在现代工业的众多领域,复合材料已成为不可或缺的关键材料。从翱翔天际的飞机,到乘风破浪的船舶,从风驰电掣的汽车,再到各类高端运动器材,复合材料凭借其独特的轻量化与高强度特性,为产品性能的提升带来了革命性的变化。然而,如同世间万物都难以逃脱岁月与外力的侵蚀,复合材料在使用过程中也极易遭受损伤,这就使得复合材料修复技术成为了保障相关产品安全、延长使用寿命的核心环节。
本文将深入探讨复合材料修复的各个方面,从基础的材料结构与损伤原因,到详细的修复流程、方法、设备及耗材,再到未来的发展趋势,为读者呈现一幅全面且深入的复合材料修复画卷。

01
复合材料的结构与损伤诱因
(一)复合材料的结构奥秘
复合材料的结构设计犹如一场精妙绝伦的材料交响乐,将不同特性的材料巧妙组合,创造出超越单一材料性能极限的全新材料体系。
夹层结构(Sandwich Structures),从外观上看,恰似一个精心制作的三明治。其两侧是薄而高强度的蒙皮,如同三明治的两片面包,承担着主要的承载任务,为结构提供了出色的强度与刚度。而中间夹着的轻质蜂窝芯材,则像是三明治中美味的馅料,不仅极大地减轻了整体结构的重量,还在增强结构稳定性方面发挥着关键作用。以飞机机翼为例,采用这种夹层结构,机翼能够在承受巨大空气动力载荷的同时,保持较轻的自身重量,从而显著提高飞机的燃油效率和飞行性能。在制造过程中,先进的胶粘剂被用于将蒙皮与芯材紧密粘接,确保在复杂的飞行环境下,结构的整体性和可靠性得以维持。
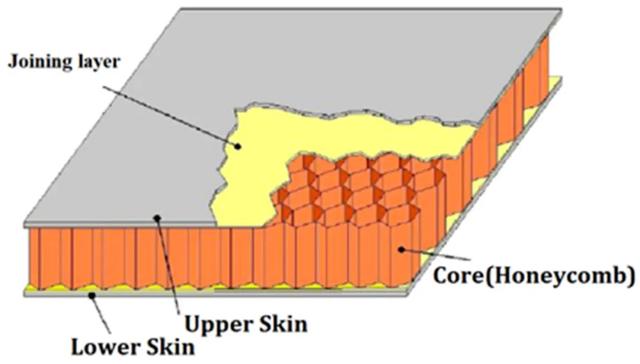
(夹层结构)
层压结构(Laminate Structures)则是另一种独具匠心的设计。它由多层纤维材料按照特定的方向和顺序精确叠加而成,如同精心编织的多层织物。每层纤维的方向都经过严格的设计与计算,如同在建筑中合理布置钢筋的走向,旨在使材料在不同方向上能够精准地展现出所需的机械性能。例如,在承受拉伸载荷的方向上,纤维会被优先排列以提供强大的抗拉强度;而在需要抵抗剪切力的部位,纤维则会以特定的角度交织。基体材料(如高性能树脂)如同纤维之间的“黏合剂”与“保护神”,紧密包裹着纤维,不仅增强了纤维之间的结合力,还为材料抵御外界的湿气、化学腐蚀等不良环境因素提供了坚实的屏障,确保材料在各种恶劣工况下仍能保持稳定的性能。
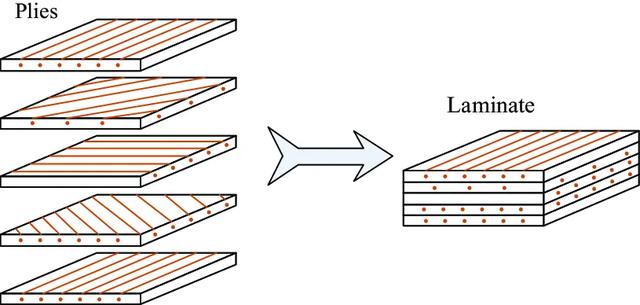
(层压结构)
(二)复合材料损伤的根源探寻
尽管复合材料拥有诸多优势,但在实际应用中,仍面临着多种损伤风险,这些损伤的成因复杂多样,涉及机械、物理和化学等多个领域。
机械冲击是复合材料常见的损伤源之一。在飞机的飞行过程中,跑道上的异物、飞行中的鸟类撞击,或者在汽车行驶时遭遇的石子飞溅等情况,都可能导致复合材料部件受到冲击。即使是看似轻微的低速撞击,也可能在材料表面留下不易察觉的凹痕,而内部却已遭受严重的损伤,如纤维断裂、分层等。这是因为复合材料的各层之间在冲击作用下可能会发生相对位移,破坏了原有的结构完整性,就如同积木塔在遭受轻微碰撞后,内部的积木块可能已经错位,尽管外表看起来可能并无大碍。
