
随着科技的持续进步,焊接加工技术亦在不断地创新与升级。近些年来,新型焊接加工技术如雨后春笋般涌现,为工业制造与加工带来了翻天覆地的变革。
在当今的工业社会中,尚无哪一种连接技术能如焊接这般,在各个领域得到如此广泛且普遍的应用。而其中最为关键的原因便是其具备极具竞争力的性价比。当人类社会迈入 21 世纪的今天,焊接已然步入了一个全新的发展阶段。当今世界的诸多最新科研成果、前沿技术以及高新技术,像计算机、微电子、数字控制、信息处理、工业机器人、激光技术等,已被广泛应用于焊接领域,这使得焊接的技术含量获得了前所未有的提高,并在制造过程中缔造出了极高的附加值。
焊接作为组装工艺的一种,通常被安置在制造流程的后期或是最终阶段,故而对产品质量起着决定性的作用。在工业化高度发达的美国,焊接被视作“美国制造业的命脉,更是美国未来竞争力的关键所在”。其主要根源就在于这样一个事实:众多工业产品的制造已无法脱离焊接技术的运用。
我国近些年来借助焊接制造成功打造出了一批具有代表性的重要产品,它们或是最大、或是最重、或是最长、或是最高、或是最厚、或是最新,这充分表明焊接在国民经济建设与社会发展中发挥着不可替代的关键作用。例如三峡水利工程、西气东输工程以及“神舟”号载人飞船,皆大量采用了焊接结构。
本文将对近几年的几种新型焊接加工技术予以介绍,并深入探讨它们的应用与优势。
一. 激光焊接技术
激光堪称 20 世纪最为伟大的发明之一,世界上首台激光器于 1960 年问世。激光焊接属于当今先进的制造技术范畴。激光焊接技术是一种凭借高能激光束照射材料表面,促使材料熔化进而连接在一起的焊接方式。相较于传统的焊接方法,激光焊接具备诸多优点。首先,激光焊接的速度极快,能够达成高效的生产目标。其次,激光焊接的焊缝狭窄,热影响区较小,能够有效减少工件变形以及焊接缺陷的出现。此外,激光焊接还能够实现异种材料的焊接,极大地拓宽了焊接的应用范围。在汽车制造、航空航天、电子、医疗器械等诸多领域,激光焊接技术均得到了广泛的应用。激光焊是以聚焦的激光束充当能源,轰击焊件接缝所产生的能量来进行焊接的一种方法。
1. 与常规焊接方法相比,激光焊有如下特点:
1)聚焦后的激光功率密度高达105 -107W/cm2,工件产生的变形极小,热影响区也很窄,多以深熔深方式,特别适宜于精密焊接和微细焊接。
2)焊接厚件时可不开坡口一次成形,获得深宽比大的焊缝。不开坡口单道焊接钢板的厚度已达50mm。
3)适宜于焊接一般焊接方法难以焊接的材料,如难熔金属、热敏感性强的金属以及热物理性能差异悬殊、尺寸和体积悬殊工件间的焊接;甚至可用于非金属材料的焊接,如陶瓷、有机玻璃等。
4)穿过透明介质对密闭容器内的工件进行焊接,适合于在玻璃的密封容器里焊接铍合金等剧毒材料。
5)可借助反射镜使光束达到一般焊接方法无法施焊的部位,YAG激光(波长1.06um )还可用光纤传输,可达性好。
6)激光束不受电磁干扰,无磁偏吹现象存在,适宜于磁性材料焊接。
7)不需真空室,不产生X射线,观察及对中方便。
激光焊的不足之处是设备的一次投资大,特别是高功率连续激光器的价格昂贵,而且对高反射率的金属直接进行焊接比较困难。
