友情提示:本公众号主要包括蒸发工艺与设备-配套机械与设备-化工环保安全-锂盐锂电四大方向内容。读者若在本期未见到自己心仪的文章,还请读者耐心等几日或翻阅早期文章。
原料情况:锂瓷石(锂长石)原矿石含水率约3%;外观一般为白色、灰白色,摩氏硬度为6~6.5,密度为2.61~2.64g/cm3,熔点为930℃左右。在自然界的锂长石矿物很难达到其理论值,锂瓷石在加热过程中,其熔点一般为 980℃。在天然锂瓷石矿,其熔点随化学组成不同而有所变化,硅的含量越大,熔点温度也越高。
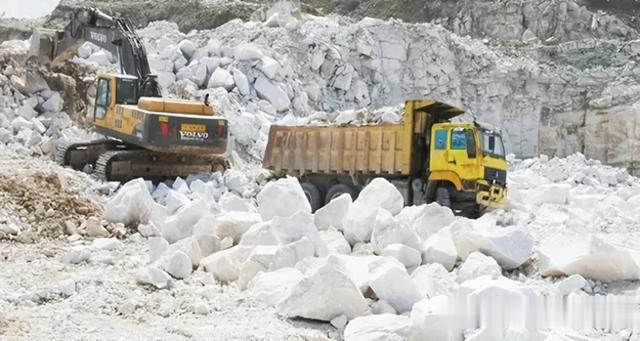
某含锂瓷土原矿化学组分如下表所示:
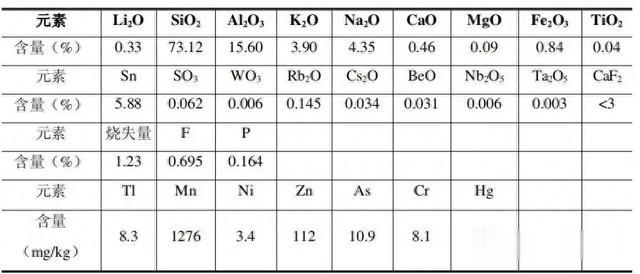
锂瓷石(锂长石)经选选矿后的锂云母精矿:锂瓷石原矿中氧化锂含量为0.33%,精选后的锂云母品位定为1.9%以上。金属锂回收率在65%以上。锂云母精矿作为提炼碳酸锂的原料。
锂瓷石经混料焙烧-溶锂除杂-沉锂及精制等环节生产电池级碳酸锂详细介绍如下:
一、混料焙烧系统
配料及混料:将锂瓷石、硫酸钙、氢氧化钙通过泵车打入原辅料罐中,再通过气流输送的形式送入各自的配料斗内,硫酸钠以装载机加料的形式加入配料斗,然后按锂瓷石和氢氧化钙、硫酸钙、硫酸钠18:2.5:3:2配备,且将焙烧烟气收集粉尘分批混入。锂瓷石和氢氧化钙、硫酸钙、硫酸钠通过配料斗分别经皮带输送机送入混料机,混料时加入少量水,使得混合料水分达到3~6%,混料过程约5min,使锂瓷石和各辅料充分混合均匀。
压制成型、焙烧:混料完成后经皮带输送机输送至给料斗暂存,再通过皮带机送入压砖机,压制成坯体,压制过程中采用全自动成型机。成型后的坯体物料经机械手在窑车上码垛成型,由于砖坯压制成型的仍然含有水分,含水率约为4%,需充分干燥,故在隧道窑系统回车线上布置干燥窑,经窑车送入,干燥后出口砖坯含水率进一步下降。干燥室为装配式钢架结构,内衬高铝砖,外侧用棉毯保温,密封严实。干燥室热量来自高温焙烧室外排高温烟气,采用分散侧送热风,顶排潮方式。送热风温度250~300℃,排潮温度100~150℃。隧道窑配有顶车机,可实现窑车不同速度的切换。

窑车从干燥窑出来后,通过摆渡车进入隧道窑焙烧窑,窑头至窑尾从长度上分不同的功能段,从前往后的分段为:排湿段、燃烧段、冷却段,各段的长度比例和温度是根据产品的烧成曲线而制定的。根据不同带温度要求和耐火保温要求,窑内砌筑相应的耐火保温材料,热源供应为多个小功率烧嘴,燃料为天然气。温度自控,采用PID控制仪表和电动调节阀调节燃料供应量来控制温度,属分散型控制。
