先进封装铜-铜直接键合技术的研究进展
张明辉 高丽茵 刘志权 董伟 赵宁
大连理工大学材料科学与工程学院 中国科学院深圳先进技术研究院 深圳先进电子材料国际创新研究院
摘要:
在后摩尔时代,先进三维封装技术成为实现电子产品集成化、小型化的重要出路。应用于封装互连的传统无铅锡基钎料由于存在金属间化合物脆性、电迁移失效、制备工艺限制等问题,已不再适用于窄间距、小尺寸的封装。金属铜的电阻率低、抗电迁移性能好,其工艺制备尺寸可减小到微米级且无坍塌现象。铜−铜(Cu-Cu)直接互连结构可以实现精密制备以及在高电流密度下服役。对Cu-Cu键合材料的选择、键合工艺的特点及服役可靠性的相关研究进展进行了总结。
1引言
人工智能、自动驾驶、5G网络、物联网等新技术的发展和应用对先进电子封装提出了更高要求。在此背景下,将多颗芯片在垂直方向堆叠互连的三维(3D)封装技术快速发展。3D封装具有微型化、低RC延迟、高传输速率、高带宽、利于异构集成等优点,成为延续摩尔定律的良好解决方案。3D封装使用微凸点及硅通孔技术(TSV)实现芯片与芯片、芯片与转接板之间的互连。目前,传统的微凸点互连材料为无铅Sn基钎料。但随着微凸点尺寸及间距的减小,Sn基钎料存在的电迁移、热迁移、金属间化合物(IMC)、桥连短路等可靠性问题加剧,亟需更好的替代方案。
铜-铜(Cu-Cu)直接键合属于金属-金属键合,在一定键合工艺条件(温度、气氛、压力等因素)下,Cu原子相互扩散实现互连键合。由于Cu的电阻率低、抗电迁移性能好,其工艺制备尺寸可减小到微米级,Cu-Cu键合成为取代钎料微凸点进行芯片级垂直互连的良好解决方案。2019年,索尼公司研发团队在Ⅲ-Ⅴ InGaAs/InP层与Si层间采用Cu-Cu键合技术,有效地减小了图像传感器产品尺寸、提高了分辨率,将像素密度提高4倍,并在单芯片上实现短波红外和可见光成像,实现数字输出。由此可见,Cu-Cu直接键合是实现3D封装制造的关键技术,并具有广阔的应用前景。
要实现高强度且可靠的键合,最为关键的影响因素是金属键合前接触面的表面状态以及键合过程中的原子扩散速率。此外,由于集成电路后道工艺(BEOL)的热预算、晶圆翘曲、偏移等问题,Cu-Cu直接键合应在较低的温度及压力下制备,并保证高可靠性及批量制造。这就要求金属在键合前的表面具有粗糙度较低、表面清洁度较高、无氧化层以及原子传输速率快等特性。目前,Cu-Cu键合技术已得到研究者们的广泛关注,大批研究者针对提高Cu-Cu键合效率及键合质量等问题展开了相关研究工作。本文对适用于Cu-Cu键合的Cu基体组织性能研究、Cu表面处理以及关于Cu-Cu键合工艺改进的国内外相关研究现状进行了介绍。
2适用于Cu-Cu键合的Cu基体组织性能研究
