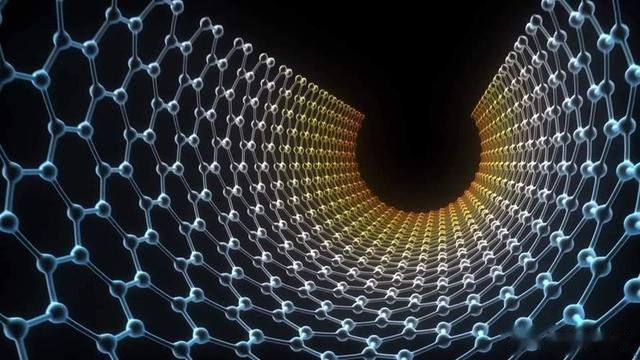
在我们的研究中,我们对未改性和改性石墨烯分散体在392 N负载下的润滑效果进行了研究。下图显示了在不同时间下,纯基础油与改性石墨烯分散体,以及未改性石墨烯分散体之间的摩擦系数。
由于摩擦系数受多种因素的影响,如法向载荷大小和速度、摩擦副的刚度和弹性、滑动速度、摩擦面接触的几何特性以及滑动过程中表面层的物理性质等,因此会出现不规则的摩擦振动。

从图中可以清楚地看到,改性石墨烯的摩擦系数大大降低。相反,从图(b)可以看出,未改性分散体的摩擦系数高于纯基础油的摩擦系数。这是因为未修饰和未破碎的石墨烯颗粒已经凝聚在一起。
随着摩擦的进行,这些凝聚物充当了磨料颗粒的角色,使润滑油膜变得不连续,进而导致磨损增加。
相比之下,在制备过程中,改性的石墨烯分散体的结构得到了改善,中间体中获得的氧化石墨烯表面含有一定的含氧基团,赋予了其表面更多的活性特性。
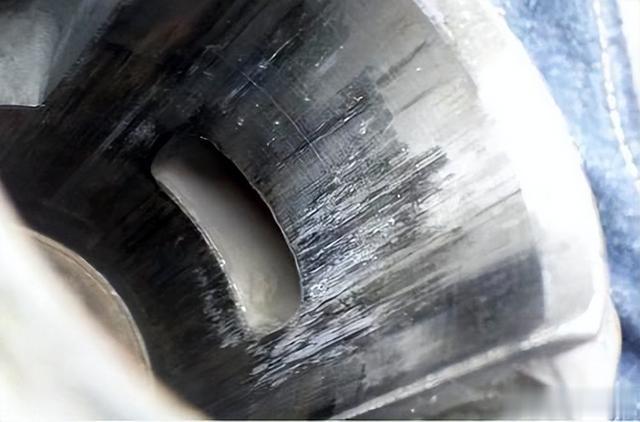
这些特性使改性的物理石墨烯颗粒更容易与润滑油接触。在本实验中,改性的物理石墨烯表现出了良好的润滑效果,并在整个测试过程中保持了稳定的性能。
其平均摩擦系数保持在约0.07左右,相比未改性石墨烯分散体降低了约26%,最低摩擦系数达到了0.0677。
根据上述测试结果,实验开始时摩擦系数的增加与磨合过程有关。摩擦金属表面的初始粗糙度导致摩擦力暂时增加,直到表面变平并变得光滑,从而减少摩擦。
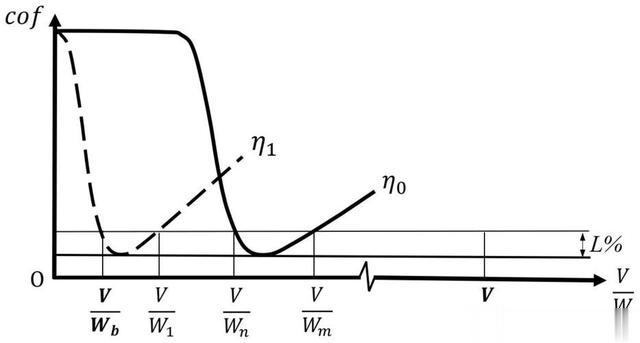