在窑头设有排烟风机,其功能是将窑内的烟气抽出,项目烟气路径为从燃烧段至干燥段进行坯体烘干,再从窑头被抽出,将抽出的高温烟气作为干燥窑的热源,助燃风机为烧嘴提供助燃空气,急冷风机的功能是向窑内供入自然风,将烧好的产品快速冷却下来,抽热风机的功能是将急冷带和尾冷带供入的冷风经与砖坯热交换后抽出。隧道窑预热烘干热量来源于烧成窑烟气、产自冷却窑余热风,使砖块预热至120℃。预热砖块通过进料小车输送至烧成窑,烧成窑内控制温度800~1000℃。焙烧中各股废气的走向见上示意图。
焙烧窑通过直接加热的方式对坯体进行高温焙烧,排湿段的温度为80~720℃,燃烧段控制烧结温度为800~1000℃,冷却段出口的温度为80℃,物料在窑内停留时间为8h。控制烧结温度为800~1000℃,已知原料熔点约为903℃左右,硫酸钠的熔点为884℃,氢氧化钙熔点580℃,硫酸钙熔点为1297℃。在该焙烧窑控制温度下,原材料中主要成分处于熔融状态,熔点较高的矿物质以固体形式存在。处于熔融状态下的原料中元素在高温焙烧作用下,与熔融状态下的硫酸盐发生离子交换反应。
锂在焙烧过程中的反应率约90%,氯元素转化为氯化氢的转化率为10%,剩余部分的氯元素以氯离子的形式存在与焙烧产物中。在经焙烧之后,原料锂瓷石中90%锂元素以硫酸锂的形式存在于焙烧产物中,10%的锂元素以氧化锂的形式存在与焙烧产物中,使得绝大部分锂元素以可溶于水的硫酸锂形式进入下一道工序。锂瓷石中的其他碱金属(钠、钾、铷、铯)以易溶盐的形式从焙烧过程中释放出来存于焙烧产物中。
锂瓷石中的其他金属元素形式存在及对应沸点或熔点温度如下:铊(熔点:303.5℃、沸点1457℃)、氧化铍(熔点:2350℃、沸点2575℃)、氧化锰(熔点:1650℃、沸点3400℃)、氧化亚铁(熔点:1370℃、沸点3414℃)、氧化镍(熔点1984℃)、氧化铜(熔点1326℃)、氧化锌(熔点1795℃)、砷(沸点614℃)、三氧化二铬(熔点:2435℃、沸点:4000℃)、氧化镉(熔点:1426℃、沸点1385℃)、氧化铅(熔点:888℃、沸点1535℃)、汞(沸点302℃)等。根据金属氧化物的性质,金属活动性顺序表中排在铜之后的金属氧化物,受热分解。根据锂瓷石的原料成分表,满足该条件的只有金属汞,汞在锂瓷石中存在的形式为单质汞。
焙烧窑焙烧温度为800-1000℃,焙烧过程中当物质沸点或熔点温度低于1000℃时,该物质的存在形式、状态发生变化。根据锂瓷石中的其他金属元素形式存在及对应沸点或熔点温度,形态发生变化的有金属砷、汞、铊、氧化铅。
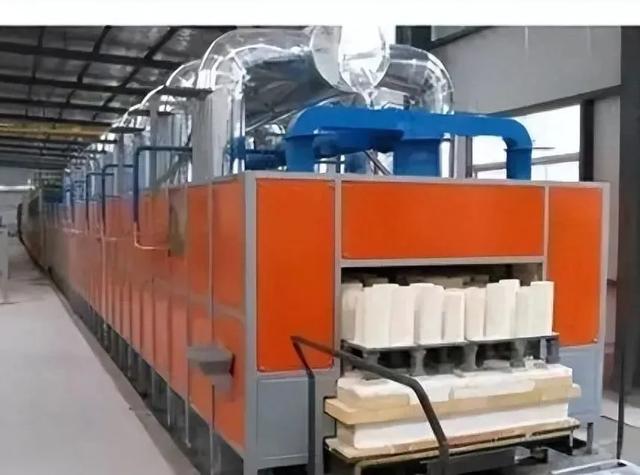
