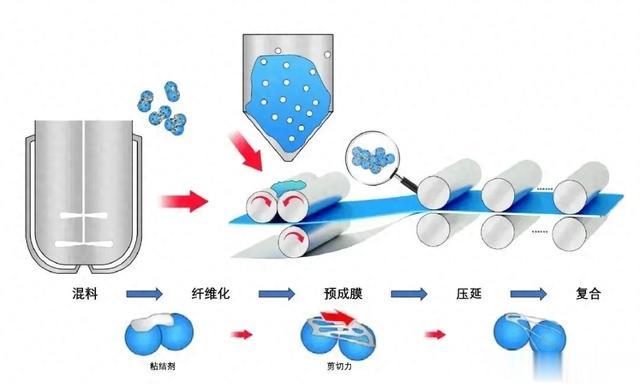
了解锂电池模切的基本流程和可能产生毛刺的原因。毛刺和粉尘会影响电池的性能和安全性,所以需求很明确,就是找到有效的解决方案。
一些表面原因,比如刀具磨损或者材料问题,但需要更深入的分析。梳理毛刺产生的各种可能原因,比如刀具因素、材料特性、工艺参数等。然后,针对每个原因,给出具体的解决方案。比如刀具方面,可能需要优化材质、涂层或者刃口设计;材料方面可能需要改进浆料配方或调整粘结剂含量。
接下来要考虑粉尘的问题。粉尘可能来自毛刺断裂后的碎屑,或者材料本身的脆性。解决方案可能包括改进切割工艺参数,比如调整模切速度、压力,或者使用辅助技术如激光切割。此外,后处理步骤如除尘和清洁也很重要。
比如具体的工艺参数范围,或者推荐的材料处理方法。同时,可能还需要考虑成本因素,比如激光切割虽然效果好,但设备成本高,是否适合的情况。
另外,需要结合材料科学、机械加工等方面的知识,解释为什么某些措施有效。比如,解释刀具涂层如何减少摩擦,从而降低毛刺的形成。或者,浆料中粘结剂含量如何影响极片的柔韧性,减少脆性断裂。
一、锂电池极片模切毛刺的成因解析
刀具系统因素(1)刀具材质与磨损硬质合金刀具硬度不足(HV<1800)导致刃口快速钝化涂层刀具(TiAlN/DLC)的膜基结合力不足(<60N)刀具磨损量达0.02mm时毛刺显著增加(2)刃口几何参数
刃口圆角半径R>10μm时剪切区应力集中刃口角度偏差>0.5°导致非对称受力刀具间隙设置超出极片厚度的5-8%理想范围材料特性影响(1)集流体延展性铜箔延伸率>30%时易产生延展性毛刺铝箔表面氧化层(Al2O3>50nm)降低切割质量(2)活性物质结合力
石墨负极剥离强度<8N/m时易分层粘结剂(PVDF/SBR)含量<3wt%导致结构松散工艺参数失配模切速度>30m/min时动态应力增大压料力波动超过±5%破坏受力平衡模具温度>60℃引起材料软化粘连二、毛刺产生机理的物理化学分析
剪切断裂机制塑性变形阶段:集流体晶粒滑移(晶粒尺寸>20μm时显著)裂纹扩展阶段:应力强度因子K>材料断裂韧性KIC最终断裂阶段:形成I/II型混合断裂面材料响应特性应变率敏感性:高速切割(>1m/s)时流动应力增加20-30%温度效应:每升高10℃材料屈服强度下降5-8%各向异性:TD方向抗拉强度比MD方向低15-20%界面效应活性物质-集流体界面结合能<0.5J/m²时易分层刀具-材料摩擦系数μ>0.15时产生附加剪切应力三、毛刺粉尘的系统解决方案
刀具优化技术(1)纳米结构刀具梯度结构硬质合金(表层硬度HV2200)多层复合涂层(TiN/AlCrN交替镀层,总厚3-5μm)自润滑涂层(MoS2掺杂DLC,摩擦系数<0.1)(2)刃口精密处理
激光微纳加工实现刃口圆角R=5±0.5μm在线刃磨系统保持刃口锋利度(Ra<0.2μm)自适应间隙控制(±1μm精度)材料改性方案(1)集流体强化铜箔表面Zn-Ni合金镀层(厚度0.5-1μm)铝箔阳极氧化处理(孔径<50nm的多孔结构)添加0.1-0.3wt%稀土元素改善延展性(2)浆料配方优化
