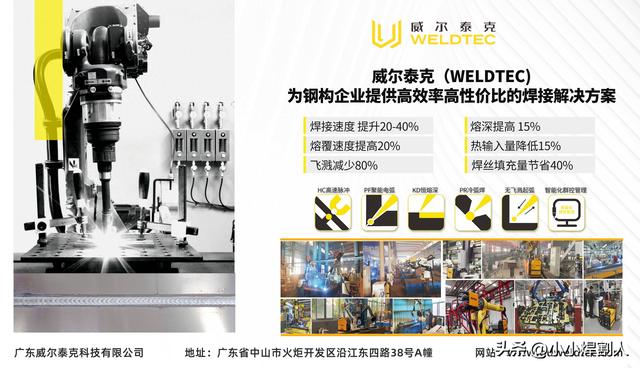
一、点焊焊接工艺参数及要点
表1 焊接工艺参数及要点

点焊接头的最小搭边宽度和焊点的最小点距
a)点焊接头的最小搭边宽度见图1
最小搭边宽度
b = 4δ+8 (当δ1<δ2 时,按δ2计算 )
其中 b ——搭边宽度,mm
δ——板厚,mm
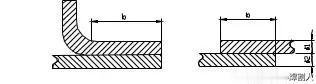
图1 搭边尺寸
点焊接头的最小搭边宽度和焊点的最小点距见表2
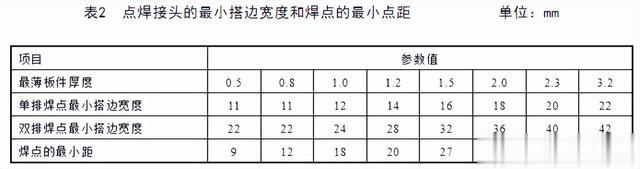
二、点焊的质量及要求
焊点外观上要求表面压痕浅而平滑,呈均匀过渡,无明显凸肩或局部挤压的表面鼓包;外表面没有明显的环状或径向裂纹,也无熔化、烧伤或粘附的铜合金。
从内部看,焊核形状规则、均匀,无超标的裂纹和缩孔等内部缺陷,以及热影响区金属组织和力学性能不发生明显变化等。
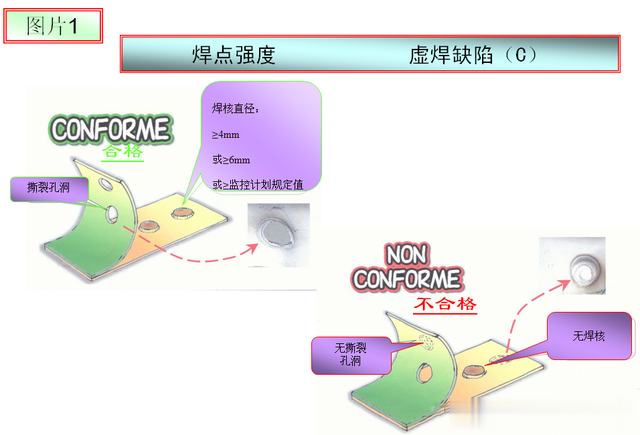
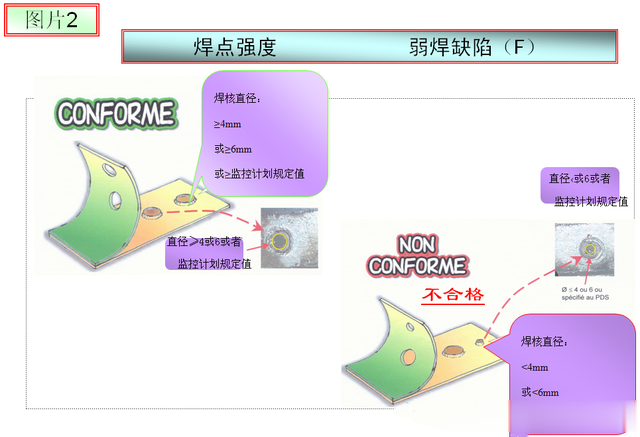
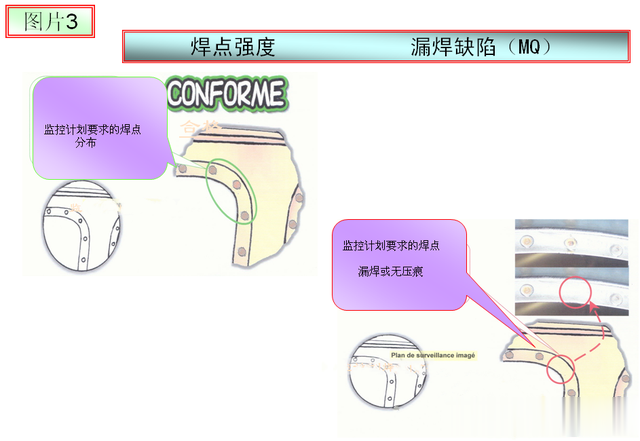
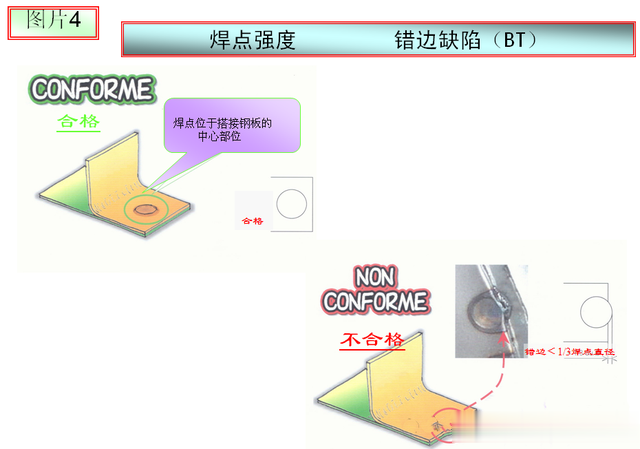
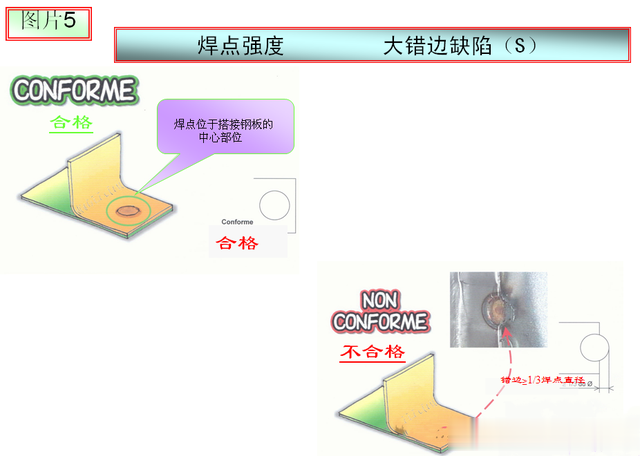
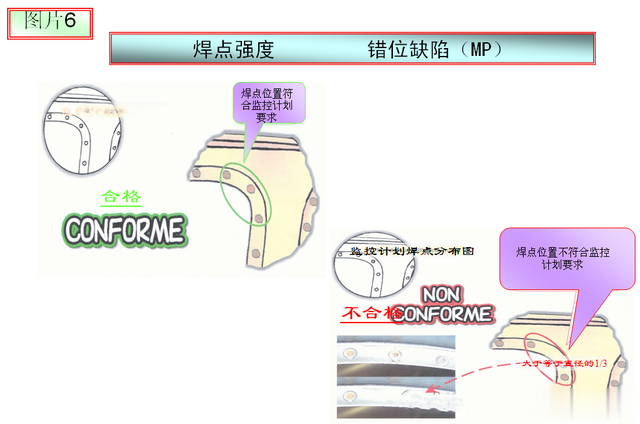
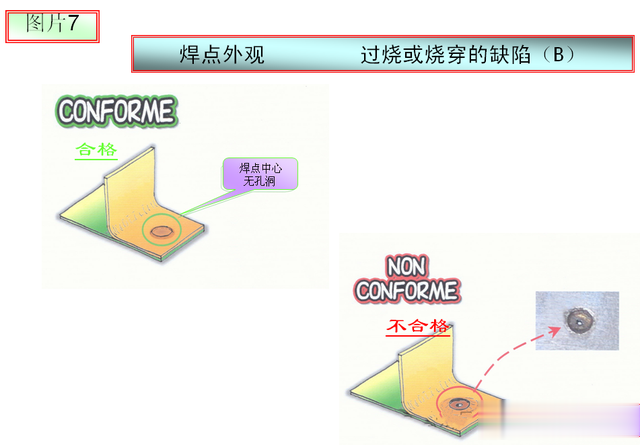