在高温焙烧过程中,锂瓷石中绝大部分氟被钙固化变成更加稳定的CaF2和CaO·3Al2O3·CaF2而存在于焙烧残渣中,该矿物不溶于水而固定在固相中,实现了大部分氟的固定,仅有少部分氟以氟化氢气体的形式随着焙烧废气而排出。焙烧反应机理如下:
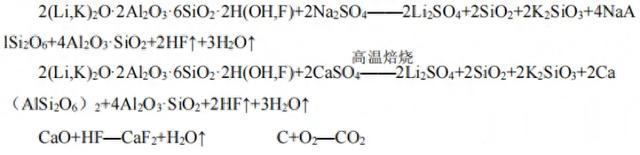
同时也发生如下副反应:
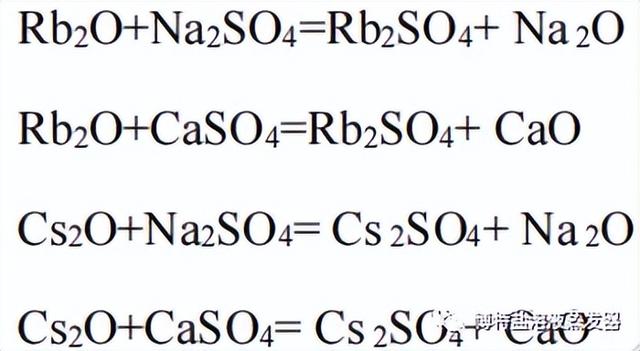
冷却:物料在高温焙烧时,由于部分物料熔融,烧结出来的坯体会有一定的强度,需对其进行冷却,在焙烧窑的冷却段中,经强制风冷却降温至150℃左右。焙烧后的冷却时间约为1.5小时。
焙烧料破碎:冷却后的焙烧料经皮带输送至颚式破碎机破碎,破碎至粒度≤30mm后,然后将破碎后的物料皮带输送至料仓储存,破碎好的熟料经料仓放料皮带输送至下一段工序。
磨粉、筛分:破碎好的熟料送入进料斗,进料斗下料至密闭皮带输送机送入立磨机内进行磨粉,磨粉后经筛分的熟料打入浆化槽内,浆化液经泵送至浸出过滤系统。不过筛的熟料返回磨粉工序继续磨粉。
二、浸出过滤系统
浸出、过滤:经过焙烧后,锂、钾、钠、铷、铯等金属元素以易溶于水的硫酸盐式存在,磨粉后的物料输送到浆化搅拌槽内浸出,浸出时间约0.5小时,浸出过程为常温,pH控制为8,过程中可使锂、钾、钠、铷、铯、钙等金属化合物充分的溶解于水中,锂浸出率约为95%左右。原料中除氧化镁极微溶于水外的其他金属氧化物均不溶于水,氧化镁溶于水的量约1L中溶解8.6mg。铷、铯元素一直存在于冷冻结晶、过滤后得到的硫酸锂溶液中,以铷硫酸、铯硫酸形式存在,一直在生产体系内循环使用,当硫酸铷、硫酸铯溶液达到溶液的饱和度时,会有少量的硫酸铷、硫酸铯晶体析出。浸出完成后使用泵将浸出液通过管道输送至卤水车间,然后采用真空带式过滤机进行固液分离,过滤出的浸出渣组成成分为二氧化硅、硫酸钙、不或难溶于水的金属氧化物、硫酸铷、硫酸铯等,浸出渣含水率约20%。浸出渣经两级逆流洗涤后洗涤液回用于浸出工序,洗涤水使用量与浸出渣为0.6:1,洗涤后的浸出渣作为固废。浸出过程主要为将硫酸锂、硫酸铝等溶解至浸出液中。抽样进行检验,其浸出液控制标准:Li2O:21~27g/L、钠≤60g/L、钾≤35g/L、外观澄清,若浸出液的氧化锂不达标,则返回至浆化搅拌槽内。

浸出过程主要化学反应方程式如下:

净化、压滤分离:浸出液中除了Li+、Na+、F-和SO42-外,还有一定量Al3+、Mg2+,该工艺主要去除浸出液中的SO42-、F-、Al3+、Mg2+。项目净化过程中加入过量的氢氧化钙进行除杂提纯,用氢氧化钙调节pH至12左右,反应1小时。其反应机理如下:
