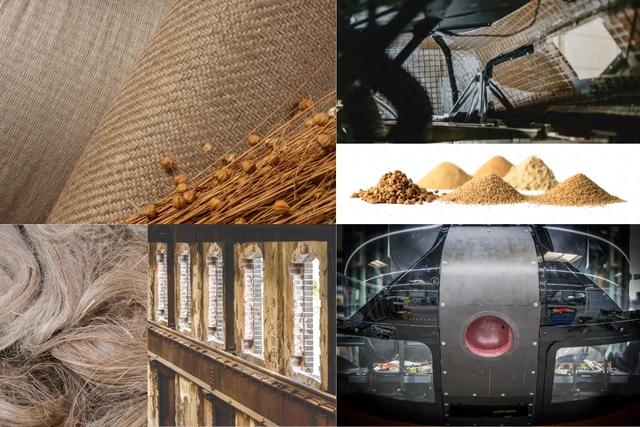
图片来源:Bcomp Ltd.(左上和右)、AZL Aachen(左下)、Braaksma Roos architects(左中)、BioPowder(右中)和空中客车公司(右下)
1980年代后期,联合国世界环境与发展委员会将“可持续性”定义为“在不损害子孙后代需求的情况下满足当代人的需求”。几十年来,这一概念一直受到人们的观察、讨论和思考,但在执行方面几乎没有什么进展。直到最近几年,可持续性才真正被视为是全球范围内的紧迫问题而成为几乎每个国家都要优先考虑的大事。这场运动由2015年签署的具有法律约束力的《巴黎协定》引领,此后,在法规、企业目标和客户需求的推动下,不断向前发展。
为减少排放和浪费、使用自然资源,以及改善从材料开发到产品制造的能源管理,并将这些贯穿到产品全生命周期及生命周期结束,复合材料行业正在付出巨大的努力。这种对完整循环的追求,是一条复杂而具有挑战性的道路,新的和正在推进的行动,不断地改变着被认为是“可持续性”的做法。复合材料的主要方法包括:开发生物材料,以及利用设备、传感器和数字化进行回收并实现节能。
本文将介绍一些公司在过去的一年中所分享的一些生物材料的进展情况。后续的文章还将讨论回收和节能方面的举措。
天然纤维及其他
在追求复合材料的可持续性方面,材料是最明显的选择,人们正在以多种方式进行开发,包括:增加对天然纤维的使用;掺入含有生物衍生成分的热固性或热塑性树脂,如,源自生物质的树脂和填料、增加生物衍生成分的百分比;上述两种方法的结合使用。
天然纤维,也称为天然纤维增强聚合物(NFRP)或天然纤维复合材料(NFC)。对于那些希望为客户提供可持续应用方案的公司而言,使用天然纤维已成为首选。这些纤维的来源多种多样,比如植物,包括大麻、黄麻、剑麻、亚麻和竹子等,甚至是动物,如丝和羊毛。这些材料的特点是可再生、提取所耗费的能源低、可生物降解且碳足迹小,同时,还具有像碳纤维或玻璃纤维等传统合成材料所具有的高力学性能。虽然NFRP越来越多地出现在各终端应用市场中,但也许,还没有一个终端应用领域能够像汽车市场那样对NFRP的追求持之以恒,其中,亚麻纤维增强材料尤其适用于从美观的内部组件到关键的安全结构等各个方面。
Bcomp Ltd.(瑞士弗里堡)的ampliTex 技术织物和powerRibs加固网格已成为这场运动的代名词,因为该公司持续地推动着亚麻纤维在汽车及其他领域的快速应用,而且其材料也已得到工业化应用——新款电动沃尔沃EX30的外观内饰部件和极星的内部和外部亚麻纤维复合材料面板、巴士空调盖以及赛车改装,比如用在BMW M4 GT4 上的外部车身组件,都使用了其材料。2024年4月,Bcomp完成了4000万美元的融资,以为其材料进入新的亚洲和北美市场提供支持。
亚麻纤维生产商 Groupe Depestele(法国诺曼底)是汽车亚麻纤维应用领域的另一家公司。该公司与 Greenboats(德国Breman)一起,在JEC World 2024展会上展示了格陵兰夏尔巴探险车,该车使用了由干浸渍天然纤维带制成的蒙皮、面板和完整结构。
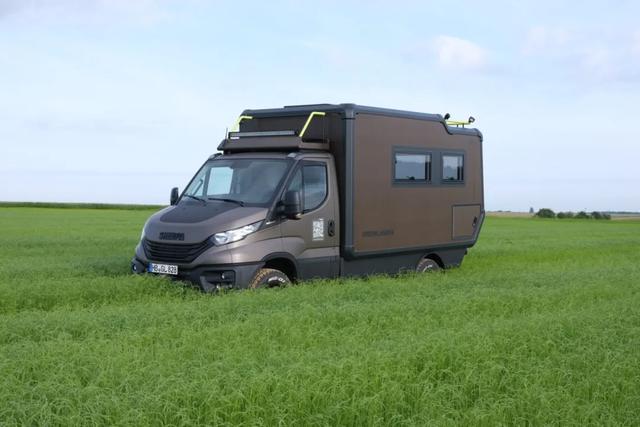
格陵兰夏尔巴探险车是一款长6370毫米、宽2170毫米、高3200毫米的车辆,凸显了使用亚麻纤维带来的美感(图片来源:Greenlander)