目前,用于焊接的激光器主要有两大类,气体激光器和固体激光器,前者以CO2激光器为代表,后者以YAG激光器为代表。根据激光的作用方式激光焊接可分为连续激光焊和脉冲激光焊。随着设备性能的不断提高、结构的日益复杂,对接头性能和变形要求越来越苛刻,许多传统的焊接方法已不能满足要求,因而,激光焊接在许多场合具有不可替代的作用。
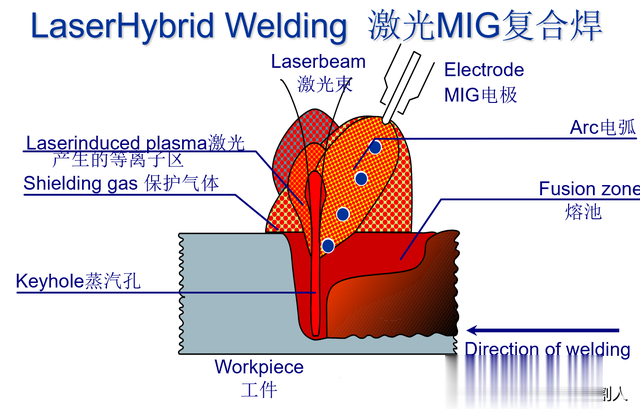
2. 激光焊复合焊接
激光复合焊接技术是指将激光与其他焊接方法组合起来的集约式焊接技术,其优点是能充分发挥每种焊接方法的优点并克服某些不足,从而形成一种高效的热源。例如,由于高功率激光焊设备的价格较昂贵,当对厚板进行深熔、高速焊接时,可将小功率的激光器与常规的气体保护焊结合起来进行复合焊接,如激光-TIG和激光-MIG等。
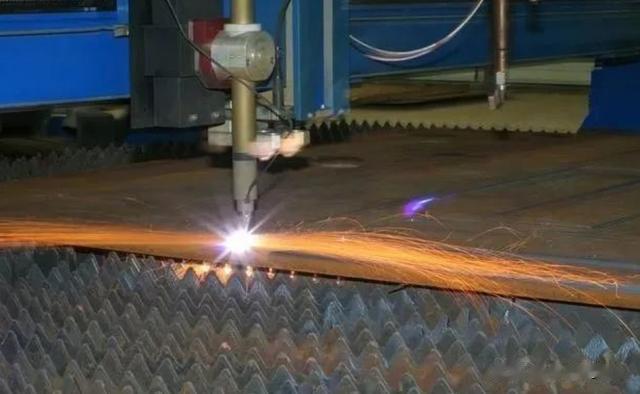
3. 激光焊应用
铝合金激光焊常采用深熔焊方式,焊接时的主要困难是它对激光束的高反射率和自身的高导热性。铝是热和电的良导体,高密度的自由电子使它成为光的良好反射体,起始表面反射率超过90%。也就是说,深熔焊必须在小于10%的输入能量开始,这就需要采用大功率或高性能的激光束来获得所需的能量密度。而小孔一旦生成,它对光束的吸收率迅速提高,甚至可达90%,从而使焊接过程顺利进行。
由于铝合金对激光的强烈反射作用,铝合金激光焊十分困难,必须采用高功率的激光器才能进行焊接。在CO2激光焊和Nd: YAG激光焊的过程中,采用等离子弧与激光复合焊接不仅能提高焊接速度(可提高两倍)、减少裂纹,还有助于得到平滑的焊缝。激光焊的优势和工艺柔性又吸引着科技人员不断突破铝合金激光焊的禁区,有力推动了铝合金激光焊在飞机、汽车等制造领域中的应用。
钛合金采用激光焊接可得到满意的结果。Ti-6A1-4V是用量最大的钛合金,广泛用于航空航天制造。对1mm厚的Ti-6Al-4V板材采用4.7kW的CO2激光输出功率,焊接速度可超过15m/min。检测结果表明,焊接接头致密、无裂纹、气孔和夹杂物。接头的屈服强度、抗拉强度与母材相当,塑性不降低。在适当的焊接参数下,Ti-6A1-4V合金接头具有与母材同等的弯曲疲劳性能。钛合金激光焊时,焊接速度一般较高(80~100m/h),焊接熔深大致为1mm/kW。激光焊焊接高温钛合金,也可以获得强度和塑性良好的接头。
二. 电子束焊接技术
电子束焊接技术是一种利用高能电子束作为热源进行焊接的方法。电子束焊接具有高能量密度、高穿透深度、低热影响区等特点。该技术在真空环境下进行,能够实现高精度和高纯净度的焊接,适用于高强度、高导电性和高导热性的材料。在航空航天、核工业、石油化工等领域,电子束焊接技术得到了广泛应用。
1.作为电子束焊的热源,电子束具有如下特点:
(1)功率密度高
电子束属于高能束流,电子束焊接时常用的加速电压范围为30~150kV,电子束电流为20~l000mA,电子束焦点直径约为0.1~1mm,其功率密度可达106W/cm2以上。
(2)精确、快速的可控性
电子作为物质基本粒子,具有极小的质量(9.1×10-31kg)和一定的负电荷(1.6×10-19C),电子的荷质比高达l.76×1011C/kg,通过电场、磁场对电子束可作快速而精确的控制。这是电子束的一个优势,与同为高能束流的激光相比,后者只能用透镜和反射镜控制,速度慢。