长期疲劳也是一个不容忽视的因素。许多复合材料部件在服役期间需要持续承受交变载荷,如飞机的机翼在每次起降和飞行过程中都会受到不同程度的应力作用,汽车发动机附近的部件在发动机的持续振动下也会承受循环应力。随着时间的推移,这些交变载荷会在材料内部引发微小裂纹,这些裂纹会逐渐扩展,就像墙壁上的细微裂缝在岁月的侵蚀下会慢慢变长变宽,最终可能导致材料的整体失效,严重威胁结构的安全性能。
高温环境对复合材料的影响同样显著。在航空航天领域,飞机发动机周围、火箭的热防护部件等区域,会面临极高的温度。在高温的作用下,复合材料的基体材料可能会发生降解,导致其力学性能大幅下降。例如,树脂基体可能会失去部分粘结强度,使得纤维与基体之间的结合变得松散,如同胶水在高温下失去粘性,导致原本紧密结合的物品分离,进而引发材料的分层、变形等严重问题,直接影响结构的承载能力和可靠性。
湿气侵入也是复合材料损伤的潜在威胁。当复合材料部件表面存在微小裂缝或损伤时,水分会趁机渗入材料内部。水分的侵入会改变材料的物理和化学性质,如导致纤维吸湿膨胀,使基体材料发生水解反应,从而降低材料的强度和刚度。在一些海洋环境或高湿度地区使用的复合材料设备,如船舶的外壳、海上风力发电机的叶片等,如果没有良好的防护措施,湿气侵入可能会加速材料的老化和损坏,大幅缩短其使用寿命。
02
复合材料修复的流程详解
(一)损伤评估:修复的关键前奏
损伤评估在复合材料修复过程中占据着举足轻重的地位,它如同医生在治疗前对患者进行的精准诊断,直接决定了后续修复方案的制定与实施。
目视检查是最基础且直观的方法,检验人员凭借丰富的经验和敏锐的观察力,仔细查看材料表面是否存在裂纹、凹痕、变色等异常迹象。然而,这种方法的局限性在于只能发现表面的明显损伤,对于材料内部深层次的问题往往无能为力,就像仅通过观察苹果的表皮,无法知晓其内部是否已经腐烂。
敲击检测则借助小型敲击工具轻击材料表面,凭借敲击时发出的声音特征来判断内部结构的完整性。当敲击到损伤区域时,声音通常会变得沉闷,这是因为内部结构的改变影响了声音的传播特性。但这种方法需要检验人员具备丰富的经验和敏锐的听觉,且对于一些微小或复杂的损伤,可能无法准确判断,类似于通过敲击西瓜来判断其成熟度,虽然有一定的经验规律,但并非绝对可靠。
无损检测(NDT)技术则是损伤评估的高科技手段,其中超声波检测利用超声波在材料中的传播特性来探测内部缺陷。超声波在遇到分层、裂纹等缺陷时会发生反射、折射和散射,通过分析反射波的信号特征,就能精确绘制出材料内部的损伤图谱,如同给材料做了一次高精度的“B 超”检查。而 X 光 扫描则能穿透材料,根据不同部位对 X 射线吸收程度的差异,生成清晰的内部结构图像,可清晰地显示出隐藏在材料内部的微小裂纹、孔洞等缺陷,为修复方案的制定提供了极为关键的详细信息。
(二)修复类型的精准抉择
根据损伤程度的差异,复合材料修复可分为简单修复、临时修复和永久修复三种类型,每种类型都有其特定的适用场景和技术要求。
简单修复适用于表面微小损伤且对结构整体性能无实质性影响的情况。例如,对于一些仅影响外观的轻微划痕或浅表擦伤,通常采用表面打磨、抛光等工艺进行处理,然后涂抹适当的保护涂层,就如同给家具表面的轻微划痕进行打蜡修复,旨在恢复材料的外观完整性,操作相对简便快捷,成本也较低。