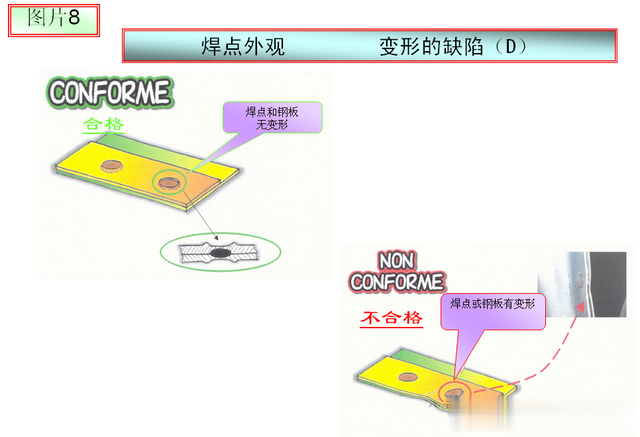
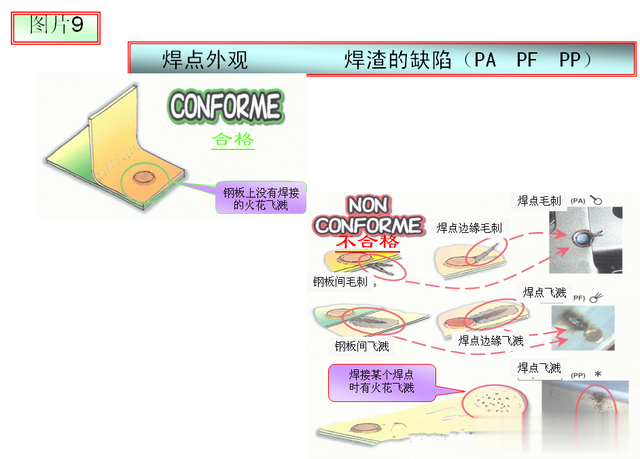
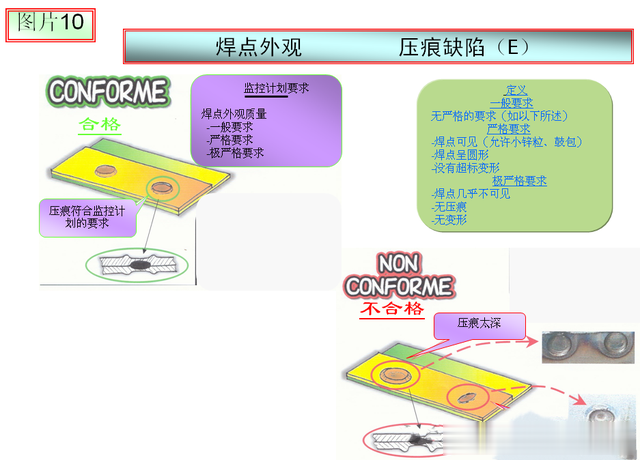
焊点基本要求
(1)焊点直径要求
焊点种类
焊点直径
钢板厚度
普通焊点
Φ≥4mm
0.6mm≤ δ ≤1.27mm
Φ≥6mm
1.27mm≤ δ ≤3.0mm
特殊焊点
Φ≥4mm
0.4mm≤ δ ≤0.8mm
Φ≥5mm
0.8mm≤ δ ≤1.2mm
Φ≥7mm
1.2mm≤ δ ≤3.0mm
(2)焊点间距 为保障产品质量,各焊点间的相互距离是有一定要求的。
最小板厚
e≤1.27mm
e>1.27mm
焊接
20mm
30mm
涂胶-焊接
45mm
45mm
(3)焊点边距 靠近切边边缘的焊点,其与边缘的最小距离应满足以下要求。
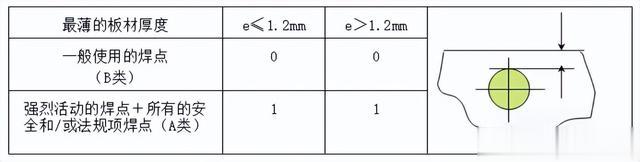
焊点具体要求
检查的每一个焊点都有一个编号,并与制造号一致。检查卡的图上详细注明焊点位置及编号,并列出每个焊点的外观、直径和属性。
⑴焊点直径:即焊点应有的最小直径。当焊点为椭圆或不规则时,取最大和最小直径的平均值。当作目视检查或非破坏性检查时,可以压痕底部直径判别。当破坏性检查时,以实际熔核直径为准。
⑵焊点属性(At或△):焊点的属性分为A类和B类。A类焊点通过以下标记表示:
S:安全项焊点
R:法规项焊点
SR:安全法规项焊点