2. 电子束焊的适用范围
1)焊件的结构形状和尺寸
焊件的厚度与电子束的加速电压和功率有关,一般单道焊接碳钢厚度可以超过100mm,或厚度超过400mm的铝板,而不需开坡口和填充金属;焊薄件的厚度可小于2.5mm,甚至薄到0.025mm;也可焊厚薄相差悬殊的焊件。
真空电子束焊焊件的形状和尺寸不能超过焊接室容积允许的范围内。非真空电子束焊不受此限制,可以焊接大型焊接结构,但必须保证电子枪底面出口到焊件上表面的距离,一般在12~50mm之间;单面焊可焊厚度一般很少超过10mm,如果厚度达到25mm以上,需要降低焊接速度,从而增加制造成本。
2)焊接的材料
在真空室内进行电子束焊时,除含有大量的高蒸气压元素的材料外,一般熔焊能焊的金属,都可以采用电子束焊。如铁、铜、镍、铝、钛及其合金等。此外,还能焊接稀有金属、活性金属、难熔金属和非金属陶瓷等。可以焊接熔点、热导率、溶解度相差很大的异种金属。可以焊接热处理强化或冷作硬化的材料,而对接头的力学性能没有太大的影响。
3)焊接有特殊要求或特殊结构的焊件
可以焊接内部需保持真空度的密封件;焊接靠近热敏元件的焊件;焊接形状复杂而且精密的零部件; 可以同时施焊具有两层或多层接头的焊件。这种接头层与层之间可以有几十毫米的空间间隔。
3.具体应用
铝和铝合金电子束焊前需要对接缝处进行除油和清除氧化膜处理,焊接过程中应控制焊接速度,以防止出现气孔并能改善焊缝成形。对厚度小于40mm的铝板,焊接速度应在60- 120cm/min;对于40mm以上的厚铝板,焊接速度应在60cm/min以下。
钛是一种非常活泼的金属,最常见的焊接缺陷是氢气孔,所以应在良好的真空条件下(<1.33×10-2Pa)进行焊接,而电子束焊接是所有工业钛和钛合金最理想的焊接方法。采用电子束焊接能有效地避免了有害气体的污染,而且电子束的能量密度大,焊接速度高,焊缝中不会出现粗大的片状α相,因而焊接接头的有效系数可达到100%。焊接时为了防止晶粒长大,宜采用高电压、小束流的工艺参数。
三. 超声波焊接技术
超声波焊接技术是一种利用超声波的振动能量来实现材料连接的焊接方法。超声波焊接具有快速、节能、环保等优点。该技术适用于塑料、金属、陶瓷等材料的连接,因此在医疗设备、电子元件、汽车零部件等领域得到了广泛应用。此外,超声波焊接还可以实现异种材料的连接,为材料连接提供了新的解决方案。
超声波焊也是一种以机械能为能源的固相焊接方法。进行超声波焊时,焊接工件在较低的静压力下,由声极发出 的高频振动能使接合面产生强裂摩擦并加热到焊接温度而形成结合。超声波焊可以用于大多数金属材料之间的焊接,能实现金属、异种金属及金属与非金属间的焊接。可适用于金属 丝、箔或2~3mm以下的薄板金属接头的重复生产。
1.超声波熔接的优点
1)节能环保
2)无需装备散烟散热的通风装置
3)成本低,效率高
4)容易实现自动化生产
5)焊接强度高,粘接牢固
6)焊点美观,可实现无缝焊接,防潮防水,气密性好
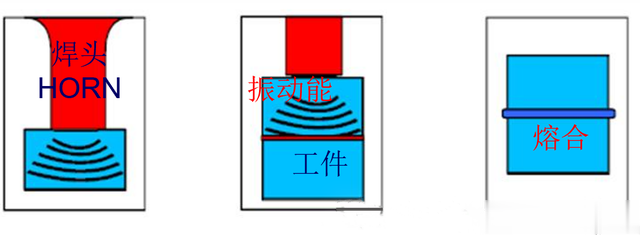
2.超声波熔接的工作原理