与纯基础油相比,石墨烯作为润滑油添加剂可以更有效地提高润滑油的耐磨性。
据推测,作用机理如下:对于纯基础油,在摩擦的初始阶段,油膜在摩擦副之间分散不均匀,这可能导致摩擦副直接接触,因为摩擦系数大,润滑油随时间增加。
然而,随着摩擦的继续,摩擦副之间形成油膜以保护它,因此此阶段的摩擦系数保持在相对稳定的状态。
当在基础油中加入一定量的未改性石墨烯时,石墨烯片可以很容易地进入接触面之间并形成保护层,这使得油膜在摩擦过程中仍然起着重要作用。
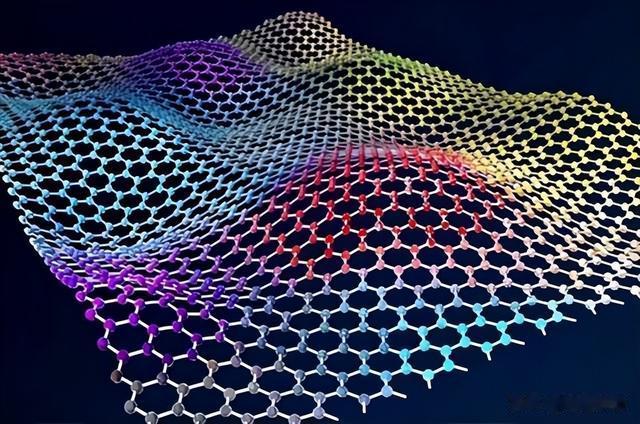
此外,摩擦过程中形成的石墨烯碎屑,还可以填充接触面上的磨损疤痕并承受部分载荷,从而减少磨损和增加承载能力的效果。
然而,未改性石墨烯颗粒和金属磨损碎屑可能会团聚并使接触表面粗糙,从而降低润滑油的耐磨性。
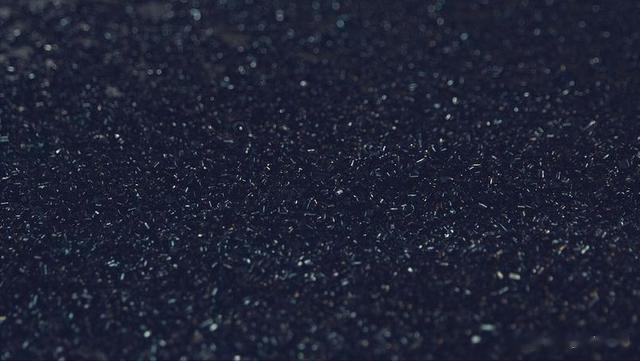
3.磨损表面表征
通过SEM和能量色散光谱(EDS)对磨损痕迹的研究,进一步揭示了石墨烯分散在钢球上的磨损表面特性和抗磨机理。
如图(a)、(b)、(c)、(d)和(e)所示,分别展示了纯润滑、未改性物理法石墨烯分散液、改性物理法石墨烯分散液、未改性化学法石墨烯分散液和化学石墨烯分散液后钢球表面的磨损点。
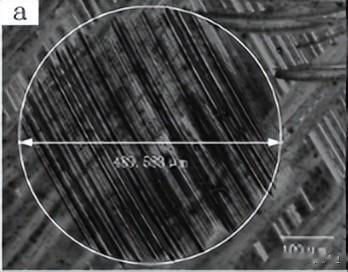
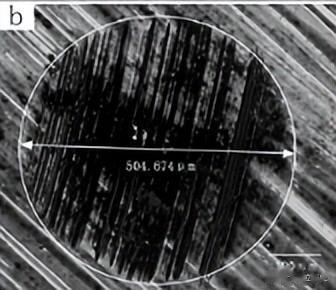
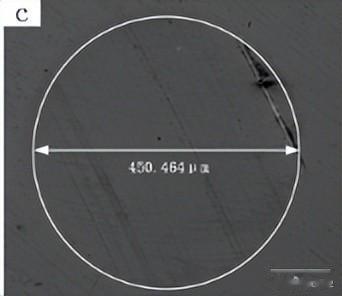
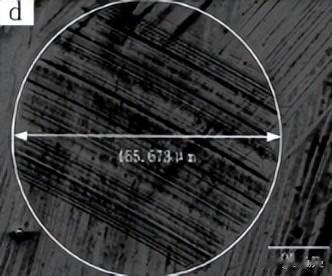