⑶ 焊点外观要求指数:车身上的焊点,其外观质量要求因其所处车身位置不同而不同。如形成商品车后依然可见的外露焊点,其外观质量直接影响整车的外观质量,因而这些焊点的外观要求较高。另有些因安全因素而有要求的焊点,如在焊装以后的工序中或将来车辆维修时,会因为焊点的外观不好或毛刺而划伤操作人员或零件等。焊点可能的外观缺陷有:压痕、焊接变形、毛刺、飞溅、过烧、烧穿等等。我们用焊点的外观等级指数表示焊点缺陷类别和轻重程度:
“2”或PS:外观很好,允许轻微压痕,禁止其它缺陷
“2 2”或PS:外观好,允许压痕,禁止其它缺陷
“6”或PP:允许压痕、变形,禁止毛刺等其它缺陷
“7”或C:允许压痕、变形和较小毛刺,禁止其它缺陷
焊点整体要求
每辆车身上的缺陷焊点数不能超过5%,前托架上的缺陷焊点不能超过3个!超过极限值时应限期整改或停线返修。
为防止缺陷焊点集中,在零件上的一组或一系列焊点中,允许有缺陷的焊点数量是有限制的,如下表:
一组B类焊点数量
1-4
5-9
10-19
>20
允许有缺陷焊点数
0(重新点焊或返修)
1
2
3
一组A类焊点数量
2-9
10-19
>20
允许有缺陷焊点数
0(重新点焊或返修)
1
2
注意表中:一组焊点的首尾两个焊点不允许有缺陷!一组焊点中不允许有两个连续的缺陷点或只间隔一个合格点的两个点!
缺陷焊点处理
(1)重新点焊。
(2)不能进行点焊时进行返修,即用一个相当的焊点取代缺陷焊点。对一般焊点,如不能返修则办理偏差回用;如被拒绝,则报废。对特殊焊点,如安全、法规项,则必须强制性返修。
(2) 修理:拆下一个零件进行重新点焊或返修。
注:返修工艺由焊装试验室制定,产品工艺部门认可。