Ca2++SO4 2-=CaSO4
Al3++OH-=Al(OH)3
Mg2++OH-=Mg(OH)2
Ca2++F-=CaF2
反应过后的浆料再经板框压滤机进行固液分离。沉淀物以滤渣形式除去,得到金属锂卤水,经管道送入卤水库;压滤产生的净化渣经板框在线洗涤后洗涤液回用于浸出工序,洗涤水使用量与净化渣为1:4,洗涤后的净化渣作为固废。净化渣主要成分为氢氧化铝、氢氧化镁、硫酸钙和氟化钙等,净化渣含水率约20%。
三、碳酸锂生产系统
碳酸锂系统主要由锂溶液精制工段(包括除杂、净化、浓缩、冷冻、消晶、离子树脂交换处理)、碳酸钠溶液精制工段、碳酸锂制备工段(包括沉锂、洗锂)、成品包装工段(包括烘干、粉碎、包装)和沉锂母液处理工段(包括母液脱碳、浓缩、出盐)等组成。
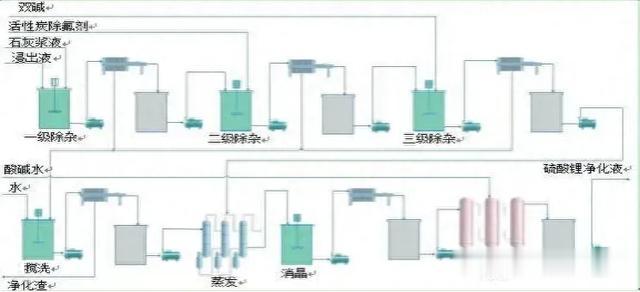
除杂、过滤:来自浸出过滤车间的浸出母液与氢氧化钠溶液按比例加入除杂釜中,控制温度60-90℃,pH8-10,调整搅拌速度使溶液充分混合,反应80min后的料浆经板框压滤机进行液固分离,滤渣经洗涤后厂区内堆存,洗涤液回用于浸出工序;滤液于除杂溶液贮罐中缓存。加入氢氧化钠的主要目的去除浸出液中的铁、铍、锰、铅、镉、铬、铊等杂质,形成铁、铍、锰、铅、镉、铊等的氢氧化物沉淀,锂溶液以滤液形式进入下道工序。铁、铍、锰、铅、镉、铬、铊等在过滤过程中主要以氢氧化物形式被除去。
具体反应方程式如下:
Mn++nOH-=M(OH)n↓(Mn+代表Fe、Be、Mn、Tl、Cd、Cr等金属离子)。
净化、过滤:除杂后的溶液送至净化釜,加入碳酸钠溶液,升温至85℃左右。反应60分钟后的料浆经板框压滤机进行液固分离,洗涤液回用于浸出工序;滤液于净化溶液贮罐中缓存后送一级蒸发系统提高硫酸锂浓度。滤渣中含有部分锂,用收集的MVR浓缩蒸发冷凝水进行洗涤,洗涤水回用于前面的浸出工段使用。净化目的是去除浸出液中的残留钙,形成碳酸钙沉淀。
具体反应方程式如下:
Ca2++CO32-=CaCO3为钙碳酸沉淀反应。
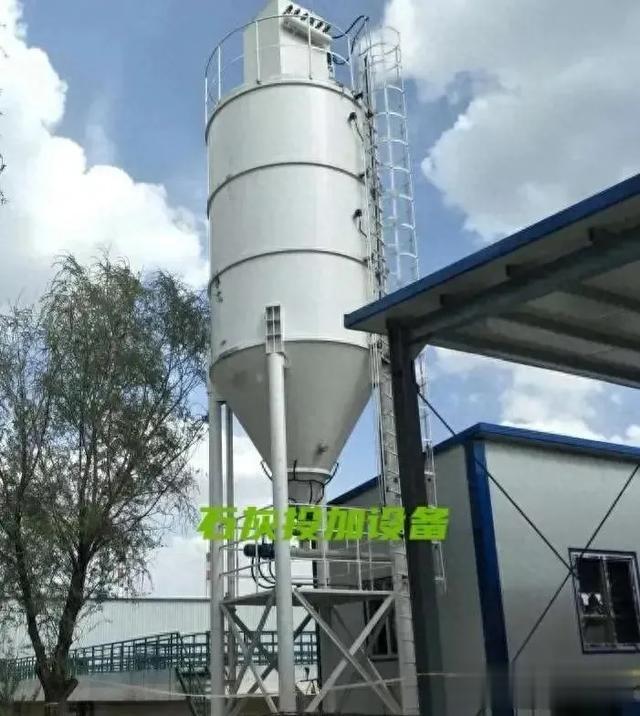
硫酸锂溶液蒸发浓缩:经过碳酸钠除钙后的溶液及后端冷冻结晶后的母液混合后,硫酸锂浓度较低,需将其浓度提高到约90g/L。工艺流程上采用博特盐溶液蒸发器的机械蒸汽再压缩(MVR)技术,即物料进入二效降膜或强制循环蒸发器进行加热蒸发,蒸发产生的二次汽经过离心压缩机将二次汽的温度提高约116℃后作为蒸发器的加热源,二次汽冷凝水先经过板式换热器与初始的硫酸锂溶液进行换热以提高溶液的进料温度,然后冷凝水部分送往浸出工序作为洗水用。蒸发浓缩温度约90~98℃。

