2月25日,日本化工龙头企业东丽集团宣布:2026年,日本东丽集团本土PTA(精对苯二甲酸)生产线将永久停产。与此同时,PTA全球停产停转消息频传:韩国乐天化学清仓巴基斯坦工厂;欧洲英力士淘汰比利时老旧装置……一场席卷全球的PTA产业撤退潮,正将中国推至聚光灯下。这个占据全球63%产能的化工大国,如何接住国际巨头抛出的“烫手山芋”?

国际化工巨头的集体退场,本质上是全球PTA产业成本重构的必然结果。以欧洲某70年代投产的老装置为例,其单位加工成本高达550元/吨,比采用英威达P8++技术的中国装置高出38%。更致命的是,中国头部企业已通过余热发电、醋酸循环等技术,将单吨PTA能耗降至358元,较行业均值低30%以上。在这场成本竞赛的背后,是技术代际的残酷碾压。日韩企业多沿用上世纪90年代的低温氧化工艺,PX单耗比中国主流工艺高0.8%,在原油价格高位震荡的2024年,仅此一项就让每吨成本增加200元。当中国PTA产能以每年860万吨速度扩张时,海外老装置如同“背着沙袋赛跑”,最终选择止损离场。
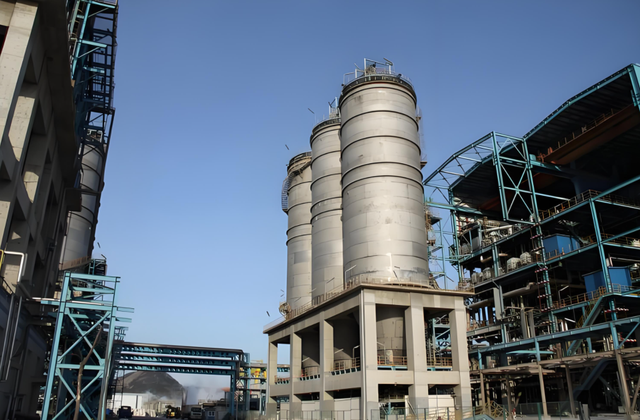
国际产能出清给中国带来的是“带刺的玫瑰”。2024年中国PTA出口量同比增长62%,首次突破600万吨,抢占日韩退出的东南亚市场。但狂欢之下暗藏隐忧:国内产能将在2025年突破9000万吨,而全球总需求仅1.2亿吨,供应过剩率将达25%。更严峻的是,行业利润率已从4000元/吨暴跌至亏损边缘,逸盛、恒力等头部企业正用规模效应苦苦支撑。
这种矛盾在产业链上尤为凸显。中国PX对外依存度仍超40%,当国际原油价格传导至PTA成本端时,国内企业既要承受原料涨价压力,又要应对下游聚酯行业压价,陷入“两头挤压”的困局。浙江某PTA生产商坦言:“现在每吨利润还不够覆盖财务成本,全靠期货套保维持现金流。”
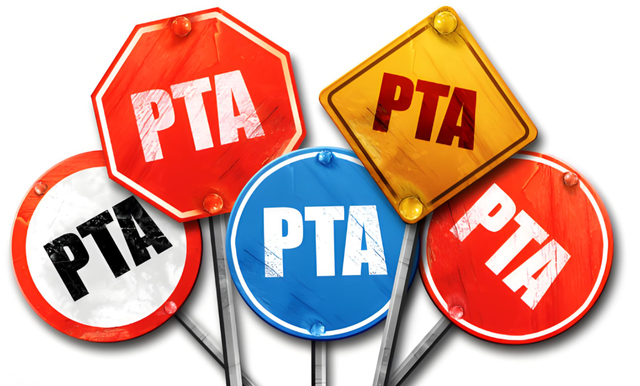
面对这场全球产业变局,中国企业正在开辟三条突围路径:
技术卡位战:恒力石化投入23亿元改造的第四代PTA装置,通过催化氧化技术将醋酸单耗降低15%,副产蒸汽发电可满足40%厂区用电。这种技术迭代正在改写竞争规则——当加工成本差距拉大到150元/吨时,老旧产能将失去生存空间。
价值链攀升战:荣盛石化联合中科院开发的医用级PTA,纯度达到99.99%,每吨售价较工业级产品高出1200元。这种转型正在打开高端工程塑料、液晶薄膜等新市场,目前国内特种PTA产能占比已从5%提升至12%。
全球资源整合战:在印尼三菱化学PTA工厂挂牌出售时,桐昆股份迅速启动尽调,计划通过并购获取东南亚港口资源。这种“产能出海+资源回补”的模式,既能规避反倾销风险,又能构建PX-PTA-聚酯全产业链壁垒。
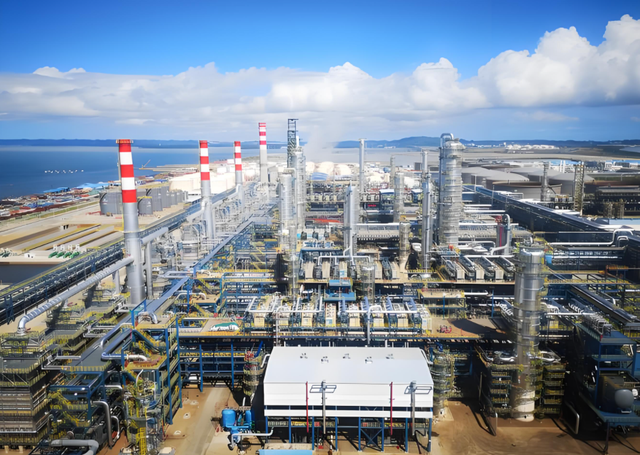
当全球PTA产业版图加速重构,中国既不能沉醉于产能扩张的虚假繁荣,也无需畏惧国际巨头的战略撤退。真正的胜负手,在于能否将规模优势转化为技术统治力——这需要头部企业把每吨50元的成本优势,转化为100元的研发投入;把产能过剩的危机,转化为淘汰落后的契机。在这场没有终局的产业马拉松中,唯有持续进化的企业,才能穿越周期迷雾。