此外,大众汽车公司已与织物制造商初创公司 Revoltech GmbH(德国达姆施塔特)达成合作,从2028年开始开发并测试仿皮革替代品。这是一种结合了工业大麻纤维和全生物基粘合剂的材料,以用作大众汽车的表面材料。
同样,德国Denkendorf纺织与纤维研究所(DITF)和RBX Créations(法国Jonzac)因开发一种大麻纸浆而获奖,该纸浆正被进一步加工成长丝纺丝纤维素纤维。生麻可在当地种植并获得,然后采用RBX Créations的专利工艺将生麻加工成细纤维纸浆,并将其溶解在离子液体中。然后,将它作为 DITF 开发的湿法纺丝工艺的原材料,并以HighPerCell为名获得专利。该溶液在沉淀浴(使用可完全回收和再利用的溶剂)中被纺成纤维素纤维,用于纺织纤维、纱线和织物的开发。
根据欧洲亚麻-亚麻布与大麻联盟(法国巴黎)的数据,2024年的亚麻收获反映了积极的提取产量。该联盟在7月份指出:预计春亚麻的秸秆产量是每公顷平均6-7吨,这是自2019年以来从未见过的重要里程碑。当然,成功的收获意味着有大量的机会来满足行业需求。
对其他天然纤维的探索和使用,虽然还处于成熟化的阶段,但仍显示出它们具有吸引力。一种以美观应用为目标(如汽车、船舶和家具行业)的新型材料,使用 了Ohoskin(意大利西里西亚)的皮革替代品,该皮革由橙子和仙人掌副产品以及ReCarbon(意大利 Busto Arisizio)的回收碳纤维制成。
通常源于蘑菇根的菌丝体复合材料,正被学术领域作为建筑材料选项进行研究,如布里斯托大学(英国)的科学家们正在微调菌丝体复合材料的特性和生产,或者,okom wrks实验室(美国伊利诺伊州芝加哥)正在研究的材料,将麻秆这样的农业废弃物作为分散相,将真菌菌丝体作为基质相,目标是,将结构菌丝体用于建筑结构保温板(SIPs)。
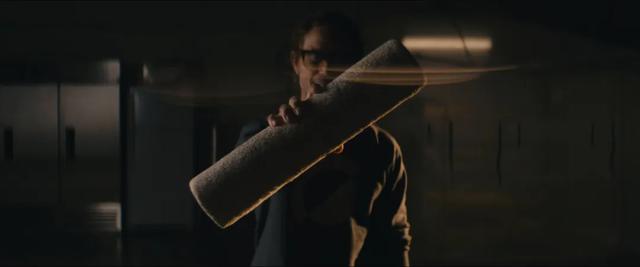
okom wrks实验室的菌丝体基材料的R值为 2.4,可为节能建筑提供更高的绝缘性能;抗压强度为1MPa,可提供耐用性和强度。与市场上其他基于菌丝体的产品相比,其强度高出1.1 个数量级,刚度高出3.9 个数量级(图片来源:okom wrks labs)
Sulapac(芬兰 Helskinki)成立于2016 年,致力于减少塑料垃圾。其材料组合包括:由来自工业副产品的木纤维与可生物降解的生物聚合物混合而成的木质复合材料,以及其他可回收的以及含有回收成分的生物基材料。这些材料可以大批量生产,具有可工业堆肥、来源可持续等优点。
此外,全球汽车供应商丰田合成株式会社(日本Kiyosu)宣布,开发了一种由从海水中提取的氢氧化镁(纤维状)制成的纤维增强材料,用于汽车内外饰部件。据说,由这种复合材料制成的表面更耐刮擦,并且在制造过程中需要的增强材料更少。
实现热固性树脂的生物基化
生物基(也称为生物衍生)树脂和添加剂已成为一种快速发展的趋势。采用这种方法的公司不是简单地使用天然纤维,而是专注于提高用于固定合成纤维的树脂基体的质量,或改进用于生产这些相同纤维的工艺。
尤其是热固性树脂,一直是复合材料行业的主要目标,如环氧树脂和乙烯基酯。虽然它们具有很强的力学性能和较高的玻璃化转变温度,但由于它们是共价交联的,所以使得产品生命周期后期的回收变得困难而又昂贵,或者几乎不可能。此外,这类树脂通常是采用石油原料开发,而石油原料是不可再生且不可持续的来源。
