碳化硅晶圆划片技术研究
高爱梅,黄卫国,韩 瑞
( 中国电子科技集团公司第四十五研究所)
摘要:
碳化硅(SiC)材料具有禁带宽度大、导热性好、载流 子 迁 移 率 高 等 优 点 ,是第 三 代 半 导 体材料的代表之一。 因其莫氏硬度大,致使划片难度增大,严重制约了碳化硅器件的规模化发展;通过分析碳化硅的材料特性和现有划片技术特点,结合工艺试验,提出了几种碳化硅晶圆的划片方法,给出工艺参数并分析各自的优缺点,获得了理想的加工工艺。
碳化 硅 是 宽 禁 带 半 导 体 器 件 制 造 的 核 心 材料,SiC 器件具有高频、大功率、耐高温、耐辐射、抗干扰、体积小、重量轻等诸多优势,是目前硅和砷化镓等半导体材料所无法比拟的,应用前景十分广阔,是核心器件发展需要的关键材料,由于其加工难度大,一直未能得到大规模推广应用。碳化硅材料的加工难度体现在:(1)硬度大,莫氏硬度分布 在 9.2 ~9.6;(2) 化学 稳 定 性 高 ,几 乎 不 与 任何强酸或强碱发生反应;(3) 加工设备尚不成熟。因此,围绕碳化硅晶圆划片工艺和设备展开研究,对推动我国碳化硅新型电子元器件的发展,促进第三代半导体产业发展有着积极的意义。
1 碳化 硅 材 料 特 性
碳化硅是ⅠⅤ-ⅠⅤ族二元化合物半导体,具有很强的离子共价键,结合能量稳定,具有优越的力学、化学性能。材料带隙即禁带能量决定了器件很多性能,包括光谱响应、抗辐射、工作温度、击穿电压等,碳化硅禁带宽度大。如最常用的 4H-SiC禁带能量是 3.23 eV,因此,具有良好的紫外光谱响应特性,被用于制作紫外光电二极管。SiC 临界击穿电场比常用半导体硅和砷化镓大很多,其制作的器件具有很好的耐高压特性。另外,击穿电场和热导率决定器件的最 大 功 率 传 输 能 力 ,SiC 热导率高达 5W/(cm·K),比许多金属还要高,因此非常适合做高温、大功率器件和电路。碳化硅热稳定性很好,可以工作在 300~600 ℃。碳化硅硬度高,耐磨性好,常用来研磨或切割其它材料,这就意味着碳化硅衬底的划切非常棘手。
目前,用于制作电子器件的碳化硅晶圆主要有 2 种,N 型导电晶圆厚度 150~350 μm,电阻率0.010~0.028 Ω·cm2,主要应用于发光二极管、电力电 子 行 业 的 功 率器 件 。 高纯 半 绝 缘 晶 圆 厚 度50 ~100 μm,电 阻 率 1 ×108 Ω·cm2,主 要 用 于 微波射频、氮化镓晶体管等领域。针对半导体行业应用的 SiC 晶圆划切,研究几种加工方法的特点及应用。