金属间的键合界面在压力作用下产生塑性变形,使界面相互接触并在高温下蠕变扩散,原子逐渐由接触区向孔洞区扩散,最终实现完整的界面连接。界面质量可以根据键合后的界面状态分为3类:(1)失效键合;(2)可见界面的成功键合;(3)不可区分界面的成功键合。Cu原子的扩散行为直接影响到键合效率及键合质量。多晶Cu基体需要在400 ℃高温下才能实现扩散键合。此外,金属Cu在含氧气氛中十分活泼,极易被氧化。多晶Cu基体在氧气气氛下,在200 ℃时效,30 min后其氧化膜厚度为50 nm左右。而当时效温度升高至250 ℃,其氧化膜厚度可达560 nm。较厚的氧化层将阻碍Cu原子的扩散,影响键合强度和电热传输性能。众所周知,材料的微观组织形态决定材料的本征特性。下面将简要介绍研究者们提出的用于提高Cu-Cu键合效率及质量的Cu微观组织。
韩国汉阳大学学者通过调节电镀工艺,在基体材料中引入高密度缺陷,研究其Cu-Cu键合效果。该团队在0 ℃下电镀制备高密度缺陷Cu(HD-Cu),并在240 ℃、80 MPa、N2气氛条件下热压键合1 h。HD-Cu组织结构及热压键合后截面聚焦离子束(FIB)成像如图1所示。经过热压键合后,HD-Cu界面两侧的晶粒生长,新生长的晶粒吞噬并消除了键合界面,形成不可区分界面的结合。HD-Cu内部存在较多缺陷及应变带,这导致Cu基体内储存较大的内应力及内应变,在键合过程中释放,成为促进扩散、影响晶粒转变的驱动力,有助于加速键合。
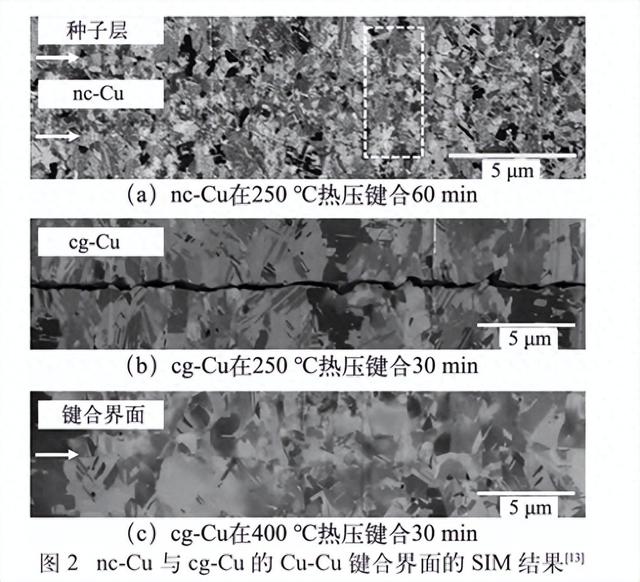
(111)择优取向纳米孪晶铜[(111)nt-Cu]是一种表面具有(111)择优取向,且Cu基体晶粒内具有纳米级间距孪晶片层的特殊Cu组织结构,由Lu等人在2004年首次发现,其具有高电导率、良好的强度及塑性匹配等性能,得到微电子领域的广泛关注。Cu在(111)表面具有较高的表面扩散速率,比在其他表面上的扩散系数快3 ~4个数量级。随着(111)取向晶粒占比的增加,键合后样品的剪切强度增加,(111)取向有助于Cu-Cu键合。同时,在250 ℃时效30 min后,(111)nt-Cu的氧化层厚度只有多晶Cu和(100)取向Cu的一半。
在200 ℃、0.69 MPa、0.133 Pa真空条件下,(111)nt-Cu即可以实现Cu-Cu键合。在400 ℃/100 ℃温度梯度条件下键合后,焊点剪切强度可达176 MPa。与其他Cu组织结构不同的是,(111)nt-Cu在键合过程中存在各向异性晶粒生长现象,如图3所示。具有(100)择优取向的晶粒从底部生长,逐渐长大并吞并键合界面,且晶粒生长方向与温度梯度方向无关。随着温度的升高,各向异性晶粒生长速率提高,在250 ℃下需要90 min实现新生长的晶粒贯穿整个键合Cu层,而在350 ℃下仅需要5 min。因此,具有优越表面扩散及抗氧化性的(111)nt-Cu被认为是Cu-Cu键合材料的优选方案。
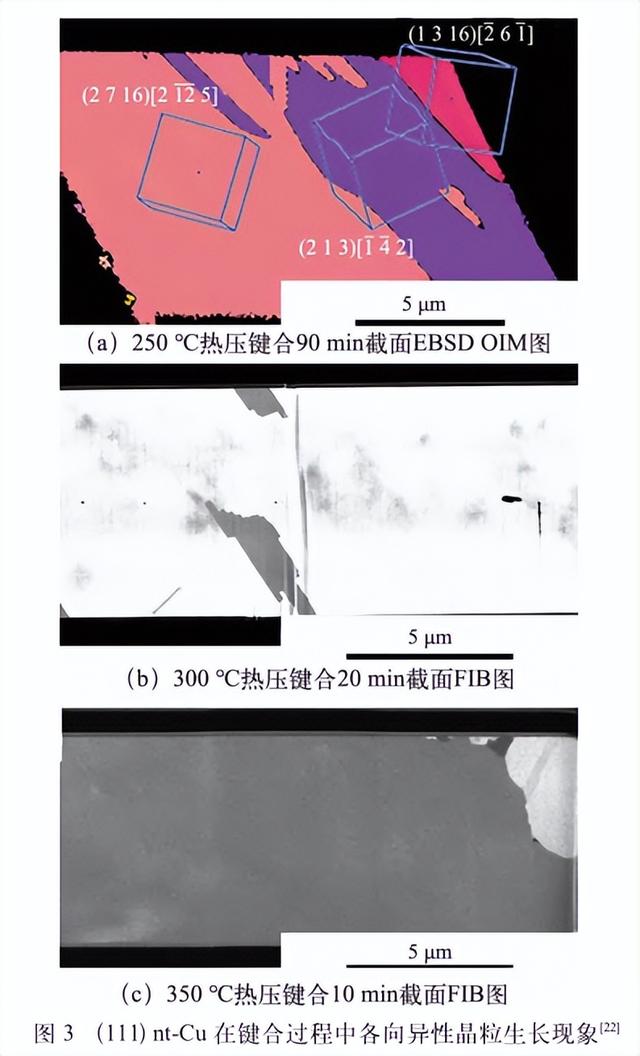
Cu基体的组织结构、择优取向以及预生成缺陷等本征特性,直接影响着材料本身的性能。通过对比发现,相比于多晶铜、HD-Cu以及nc-Cu,(111)nt-Cu本身具有较好的电性能以及力学性能,同时兼具较高的表面原子扩散速率以及良好的抗氧化性,是Cu-Cu键合工艺的优选组织方案。
