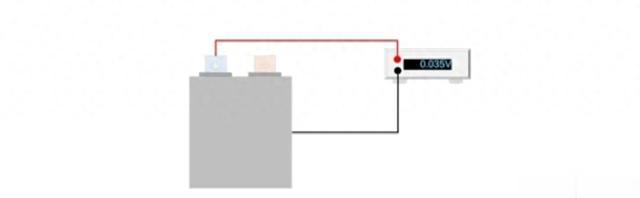
一、测试目的与重要性
安全性保障
检测电池绝缘材料(如隔膜、外壳)在高电压下的耐击穿能力,避免内部短路或漏电引发热失控,为电池安全使用筑牢防线。
质量控制
用于验证生产工艺的稳定性,排查隔膜是否存在微孔不均、杂质等缺陷,以及封装是否完整,是把控电池质量的重要环节。
二、基本原理
高压施加与漏电流监测
在电池两极或电极与外壳间施加高于工作电压的测试电压,通过精确测量漏电流来判断绝缘性能。
直流耐压测试:这是常用的测试方法,模拟电池实际工作状况,施加直流高压(一般为1.5 - 2倍额定电压 + 500V ),检测稳态漏电流情况。
交流耐压测试:使用频率相对较低,但可用于检测容性负载下的绝缘缺陷(如局部放电现象),较多应用于研究场景。
三、测试步骤与连接方式
典型配置
正极 - 外壳测试:将高压端连接电池正极,外壳接地,以此检测正极的绝缘性能。
负极 - 外壳测试:原理同正极 - 外壳测试,用于检测负极的绝缘情况。
极间测试:针对已装配完成的电池施加极间高压,评估隔膜的耐压性能(操作时需谨慎,防止损伤电池)。
流程
逐步升高电压至目标值,保持设定时间(如60秒 ),同时监测电流,要求电流不超过规定标准(通常要求 < 1mA ) 。
四、测试电压标准与规范
国际标准参考
IEC 62133:针对便携式电池,明确规定测试电压为最高工作电压的1.5倍 + 500V 。
UL 1642:要求施加直流电压(如500V或更高 ),并维持1分钟,期间电池无击穿现象。
行业实践
对于动力电池(如应用于电动汽车的电池 ),可能需要承受数千伏的测试电压,具体数值依据电池设计标准而定。
五、关键设备与技术参数
耐压测试仪
需具备高精度的高压输出能力(0 - 5kV或更高 ),以及微安级的电流检测精度。
安全防护
设备应具备过流保护、电弧检测、紧急断路等功能,防止在测试过程中电池损坏或对人员造成危险。
六、与绝缘电阻测试的对比
绝缘电阻测试
在低压(如500V DC )条件下测量电阻值(一般要求 > 100MΩ ),主要评估电池常态下的绝缘性能。
耐压测试
在高压环境下验证电池的极限绝缘强度,测试更为严格,能够发现如微小裂纹等潜在的绝缘缺陷。
七、影响因素与注意事项
材料特性
隔膜的介电强度(如PE/PP材质通常为300 - 500V/μm )、厚度及其均匀性对测试结果有重要影响。
环境条件
湿度、温度等环境因素可能会影响电池表面漏电情况,因此建议在干燥环境中进行测试。
极化效应
长时间施加电压可能导致电解液极化,可考虑采用短时升压或阶梯式测试方法来避免该问题。
误判规避
确保测试夹具接触良好,同时排除外部干扰(如环境电磁噪声 ),防止出现测试结果误判。
八、实际挑战与解决方案
测试后电池状态
若测试过程中电池未发生击穿且漏电流符合标准,电池可继续安全使用;若发生击穿,则需对电池进行报废处理。
复合材料测试
对于多层隔膜或固态电解质等复合材料,需进行分层测试,分析各层对耐压性能的贡献。
动态老化评估
在电池进行循环充放电后再次进行耐压测试,监控绝缘性能的衰减情况(如枝晶生长导致隔膜弱化 )。
九、前沿技术与发展
在线监测系统
将耐压测试集成到生产线中,通过局部放电检测等技术实时反馈电池绝缘缺陷位置。
材料研究
致力于开发高介电强度的隔膜(如陶瓷涂层隔膜 ),以提升电池的耐压极限。
总结
锂电绝缘耐压测试通过施加高压并分析漏电流情况,保障电池在高风险工况下的绝缘可靠性。测试过程需严格遵循相关标准,综合考虑材料特性与环境因素并加以控制,全面评估电池安全性。未来,智能化测试手段与高耐压材料的研发将成为重点发展方向,以满足更高能量密度电池的安全需求。