生物基热固性树脂(特别是部分生物衍生的树脂)的发布或推出已变得越来越普遍。比如,Exel Composites(芬兰Vantaa)的目标是,通过收购 Ineos(美国俄亥俄州都柏林)的Envirez生物基树脂,逐步在商业规模上淘汰使用碳氢化合物衍生树脂。与传统的源自原油的碳氢化合物树脂相比,该系统的化学成分中含有23%的生物基乙二醇,这意味着与之相关的生产排放减少了21%。美国国家可再生能源实验室(NREL,美国科罗拉多州戈尔登市)发布了有关生物质衍生的“聚酯共价适应性网络”或专为可回收风机叶片而开发的PECAN树脂。合作伙伴们发现,它优于某些树脂,并能够在使用寿命结束时(EOL)进行化学回收。

PECAN树脂已被用于制造9米长的风机叶片原型,以证明其可制造性(图片来源:Werner Slocum, NREL)
其他开发成果包括:Super Resin公司(日本东京)的植物基环氧树脂,这是源自日本雪松的乙二醇木质素与环氧树脂的混合物;Syensqo(比利时布鲁塞尔)的 MTM 49-3 树脂,该树脂含有30%的生物源单体,可满足汽车行业的可持续发展要求;Holland Composites(荷兰Lelystad)的Duplicor生物基耐火复合材料,它已在各种复合材料屋顶结构和立面中得到应用,包括荷兰的Van Gendt Hallen、The Pulse 以及最近的荷兰银行 ABN AMRO。“我们正在使用一种植物基树脂,并根据应用混合可能的纤维。”与Holland Composites合作的 Solico Engineering的董事总经理 Eric van Uden 解释说,“我们在夹层结构中不再使用PIR(聚异氰脲酸酯)或EPS(发泡聚苯乙烯)泡沫,而只使用回收的PET泡沫。”他承认,后者不是生物基的,但它确实有助于减少塑料对环境的影响。目前,Duplicor生物基耐火复合材料以预浸料和板材的形式在全球范围内销售。

荷兰银行大楼的重建将Duplicor生物复合材料用于立面(图片来源:Duplicor)
此外,其他一些公司介绍了正在使用生物基树脂系统的特定客户应用,或者提到了自身产品向使用可持续树脂的过渡:
1.聚酯树脂供应商 Büfa Composite Systems(德国Rastede)现在提供苯乙烯低的以及无苯乙烯的产品、生物基原材料以及使用回收原材料的产品。
2.Sicomin(法国Châteauneuf les Martigues)的 GreenPoxy 33 生物树脂系列已被用于制造具有亚麻纤维多轴增强层、CNC 铣削木芯和竹轨截面的环保型双头风筝板。
3.赫氏(美国康涅狄格州斯坦福德)的HexPly Nature系列生物衍生预浸料已被用于该公司的冬季运动产品生产中。
4.考泰斯德事隆(德国波恩)推出的Green+产品由20%的生物质材料和/或25% 的回收材料制成,以Pentatonic Green+形式进行展示,这是一种由丢弃在海洋中的渔网制成的复合材料电动汽车的电池壳。
