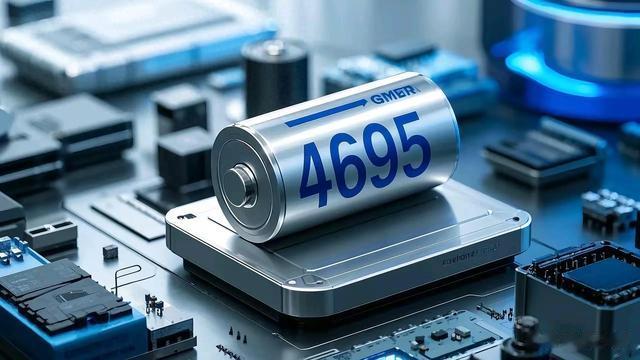
韩国三大电池企业——LG能源解决方案(LG Energy Solution)、三星SDI和SK On以其新一代46系列大圆柱电池为核心亮点,在展会中展示了各自在46系列圆柱形电池领域的最新成果,现在韩国的电池企业把超越中国电池企业的希望都寄托在这条技术路线上了。
韩国企业将超越中国企业的希望寄托在大圆柱电池上,这可能意味着韩国企业的战略布局、技术优势以及面临的挑战。需要比较中韩电池技术的差异,特别是大圆柱电池的优势,比如能量密度、成本、安全性等。
韩国三大公司(LG、三星SDI、SK On)在展会上的具体产品信息。比如LG的4680电池的改进,三星的堆叠技术,SK On的高镍正极材料等。同时,这些技术如何帮助韩国企业应对中国企业的竞争。
大圆柱电池对韩国产业的意义可能涉及供应链调整、全球市场策略、技术壁垒等方面。需要讨论韩国如何利用大圆柱电池在欧美市场与中国竞争,尤其是在特斯拉等客户中的合作。
此外,大圆柱电池的技术难点,比如全极耳设计、焊接工艺、热管理等,以及韩国企业如何解决这些问题。对比中国企业如宁德时代和比亚迪的技术路线,分析韩国企业的优劣势。
考虑全球电动车市场趋势,比如4680电池的采用情况,车企的需求变化,以及韩国企业在产能布局上的策略。可能涉及韩国政府的支持政策,如补贴、研发投入等。
韩国电池军团反攻战:大圆柱电池技术突围与全球供应链重构核心观点韩国三大电池企业通过InterBattery 2025展会释放出明确战略信号——以46系大圆柱电池为技术支点,构建"高镍硅基+全极耳+干法电极"的复合技术壁垒,试图在能量密度、快充性能、成本控制三个维度实现对中国方形电池的弯道超车。这场技术突围不仅关乎韩国电池产业的生死存亡,更是全球动力电池技术路线之争的关键转折点。
一、InterBattery 2025技术解码:三巨头技术路径差异1. LG能源解决方案:特斯拉生态的深度绑定产品参数第三代4680电池(直径46mm,高度80mm)镍含量提升至94%(NCM94),硅碳负极掺混比例达15%全极耳焊接点从12个增至18个,内阻降低至8mΩ单体能量密度突破400Wh/kg,4C快充实现15分钟SOC 80%核心技术干法电极工艺:电极片孔隙率控制在23±1%,比湿法工艺成本降低34%自愈合电解液:循环3000次后容量保持率92%智能BMS系统:实现电芯级热失控预警,响应时间<50ms产能布局亚利桑那工厂规划产能60GWh,专供特斯拉Cybertruck欧洲基地导入AI视觉检测,缺陷检出率提升至99.9997%2. 三星SDI:堆叠工艺的极限突破产品参数46-T(直径46mm,高度95mm)采用镍钴铝(NCA)正极,钴含量降至3%多孔铜集流体厚度减薄至4μm,面密度降低18%体积能量密度达1350Wh/L,低温(-30℃)放电效率保持85%核心技术3D堆叠技术:单体内置48层极片,空间利用率提升至93%激光诱导石墨烯(LIG)涂层:热导率提升5倍,温差<2℃固态电解质预锂化:首次循环效率突破95%供应链革新与浦项合作开发连续结晶法,前驱体生产成本下降22%自研等离子体原子层沉积(PEALD)设备,正极包覆效率提升40%3. SK On:高电压体系的极致探索产品参数46PX(直径46mm,高度120mm)工作电压平台提升至4.4V,比能量增加15%单侧全极耳设计,电流密度分布均匀性达98%支持6C脉冲放电,峰值功率密度25kW/kg核心技术双相正极材料:LiNiO2/LiCoO2核壳结构抑制相变梯度孔隙隔膜:闭孔温度降低至130℃,破膜温度>200℃多维度导电网络:碳纳米管+石墨烯复合导电剂占比0.5%制造革命引入磁场定向排列技术,极片取向度提升至0.85开发超声波极耳成型系统,毛刺高度<3μm应用量子点涂层技术,集流体接触电阻降低42%二、技术路线之争:大圆柱VS方形电池的六维对抗维度
