优化关键工艺参数提升功率器件引线键合的可靠性
聂洪林 陈佳荣 任万春 郭林 蔡少峰 李科 陈凤甫 蒲俊德
(西南科技大学 信息工程学院 四川立泰电子有限公司)
摘要:
探究了引线键合工艺的重要参数对功率器件键合可靠性的影响机制,进而优化超声引线键合工艺参数。采用单参数变化实验设计方法,改变超声功率、键合压力、键合时间等关键参数制备芯片,利用拉断力测试方法表征引线键合的质量,研究工艺参数与键合质量的映射关系,分析其影响机理;进一步利用正交实验得到引线键合关键工艺参数的优化配方。实验结果表明,当超声功率210 mW、键合时间80 ms 和键合压力3.4 N 时,可得到较好的键合可靠性和数据收敛性。而且,参数中超声功率对键合可靠性的影响最大,键合压力次之,而键合时间的影响不显著。
0 引言
集成电路技术的高速发展对封装工艺的可靠性提出了更高要求[1],引线键合工艺是实现芯片内部器件与外部管脚之间可靠电气连接的至关重要环节[2]。超声引线键合是目前的主流键合技术,具备低热预算、高经济性、强适配性等优点[3],占据了90% 以上的应用市场。然而有统计表明,超过25% 的半导体器件的可靠性问题是由引线键合失效导致[4]。由于功率器件的工作电压/ 电流较高,对工艺参数的优化和可靠性提升提出了更高要求[5]。在超声引线键合工艺中,对引线键合可靠性影响最大的关键工艺参数有超声功率、键合压力、键合时间等[6-8]。键合参数设置不合理可能导致键合强度降低、变脆以及接触电阻变大等问题,甚至出现器件开路或电性能退化等严重失效[9-10]。因此,研究人员针对超声引线键合的失效原因和参数优化展开了相关研究,罗珏等[11] 研究了第二点键合金丝的短尾失效问题,并讨论其主要影响因素和形成机理。范俊玲等[12] 通过调整键合压力与超声功率参数,讨论了银基键合线楔焊点形貌的影响因素。曹军等[13] 深入研究了热超声键合工艺的烧球时间、超声功率和键合压力等参数对金丝键合质量的影响。然而,目前研究主要针对金丝或超细引线的键合失效,而较少关注功率器件的粗铝线键合失效与参数优化问题,制约了大电流/ 电压条件下的功率器件引线键合可靠性提高。
本文拟采用单一变量试验法,设计功率器件的超声引线键合工艺参数实验,利用拉断力测试设备表征引线键合的可靠性,讨论键合可靠性背后的物理机制。进一步利用正交实验给出超声引线键合的工艺参数的最优配置,为功率器件的超声引线键合工艺可靠性提高提供技术支撑。
1 超声键合系统及其原理
功率器件一般采用超声引线键合法[14]。如图1 所示,超声引线键合系统主要由超声发生器、安装环、变幅杆及键合工具等组成。超声发生器将工频信号转变为主频约60 KHz 的高频正弦信号。再利用压电陶瓷的逆压电效应,将超声发生器产生的高频信号转变成机械振动,经变幅杆调整使劈刀产生振幅为4~5 μm 的前后振动[15]。
