近日,工业和信息化部科技司公示“2024年钢铁行业重点场景数字化转型典型案例结果”名单,南钢“高炉水渣系统智能无人抓渣行车系统应用案例”“基于产供销一体化的智慧运营平台”“面向能源管理场景的智慧能源管控一体化平台应用案例”榜上有名。
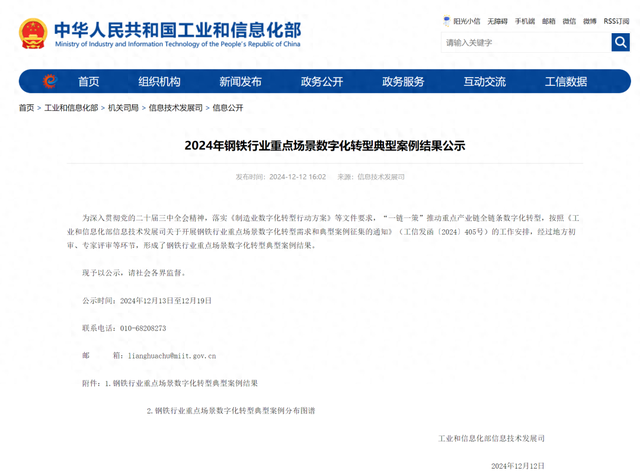
本次由工业和信息化部发起的典型应用案例征集活动,聚焦于钢铁行业及上下游关键场景,旨在解决数字化转型过程中遇到的核心难题。活动通过征集转型需求和典型案例,形成了钢铁行业数字化转型场景图谱,不仅梳理了行业转型需求,也筛选出一批可复制、有推广价值的数字化实践案例,并公示了优秀的数字化转型服务商,强化了供需双方的精准对接。
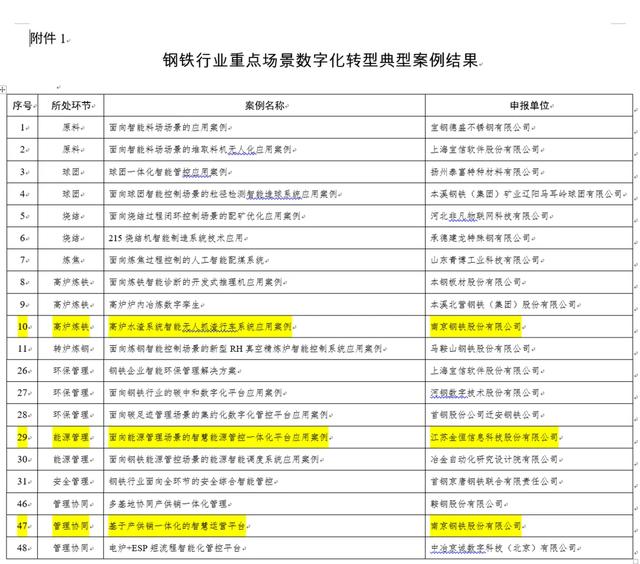
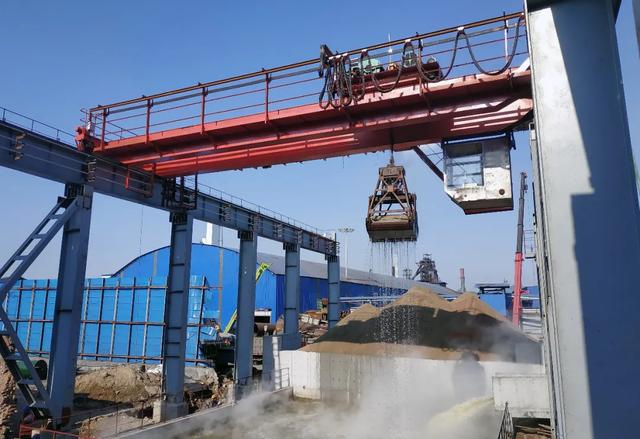
“高炉水渣系统智能无人抓渣行车系统应用案例”成功将智能无人抓渣系统应用于高炉炼铁的水渣处理工序,实现了行业技术创新的重大突破。针对高炉炼铁出铁口渣处理工序的恶劣环境,无人行车系统有效替代了人工操作,避免了工人长期在有害蒸汽和高温环境中作业,保障了职业健康,降低了安全事故风险。
项目基于PLC+变频控制技术,结合行车抓料作业模型算法,实现了行车的自主控制作业,定位精度高达毫米级,大幅提升了作业效率和精准度,满足了高炉炼铁生产线的快速、准确物料搬运需求。通过构建数字化平台,实现了对多台无人行车的集中监控和智能调度,优化了生产流程,减少了设备冲突和碰撞,提高了整体生产效率和设备利用率。利用实时监测和数据分析技术,系统能够提前发现设备潜在故障,实现预测性维护,降低了设备维护成本和停机时间,提高了设备的可靠性和稳定性。通过精准控制能源消耗,系统显著降低了无人行车的能耗,实现了节能减排,符合当前绿色制造的发展趋势。该解决方案已成功应用于钢铁、物流等多个行业,展现出强大的市场适应性和推广价值,为制造业和物流业的智能化发展提供了有力支撑。
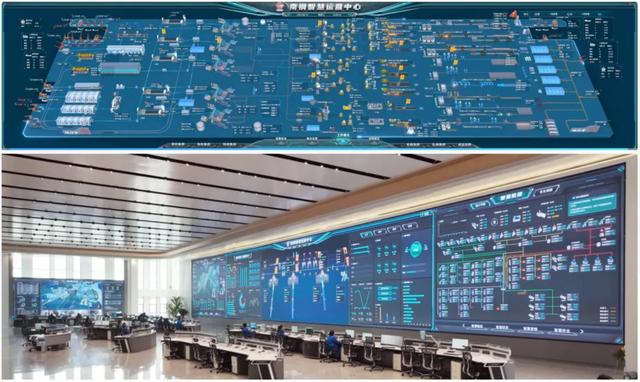