3键合前金属表面处理
电镀成本低、效率高,并且可以通过调控添加剂、电流密度等方式沉积不同的组织结构,因此成为晶圆级铜互连材料的主要制备方式。然而,电镀沉积的铜表面粗糙度较大且有一定的边缘效应,均匀性和平整性有待提高,不适于直接金属互连。此外,电镀后需要去除多余金属沉积物,暴露出绝缘介质层以形成电路。所以,在键合前进行表面金属余量去除及平整化处理是有必要的。化学机械抛光(CMP)技术通过机械磨抛去除化学软化的表面,与其他工艺相比具有最长的平面化长度,是一种半导体器件制造以及整体平整化的有效手段。
在此基础上,还可以通过对金属键合表面进行特殊的物理或化学方法处理,从而去除金属表面预先生成的氧化物,形成表面钝化层以阻止进一步氧化,或在金属表面形成一定的化学键以促进键合。下面简要介绍一些广泛研究的表面处理方法。
3.1 表面湿法化学处理
Cu-Cu低温键合发展的主要挑战是Cu表面容易氧化,需要在键合前获得洁净的金属表面而非氧化物。使用酸溶液进行键合前湿法预处理是去除表面氧化物的有效手段之一。常用的酸溶液包括硫酸、盐酸、乙酸以及柠檬酸等。
台湾交通大学科研团队详细对比了4种酸溶液的表面处理效果。图4为4种酸溶液表面湿化学处理后的Cu-Cu键合截面SEM图。从表面氧化层清洁能力的角度,对湿法化学处理后的铜膜表面进行X射线光电子能谱(XPS)成分检测分析,发现硫酸、柠檬酸和盐酸都具有较好的清洁强度,而乙酸的清洁能力相对较差,处理30 s后表面氧含量仍超过5%。湿法化学处理后会增加金属表面粗糙度,从而导致键合后在界面处形成预生成孔洞。对比发现,经过柠檬酸处理后样品的键合界面孔洞相对较小且少,相应地Cu-Cu键合后样品的剪切强度也较高。因此,相对而言,柠檬酸更适合用于Cu-Cu键合前的表面化学预处理。
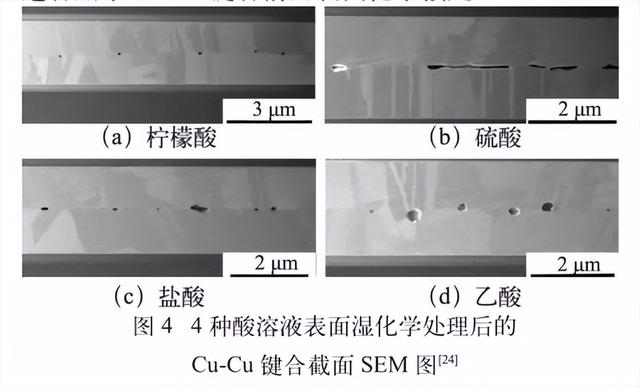
3.2 离子体表面活化键合
表面活化键合(SAB)通过使用溅射粒子轰击进行表面改性,可以降低内应力,去除表面氧化膜,对表面结构及化学成分进行调控,从而实现低温金属键合。日本东京大学Suga等人率先提出SAB方法,并在室温下实现Cu-Cu键合。他们利用40~100 eV低能Ar离子轰击Cu表面,在1000级超洁净环境以及超高真空(约133.32×10-8Pa)条件下实现原子级Cu-Cu键合,键合强度超过6.47 MPa。韩国首尔科技大学Kim团队分两步对Cu表面依次进行Ar、N2等离子体轰击处理,并进行SAB,Ar/N2两步法等离子体活化处理低温Cu-Cu键合机理如图5所示。在沉积Cu金属层后,表面存在一定污染物。Ar离子轰击Cu膜去除一定污染物并在表面产生Cu+活性键。在进行N2等离子体处理时,Cu+活性键与N3-离子结合,形成Cu3N,游离的Cu原子被掺杂进Cu3N的晶格中,形成Cu4N结构。Cu4N具有较高的生成焓(13.23 eV),处于亚稳态,在低温时可以作为表面氧化阻挡层,而在200~300 ℃高温时可以分解,从而可以形成Cu-Cu之间的原子级键合。