临时修复则是在紧急情况下或设备无法立即进行全面修复时采取的权宜之计。比如在飞机飞行途中发现复合材料部件出现小面积损伤,为确保飞行安全,可采用临时补丁进行修复。临时补丁通常选用易于安装和拆卸的材料,如高强度胶带或简易的纤维布片,并使用临时胶粘剂进行固定。这种修复方式虽然不能完全恢复部件的原始性能,但能在短时间内起到一定的防护作用,防止损伤进一步恶化,就像给伤口贴上创可贴进行临时止血和保护,待设备返回基地或具备修复条件时,再进行彻底的修复。
永久修复是最为严格和复杂的修复方式,要求修复后的部件在性能上完全等同于原始部件,必须严格遵循设计规范和工艺标准。对于大面积的分层、纤维断裂等严重损伤,需要精心拆除受损部分,选用与原始材料相同或性能高度匹配的纤维、树脂等材料进行修复。修复过程中,要确保修复材料与原始材料之间的紧密结合和良好的力学性能传递,如同进行高精度的外科手术,对医生的技术水平和手术环境都有极高的要求,需要在专业的维修车间,由经验丰富的技术人员使用先进的设备和工艺完成。
(三)修复实施:重塑材料性能的关键步骤
修复实施阶段是将修复方案转化为实际行动的核心过程,涵盖了受损区域清理、修复材料填充与固化等多个关键环节,每个环节都紧密相连,共同决定着修复的最终质量。
受损区域清理是修复的首要任务,如同清理伤口的坏死组织,需要将破损、松散的材料彻底清除干净,确保修复区域表面平整、清洁,为后续修复材料的良好附着创造条件。在清理过程中,要严格控制清理范围和深度,避免对周围未受损材料造成二次损伤,同时要采用适当的工具和方法,如精细的打磨设备、专用的溶剂清洗等,确保清理效果达到最佳。
修复材料填充则需根据损伤类型和修复方案,精准选择合适的材料并进行填充操作。对于分层损伤,要将新的纤维材料按照正确的方向和顺序铺设在清理后的分层区域,并使用高性能的胶粘剂确保纤维与原始材料紧密结合;对于孔洞或缺失部分的修复,则需选用与原始材料相近的填充材料,如预浸料或特制的填充树脂,进行精确填充,使其与周围材料无缝衔接,恢复结构的完整性。在填充过程中,要严格控制材料的用量和填充密度,确保修复部位的力学性能能够满足要求。
固化过程是修复材料与原始材料实现一体化的关键环节,通过加热、加压或两者结合的方式,使修复材料中的树脂充分交联固化,形成稳定的化学键,从而获得所需的强度和刚度。在固化过程中,温度、压力和时间等参数的控制至关重要,如同烹饪美食时对火候和时间的精准把握。不同的修复材料和结构可能需要不同的固化工艺,例如,一些热固性树脂需要在特定的高温环境下保持一定时间才能完全固化,而在使用真空袋或热压罐进行固化时,要确保设备的密封性和温度均匀性,以保证修复区域的材料性能均匀一致,避免出现局部缺陷。
(四)质量检测:修复质量的严格把关
质量检测是复合材料修复的最后一道防线,其目的在于确保修复后的部件能够安全可靠地投入使用,如同产品出厂前的严格质检环节。
无损检测技术再次在这一阶段发挥关键作用。超声波检测不仅可以复查修复区域是否存在分层、气泡等缺陷,还能检测修复材料与原始材料之间的结合强度,通过分析超声波在界面处的反射和透射信号,判断结合界面的质量。红外热成像技术则利用材料在受热过程中的温度分布差异,检测修复区域是否存在内部缺陷或不均匀性。例如,当修复区域存在空洞或脱粘时,在加热过程中该部位的温度变化会与周围正常材料不同,通过红外热成像设备可以清晰地捕捉到这些异常温度区域,从而准确判断修复质量。