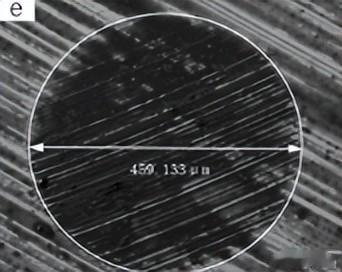
图(a-1)至(e-1)显示了放大的磨损疤痕,图(a-2至e-2)和(a-3至e-3)则显示了选择的点和区域的EDS频谱图。
在摩擦试验后,钢球表面出现明显的磨损痕迹,表现为明显的犁削效果、变形痕迹和众多划痕。

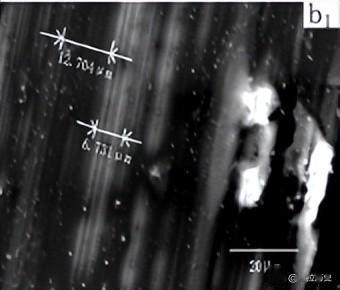
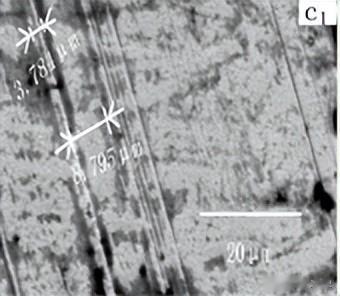
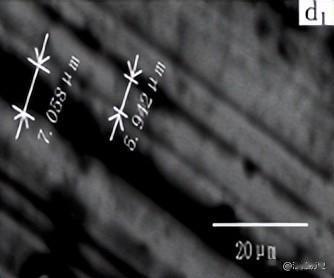
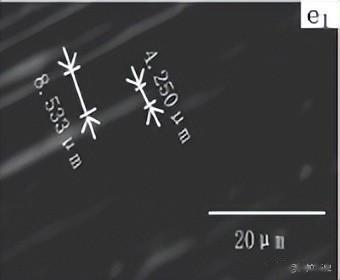
具体来说,对于纯润滑情况下,磨损痕迹较为明显,而未改性的物理法石墨烯分散液也显示了一定的磨损效果。
下图显示了磨损点直径的直方图。更直观地看到,在改性石墨烯分散体的作用下,钢球表面的磨损疤痕直径比纯基础油作用下的钢球表面的直径低8.0%,与未改性的物理石墨烯相比,钢球表面的磨损点直径降低了10.7%。石墨烯分散体的作用。
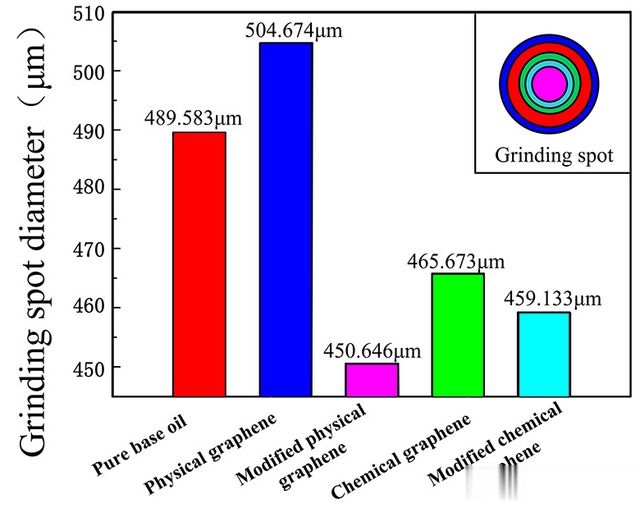
从图(a-1)到(e-1)可以看出,磨损痕迹的SEM显微照片显示磨损痕迹中有许多深槽和凹坑。摩擦表面上的暗区清晰可见,这可能是由于石墨烯颗粒的摩擦膜的形成。
通过磨损表面内部的EDS分析(图(a-2至e-2)和(a-3至e-3)),确认薄膜形成被确认为磨损表面上碳浓度的增加。
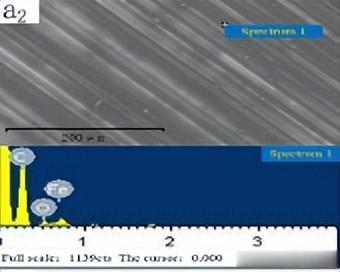
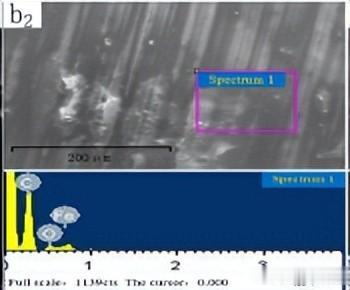