经过Ar/N2两步法等离子体表面活化处理后,可以在260 ℃、0.9 MPa条件下热压键合1h,实现Cu-Cu键合。经处理后,Cu-Cu键合样品的剪切强度由27 MPa提升至51 MPa,键合强度提升近1倍。此外,哈尔滨工业大学王晨曦课题组结合甲酸表面化学湿法处理以及Ar/O2两步等离子体活化处理工艺,在200 ℃、2.5 MPa、大气环境下热压键合30 min后,Cu-Cu键合的最高键合强度可达到13.46 MPa。
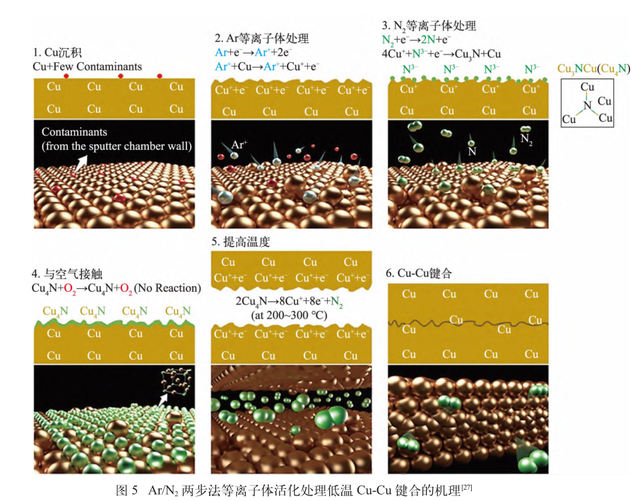
3.3 自组装分子层键合
新加坡南洋理工大学的Tan等人在2009年提出了在 Cu 层表面制备一种自组装单层(SAM)薄膜作为临时钝化层来降低Cu-Cu直接键合温度的方法。此SAM薄膜由烷烃硫醇构成,之前曾被用作引线键合的钝化层。此工作所用烷烃硫醇为1-己硫醇(CH3-(CH2)4-CH2-SH),其一端为疏水的甲基(—CH3),另一端为巯基(—SH)。巯基与Cu等面心立方金属表现出较强的亲和性,与表面Cu原子之间形成S-Cu键,将碳链吸附到表面。然后,分子远离表面,使亚甲基链彼此平行并倾斜,以最大化它们之间的范德瓦尔斯相互作用,从而使尾部基团暴露在表面。这导致在Cu表面形成有序且密集的分子单层。此时,SAM薄膜作为临时钝化层,可以减缓氧化物在Cu膜表面的扩散与反应,保持表面的清洁度。在N2氛围下,在250 ℃下烧结10 min后,可以去除SAM薄膜层。然后在真空环境下,在250 ℃下热压1 h完成键合。经过SAM处理后的键合,在键合界面处呈现出干净的键合形貌,大的Cu晶粒跨过键合界面生长,形成稳固的Cu-Cu键合。这种SAM处理方法有效地将 Cu-Cu键合温度降低至250 ℃,并可以延长处理后晶圆的窗口期,在较长时间内防止表面氧化。
3.4 惰性金属钝化层
Pt、Pd、Au等贵金属具有抗氧化特性,表面沉积一层贵金属钝化层将有效阻碍Cu与O2接触,减缓键合表面的氧化速率。金属钝化层促进Cu-Cu键合机理如图6所示,表面沉积钝化层后的Cu-Cu键合过程主要有以下三步:(1)在外应力作用下,沉积贵金属的键合接合面相互接触,此时仍有孔隙存在,未形成键合;(2)随着键合温度的升高,Cu原子通过钝化的晶界扩散到键合界面的非键合区,形成非晶态Cu来填充钝化层之间的空隙;(3)热压键合后可以通过后退火工艺,使扩散在钝化层中的Cu原子再结晶,进一步提高键合的质量和强度。相比于Cu的晶界自扩散,Cu在钝化层中的扩散系数较高,更容易扩散,这促使Cu-Cu键合可在较低的温度下实现。
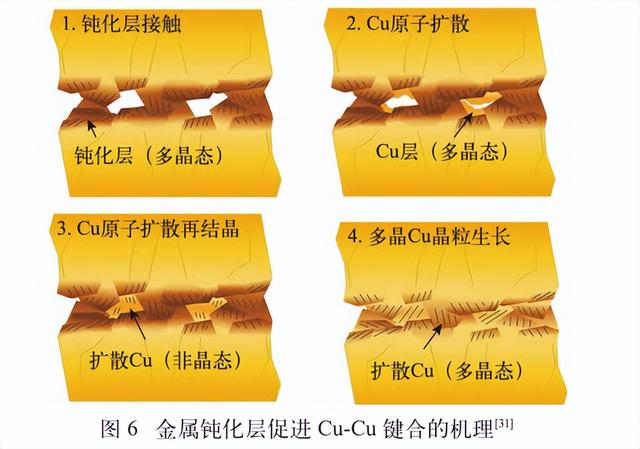
台湾交大Chen课题组使用Au做钝化层,在150 ℃下实现Cu-Cu键合,其键合强度为0.94 MPa。此外,他们在Cu表面溅射沉积10 nm厚的Pt钝化层,随后在180 ℃、133.32×10-5Pa环境下热压键合50 min。X射线能谱(EDX)检测到在键合界面处仅具有较低的O原子浓度,Pt可以在一定程度上阻挡表面氧化。此外,Cu原子扩散至键合界面与Pt相溶,实现原子级扩散键合。键合样品的电阻率经500次温度循环测试(TCT)后,其电阻仍保持稳定。