超声波熔接装置是通过一个电晶体功能设备将当前50/60Hz的电频转变成20KHz或40KHz的电能高频电能,供应给转换器。转换器将电能转换成用于超声波的机械振动能,调压装置负责传输转变后的机械能至超声波熔接机的焊头。焊头是将机械振动能直接传输至需压合产品的一种声学装置。
振动通过焊接工作件传给粘合面振动磨擦产生热能使塑胶熔化, 振动会在熔融状态物质到达其介面时停止,短暂保持压力可以使熔化物在粘合面固化时产生个强分子键, 整个周期通常是不到一秒钟便完成,但是其焊接强度却接近是一块连着的材料。
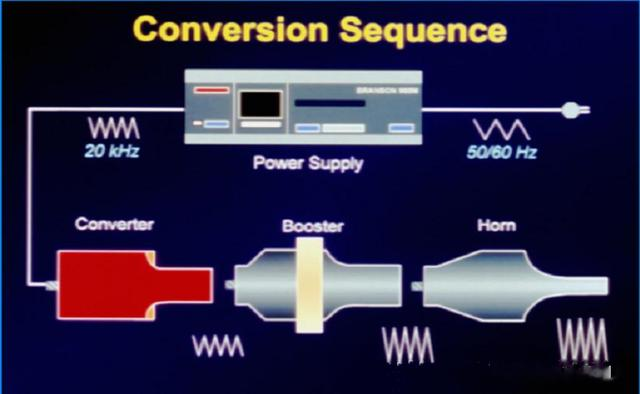
由超声波的工作原理我们可以知道,超声波的实际功率并不大,工作时间短,所以产生的热量有限,所以一般只适用于一些熔点较低(400℃ 以下)的材料。主要以热塑性的聚合物即塑料为主。我们主要了解一下各种塑料的熔接特性。一般来说,聚合物的熔点越高,其焊接所需的超音波能量越多。材料的硬度对其是否能有效传输超音速振动是很有影响的。总的说来,愈硬的材料其传导力愈强。
四. 摩擦焊接技术
搅拌摩擦焊(Friction Stir Welding,简称FSW)是基于摩擦焊技术的基本原理,由英国焊接研究所(TWI)于1991年发明的一种新型固相连接技术。与常规摩擦焊相比,其不受轴类零件的限制,可进行板材的对接、搭接、角接及全位置焊接。被誉为“继激光焊后又一次革命性的焊接技术”。
摩擦焊接技术是一种利用摩擦热能来实现材料连接的焊接方法。摩擦焊接具有节能、环保、高效等优点。该技术适用于同种或异种材料的连接,特别适合于大型结构件的连接。在石油化工、船舶制造、轨道交通等领域,摩擦焊接技术得到了广泛应用。
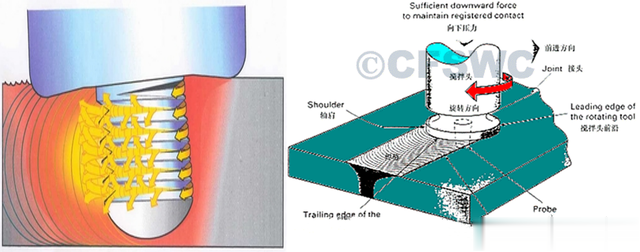
与传统的熔化焊方法相比,搅拌摩擦焊接头不会产生与熔化有关的如裂纹、气孔及合金元素的烧损等焊接缺陷;焊接过程中不需要填充材料和保护气体,使得以往通过传统熔焊方法无法实现焊接的材料通过搅拌摩擦焊技术得以实现连接;焊接前无须进行复杂的预处理,焊接后残余应力和变形小;焊接时无弧光辐射、烟尘和飞溅,噪音低;因而,搅拌摩擦焊是一种经济、高效、高质量的“绿色”焊接技术。
摩擦焊生产率较高,原理上几乎所有能进行热锻的金属都能摩擦焊接。摩擦焊还可以用于异种金属的焊接。要适 用于横断面为圆形的最大直径为100mm的工件。
搅拌摩擦焊的应用:
1. 搅拌摩擦焊发明初期主要解决铝合金薄板的焊接问题,随着搅拌摩擦焊焊接工具的开发和工艺技术的发展,目前,搅拌摩擦焊可以焊接所有系列的铝合金材料,包括那些难于用熔化焊方法连接的高强铝合金材料,如2xxx(Al-Cu)系列、7xxx(Al-Zn)系列铝合金,也可用于不同种类铝合金材料的连接,如5xxx(Al-Mg)与6xxx(Al-Mg-Si)系列铝合金铝合金的焊接。在材料的厚度上,搅拌摩擦焊单道焊可以实现厚度为0.4~100mm铝合金材料的焊接;双道焊可以焊接180mm厚的对接板材。2. 搅拌摩擦焊在钛合金焊接中的应用也日趋广泛,采用搅拌摩擦焊技术焊接钛合金Ti-6 Al-4 V,可以得到高质量的焊缝,且焊接速度快、成本低、效益好、操作简单。3.搅拌摩擦焊接铜合金,可以消除熔化焊时的焊缝成形差、热裂倾向大、难于熔合、未焊透、表面成形差等外观缺陷、焊缝及热影响区热裂纹、气孔等内部缺陷。当选用尺寸合适的锥形螺纹形搅拌针时,焊缝成形良好;而选用圆柱形搅拌针时,焊缝容易产生缺陷。这说明螺纹形搅拌针的螺纹槽能改善热塑性材料的流动,从而有利于形成致密的焊缝。五. 冷喷涂焊接技术
