热学特性是功率器件的灵魂!
芯片工作产生的热量通过不同的介质、界面传递到散热器,将热量散出,传递路径的热阻用Rthjc来表示。
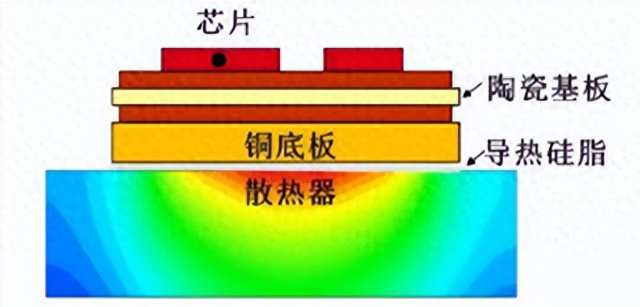
Note:
1)芯片面积越大,热阻越小;
2)热阻并非恒定值,受脉宽、占空比等影响;
3)对于新能源汽车直接冷却,热阻受冷却液流速的影响;
对于模组来讲,技术迭代主要围绕封装和连接。目前电机逆变器中IGBT模块普遍采用铜基板,上面焊接覆铜陶瓷板(DBC,DirectBond Copper),IGBT 及二极管芯片焊接在DBC板上,芯片间、芯片与DBC板、芯片与端口间一般通过铝绑线来连接,而基板下面通过导热硅脂与散热器连接进行水冷散热。模组封装和连接技术始终围绕基板、DBC板、焊接、绑定线及散热结构持续优化。
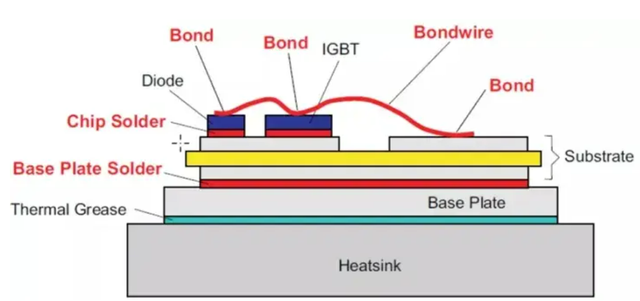
1)芯片间连接方式:铝线/铝带→铜线→平面式连接。
目前IGBT芯片之间大多通过铝线进行焊接,但线的粗细限制了电流强度,需要并联使用、或者改为铝带连接,但是铝质导线由于材料及结构问题易产生热疲劳加速老化断裂导致模块失效。
因此,Danfoss等厂商引入铜导线来提高电流容纳能力、改善高温疲劳性能,三菱电机、德尔福及赛米控则分别采用CuLead Frame(引线框架)、对称式的DBC板及柔性电路板实现芯片间的平面式连接,并与双面水冷结构相结合进一步改善散热,维持模块的稳定性。
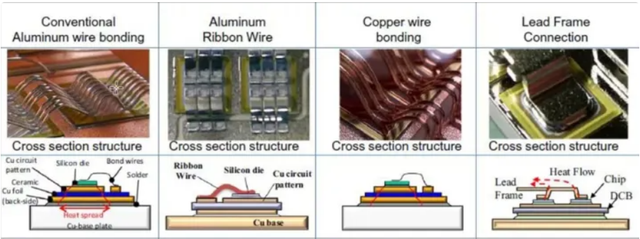
2)散热结构:单面间接散热→单面直接水冷→双面水冷结构。
最初的间接散热结构是将基板与散热器用导热硅脂进行连接,但导热硅脂散热性较差,根据Semikron公司的《功率半导体应用手册》,贡献了芯片到散热器之间50%以上的热阻。
单面直接水冷结构在基板背面增加针翅状(PinFin)散热结构,无需导热硅脂,直接插入散热水套中,热阻可降低40%以上。富士的第三代单面直接水冷结构则将基板散热针翅与水套实现一体化,进一步降低30%的热阻。目前英飞凌HP2/HPDrive、三菱电机J1系列、比亚迪V-215/V-315等主流汽车IGBT模块均采用单面直接水冷结构。
目前双面水冷的结构也开始逐步应用广泛,普遍在芯片正面采用平面式连接并加装Pin-Fin结构实现双面散热,目前代表性的应用包括InfineonHP DSC 模块、德尔福Viper模块(雪佛兰Volt)及日立的双面水冷模块(奥迪e-tron)