在金属表面沉积钝化层可以有效地防止表面氧化,促进扩散,并与现有的封装制造工艺兼容,但溅射工艺沉积的速率低,惰性金属价格昂贵,成为大规模生产的阻碍。
在Cu-Cu键合前,对基体表面通过化学或者物理方法进行表面清洁、改善表面抗氧化性和表面原子扩散性能是必不可少的。第3节总结了常见的表面处理方法,具体方法的选择需要结合预期效果、工艺窗口期、设备要求以及预算等方面进行综合考虑。除此之外,也可以对2种及以上的表面处理方法进行组合,从而实现理想的键合效果。
4 Cu-Cu键合工艺方法
研究者们还通过改进键合工艺,如调节环境气氛、引入外加能量、改变键合结构等方式,提高键合效率。下面对相关研究进行简要介绍。
4.1 键合环境气氛
金属Cu在含氧气氛中极易氧化,因此需要较高的温度和压力促进原子扩散和氧化膜破碎,使得Cu原子扩散,穿过氧化物形成键合。在这种情况下,键合环境中的氧含量控制变得极为重要。
如前文所述,在超高真空条件下,具有洁净表面的Cu膜在室温下也可以实现键合。此外,在惰性气体保护下也可以在一定程度上防止氧化。台湾交大CHEN等人在100 ℃/300 ℃温度梯度(界面温度经模拟约为144~148 ℃)以及64 MPa的压力条件下,通过N2注入保护的方式减缓Cu的表面氧化,实现Cu-Cu键合。除上述环境气氛外,通入甲酸蒸汽可以创建局部还原环境,对CuO进行原位清洁,从而实现Cu-Cu键合。在100~150 ℃时,甲酸最初以气态形式与CuO层反应,形成甲酸铜和水蒸气,此时薄的甲酸铜层覆盖在裸铜表面。当表面温度升高到200 ℃以上时,甲酸铜层分解成CO2和H2,同时在表面上生成纯Cu金属。甲酸还原CuO的化学反应方程式如下:

在甲酸蒸汽中,在施加约250 MPa压力以及界面温度为240 ℃的条件下,键合5 s后即可达到大于150 MPa的键合强度。
然而,这些方法在实际工艺生产中存在一定阻碍,在大型机器中创建超高真空或者维持惰性环境需要极高的气体流速(500~1000 L/min),实现十分困难,而甲酸蒸汽的引入对于设备以及操作要求同样较高。
4.2 超声辅助键合
超声辅助键合常用于芯片或晶圆之间Au凸点或Au引线的键合。超声可以增加键合界面的能量,软化键合界面,提高塑性变形程度和扩散速率,破碎表面氧化层,从而提高键合效率。相对于Au,Cu的硬度更大且氧化速率更高,键合难度更大,但仍有学者对此进行了尝试。Silicon Austria Labs的Roshanghias等人使用超声振动辅助热压键合,当超声能量为6 W、外加键合压力为6 MPa、键合界面温度大于300 ℃时,仅需几百毫秒即可达到74 MPa的键合强度;但是当超声超过一定功率时,超声振动加剧,将破坏已结合的键合界面,不利于键合。热超声键合设备如图7所示。
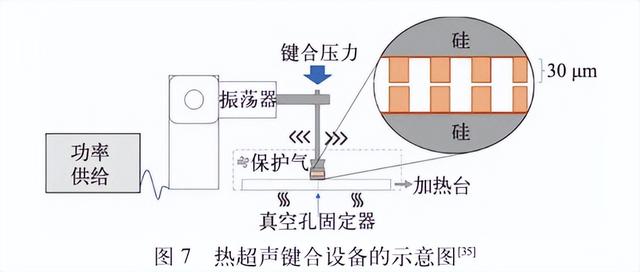