还有一种趋势是,在树脂生产(包括生物基热塑性塑料)中,将木质素等生物材料用于前体材料。比如,由可持续技术创新者 Sonichem(前身为Bio-Sep,英国南安普敦)领导的一个联盟,希望用可再生、经济高效的替代品来取代常用的石化产品,用于生产汽车行业所需的塑料、树脂和复合材料,这包括将锯末(林业作业的生物质副产品)转化为高质量的木质素,作为生物基平台化学品的基础。另一个例子是,Synergy Horizon Poland(波兰 Dabrowka)与克劳斯玛菲(德国Laatzen)之间的联合开发研究:在挤出过程中使用30%的水解木质素开发生物基PLA。克劳斯玛菲首先利用其ZE Blue Power 28实验室挤出机及其小型ZE Blue Power 42生产型配混机来掺入这种天然材料。
评估生物基前体
不仅生物衍生树脂受到人们的关注,而且用于合成纤维(主要是碳纤维)的工艺也在被重新评估。传统上,碳纤维是由各种不可再生的前体制成的,包括聚丙烯腈(PAN)、人造丝和沥青。这些纤维经过化学处理和碳化,被制成当今许多制造商使用的高强度纤维。然而,随着复合材料制造方式不断向可持续方向发展,生物基富碳前体(如木质素或生物基 PAN)正越来越多地得到研究和证明。在寻求将木质素作为生物复合材料来源方面,DITF是一家一直走的最前沿的组织,其研究包括将水纺木质素纤维作为PAN前体的替代品,以及将木质素基保护涂层用于纱线和织物表面,其大量的实力和技术中心致力于解决从分子和纤维化学到最终用途产品的所有问题。
该领域的其他一些公司已经或将要实现生物基PAN替代品的商业化。比如,Southern Research 开发的以生物质为重点的丙烯腈(CAN)生产工艺于2023年获得Trillium Renewable Chemicals(美国田纳西州诺克斯维尔)的许可,正被商业化用于生产CAN和乙腈。生物质,即称为木糖和葡萄糖的非食用糖(或碳水化合物),是从木质生物质中获取的。此后,Trillium 一直致力于在美国建造一个市场规模的示范工厂。
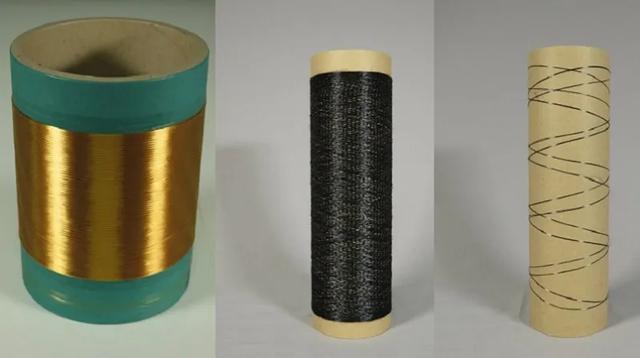
水纺木质素前体纤维、稳定和碳化的连续长丝(图片来源:DITF)
通过另一种方法,空中客车公司(法国图卢兹)使用了生物基碳纤维的直升机机头面板,该面板是用空中客车团队生产的生物基丙烯腈前体开发的。这种替代丙烯腈源于国际可持续性与碳认证(ISCC)认可的非化石原料,如木材和食物垃圾、回收的食用油和/或藻类,以及氨和丙烯的可再生来源。测试表明,这种机头面板具有与传统碳纤维增强聚合物(CFRP)面板相同的性能,但碳排放明显更低。
粘合剂、添加剂的新时代
添加剂和粘合剂虽然可能不像纤维和生物聚合物那样应用广泛,但在复合材料部件的可持续性方面仍然发挥着重要作用。
匹兹堡大学斯旺森工程学院的研究人员们从水凝胶、液晶弹性体和贻贝的天然生物粘合剂中汲取灵感,在分子水平上优化了粘合剂系统。“这项技术对于增强平台和管道等水下基础设施至关重要。” 匹兹堡大学斯旺森工程学院机械工程和材料科学助理教授、该项目的研究人员之一Qihan Liu说道。
此外,分布在欧洲西北部的项目合作伙伴们正在Biobased Debondable Adhesives(BiDebA)项目中展开合作,开发源自可再生资源的生物基粘合剂,以促进复合材料的脱粘以及在运输市场的循环利用。
BioPowder(马耳他Birkikara)是纤维添加剂和功能性复合材料填料的专业公司,该公司为如何利用添加剂实现可持续性提供了很好的范例。其Olea FP系列生物基和可生物降解的功能性复合材料填料由升级回收的橄榄石制成,具有高稳定性、低吸水吸油性、硬度高、耐磨性好等特点,并提供多种纹理效果。