对于A类焊点,如焊点失效可能影响零件功能,则应按特殊规程(返修条件及程序)处理,应严格限制那些可能失效产生危险焊点中的A类焊点。
以下焊点不能有A类焊点:
——两层或三层厚板焊接;
——有焊点位置和最小间距要求时;
——外观焊点;
——搭接焊有强度要求时。
三、各种缺陷及原因分析
1、虚焊脱焊
虚焊脱焊直接影响焊点强度,主要表现在焊接区域内产生电阻热量不够,以致没有形成焊核。点焊主要热源方式为
Q=0.24I(2R件+R触+2R极)t
式中:Q—热量
I—电流
R—电阻
t—时间
2R极—电极与焊件接触电阻
R触—搭接焊间的电阻
由式中克践,影响发热量大小的主要因素是I、t及R。从有关资料图表中可看出,焊透率A与电极头直径d及I、t成正比关系,与压力成反比关系、随着I、t的增加,焊透率增大。但是,过大的I、t将会产生深坑、飞溅、烧穿等,将会使接头疲劳强度大为降低。压力过大,接触电阻减少,发热量不足,焊透率降低。
此外,影响因素还有:生产电压不稳定;电极头接触面积增大;零件表面存在油污和氧化膜铁锈,使零件之间及店即将的接触电阻显著增加,甚至出现局部不导电,影响点焊的热量析出,形不成核心;焊点分布过多过密集,是分流增加,导致焊点加热不足等。
因此焊前必须清除焊件表面的油污和铁锈,定期检查更换电极头,经常检查电流、电压变化情况。根据实际条件,综合考虑其他因素,适当的选取I、t、d及F和硬软规范,是刚好不出现飞溅为临界值获得良好的焊接质量。
2、过少与塌陷
通常电流过大,电焊时间过长,使核心直径扩大的速度有可能突破相对变薄的塑性环,焊接区温度剧增,发生局部熔化、飞溅,核心区发生变形,甚至过烧。因此,当采用大电流焊接工艺时,对通电时间必须严格控制,对焊件的油污及锈蚀必须清除。