使用这种方法可以在一定程度上实现短时快速低温键合,但是要求晶圆表面有较好的平整度和共面性,超声功率、温度及压力控制要适配,对工艺操作及设备的要求也相对较高。
4.3 Cu柱-Cu凹槽键合
如第3节所述,在键合前进行CMP处理是必要的。然而,CMP具有严苛的工艺公差和较高的制造及设备成本。因此,研究在无CMP处理情况下的低温键合也有一定的意义。
CHOU等人创造性地提出了一种通过改进键合图形,促进金属塑性变形、加快蠕变扩散的方法。他们在一侧晶圆上沉积制备Cu柱结构,在另一侧晶圆上制备了具有凹形开口的光敏聚酰亚胺层,形成图案,并沿着凹面电镀Cu凹槽结构。这种方法的机理可以用塑性变形和热补偿来解释。塑性变形是一种不可逆的形状变换,它对作用力作出响应。Cu原子的排列受到外部高应力作用的破坏,导致位错穿过晶格。晶体倾向于在位错处相互滑动,导致内耗产生内能或热量。这种放热反应提供了额外的热能,以驱动Cu原子的扩散并协助键合过程,这个过程称为热补偿。这种机制可以解释Cu柱-Cu凹槽键合中无CMP低温键合的原因,Cu柱-Cu凹槽键合机理如图8所示。与传统的Cu柱-柱键合不同,在Cu柱-Cu凹槽键合过程中,在键合开始时,只有Cu柱的底角与凹槽接触,产生较大应力。在这种大应力作用下,Cu柱和Cu凹槽面的结合区域发生了强烈的塑性变形,增加了热补偿,使得Cu柱在结合过程中可以逐渐填充Cu凹面,以实现低温Cu-Cu直接键合。
这种方法可以在无CMP处理的情况下,在200 ℃以下进行低温键合。但是在Cu柱-Cu凹槽接触侧壁处的键合效果不佳,仍有较大孔洞及裂纹存在。并且特殊的图形结构对于窄间距、小尺寸焊点制备的要求较高,因此该方法目前仅停留在试验阶段。
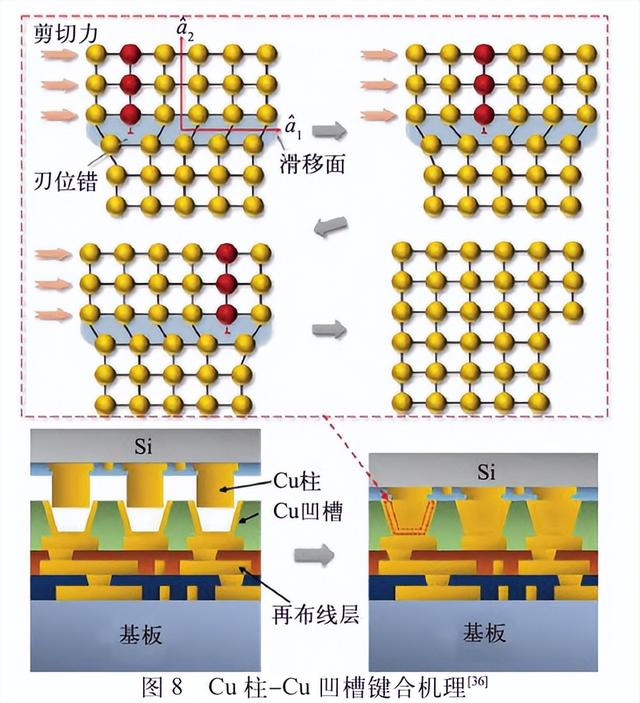
4.4 DBI混合键合技术
Direct bonding interconnect(DBI)是由美国Ziptronix公司发明的一种混合键合技术。这种技术通过将介质层和Cu再布线层共平面图形化,先在低温条件下使介质层键合,再通过退火等方式实现金属互连,DBI混合键合技术工艺流程如图9所示。2种热膨胀系数(CTE)不匹配的材料容易产生应力和翘曲,有利于异构集成。在初始阶段,2个晶圆表面被CMP平整化后,首先对需要氧化键合的介质层进行表面活化或化学修饰,然后将2个表面对齐,在2个模具或晶圆之间自发地产生机械低温直接氧化键,将2个这样的芯片或晶圆表面结合在一起。一般的绝缘氧化介质层材料为SiO2,对晶圆表面进行化学处理和等离子体活化后,使得表面以Si-OH或Si-NH2亲水基团终止,通过形成范德华键来达到高键强度,2种基团反应方程式如下:

经过CMP处理后,如果接触金属延伸至晶圆表面几纳米以上且不含原生氧化物,则可以自发地产生原子扩散,形成三维电互连。另外,如果接触金属在表面以下(形成金属隐槽)几纳米处,并且具有原生氧化物,则可以进行加热退火处理,由于接触金属比周围的电介质材料具有更大的热膨胀系数,导致了金属键的形成和三维电互连。当接触金属被CMP处理抛光过多,金属接触表面低于晶圆面较多,此时加热膨胀后也无法连接,形成无效电器互连。晶圆混合键合技术可以用于2 μm间距的凸点互连、芯片-晶圆(die-to-wafer)以及晶圆-晶圆(wafer-to-wafer)的封装互连中。
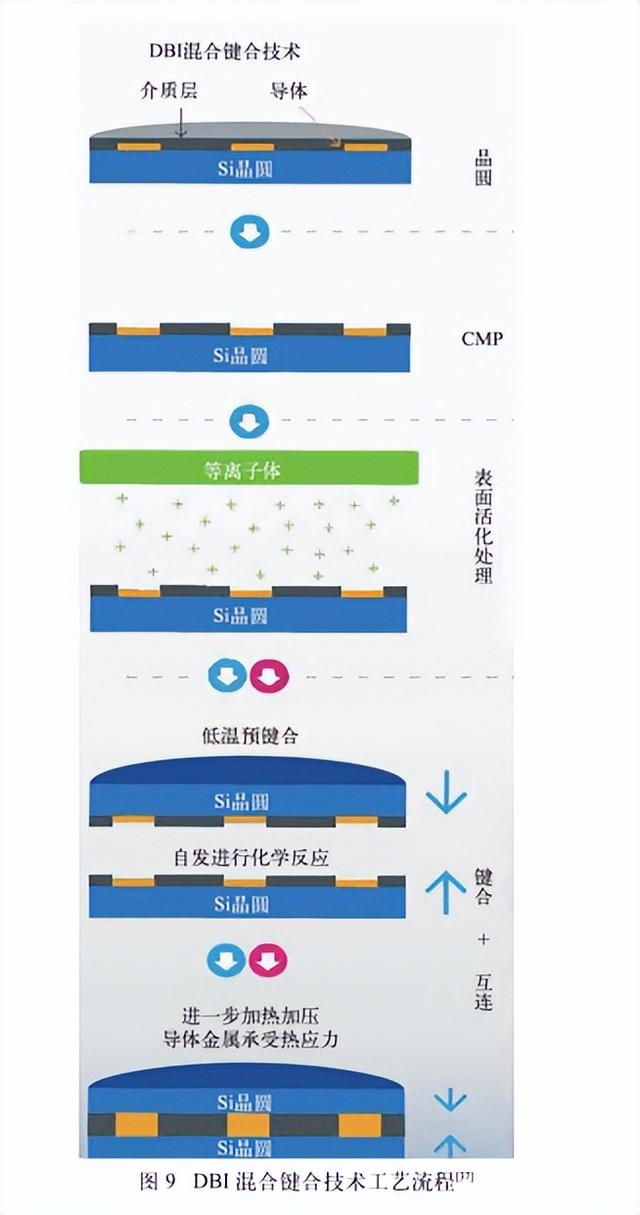
目前,常用作焊点的Sn基钎料,如SAC305等,其熔点在220 ℃左右,回流温度在250 ℃以上。Cu-Cu键合技术取代Sn基钎料技术的关键在于,可以在提高焊接性能的同时不改变甚至降低键合所需的温度及压力。随着键合工艺的革新和进步,现在Cu-Cu键合工艺温度已经从传统热压键合的300~400℃降低到250 ℃以下,使用DBI技术甚至可以进行室温连接(后续需退火)。但是现有研究还在实验阶段,需要严苛控制键合环境及制程,后续需要对工艺进行持续优化,进一步降低热预算并提高键合强度及服役可靠性,提升良率并降低成本。
5 Cu-Cu键合性能评价
一般来说,电子封装的基本功能包括电源供给、信号交流、散热、芯片保护、机械支撑等。Cu-Cu键合技术作为一种新型封装互连方法,也需要对上述性能及功能进行测试和评价,主要为初始键合效果测试、电学性能表征以及服役可靠性评估。
5.1 Cu-Cu键合效果测试
首先,可以对键合后的样品进行表面形貌观测判定。首先,可以对键合后的样品进行直接成像来观测判定。一种方法是使用超声扫描显微镜(SAT)对键合样品表面进行扫描,当高频超声波发射至样品内部后,由于不同材质的声阻抗不同,对声波的吸收和反射程度的不同,通过采集反射或穿透的超声波能量信息可以显示键合样品内部出现的分层、裂缝或者空洞等缺陷;还可以通过扫描电子显微镜(SEM)、FIB离子像或透射电子显微镜(TEM)等对键合样品的截面进行成像,直观地观察键合界面处是否实现连接。
通过力学测试也可以对键合强度进行评价。常用的力学测试方法为剪切强度测试。下面列举其中一种常用的试验方法:将芯片切割成大小不同的2片,将尺寸较小的芯片通过Cu-Cu键合方式连接在大芯片(基板)之上;将推刀以一定剪切高度置于基板上,以一定剪切速率缓缓推动上部芯片,直至芯片与基板分离;由此通过最大剪切力和键合面积计算出剪切强度,剪切强度的测试方法如图10(a)所示。此外,还有一种基于裂纹扩展理论的键合表面能定量评估方法,键合能的测试方法如图10(b)所示,表面能和裂纹几何形状的关系如式(5)所示:

其中,γ是以erg/cm2为单位的比表面能,2y和L分别为裂纹间距和长度,t为晶圆厚度,E为晶圆的弹性模量。将厚度为2y的刀片插入键合样品缝中,测量得到裂纹长度L。刀片插入后分离区的边界在透射红外光中显示为一系列平行于刀片边缘的干涉条纹。使用红外图像转换器测量叶片边缘和裂纹尖端第一条条纹之间的距离,即为裂纹长度L。由于这种测试方法较为复杂,没有被研究者们用作评价键合强度常用的试验方法。Cu-Cu键合材料及工艺键合强度对比如表1所示。