2 碳化 硅 晶 圆 划 片 方 法
2.1 砂轮 划 片
砂轮划片机是通过空气静压电主轴驱动刀片高速旋转,实现对材料的强力磨削。所用的刀片刃口镀有金刚砂颗粒,金刚砂的莫氏硬度为 10 级,仅仅比硬度 9.5 级的 SiC 略高一点,反复地低速磨削不仅费时,而且费力,同时也会造成刀具频繁磨损。如:100 mm(4 英寸)SiC 晶圆划切每片需要6~8h,且易造成崩边缺陷。因此,这种传统的低效加工方式已经逐渐被激光划片取代。
2.2 激光 全 划
激光划片是利用高能激光束照射工件表面,使被照射区域局部熔化、气化,从而达到去除材料,实现划片的过程。激光划片是非接触式加工,无机械应力损伤,加工方式灵活,不存在刀具损耗和水污染,设备使用维护成本低。为避免激光划透晶圆时损伤支撑膜,采用耐高温烧蚀的 UV 膜。
目前,激光划片设备采用工业激光器,波长主要有 1064 nm、532 nm、355 nm 三种 , 脉 宽 为 纳秒、皮秒和飞秒级。理论上,激光波长越短、脉宽越短,加工热效应越小,有利于微细精密加工,但成本相对较高。355 nm 的紫外纳秒激光器因其技术成熟、成本低、加工热效应小,应用非常广泛。近几年 1064 nm 的皮秒激光器技术发展迅速,应用到很多新领域,获得了很好的效果。图 1、图 2 分别对 2 种激光器划切 SiC 晶圆的效果进行了对比。
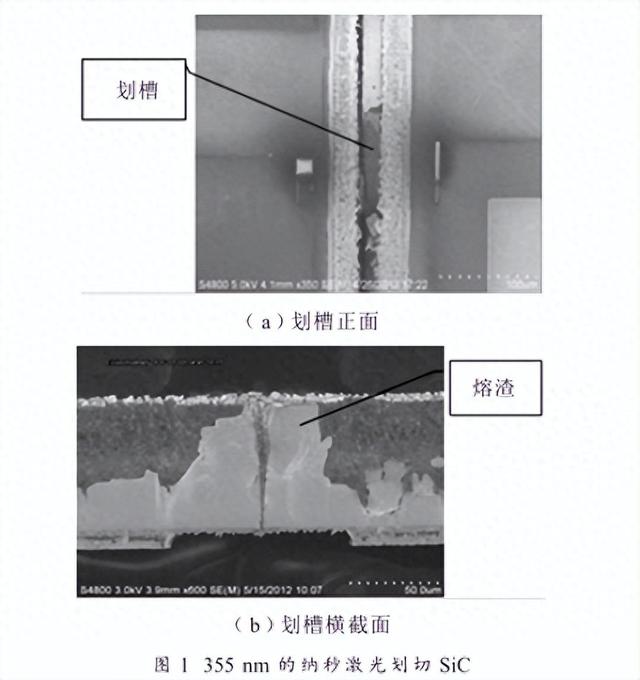
从图 1、图 2 中可以看出,355 nm 紫外激光加工热效应小,但未完全气化的熔渣在切割道内粘连堆积,使得切割断面不光滑,附着的熔渣在后续工艺环节容易脱落,影响器件性能。1064 nm 的皮秒激 光 器 采 用 较 大 的 功 率 ,划 切 效 率 高 ,材 料 去除充分,断面均匀一致,但加工热效应太大,芯片设计中需要预留更宽的划切道 。355 nm 纳秒 和1064 nm 皮秒激光器的参数及其 2 种激光器划切准100 mm、厚 80 μmSiC 晶圆的效果如表 1 所示。
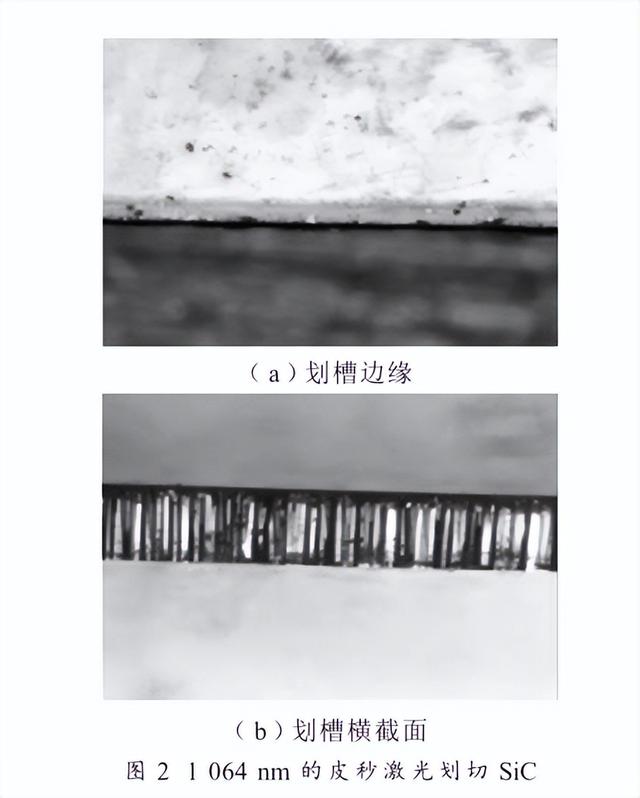

2.3 激光 半 划
激光半划适用于解理性较好的材料加工,激光划切至一定深度,然后采用裂片方式,沿切割道产生纵向延伸的应力使芯片分离。这种加工方式效率高,无需贴膜去膜工序,加工成本低。但碳化硅晶圆的解理性差,不易裂片,裂开的一面容易崩边,划过的部分仍然存在熔渣粘连现象,如图 3 所示。