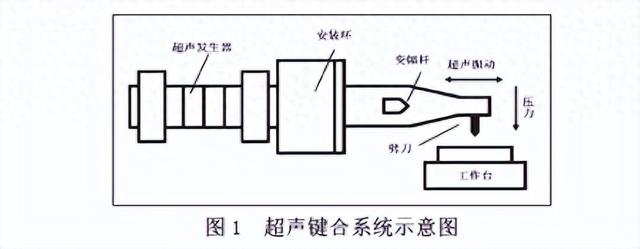
引线键合过程中,劈刀在键合线与界面之间施加一定的键合压力。在超声能量和压力的共同作用下,一方面键合界面处的氧化膜破碎并露出洁净界面,另一方面促使铝线发生塑性形变使键合线与金属面之间的原子层形成共价键结合,从而实现了芯片内部器件与外部管脚之间的紧密可靠电气连接。
2 实验设计
2.1 材料选用
材料选择。功率器件选择沟槽型肖特基功率二极管( 型号:M30T100CT,四川立泰电子有限公司)。芯片表面材质为CuAl 合金,硅基与芯片之间粘合铝层厚度约为4~5μm。为满足功率器件大电流工作要求,键合线选择直径380μm 的粗铝丝( 纯度99.99%),并采用TO-200 的封装形式。键合设备采用全自动超声键合机( 型号:W60,创唯新)。
2.2 实验设计
2.2.1 单参数变化实验设计
在基准工艺参数条件基础上,分别调整引线键合关键工艺参数,包括超声功率、超声时间以及键合压力。每个关键工艺参数在基准上下分别取2 个点,每个参数点键合150 根铝线,进行可靠性实验( 如表1)。由于第二键合点的可靠性远优于第一键合点,因此本研究主要针对第一键合点的键合工艺参数进行优化实验设计。
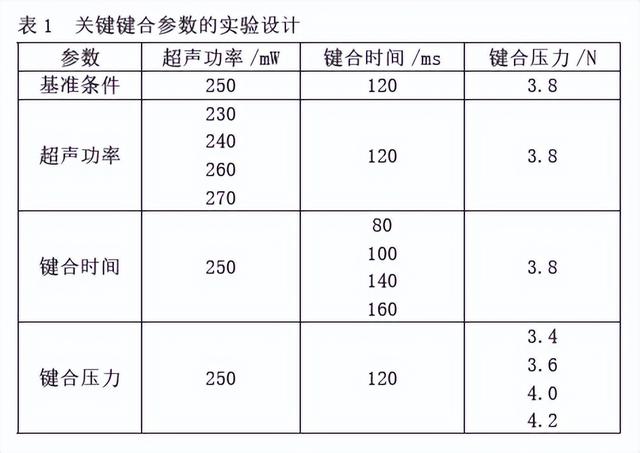
2.2.2 正交实验设计
如表2 所示,采用3 因素4 水平的正交实验设计方案。3 因素包括影响键合强度的三个核心工艺参数:超声功率、键合时间、键合压力;4 水平是在单参数实验结果基础上,综合高功率二极管的应用特征和工程经验,设定工艺参数范围和四个实验点。每组设置40 个样本进行实验以消除随机误差的影响,采用最大拉断力(FMBF,Maximum Breaking Force) 的平均值表征正交实验结果。进一步探究不同参数对键合质量的影响机制及最优参数配方。
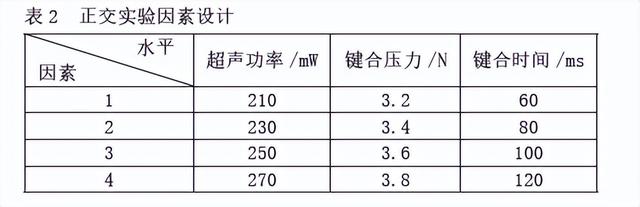
2.3 键合质量评估方法
最大拉断力测试。键合强度是评估键合质量好坏的重要技术指标[16], 其检测方法可分为键合拉力测试(BPT) 与剪切力测试(BST) 两种。本实验采用拉断力测试仪( 型号:XL30) 测试最大拉断力,以表征引线键合强度。所采用仪器和方法符合中国国家标准《微电子器件实验方法和程序(GJB-548B-2005)》和美国国家标准(MIL-STD-883)。拉断力测试过程如图2 所示,包括拉钩与键合线对准、施力后键合线的弹/塑性变形、拉断三个主要阶段。
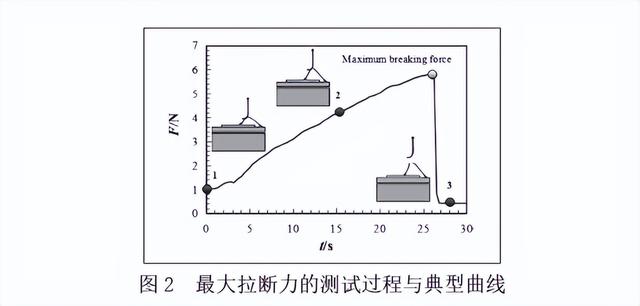
物理失效的显微观察。测试后对产生的物理失效进行分析,采用光学显微镜( 型号:AD409) 观察具体失效部位及其形貌。引线键合可靠性与拉断位置有关,如果出现在拉钩施力处,则为正常拉断;若在键合点处,则可靠性不合格;而位于颈缩点断裂,则需要再次测量确认其可靠性。