纤维和树脂可持续发展重点
可持续性还推动了各种正在进行的项目,实施这些项目的联盟旨在解决整个复合材料系统的问题。一个例子是EOLIAN,这是为回收风机叶片而付出巨大努力的结果。这个由欧盟资助的项目采用生物基vitrimer树脂和带有集成传感器(用以实现结构健康监测)的玄武岩纤维,开发可修复和可回收的叶片。
SUSPENS 项目正在应对的挑战是,在为汽车、航海休闲和航空领域制造夹层复合材料和空心结构的过程中减少对环境的影响。该项目第一年致力于开发材料,特别是要用95%以上源自生物的环氧树脂和聚酯来开发树脂,以及用天然纤维和回收的碳纤维和玻璃纤维来制造可持续的增强材料。该项目的其余部分将通过试样测试来验证材料性能。
同时,由DITF领导的 DACCUS-Pre 项目制作的墙体元件示范件,采用了一种由天然辉长岩、木质素基碳纤维和生物炭制成的新型复合材料,这是钢筋混凝土的替代品,可用作建筑材料。
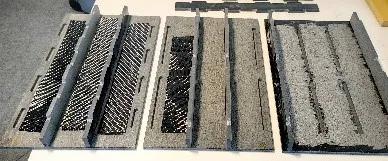
通过 DACCUS-Pre 项目对墙体构件进行结构设计,这是钢筋混凝土的替代品(图片来源:DITF)
CUBIC项目是一项始于2023年9月的研究和创新计划,由 Aitiip 技术中心(西班牙Zaragoza)领导,致力于研究生物基中间体如长丝、片材(有机片材和单向带)、粒料和粉末以及它们的组合,以克服当前技术方面的限制。该项目考虑了技术设计、要使用的材料、加工性和生命周期等方面的问题,目前已创造了不同类型的生物基聚酰胺、碳纤维和环氧树脂。
同样值得一提的是由西班牙研究中心Ideko(Elgoibar)领导的BioStruct项目,在此项目中的欧洲合作伙伴致力于到2026年解决与在风能或海事等行业的工业结构中使用生物基复合材料相关的技术问题。虽然其目标更多的是促进天然纤维和生物树脂的使用,而不是其自身开发的选项,但这项研究仍有助于了解生物基材料的力学性能,以准确设计结构部件并使其能够在此类应用中得到使用。
除上述研究项目外,还有一些公司已经在考虑采用生物基树脂和纤维来制造商业化的部件。Greenboats GmbH 就是一个例子。该公司成立于2013年,不仅将自身定位为一家用亚麻纤维和生物基树脂建造船只的船舶制造公司,还是一家专门从事天然纤维复合材料的技术公司。该公司不断调整其产品,目前已从夹芯板的大批量生产发展到可持续露营车的制造。
生物材料将不可或缺
尽管该领域取得了进展,但生物复合材料仍有许多挑战需要克服。比如,根据材料的不同,它们的成本仍高于更传统的基于化石燃料的复合材料,并且其产量可能并不总能满足行业所需(如亚麻纤维的可用性取决于给定年份内的作物产量)。此外,没有必要的性能数据,特别是种类繁多的成分,这,已成为考虑选择一些生物材料用于商业应用的巨大障碍。
但无论面临何种挑战,在如此广泛的范围内,更可持续的复合材料(天然纤维、生物基前体、100%或生物基热固性树脂以及生物基粘合剂和添加剂)的开发和商业化,在推动行业可持续发展方面,显示出巨大的前景。
文章来源:长三角复合材料碳纤维技术创新
注:本站转载的文章大部分收集于互联网,文章版权归原作者及原出处所有。文中观点仅供分享交流,如涉及版权等问题,请您告知,我将及时处理!