“基于产供销一体化的智慧运营平台”实现了钢铁行业智慧运营的重大突破。项目依托工业互联网平台,通过自研FSI2平台实现百万级工业数据的融合与毫秒级同步,构建了涵盖原料、炼铁、铁调、炼钢、轧钢、成品六大集群的一体化管控中心。
该平台集成了生产、采购、营销、物流、成本等多个业务模块,实现了全流程的数据共享与业务协同,显著提升了生产效率和运营管理能力。通过数据集成与共享,实现了从源头采购到产品交付的全链条智能化协同,显著缩短了生产周期和库存周转天数,提高了产业链整体运营效率。运用大数据分析技术,精准预测市场趋势,为生产计划提供科学依据,确保供需精准对接与平衡,提升了市场响应速度和客户满意度。
构建了产业互联模块,实现了供应链上下游企业的高效协同,解决了信息不对称问题,提高了供应链透明度和灵活性,降低了运营成本。引入数字孪生技术、智能排程系统、余材替代模型等先进技术,优化了生产流程,提高了产品成材率和交付能力,降低了无效库存占用。项目实施后,南钢吨钢质量成本大幅下降,采购年降本效果显著,高附加值产品产能和重点客户订单量显著提升。
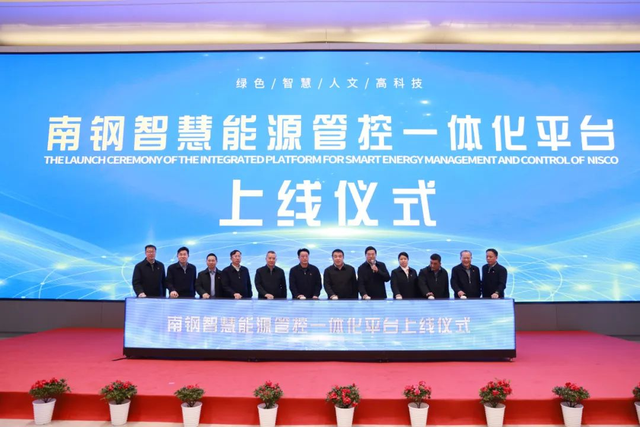
“南钢智慧能源管控一体化平台”依托自研工业互联网平台构建,以大数据为核心驱动,融合物联网、人工智能、大数据算法分析与工业智能建模等前沿技术。
平台涵盖能源监屏、运行管理、智能决策、能源分析、工序精管、碳排管理、节能技术、法规制度等8大模块,紧密围绕生产经营实时数据,强化能源调度系统中各介质的协同与优化效能,通过在线预测能源介质平衡提供精准指导,深度细化与拓展时间粒度、空间广度及分析深度等能源管理关键指标,全方位推动企业精益产能与精准用能。
该平台在南钢成功落地应用,有效实现原能源管理系统的深度融合与迭代升级,达成平台一体化、管理集约化、监控调度扁平化,大幅提升能源系统管理效率与管控水平。首创能源动力供应集群控制、智慧管理与智能决策一体化的数字能源管理模式。经数据统计,平台助力南钢优化人力配置,新水耗量、吨钢电耗双降,自发电比与节能效益齐升,在减碳降耗与降本增效方面成效卓越。
来源:南京钢铁