此外,还可以采用力学性能测试方法对修复后的部件进行抽样检测,如拉伸试验、剪切试验等,直接评估修复区域的力学性能是否达到设计要求。这些测试方法能够提供量化的数据,直观地反映修复效果,但需要注意的是,抽样测试应具有代表性,且测试过程要严格遵循相关标准和规范,确保测试结果的准确性和可靠性。只有通过了严格质量检测的修复部件,才能被允许重新投入使用,为设备的安全运行提供有力保障。
03
复合材料常见损伤类型与修复方法详解
(一)分层损伤修复:重建层间结合力
分层损伤是复合材料中较为常见且危害较大的一种损伤形式,通常由冲击或长期载荷作用引发,导致材料不同层之间的粘接失效,严重削弱结构的整体性能。
修复分层损伤时,首先要对受损区域进行细致的清理,使用专用工具小心地去除已分层的材料层,确保清理后的表面干净、平整,无残留的松散纤维或杂质。这一过程如同拆除旧建筑中松动的砖块,为后续的重建工作奠定基础。
接着,选用与原始材料性能相匹配的纤维材料和高性能胶粘剂进行填充和粘接。新纤维材料的铺设要严格按照原始材料的纤维方向和层叠顺序进行,确保修复后的结构在力学性能上与原始结构尽可能一致。在涂抹胶粘剂时,要确保胶粘剂均匀分布,充分浸润纤维,形成良好的粘接界面,就像在砌墙时使用均匀的水泥浆确保砖块之间紧密结合。
最后,采用加热设备或热压工艺对修复区域进行固化处理,使胶粘剂充分交联固化,增强纤维与纤维、纤维与基体之间的结合力。固化过程中的温度、压力和时间参数需根据修复材料的特性和部件的结构要求进行精确设定和严格控制,以保证修复效果的稳定性和可靠性,使修复后的分层区域能够重新承受载荷,恢复结构的完整性和强度。
(二)层压分裂修复:恢复内部结构完整性
层压分裂损伤多发生在材料内部高应力集中区域,如螺栓孔周围或部件边缘,表现为类似裂纹的损伤,但尚未穿透整个材料厚度。
修复时,首先要对分裂区域进行逐层打磨,打磨的深度和范围需根据损伤的具体情况精确确定,目的是去除受损的纤维层,同时形成一个有利于修复材料附着和融合的表面轮廓,类似于对木材表面进行精细打磨,使其能够更好地接受后续的处理。
然后,按照原材料的纤维方向和层压工艺,使用与原始材料相同或性能相近的纤维层和基体材料进行逐层填补修复。在填补过程中,要确保每层材料的铺设紧密、平整,层间结合良好,如同精心编织一件复杂的织物,每一层都要紧密相连,共同构成一个完整的结构。
最后,利用真空袋技术和加热设备进行固化处理。真空袋技术通过抽真空排除修复区域内的空气和挥发物,使修复材料在压力作用下紧密贴合在原始材料表面,避免出现气泡和分层现象;加热设备则为固化过程提供所需的温度条件,促进树脂的交联反应,确保修复区域的强度和刚度得以恢复,使修复后的材料能够重新承受正常的工作载荷,保证结构的安全性和可靠性。
(三)热损伤修复:应对高温引发的难题
热损伤主要是由于局部过热导致复合材料基体材料降解,进而引发层间剥离、裂纹等严重问题,常见于航空发动机附近、高温工业设备等环境中的复合材料部件。
修复热损伤时,首要任务是彻底清除所有受热降解的部分,这需要使用高温耐受性好的工具和溶剂,确保受损区域被完全清理干净,不留任何隐患,就像切除身体上的坏死组织,为新组织的生长创造良好的环境。