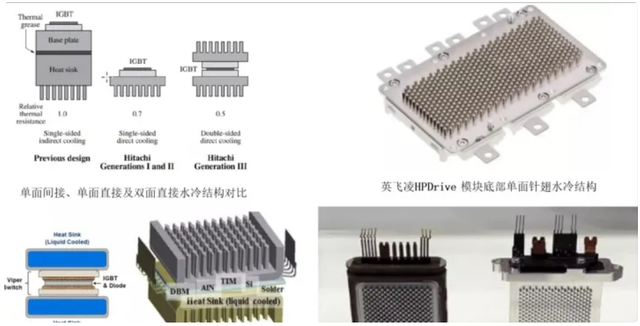
3)DBC板及基板:材料迭代
未来DBC板的材料由Al2O3→AlN→Si3N4迭代,基板材料由Cu向AlSiC迭代。
基板与DBC 板材料、以及DBC板与Si基芯片之间膨胀系数的差异决定了在大的温度变化时连接层是否会出现变形和脱落。DBC板材料需要重点考虑与Si基芯片热膨胀系数的匹配因素,其次考虑是否具备高热导率,目前应用最广的Al2O3陶瓷材料热导率较低、且与芯片的膨胀系数差异较大,局限性很明显,AlN、Si3N4凭借与Si材料更为接近的热膨胀系数、更高热导率开始逐步导入,比如德尔福Viper模块应用AlN陶瓷材料。
基板与散热器直接相连,需要重点考虑热导率,其次考虑与芯片、DBC之间热膨胀系数的匹配,目前常用铜基板来实现快速散热,而AlSiC热导率虽不如铜,但热膨胀系数更接近芯片及DBC,能够有效改善模块的热循环能力,渗透率快速提升。另外有部分厂商直接采取无基板的设计策略,比如赛米控汽车级功率模块SkiM直接将DBC通过高性能导热硅脂直接压在散热器上,配合银烧结技术最终将其温度循环能力提高15倍。
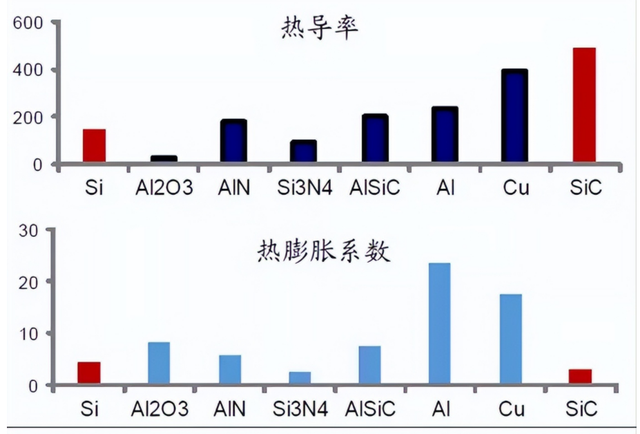
4)芯片、DBC板以及基板间连接方式:SnAg焊接→SnSb焊接、Ag/Cu烧结
目前芯片之间的绑定线、芯片与DBC板及DBC板与基板间的连接普遍通过SnAg焊接的方式,但温度循环产生应力容易导致DBC板和散热基板之间焊接层出现裂缝,焊接老化也会引起芯片温度上升,最终影响模块的寿命。
因此SnSb焊接、低温银烧结、铜烧结等技术逐步引入,比如富士电机车载IGBT模块在DBC和基板之间采用SnSb焊接代替SnAg焊接抑制裂痕扩展。
Semikron的SKiN技术采用Ag烧结,日立汽车功率模块采用Cu烧结,实现稳定的连接、更优的温度特性更长的寿命。
其中,根据Semikron官网,Ag烧结层厚度比焊接层至少薄70%,热导率提升3倍,热阻减小为1/15,但成本较高,Cu烧结的抗电子迁移能力及热循环能力更好,成本相较于Ag也明显降低,但烧结易出现氧化,对模块厂商的技术能力要求非常高。

珠海富士智能股份有限公司专注于IGBT散热铜底板研发与制造!http://www.fujichinon.com/