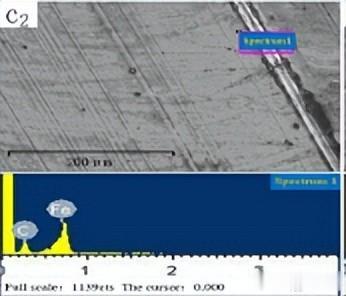
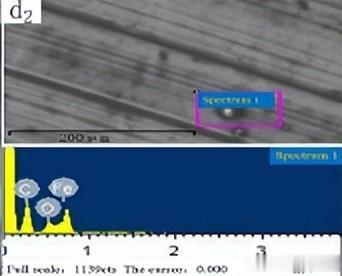

这一结果证明,石墨烯颗粒的增加导致润滑的增加,改性的石墨烯颗粒可以稳定地吸附在摩擦表面上,在摩擦表面上迁移形成物理沉积膜,并提供较低的剪切强度,导致层间滑动,从而提高摩擦副表面的耐磨性。
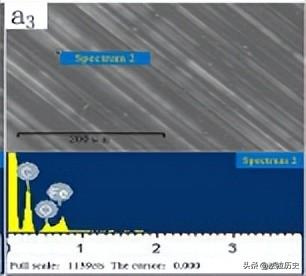
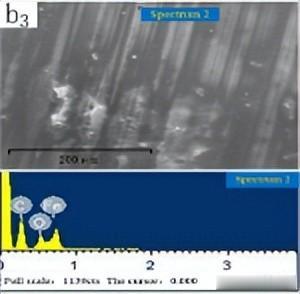

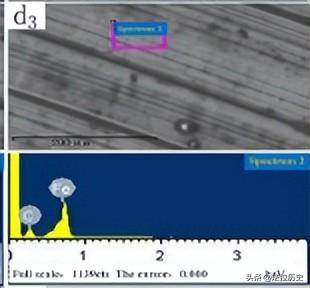
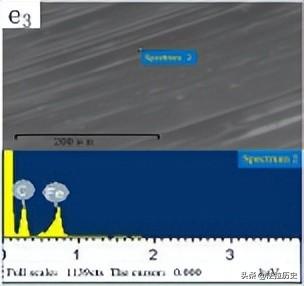
化学氧化还原过程主要通过在石墨烯边缘形成羧基和羟基等含氧基团来进行。同时,在石墨烯的层间插层过程中,也会引入环氧基或羰基等含氧基团。
这个过程可以扩大石墨烯层间距,使得在外力作用下容易剥离,从而得到氧化石墨烯。虽然该方法得到的产物收率较高,设备相对简单,但是反应时间较长且石墨烯结构容易遭到严重破坏。
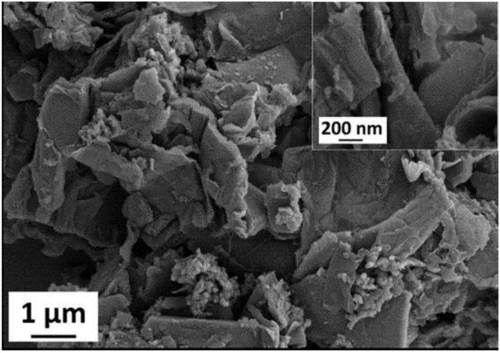
另一方面,物理液相汽提法制备的石墨烯是一种本征石墨烯材料,没有任何物理化学性质的添加。因此,这种方法得到的石墨烯质量较高,非常适合进行理论研究。
这也是相比于化学方法,物理方法获得的石墨烯分散体在摩擦学性能方面具有优势的重要原因。
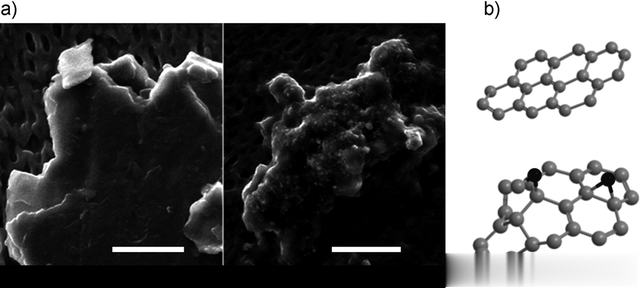