3 结果与讨论
3.1 基于单参数实验的影响机制分析
3.1.1 超声功率
利用单参数变化实验法,改变超声引线键合工艺的超声功率(230,240,250,260,270mW),制备好引线键合芯片后,分别测试其最大拉断力。如图3(a) 所示,随着超声功率增加,最大拉断力在给定功率范围内呈波动式变化。其中在240mW和270mW 处,拉断力分别比基准条件250mW 处大10.58% 和11.71%. 同时,240mW 与260mW 处的标准差分别比基准条件小10.28% 和12.70%. 如图3(b) 所示,超声功率为240mW 时,不仅拉断力较大、键合强度高,而且测试数据收敛、可重复性好。
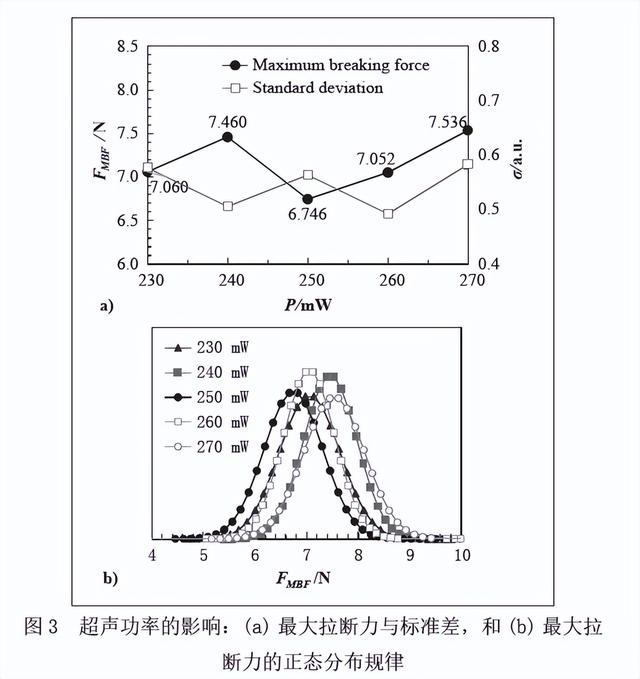
因此,在功率器件的粗铝线键合工艺中,超声功率将影响键合强度和工艺一致性。在基准条件基础上,建议将粗铝丝第一键合点的超声功率控制在240±5mW。
3.1.2 键合时间
如图4(a) 所示,改变超声键合时间(80,100,120,140,160ms) 后,最大拉断力先减小后增大。其中在80 和100ms 处,拉断力分别比基准条件120ms 处大13.39% 和10.27%,同时标准差分别比基准条件小16.13% 和16.49%。图4(b) 中,尽管在140ms 处的数据收敛性最好,但其可靠性仅比基准条件高4.39%。因此当键合时间为80~100ms 时,键合强度高,而且测试数据收敛较好。

因此,在功率器件的粗铝线键合工艺中,键合时间控制对键合可靠性的影响较大。在基准条件下,将超声键合时间选取在80~100ms 之间较合适。
3.1.3 键合压力
如图5(a) 所示,改变键合压力(3.4,3.6,3.8,4.0,4.2N),拉断力在3.6N 处达到最大值7.764N,比基准条件大15.33%,而且此时的标准差最小,仅为0.412。从图5(b) 中可以看出,键合压力3.6N 时,可靠性最好、数据最收敛。
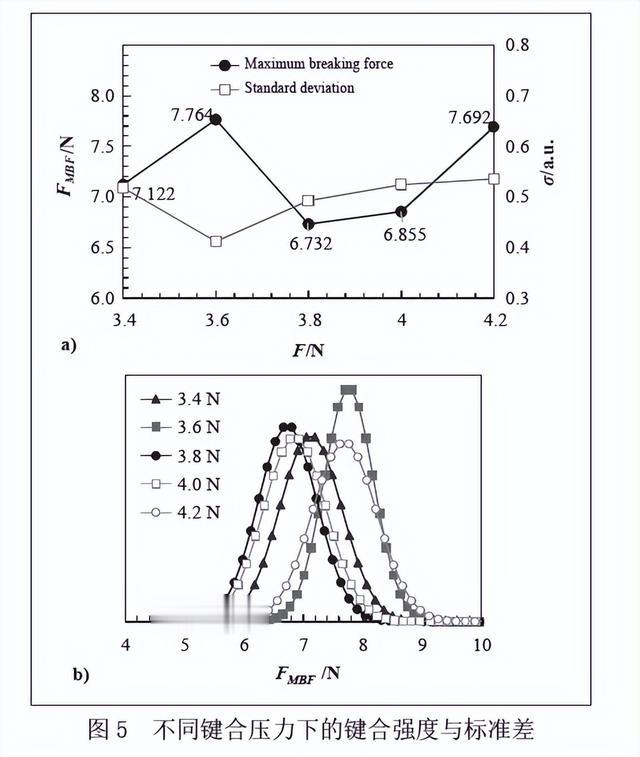
因此,在功率器件的粗铝线键合工艺中,合理选择键合压力对保证键合可靠性与工艺一致性至关重要。在基准条件下,将超声键合压力选取在3.6±0.2N 较合适。
3.2 基于正交实验的参数优化
单参数实验有利于分析引线键合工艺的单一参数对可靠性的影响机制,然而该方法仅关注工艺参数的局部改变,引线键合参数的整体优化需要采用正交实验方法。正交实验广泛应用于多因变量与结果中耦合关系的研究,可通过选取完全实验中的代表点,既大大减少了繁复的实验次数,又可分析各因变量的相互关系,最终得到全局优化后的工艺参数配方。