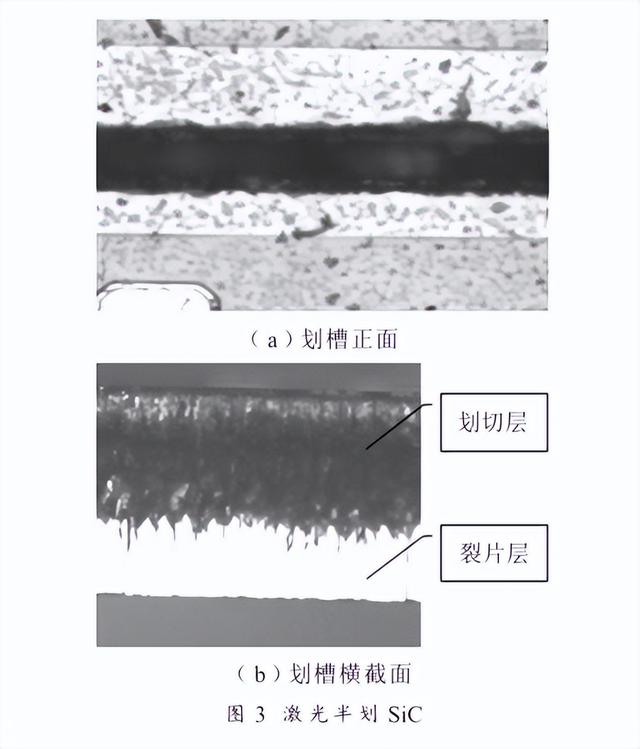
2.4 激光 隐 形 划 切
激光隐形划切是将激光聚焦在材料内部,形成改质层,然后通过裂片或扩膜的方式分离芯片。表面无粉尘污染,几乎无材料损耗,加工效率高。实现隐形划切的 2 个条件是材料对激光透明,足够的脉冲能量产生多光子吸收。碳化硅在室温下的带隙能量 Eg 约为 3.2 eV,即为 5.13×10-19 J。1064 nm 激光光子能量 E = hc/λ =1.87×10-19 J。可见 1064 nm 的激光光子能量小于碳化硅材料 的吸收带隙,在光学上呈透明特性,满足隐形划切的条件。实际的透过率与材料表面特性、厚度、掺杂物的种类等因素有关,以厚度 300 μm 的碳化硅抛光晶圆为例,实测 1064 nm 激光透过率 约 为67%。选用脉冲宽度极短的皮秒激光,多光子吸收产生的能量不转换成热能,只在材料内部引起一定深度的改质层,改质层是材料内部裂纹区、熔融区或折射率变化区。然后通过后续的裂片工艺,晶粒将沿着改质层分离。
碳化硅材料解理性差,改质层的间隔不能太大。试验采用 JHQ-611 全自动划片机 和 350 μm厚的 SiC 晶圆,划切 22 层,划切速度 500 mm/s,裂开后的断面比较光滑,崩边小,边缘整齐,如图4 所示。
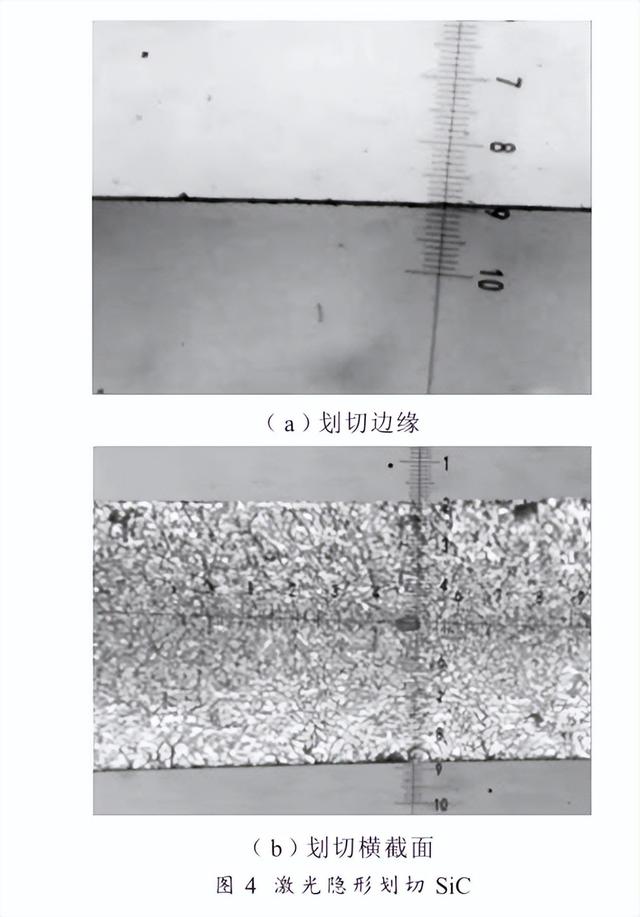
2.5 水导 激 光 划 切
水导激光是将激光聚焦后导入微水柱中,水柱的直径根据喷嘴孔径而异,有 100~30 μm 多种规格。利用水柱与空气界面全反射的原理,激光被导入水柱后将沿着水柱行进方向传播。在水柱维持稳定的范围内都能进行加工,超长的有效工作距离特别适合厚材料的切割。传统激光切割时,能量的累积和传导是造成切割道两侧热损伤的主要原因,而水导激光因水柱的作用,将每个脉冲残留的热量迅速带走不会累积在工件上,因此切割道干净利落。基于这些优点,理论上水导激光切割碳化硅是不错的选择,但该技术难度大,相关的设备成熟度不高,作为易损件的喷嘴制作难度大,如果不能精确稳定地控制微细水柱,飞溅的水滴烧蚀芯片,影响成品率。因此,该工艺目前尚未应用到碳化硅晶圆生产环节中。
3 结束 语
本文分析了目前碳化硅晶圆划片的几种工艺方法,结合工艺试验和数据,比较各自的优劣和可行性。其中,激光隐形划片与裂片结合的加工方法,加工效率高、工艺效果满足生产需求,是碳化硅晶圆的理想加工方式。