3、裂缝
在焊核结晶过程的高温中,金属强度很低,或存在脆性组织,不足与克服收缩所产生的拉力,易产生裂纹;焊件表面锈蚀等杂质进入焊核与某些合金元素形成低熔共晶也会引起内裂纹;电流过大,温度急剧变化,内外冷却不平衡,限制了焊核结晶时的收缩,也会在焊核中心形成缩孔。因此,要克服裂纹的缺陷,除选择合适的电流电压之外,在焊件加热结束后,应使电极压力继续适当延长一段时间,迫使焊核结晶在压力作用下,产生一定的挤压变形,以弥补金属冷却时的收缩,有助于防止产生裂纹和锁孔。
缺陷
产生缺陷的原因
改进措施
压痕过深及表面过热
1.通电时间过长
2.电极压力过大
3.电流过大
4.电极端面尺寸过小
1.调整规范
2.改变电极端面角度,减小电极压力
3.改善冷却条件,减小电流
4.修磨电极头端面,使端面尺寸达到工艺要求
表面局部烧穿
1.电极端面形状过小
2.电流过大
3.焊接时间过长
1.修整电极,达到工艺要求
2.减小电流
3.缩短焊接时间
未焊透,核心小
1.电流小,电极压力大。
2.电极工作表面直径大
3.表面清理不良
4.焊接时间过短
1.增大电流,减小电极压力
2.修整电极,达到工艺要求
3.清理表面
4.加长焊接时间
喷溅
1.焊件或电极表面不干净
2.电极压力小加压时间短
1.清理焊件与电极表面
2.提高电极压力,增加加压时间
熔化不均,焊点不规则
电极端面不平整
修整电极端面
四、焊接参数初选表
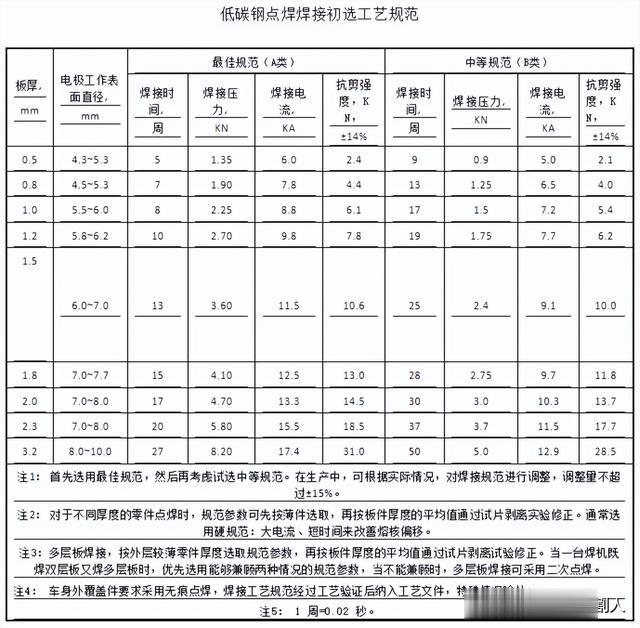
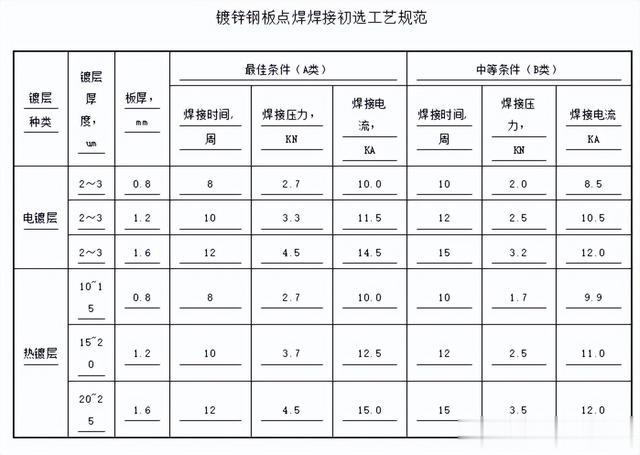