本实验研究了两种不同制备工艺对石墨烯分散体的分散稳定性和摩擦学性能的影响。结果表明,改进的物理方法石墨烯分散体表现出最佳的抗磨损和抗摩擦性能,其摩擦系数最低。
在扫描电镜下观察到了明显的润滑效果。这是因为通过氧化还原法得到的氧化石墨烯表面含有一定的含氧基团。
这些含氧基团具有特殊的特性,例如表面活性,导致所得石墨烯具有较大的结构缺陷和接触面积。

因此,在界面原子重新分布、最外层表层的重建以及界面纳米结构的原位形成时会发生,进而影响了其润滑性能。
由于润滑状态的稳定性与环境气体的特性密切相关,因此研究碳-金属表面与气态物质之间的摩擦化学相互作用对于纳米摩擦学的发展非常重要。

深入研究材料摩擦磨损过程中表面和界面上发生的化学反应,对于在微观或分子和原子尺度上探索材料的磨损机理具有重要意义。
这些研究有助于更好地理解材料的摩擦学性能,并为纳米级润滑剂的设计和应用提供了有益的参考。
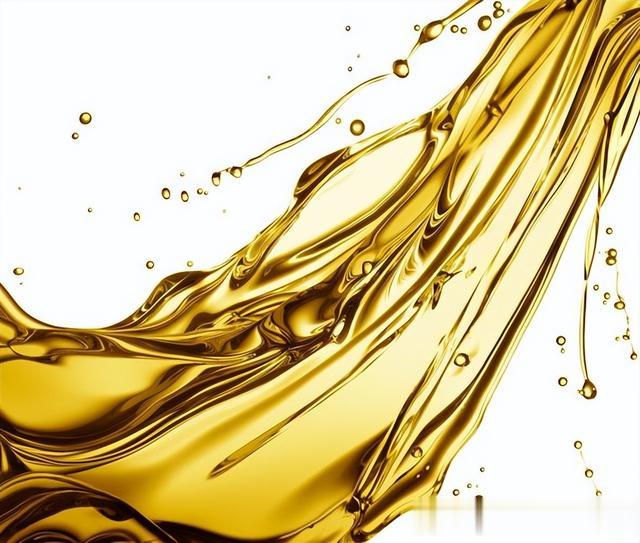
1.温思, 黄平. 摩擦学原理.霍博肯:约翰·威利父子,2012年。
2.郑琪, 韩斌, 崔鑫, 等.石墨烯工程胶凝复合材料:小而大的影响。纳米纳米技术 2017;7: 1–18.
3.刘毅, 格雷F, 郑琪.石墨烯的高速滑动摩擦和新颖的途径是持久的超润滑性。科学代表 2014;4: 4875.
4.范旭, 夏茹, 王玲, 等.多层石墨烯作为本通润滑脂中的润滑添加剂。特里博尔莱特 2014;55(3): 455–464.
5.王杰, 郭鑫, 何莹, 等.不同接触形式下石墨烯作为润滑脂添加剂的摩擦学特性.部落国际 2018;127: 457–469.