现在时代很多人说自动化的原因是人工成本太高,其实并不然,如今的国内依然出于人口红利的时代,更何况对如今的制造业来说,如果业务口打开,人工成本基本不会成为制造业的压力。
真正让这些制造业大佬们原因选择自动化的原因主要就是因为人工的误差太高,远远无法产线对品质的要求,比如我们时下比较火热的芯片半导体企业,检测缺陷等方面就不得不采用视觉检测技术了,但是很多企业引进了机器视觉系统,却并没有很理想是什么原因呢?其实你做不好视觉检测的难点主要有这几点!
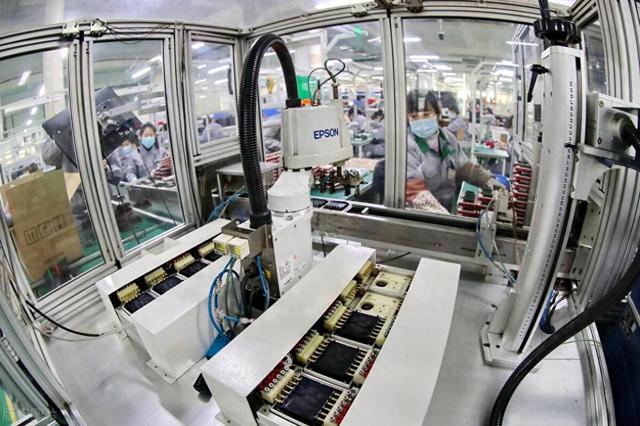
在我们实施视觉检测产线的时候会发现,实验室比较稳定的结果,实际落地却会出现这样那样的问题,其主要原因就是因为车间生产线带来的直接影响,我们可以在实验室模拟产线情况,但是却模拟不出各种突发的问题,比如环境的温度、湿度等等领域的变化,是直接影响传感器性能的!
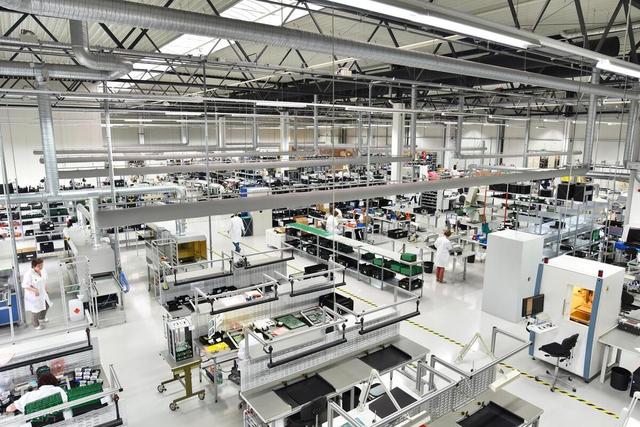
除此之外我们要知道视觉检测系统从来不是一个单独出现的存在,他和其他机械体统共存的时候,就会受到误差和震动的影响,这个情况的出现极有可能导致采集的图像数据发生偏移变形!
节拍速度对于制造业来说,引进视觉系统还要考虑一个问题,那就是预算,如果预算达不到,那么供应商采取次一级的视觉检测设备,很有可能导致检测速度无法赶上生产节拍,导致产线产品大量积压。
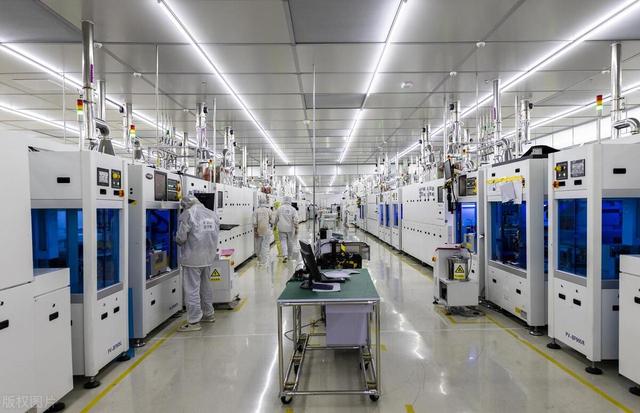
当然了即使是相匹配的视觉检测产品,也面临一些考验,比如高速运作的产线需要视觉检测系统长时间的稳定工作,这种时候就要考验设备的稳定性和可靠性,否则出现故障整条产线都有可能因此而停滞下来!
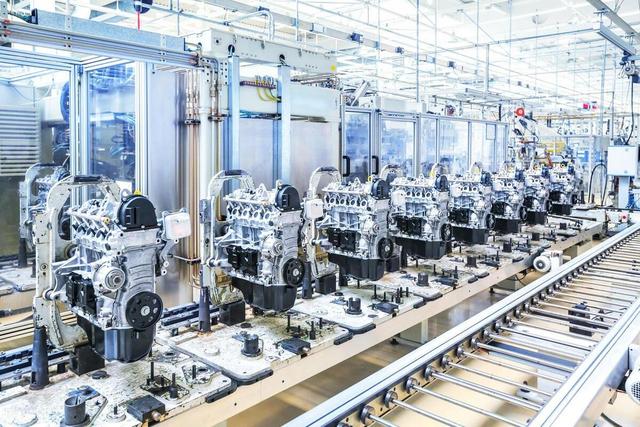
当产线的工件大小不一致的时候,如果差距不大,那么也看不出来什么具体差异,如果差距比较大,那么普通镜头可能无法对太大的工件采集完整的图像,直接导致尺寸测量的精准性,甚至可能影响采集图像的细节问题,因此对于这样的产线我们在设计之初就要对光源镜头等设备进行充分的考量,留出预留值来解决问题。
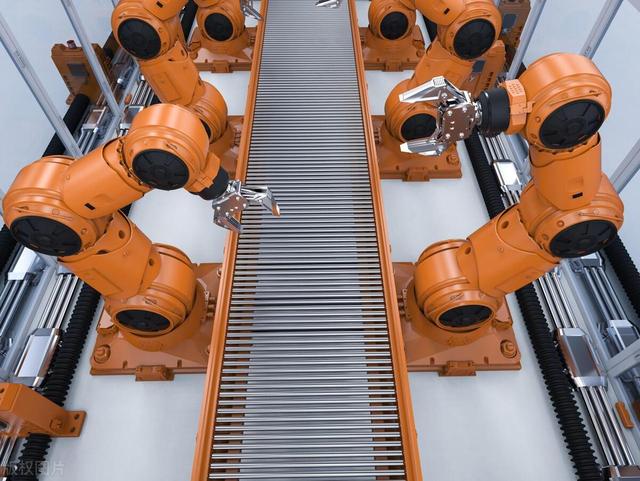
其次尺寸不同,软件算法可能就要随时调整,这样也会影响检测的精度和效率,对于极端大小的工件,甚至有可能无法提供准确的检测,此时我们如果遇到这些问题就需要提早准备自适应算法哦!
当然产线上遇到的检测问题绝不会只有这些,如果你们有相关问题,可以在评论区留言哦!