冷喷涂焊接技术是一种利用高速粒子流将材料喷涂在基体表面并形成固态涂层的方法。该技术具有高效、节能、环保等优点,适用于金属和非金属材料的涂层制备和修复。在机械制造、航空航天、能源等领域,冷喷涂焊接技术得到了广泛应用。
冷喷涂(Cold Spray),又称为冷气动力学喷涂(Cold Gas Dynamic Spray,简称CGDS),是基于空气动力学,采用高压气源将固态粒子带动至极高的速度撞击基板,从而沉积形成涂层。
冷喷涂是一种实现材料表面多功能化的有效技术,其原理是以压缩气体作为加速气流,带动5-45μm的粉末颗粒,以低温(室温-600℃)超音速在完全固态状态下撞击基板,使颗粒发生强烈塑性变形,并沉积形成堆积层,完成三维零件的制造。该技术具有高效、致密和耐腐蚀等特性,非常适合灵活复杂的打印环境,目前冷喷涂技术已经广泛应用于军事、航天领域,同时在航空、能源、医疗等领域也展现出广泛的应用潜力。

1. 冷喷涂焊接技术优势
1)多材料适用性:可用于喷涂多种材料,包括金属、塑料、陶瓷等,具有较强的通用性。
2)耐用性和保护性:所形成的涂层通常具有很强的耐腐蚀性和耐磨损性,能够保护基材并延长其使用寿命。
3)冷喷涂对环境基本无污染,喷涂飞溅的粉末可以回收再利用。
4)冷喷涂层内残余应力小,且为压应力,有利于制备较厚涂层。
5)涂层的化学成分以及显微组织结构可与原材料保持一致,基本上不存在氧化、合金成分烧损、晶粒长大等现象,可以喷涂热敏感材料和活性金属及高分子材料,适用于非晶、纳米晶涂层的制备。
2.冷喷涂技术应用
冷喷涂铝及其合金涂层可用于修复铝合金的工业零部件,受到学术界和工业界的广泛关注。铝及其合金虽然强度和熔点较低,但冷喷涂时塑性好、变形能力高、临界速度低,是理论上易于喷涂的材料。Al-Sn二元合金具有优异的抗粘性能和低模量,常被用作汽车行业的滑动轴承材料。
冷喷涂铜涂层的各项物理指标及性能都很优异,冷喷涂铜涂层非常致密,几乎没有孔隙,在喷涂状态下其导电率可接近本体的100%。
在冷喷涂中, 钛和钛合金沉积所需的临界速度较高,因此若要获得致密的钛和钛合金涂层,需要用高压冷喷涂设备和较高的参数(例如:氮气作为载气,气体温度 800~1100℃,气体压强 4~5Mpa)。另外,使用氦气作为载气可以使钛和钛合金颗粒加速到更高的速度,从而使钛和钛合金颗粒发生更强烈的塑性变形和更强的结合强度,因此使用氦气可以使钛和钛合金涂层非常致密。
Inconel 718 是一种镍基超级合金,合金元素包括 Ni、Cr、Mo、Nb、Ti 和 Al。通过形成γ'和γ "强化相以及细小/稳定的碳化物,Inconel 718 在高温下具有高强度和良好的抗氧化性和抗气体腐蚀性,因此被广泛应用于工作温度较高的航空航天零部件。与易于喷涂的纯镍相比,Inconel 718 具有较高的屈服强度、较差的塑性和较高的应变硬化率,因此很难进行冷喷涂。与钛合金类似,Inconel 718 冷喷沉积所需的临界速度也很高。