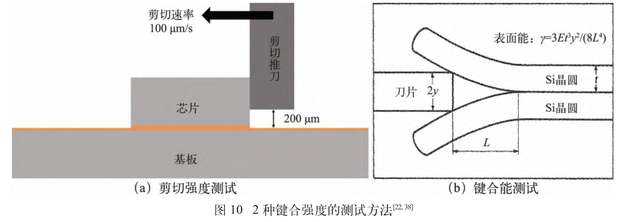
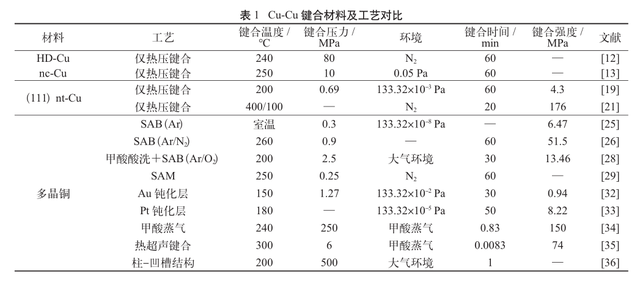
5.2 电学性能测试
除保障机械支撑外,提供电气互连也是键合点的主要用途之一。常用的电阻测量手段有开尔文结构电阻测试和菊花链结构电阻测试。2种Cu-Cu键合焊点电阻测试方法如图11所示。开尔文结构电阻测试通过Cu再布线层从键合焊点处引出导线至电压电流测试焊盘,通入电流后,通过测量焊盘之间的电压差,结合电流值计算Cu-Cu键合凸点的电阻。这种方式可以用来测量单一凸点或键合结构的电阻值。菊花链结构电阻测试则将多个键合点互连,可以同时测量多个键合点的电阻均值,用来研究大规模键合产率。

5.3 可靠性评估
可靠性指在一定时间周期内,系统的正常工作概率在可接受的范围内。一般通过进行加速试验,对产品施加比实际应用中强度更大的载荷,在短时间内获得关于产品可靠性的数据,并评估其失效模式。常见的Cu-Cu键合可靠性试验有电迁移、TCT测试等。在电迁移可靠性评价方面,一般通过较高电流密度激发失效。在电流密度较高时,电子运动可以带动金属中的原子迁移,导致导线上出现空洞或小丘,使得导线发生短路或者断路失效。在TCT可靠性评价方面,由于封装系统中多种材料的CTE不匹配,导致在热循环中产生较大的热应力,应力使得芯片连接处产生裂纹,从而产生热形变失效。一般将20%电阻变化率作为可靠性失效判定的标准。
Chen等人结合开尔文结构电阻测定以及离子像观察方法对TCT以及电迁移后的Cu-Cu键合样品进行失效分析。研究发现,在电流及热应力作用下,键合后预留的初始微小孔洞和裂纹将逐渐聚集、长大,成为缺陷萌生源。因此,初始的键合质量对样品服役的可靠性有较大的影响。
通过对Cu-Cu键合后的样品进行键合界面微观组织观察以及剪切等力学性能测试,可以对键合质量进行初步的判定。此外,通过焊点通电试验并且结合可靠性测试,对样品服役性能进行评估。目前,业界亟需对键合界面质量、力学性能、可靠性评估进行判定标准统一化,便于同行评定以及行业规范的制定。
6 结束语
随着人们对电子产品要求的日益提高以及高新科技的进步,对半导体器件设计及封装的要求也越来越高。Cu-Cu键合技术具有高强度、抗电迁移性能良好以及工艺制备尺寸可降低到微米级等优点,在芯片-芯片以及晶圆-晶圆间的高密度互连等方面具有极大的发展前景,成为取代传统Sn基钎料凸点互连的优选解决方案。目前主流的研究团队主要分布在美国、日韩、以及中国台湾、香港等地区。本文总结了Cu-Cu直接键合技术的材料组织、表面处理、工艺方法以及性能评价等方面的成果,概述了国内外Cu-Cu键合的相关研究进展,并通过不同组织工艺的键合强度对比,为后续键合材料及工艺的研究提供理论参考。从先进封装小型化的发展需求来看,我国亟需大力开展Cu-Cu直接键合技术的研究,深入研究界面的反应机理,力求开发出更低的温度、压力键合工艺,并对Cu-Cu键合工艺及质量评判标准进行归一化,以便实现先进互连技术的更新迭代。