如图6 所示,引线键合可靠性随着超声功率的增大呈明显下降趋势,而键合压力和时间的影响趋势并不显著。其中超声功率的极差为0.73,分别比键合压力和时间的极差大1.61 和9.43 倍。因此,在功率器件的粗铝丝引线键合工艺中,超声功率对键合可靠性影响最大,键合压力次之,而键合时间的影响并不显著。

正交实验的键合可靠性测试数据如图7 所示。尽管在条件3 处(210mW,360N,100ms)的键合强度7.575N 最大,但其标准差0.510 也为最大,说明该条件下的数据收敛性最差。条件16(270mW,3.8N,60ms)的键合强度和标准差分别比条件3 小3.84% 和50.39%,可见其数据收敛性大大提高,强度则有一定程度降低。而在条件2(210mW,3.4N,80ms)的键合强度仅比条件3 低1.48%,但其标准差却改善了32.31%。综上所述,对于高功率器件的粗铝丝键合工艺,当超声功率为210mW、键合压力为3.4N 和键合时间为80ms 时,为引线键合的最优工艺参数,其第一键合点的键合强度与数据收敛性的综合可靠性较好。
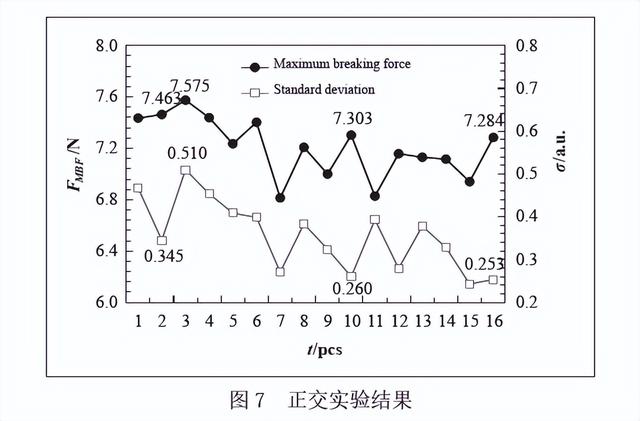
3.3 失效机理分析
引线键合过程主要依靠超声功率和劈刀压力,将能量用于去除表面氧化层,同时通过超声产生材料间摩擦而形成可靠的共价键连接。根据不同材质、表面状态和引线尺寸优选合适的工艺参数,可保证引线键合的可靠性。如图8(a) 所示,当引线键合工艺可靠性较好时,拉断力测试后键合线从拉钩施力处断裂,而键合点保持可靠的连接状态;当键合施加的能量过大时,如超声功率、时间和压力过大,会引起键合线颈缩点部的过度塑性变形,键合线受损而导致强度和牢固性降低,拉断力测试时键合线便从颈缩点处断裂( 如图8(b) 所示),而且,施加在芯片上压力过大还可能引起芯片内部器件的损伤;相反地,引线键合时施加的能量过小( 功率小、时间短、压力小),可能导致如图8(c) 所示的失效形貌,键合线从键合点处整体脱离。这是由于键合线的塑性变形不足而导致共价键合不强与键合面积太小,而且同时可能存在芯片表面的氧化层未完全去除的问题,从而降低了引线键合工艺的可靠性。

4 结束语
本文针对功率器件的大电流/ 电压应用需求,对其超声引线键合的工艺可靠性展开研究。采用单一变量实验设计方法,变化超声引线键合的关键工艺参数包括超声功率、键合时间和键合压力,探究引线键合工艺参数与可靠性之间的相互影响机制和优化方向。进一步采用正交实验设计方法,探究最佳键合参数。研究表明,在基准工艺条件基础上,分别单独对关键工艺参数进行了优化调整:超声功率210mW、键合时间80ms 和键合压力3.4N 时,可得到较高的键合可靠性和较好的数据收敛性。进一步地,通过对键合失效形貌的显微图像观察,研究了键合失效的内部机制,发现键合能量过大时,会出现键合线颈缩点断裂失效;能量太小会造成表面氧化层去除不足和有效键合的强度面积太小等问题,导致键合点整体脱落。该研究为功率器件的引线键合工艺可靠性优化指明了方向。