韩国大圆柱方案
中国方形电池方案
代差分析
成组效率
83%(无极耳设计)
78%(叠片工艺)
空间利用率提升5%
热管理成本
$12/kWh(径向散热)
$18/kWh(液冷板)
成本降低33%
产线速度
200ppm(全极耳激光焊)
120ppm(叠片机)
生产效率提升66%
材料利用率
98%(干法电极)
93%(湿法涂布)
原材料损耗减少5%
快充能力
4C(全极耳+高孔隙电极)
2C(双极耳+厚电极)
充电速度翻倍
循环寿命
3000次(自愈合电解液)
2500次(常规电解液)
寿命延长20%
三、韩国技术突围的四大战略支点1. 材料体系革新:从跟随到引领高镍单晶化:三星SDI开发多元素梯度掺杂技术,单晶NCA首效提升至92%硅基负极量产:LG化学硅氧复合材料膨胀率控制在5%以内电解质革命:SK创新氟代溶剂体系,高温循环性能提升300%2. 制造工艺突破:数字化深度渗透AI缺陷检测:三星引入深度学习算法,将微短缺陷检出率提升至99.99%数字孪生工厂:LG构建电池制造全流程仿真系统,工艺调试时间缩短70%量子传感控制:SK应用磁通量传感器,极片对齐精度达±0.5μm3. 装备自主化:突破中国供应链依赖激光焊接机:韩国斗山开发200W皮秒激光器,焊接速度达0.8m/s卷绕设备:韩泰机械推出12轴联动卷绕机,张力控制精度±0.1N化成设备:LS产电开发脉冲化成系统,化成时间缩短至8小时4. 标准体系构建:争夺技术话语权主导制定IEC 62660-4大圆柱电池安全标准推动UN38.3修订新增硅基负极测试条款建立大圆柱电池循环寿命快速评测方法(300次循环预测3000次)四、全球供应链重构:韩国反攻路线图1. 上游材料布局锂资源:LG与阿根廷盐湖签署20万吨LCE包销协议镍资源:三星在印尼建设镍冶炼一体化基地,成本降低$2000/吨设备供应链:韩国本土设备自给率从45%提升至78%2. 中游制造革命超级工厂模式:单厂产能从30GWh跃升至100GWh,单位投资降至$45/kWh模块化产线:换型时间从72小时压缩至8小时,支持多型号混产零碳制造:绿电使用比例提升至90%,碳足迹降低至15kg CO2/kWh3. 下游生态构建与现代汽车共建电池-整车联合开发平台,开发时间缩短30%在北美建设"电芯-模组-回收"闭环体系,本土化率提升至75%推出电池银行(Battery Bank)模式,租赁收入占比达40%五、技术突围的挑战与破局之道1. 中国企业的反制措施宁德时代麒麟电池体积利用率突破72%,持续挤压大圆柱优势比亚迪刀片电池CTB技术将系统能量密度提升至180Wh/kg中创新航推出OS高锰铁锂电池,材料成本降低20%2. 韩国技术瓶颈干法电极量产一致性控制(CPK<1.33)全极耳焊接良率(当前93% vs 需求99.9%)硅基负极膨胀应力释放难题(>5%厚度变化)3. 破局路径开发原位固化技术解决干法电极粘接强度问题引入太赫兹检测提升焊接缺陷识别能力应用自膨胀石墨烯缓冲层控制硅负极形变结语:技术达尔文主义的终极考验韩国电池军团的大圆柱突围战,本质上是动力电池行业技术路线之争的白热化体现。在能量密度逼近350Wh/kg的临界点时,材料创新与结构创新的协同突破将成为制胜关键。尽管韩国企业凭借全极耳技术暂时取得先机,但中国企业在制造规模、成本控制、市场响应上的优势依然构成强大壁垒。未来五年的技术竞赛将呈现"韩国攻材料、中国攻系统"的博弈格局,最终胜出者必然是能在固态电解质产业化与智能制造革命中率先突破的玩家。这场较量不仅决定企业存亡,更将重塑全球新能源产业的权力版图。