随后,选用耐高温的树脂或修复材料进行填充和修复。这些耐高温材料通常具有特殊的化学结构和性能,能够在高温环境下保持稳定的力学性能和化学稳定性。在填充过程中,要确保材料填充密实,与周围未受损材料形成良好的过渡,避免出现应力集中点。
完成修复后,必须进行严格的耐高温性能测试,模拟实际工作中的高温环境,对修复区域的力学性能、尺寸稳定性等进行全面检测。只有通过测试,证明修复后的部件能够满足高温工况下的使用要求,才能确保其安全可靠地投入运行,防止因热损伤修复不当而引发的二次故障。
(四)夹层板损伤修复:兼顾芯材与蒙皮修复
夹层板损伤通常由冲击或压力过大引起,导致芯材和表层同时受损,修复过程需要综合考虑芯材和蒙皮的修复方法,确保整个夹层结构的性能恢复。
首先,小心地移除受损的芯材部分,在移除过程中要避免对周围结构造成进一步破坏。然后,根据原始芯材的性能和结构特点,选用合适的新材料进行填充。填充时要确保芯材的密度、强度等性能与原始芯材相匹配,并且与上下蒙皮之间的粘接良好,能够有效地传递载荷,就像更换建筑物中的承重柱,新柱子要与周围结构紧密结合,共同承担载荷。
对于受损的蒙皮,根据损伤程度采用相应的修复方法,如对于表面划痕或小面积破损,可进行表面打磨、补漆或采用补丁修复;对于大面积损伤或贯穿性损伤,则需切除受损部分,使用与原始蒙皮相同的材料进行拼接修复。在修复蒙皮过程中,要注意保证蒙皮的平整度和与芯材的贴合度,确保整个夹层板的结构完整性和力学性能得以恢复,使修复后的夹层板能够继续正常工作,满足使用要求。
04
修复设备与耗材的技术深度解析
(一)真空袋装置:确保修复紧密贴合的关键工具
真空袋装置在复合材料修复中扮演着至关重要的角色,其工作原理基于真空技术,通过排除修复区域内的空气,实现修复材料与基体材料的紧密贴合,有效避免气泡和分层等缺陷的产生。
真空袋膜是真空袋装置的关键组成部分之一,它通常由高强度、耐温性好且具有一定柔韧性的材料制成,如聚酰胺或聚酯薄膜。其主要功能是在修复过程中形成一个密封的空间,将修复区域与外界环境隔离,防止空气进入。在使用时,真空袋膜要紧密覆盖在修复部件和修复材料上,并通过密封胶条确保其边缘密封良好,就像给伤口贴上一层密封的绷带,为修复创造一个稳定的环境。
导气布则负责在真空袋内构建空气通道,促进空气的顺畅排出。它一般具有良好的透气性和一定的强度,在铺设时要合理分布在修复区域周围,确保在抽真空过程中,空气能够迅速、均匀地从修复区域通过导气布流向真空泵,避免因空气滞留而产生气泡,如同在排水系统中设置合理的排水管道,保证水流顺畅。
胶粘剂是连接修复材料与基体材料的重要纽带,在真空袋装置中常用的胶粘剂如 Redux 胶膜,具有优异的粘结性能和耐温性能。在修复过程中,胶粘剂在真空压力和加热条件下,能够充分浸润修复材料和基体材料表面,形成牢固的化学键合,确保修复区域的整体性和强度,就像胶水将两块木板紧密粘在一起,使其成为一个整体。
(二)加热设备:固化修复材料的能量
加热设备在复合材料修复中是不可或缺的,其核心作用在于为修复材料的固化过程提供精准且稳定的热量,促使树脂或胶粘剂充分交联反应,从而确保修复区域达到预期的强度与性能标准,使其能够重新承担起结构载荷。
