2024年3月6日上海汽轮机厂成功召开《超超临界汽轮机用ZG13Cr9Mo₂Co₁NiVNbNB耐热钢铸件 技术条件(JB/T 14047-2021)》的科技成果鉴定会,该标准是国内外首个含Co和B的先进9~10%Cr铁素体耐热钢行业标准。这标志着由上海汽轮机厂研制的620℃~630℃汽轮机铸件用钢ZG13Cr9Mo₂Co₁NiVNbNB从研发到落地,从试制品到批量产品,从依赖进口到实现全面国产化,从企业标准到行业标准的技术路线取得了巨大成功,成果达到了国际领先水平。
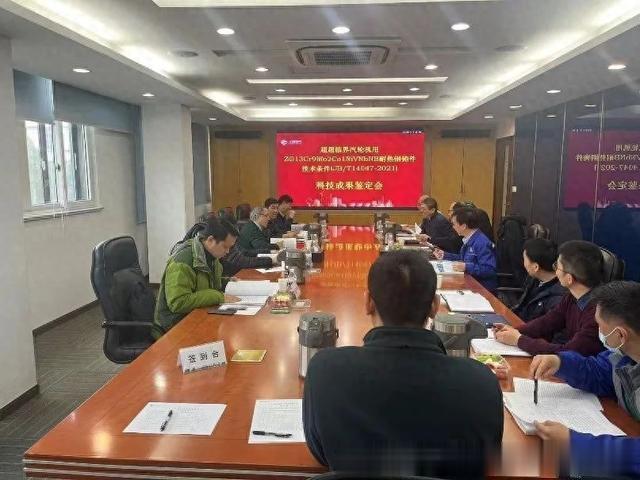
一、研发背景
相对于常规超超临界机组,新型高参数超超临界机组的再热蒸汽温度将提高到620℃~630℃。因此,传统的9~10%Cr钢已经不能满足新机组的设计需求。新型铁素体耐热钢的研发被提上日程。
二、研制历程
上海汽轮机厂自2009年开展ZG13Cr9Mo₂Co₁NiVNbNB的科研开发工作。在化学成分设计、热处理工艺及材料应用性能方面取得技术创新和突破,并获得相应的关键技术。
上海汽轮机厂通过在传统的9~10% Cr钢基础上进行调整和改进,添加Co和B元素,开发了含Co和B的新型铁素体耐热钢ZG13Cr9Mo₂Co₁NiVNbNB。通过开展热处理工艺试验研究,掌握该材料的最优热处理工艺,测试并掌握了全面应用性能数据,为设计计算提供依据。根据科研成果,上海汽轮机厂制定了ZG13Cr9Mo₂Co₁NiVNbNB耐热钢铸件的企业标准,并开展铸件的首件试制以及制造工艺研究。
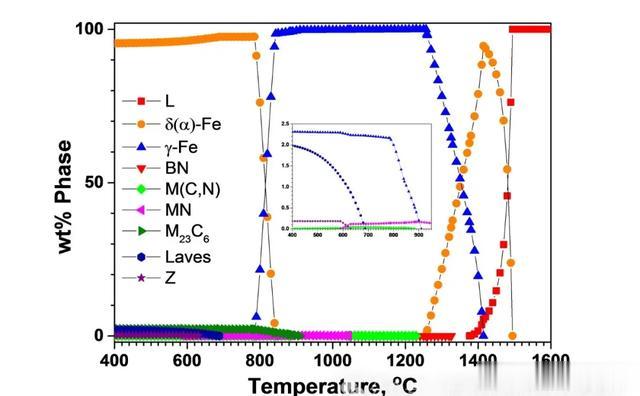
图1 ZG13Cr9Mo₂Co₁NiVNbNB准平衡态计算相图
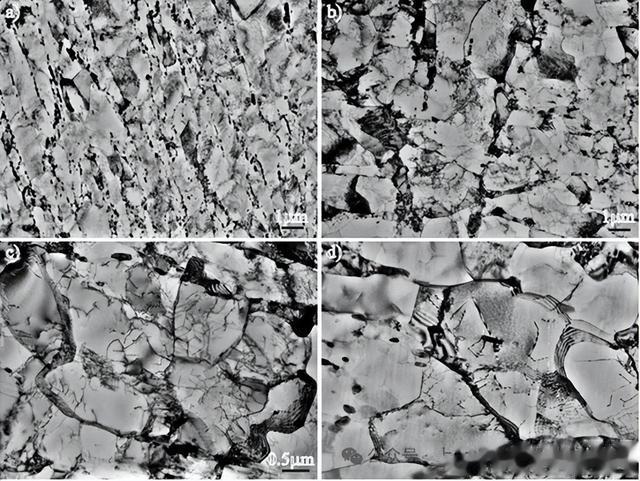
图2 ZG13Cr9Mo₂Co1NiVNbNB持久样品的显微组织TEM图像
最初在奥钢联和JSW等国外供应商进行中压内缸铸件的试制,在上海汽轮机厂进行再热阀壳铸件的试制,均试制出合格的铸件,并于2013年成功应用于国际首台再热温度为620℃的超超临界机组。