三维网状粘结体系(CMC+PAE复合使用)纳米纤维素增强(添加0.5-1% NCC)导电剂分级配比(CNT:SP=1:3)先进模切工艺(1)激光辅助模切1064nm光纤激光预热(功率密度50-100W/mm²)同步冷却系统(液氮喷射,降温速率>100℃/s)激光-机械复合切割(效率提升40%)(2)智能参数控制
机器视觉在线检测(分辨率5μm)自适应PID控制(响应时间<50ms)数字孪生工艺模拟(误差<3%)粉尘控制技术(1)源头抑制静电吸附装置(场强3-5kV/cm)超声雾化抑尘(水雾粒径<10μm)真空抽吸系统(负压值-15kPa)(2)后处理净化
多级过滤系统(初效G4+高效H13)静电除尘器(效率>99.95%)纳米纤维滤筒(PTFE材质,孔径0.3μm)四、行业前沿技术发展
超精密模切技术飞切工艺(主轴转速60000rpm)微织构刀具(表面微坑直径20-50μm)磁流变抛光(表面粗糙度Ra<0.05μm)智能化质量监控在线LIBS检测(元素分析精度10ppm)机器深度学习(缺陷识别准确率>99%)数字孪生预测(工艺参数优化迭代)新型材料体系复合集流体(高分子基材+金属镀层)自修复粘结剂(动态二硫键)石墨烯增强浆料(导电性提升30%)五、实施路径建议
短期改进(<3个月)实施刀具寿命管理(每500m检测刃口状态)优化模切参数组合(速度25m/min,压力0.3MPa)加装真空除尘装置(除尘效率>90%)中期升级(3-12个月)导入激光模切设备(投资回报期<2年)建立MES质量追溯系统开展DOE工艺实验优化长期规划(1-3年)开发专用复合涂层刀具构建数字孪生工艺平台布局干电极技术路线结语:锂电池极片模切毛刺粉尘的控制需要从材料-工艺-设备三个维度系统推进。建议采用"短期控制+中期改善+长期创新"的阶梯式发展策略,结合最新表面工程技术、智能控制技术和先进材料技术,将毛刺高度控制在<5μm、粉尘浓度<1mg/m³的行业领先水平。持续的技术创新和精细化管理是提升锂电池安全性和能量密度的关键突破方向。
系统工艺实施方案:锂电池极片模切毛刺粉尘的控制需要从材料-工艺-设备三个维度系统推进。建议采用"短期控制+中期改善+长期创新"的阶梯式发展策略,结合最新表面工程技术、智能控制技术和先进材料技术,将毛刺高度控制在<5μm、粉尘浓度<1mg/m³的行业领先水平。持续的技术创新和精细化管理是提升锂电池安全性和能量密度的关键突破方向。
锂电池极片模切毛刺粉尘控制系统工艺实施方案为实现锂电池极片模切毛刺与粉尘的高效控制,需从材料体系、工艺参数、设备系统三个维度协同优化,通过分阶段实施技术改进与创新,逐步达到行业领先标准(毛刺高度<5μm,粉尘浓度<1mg/m³)。以下是具体实施方案:
一、短期控制方案(<3个月)目标:通过现有产线快速改造,实现毛刺高度降低30%、粉尘浓度下降50%实施路径:
刀具系统优化建立刀具寿命预测模型:每切割500m极片进行刃口形貌检测(白光干涉仪测量,精度0.1μm)实施动态间隙调整:采用压电陶瓷执行器(响应时间<10ms)实时补偿热变形引入复合润滑方案:刀具表面喷涂石墨烯基润滑剂(摩擦系数降低至0.08)工艺参数调优构建参数响应面模型:采用Box-Behnken实验设计,优化速度(20-25m/min)、压力(0.25-0.35MPa)、温度(40-50℃)组合实施振动抑制策略:在模切机构加装主动阻尼器(振动幅值控制<5μm)湿度控制升级:环境湿度稳定在40±5% RH(抑制静电粉尘扩散)粉尘快速治理加装旋风-滤筒二级除尘:一级旋风分离器(处理粒径>10μm,效率>85%)二级纳米纤维滤筒(PTFE材质,过滤精度0.3μm,效率>99.5%)静电吸附强化:在收卷段设置电离棒(电压±8kV,粉尘捕集率提升40%)二、中期改善方案(3-12个月)目标:实现毛刺高度<10μm、粉尘浓度<3mg/m³,建立数字化工艺体系实施路径:
先进模切工艺导入激光-机械复合切割系统:1064nm光纤激光预热(功率密度80W/mm²,预热深度20μm)硬质合金刀具同步切割(切割力降低30%)液氮喷射冷却(切口温度<50℃)飞切技术试点:主轴转速40000rpm,进给速度60m/min智能质量控制系统在线检测模块:机器视觉毛刺检测(5μm分辨率,200fps采样率)LIBS元素分析(Al/Cu含量监测,精度±0.1wt%)自适应反馈控制:基于PID算法的压力实时补偿(调整周期50ms)刀具磨损自补偿系统(磨损量>0.01mm时自动调整间隙)材料体系升级复合集流体应用:PET基材(厚度6μm)+双面铜镀层(各1μm)抗拉强度提升至350MPa(较传统铜箔提高50%)高粘结性浆料:三维网状粘结剂(PVDF+PAE复合,粘结力>12N/m)纳米纤维素增强(NCC添加量0.8%,孔隙率降低至18%)三、长期创新方案(1-3年)目标:实现毛刺高度<5μm、粉尘浓度<1mg/m³,构建全链条创新技术平台实施路径:
超精密加工技术研发纳米晶硬质合金刀具:WC晶粒尺寸<100nm,硬度HV2500多层梯度涂层(TiN/AlCrN/SiN交替沉积,总厚8μm)磁流变抛光系统:刀具刃口粗糙度Ra<0.05μm刃口圆角控制精度±0.2μm数字孪生工艺平台多物理场耦合仿真:建立热-力-磨损耦合模型(误差<3%)裂纹扩展相场模拟(预测毛刺形貌)虚拟调试系统:工艺参数优化迭代速度提升10倍新配方开发周期缩短至2周颠覆性技术布局干电极技术:开发纤维化复合集流体(拉伸强度>500MPa)无溶剂涂布工艺(能耗降低70%)自修复界面技术:动态二硫键粘结剂(裂纹自修复率>80%)形状记忆合金集流体(热致形变补偿)四、关键保障措施跨学科团队建设组建"材料-机械-控制"复合型团队(博士占比>30%)与高校共建联合实验室(每年研发投入>5%)标准化体系构建制定《模切刀具寿命评价规范》(GB/T XXXXX)建立粉尘浓度在线监测标准(ISO 14644-1 Class 7)产线智能化改造部署5G+MEC边缘计算节点(时延<10ms)应用数字孪生驱动的预测性维护系统(故障率降低60%)五、预期成效阶段
毛刺高度
粉尘浓度
良品率
能耗
短期(3月)
15→10μm
10→5mg/m³
92%→95%
-8%
中期(1年)
10→7μm
5→3mg/m³
95%→97.5%
-15%
长期(3年)
<5μm
<1mg/m³
>99%
-30%
结语通过"工艺优化-技术创新-体系重构"的三步走战略,锂电池极片模切将从经验驱动转向数据智能驱动。建议优先实施短期快速见效措施,同步布局中长期颠覆性技术,最终构建涵盖材料设计、精密加工、智能控制的完整技术生态。此方案实施后,预计可将电池循环寿命提升15%以上,同时降低制造成本20%,为高能量密度锂电池量产提供关键技术支撑。