在热损伤修复场景中,加热设备的重要性尤为凸显。当复合材料因高温而遭受基体降解、层间剥离等损伤时,修复材料需要在特定的高温条件下进行固化,以恢复结构的完整性和耐高温性能。加热设备能够精确控制温度,模拟材料在实际工况下所需的固化环境,确保修复后的材料能够在高温环境中稳定工作,避免因修复不当而导致的二次失效。
在高强度、结构性修复方面,加热设备同样发挥着关键作用。对于承受较大载荷的复合材料部件,如飞机机翼大梁、汽车车架等部位的修复,修复材料的固化质量直接关系到部件的整体性能和安全可靠性。加热设备通过均匀加热,使修复材料在各个部位都能达到理想的固化状态,保证修复区域与原始材料之间形成良好的力学性能过渡,防止出现应力集中点,从而确保整个结构在修复后能够安全、稳定地运行。
(三)无损检测工具:修复质量的守护卫士
无损检测工具在复合材料修复过程中犹如一双双敏锐的眼睛,时刻监测着修复质量,确保修复工作的每一个环节都符合标准,为复合材料部件的安全使用提供有力保障。
超声波检测是一种广泛应用的无损检测技术,其原理是利用超声波在材料中的传播特性来检测内部缺陷。超声波由换能器产生,通过耦合剂传入复合材料内部。当遇到分层、空隙、裂纹等缺陷时,超声波会发生反射、折射和散射现象,反射波被换能器接收后,经过信号处理和分析,就能绘制出材料内部的缺陷图谱。在复合材料修复前后,超声波检测能够快速、准确地发现修复区域是否存在隐藏的缺陷,如修复材料与原始材料之间的粘接不良、内部气泡等问题,为修复质量的评估提供关键数据。
红外热成像技术则基于材料在受热或受冷过程中的热传导特性来检测缺陷。在检测过程中,通过对复合材料表面施加一定的热激励,正常区域和缺陷区域会因热传导差异而呈现出不同的温度分布。红外热成像仪能够捕捉到这些温度变化,并将其转化为可视化的图像,从而清晰地显示出热损伤区域、分层边界等缺陷。这种检测方法具有非接触、大面积快速检测的优势,在复合材料修复质量检测中能够有效地发现一些宏观缺陷和潜在的热相关问题,与超声波检测相互补充,共同确保修复后的复合材料部件质量可靠。
05
复合材料修复的未来发展趋势展望
(一)自动化修复:迈向精准高效的新时代
随着科技的不断进步,自动化修复技术正逐渐成为复合材料修复领域的重要发展方向。在未来,机器人将在修复过程中发挥核心作用,极大地提高修复的精准度和效率,减少人为因素带来的误差和不确定性。
机器人配备先进的激光扫描系统,能够对复合材料部件进行快速、高精度的三维扫描,精准识别损伤区域的位置、形状和大小等详细信息。通过智能算法对扫描数据进行分析处理后,机器人能够自动规划出最优的修复路径和材料铺设方案,如同经验丰富的工程师在脑海中迅速制定出修复策略。在材料铺设过程中,机器人能够精确控制修复材料的用量、铺设角度和厚度,确保每一层修复材料都能完美贴合在受损部位,实现与原始材料的无缝对接。例如,在飞机机翼复合材料蒙皮的修复中,机器人可以在狭小的空间内准确地进行修复操作,避免了人工操作可能带来的损伤扩大或修复质量不稳定等问题,大幅缩短修复时间,提高修复质量,为航空航天等领域的高效运维提供有力支持。
(二)智能材料的应用:赋予材料自我修复的神奇能力
智能材料的研发与应用将为复合材料修复带来革命性的变化。未来的复合材料有望具备“自愈”功能,如同拥有生命一般能够自动修复自身的损伤。