早期机组的ZG13Cr9Mo₂Co₁NiVNbNB钢汽缸铸件均依赖进口,上海汽轮机厂联合国内铸件供应商二重重型装备有限公司积极推进该材料汽缸铸件的国产化制造工作,并于2014年试制成功合格铸件。随后,国内哈尔滨汽轮机厂、东方汽轮机厂等也逐步实现了超超临界汽轮机汽缸、阀壳等关键零部件的国产化工作。
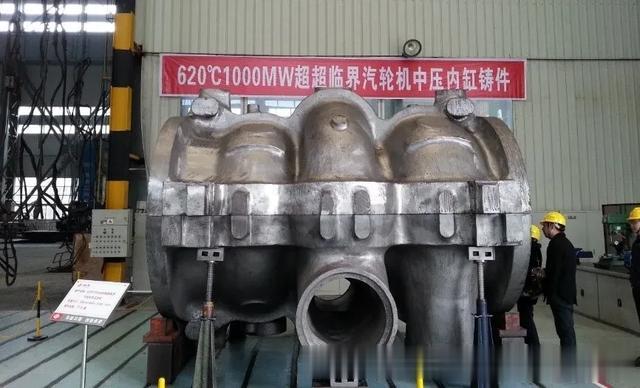
图3 二重试制的首件ZG13Cr9Mo₂Co₁NiVNbNB耐热钢汽缸铸件
三、行业标准
ZG13Cr9Mo₂Co₁NiVNbNB钢的开发应用和实现铸件国产化生产制造,极大地推动了我国先进火电装备制造业向高端自主发展。但是长期以来,行业里面缺少适用于620℃~630℃超超临界汽轮机用材料铸件行业标准。
2016年,上海汽轮机厂牵头组织二重、哈汽,通过全国大型铸锻件标准化委员会申请立项制定行业标准《超超临界汽轮机用ZG13Cr9Mo₂Co₁NiVNbNB耐热钢铸件 技术条件》。2017年8月由工业和信息化部批准下达行业标准项目计划(工信厅[2017]70号),计划编号2017-0497T-JB,项目名称“超超临界汽轮机用ZG13Cr9Mo₂Co₁NiVNbNB耐热钢铸件 技术条件”,正式启动标准的制定工作。
《超超临界汽轮机用ZG13Cr9Mo₂Co₁NiVNbNB耐热钢铸件 技术条件(JB/T14047-2021)》于2021年5月1发布,2021年10月1日实施。此后,ZG13Cr9Mo₂Co₁NiVNbNB耐热钢铸件更为行业所认可。
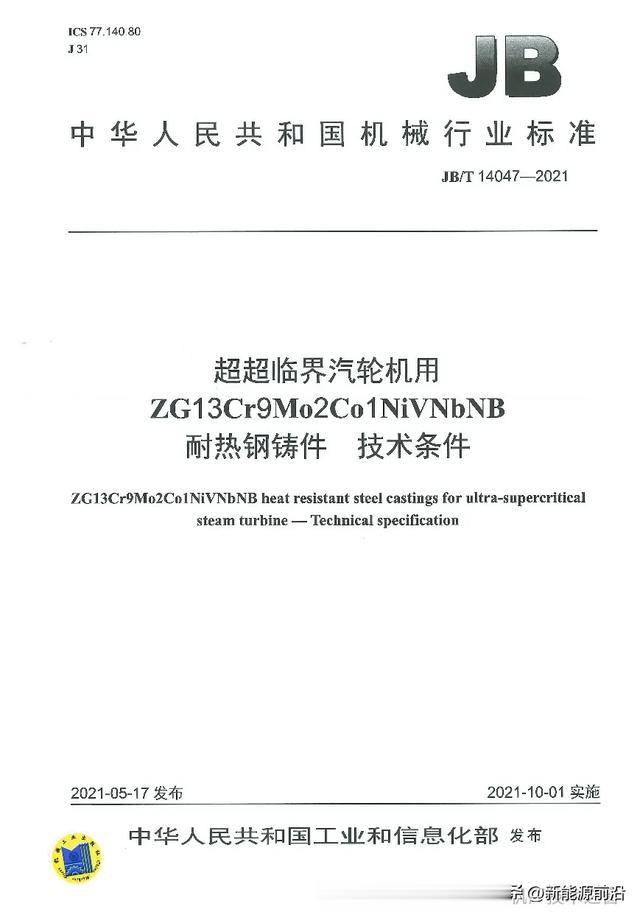
图4 JB/T14047-2021
四、社会、经济效益
近年来随着国家电力行业绿色低碳转型的快速发展,620℃~630℃机组占比逐年提高,国内主要三大汽轮机制造厂上汽、哈汽、东汽每年约有70台机组投产,基本上实现了ZG13Cr9Mo₂Co₁NiVNbNB耐热钢铸件的国产化制造,给国内铸件制造行业带来了巨大的经济效益。
采用ZG13Cr9Mo₂Co₁NiVNbNB耐热钢铸件的620℃~630℃先进的高参数超超临界汽轮机组,其机组效率更高、排放更低,引领了超超临界汽轮机组技术发展的重要方向,顺应了国家提出的“高效、清洁、低碳”的能源发展方向,社会和环保等综合效益十分显著。