3. 冷喷涂技术的未来发展方向
1)材料多样化:冷喷涂粉末类型涵盖金属、陶瓷、高分子及复合粉末。对金属粉末的冷喷涂研究是最早开始的,主要以铜、铝、银、钛、镁、锌、锡、钽、铁基、镍基、钛基、镁基、锌基合金等稳态材料为主,目前朝着非晶、准晶和高熵合金等亚稳态材料方向发展。进一步扩展可用材料范围,以适应不同行业和应用的需求。
2)技术复合化:随着材料体系多样化的发展,原有的工艺条件不能满足特殊材料的沉积要求,因此,复合型冷喷涂技术的开发成目前的研究重点。西安交通大学焊接与涂层研究所开发了微锻辅助冷喷涂技术,剑桥大学和浙江工业大学激光加工技术工程研究中心开发了激光辅助冷喷涂技术。
3)应用高端化:目前冷喷涂技术一般以军事、航天装备应用为主,冷喷涂技术商业化应用主要为旋转靶材,如冷喷涂旋转钛铝、锌铝、锌锡、钛、钽、银、铜、镍铬等,应用于半导体、平面显示、磁存储、玻璃镀膜、装饰镀等领域。
4)可持续性与环保:发展更环保的材料和打印方法,减少资源消耗,促进可持续制造。
六. 焊接机器人
焊接机器人乃是投身于焊接(涵盖切割与喷涂)作业的工业机器人,其由机器人本体与控制柜共同构成,且于工业机器人的末轴法兰处装配焊钳或焊(割)枪,从而能够展开焊接、切割或者热喷涂等工作。
焊接机器人当下已在汽车制造业中获得了广泛运用,诸如汽车底盘、座椅骨架、导轨、消声器以及液力变矩器等的焊接,特别是在汽车底盘的焊接生产中,其应用尤为普遍。在采用机器人焊接之后,极大地提升了焊接件的外观品质与内在质量,确保了质量的稳定性,降低了劳动强度,优化了劳动环境。
焊接机器人堪称焊接自动化领域的革命性进展,它突破了焊接刚性自动化的传统模式,开辟出了一种柔性自动化的崭新途径。就刚性的焊接自动化设备而言,当前它仅适用于中、大批量产品的自动化生产,故而在中、小批量产品的焊接生产中,手工焊依旧是主要的焊接方式。
焊接机器人让小批量产品的自动化焊接生产成为现实,鉴于机器人所具备的示教再现功能,焊接机器人完成一项焊接任务,仅需人力为其进行一次示教,它便能精准地重现示教的每一个操作步骤。倘若要机器人从事另一项工作,无需变更任何硬件,只需再次对其进行示教即可。正因如此,在一条焊接机器人生产线上,能够同时自动生产若干种焊件。
未来焊接的发展趋势:
1、提高焊接生产率是推动焊接技术发展的重要驱动力
2、提高准备车间的机械化,自动化水平是当前世界先进工业国家的重点发展方向。
3、焊接过程自动化,智能化是提高焊接质量稳定性,解决恶劣劳动条件的重要方向。
焊接技术自发明至今已有百多年历史,它几乎可以满足当前工业中一切重要产品生产制造的需要。但是新兴工业的发展仍然迫使焊接技术不断前进。微电子工业的发展促进微型连接工艺的和设备的发展;又如陶瓷材料和复合材料的发展促进了真空钎焊、真空扩散焊。宇航技术的发展也将促进空间焊接技术的发展。
焊接工艺近乎运用了世上所有能够加以利用的热源,诸如火焰、电弧、电阻、超声波、摩擦、等离子、电子束、激光束、微波等等。在历史进程中,每一种热源的诞生,皆伴随着新的焊接工艺的涌现。然而,时至今日,对于焊接热源的开发与研究仍未停歇。