在一些新型复合材料的设计中,内部预先嵌入了特殊的修复剂微胶囊或纳米容器。当材料受到外力作用产生裂纹时,裂纹的扩展会破坏这些微胶囊或纳米容器,使其中的修复剂释放出来。修复剂在毛细管作用或其他物理化学机制的驱动下,迅速填充到裂纹缝隙中,并发生固化反应,实现对裂纹的自动修复。例如,在一些承受交变载荷的复合材料结构件中,如桥梁的拉索、风力发电机的叶片等,智能材料的应用能够实时监测和修复微小损伤,有效延长材料的使用寿命,降低维护成本,提高结构的安全性和可靠性,为基础设施和能源领域的可持续发展提供新的技术解决方案。
此外,形状记忆材料也将在复合材料修复中得到应用。这类材料在受到一定的温度、应力等外部刺激后,能够自动恢复到预先设定的形状。在复合材料修复中,当修复区域需要精确恢复到原始形状时,形状记忆材料可以发挥重要作用。例如,在一些复杂形状的复合材料部件修复后,通过对形状记忆材料进行适当的加热或施加应力,使其带动修复区域恢复到理想的形状,确保修复后的部件在外形和尺寸上与原始部件高度一致,提高修复的精度和质量。
(三)可持续修复技术:兼顾环境与资源的绿色发展
在全球环保意识日益增强的背景下,复合材料修复技术也在朝着可持续发展的方向迈进,致力于开发环保友好型的修复材料和工艺,减少对环境的影响和资源的消耗。
可回收利用修复材料的研发是可持续修复技术的关键领域之一。研究人员正在探索开发新型的复合材料修复材料,这些材料在完成修复使命后,能够通过特定的回收工艺进行回收再利用,实现资源的循环利用,减少废弃物的产生。例如,一些生物基复合材料或可降解聚合物材料被应用于复合材料的修复,这些材料在自然环境或特定的回收条件下能够逐渐分解或被重新加工成新的材料,降低了对传统不可再生资源的依赖,减少了对环境的污染。
绿色固化技术也是可持续修复技术的重要研究方向。传统的固化工艺可能需要消耗大量的能源,并在固化过程中产生一定的污染物。而绿色固化技术则致力于开发低能耗、无污染的固化方法,如利用太阳能、微波能等清洁能源进行固化,或者采用新型的无溶剂、低挥发性的固化剂和树脂体系。这些绿色固化技术不仅能够降低修复过程中的能源消耗和环境污染,还能提高修复效率和质量,为复合材料修复行业的可持续发展提供技术支撑,实现经济效益与环境效益的双赢。
06
总结
复合材料修复作为一门融合材料科学、工程力学、制造技术等多学科知识的复杂技术领域,在现代工业的发展中起着至关重要的作用。从损伤的精准评估、修复类型的合理选择,到修复过程的精细实施和质量的严格检测,每一个环节都需要高度的专业知识和精湛的技术工艺。随着自动化技术、智能材料和可持续发展理念的不断推进,复合材料修复技术正迎来前所未有的发展机遇,未来将朝着更加高效、智能、绿色的方向发展。这不仅将为航空航天、汽车、船舶等传统行业带来更高的安全性和可靠性保障,延长设备的使用寿命,降低运营成本,还将为新兴的高端制造业和绿色能源产业等提供强有力的技术支持,推动整个工业领域的创新与可持续发展,在全球经济和社会发展的进程中留下浓墨重彩的一笔。在未来的研究与实践中,持续关注和投入复合材料修复技术的发展,不断探索创新,对于提升我国在全球制造业中的竞争力,实现工业的高质量发展具有重要的战略意义。
文章来源:碳纤维研习社
注:本站转载的文章大部分收集于互联网,文章版权归原作者及原出处所有。文中观点仅供分享交流,如涉及版权等问题,请您告知,我将及时处理!