消晶:来自蒸发车间的浓缩锂液含有少量的晶体,于浓缩锂液储罐中缓冲后送至消晶釜进行消晶。
锂溶液离子树脂交换:消晶后,锂溶液中钙、镁离子可能有点偏高,需要采用螯合树脂进一步纯化,除去钙、镁等离子(螯合树脂是一类能与金属离子形成多配位络和物的交联功能高分子材料。螯合树脂上的功能原子与钙、镁等离子发生配位反应,形成类似小分子螯合物的稳定结构,而离子交换树脂吸附的机理是静电作用)。当树脂运行失效后,用清水反冲树脂,再用酸对树脂再生洗脱转变为轻型状态,再用氢氧化钠溶液转型为钠型状态,树脂得到再生可继续使用,再生溶液含有锂,返回浸出工序。硫酸锂溶液经处理达控制要求,打入储罐供沉锂使用。
沉锂、离心分离:将碳酸钠溶液(为保证沉锂纯度更高,精制碳酸锂溶液杂质更少)和浓缩锂溶液送至沉锂釜,保持沉锂釜内反应温度90-95℃,并持续搅拌反应2h,沉锂反应后离心机进行离心分离,得到碳酸锂湿料和沉锂母液,沉锂母液送至脱碳工序,碳酸锂湿料送至洗锂工序。
沉锂主要反应:
Li2SO4+Na2CO3=Li2CO3↓+Na2SO4
洗锂、离心分离:碳酸锂湿料需要进行浆化洗锂,将钠离子、硫酸根、残留碳酸根等杂质洗干净。具体操作:沉锂离心后的碳酸锂固体与纯水按一定比例加入,于浆化罐中搅拌;然后泵入洗锂釜,陈化时间为60-90min。待陈化完成,浆化料进行离心分离和洗涤,得到合格的湿碳酸锂,洗锂液中含有溶解的碳酸锂,用于碳酸钠溶液的制备。
碳酸钠溶液制备工段:将碳酸钠用洗锂水溶液溶解配置成碳酸钠溶液,配制好后的溶液于碱液中转存储罐备用。
脱碳:沉锂母液送往脱碳釜,加浓硫酸酸化脱碳(脱碳加入硫酸主要为去除沉锂母液中的碳酸根离子),溶液pH控制在4-6。产生的CO2经釜内排气孔排出,加入硫酸目的是与碳酸根离子,生成二氧化碳和水,不产生固体。CO2排出后,再加入氢氧化钠,目的是把溶液pH值调成弱碱性,母液浓缩时,可大大减少对蒸发浓缩设备的腐蚀(含氟离子在酸性环境下对设备的腐蚀较大)。脱碳后,脱碳溶液输送到MVR蒸发器进行蒸发浓缩处理。
脱碳反应方程式:
H2SO4+CO32-=SO42-+CO2↑+H2O
沉锂母液蒸发结晶:脱碳后的沉锂母液,输送到博特盐溶液MVR蒸发器进行蒸发浓缩。脱碳后沉锂母液通过板式换热器预热后,进入蒸发系统进行蒸发浓缩,温度90~98℃,将母液浓缩到一定程度,使钾、钠形成晶体析出,蒸发冷凝水收集后回用。浓缩结晶盐用离心式过滤机进行过滤,固相为钠钾盐晶体,送至钠钾盐暂存库,后返回配料、混料工序作为添加剂配料,液相为含少量硫酸锂的硫酸钾钠饱和溶液。为回收溶液中的硫酸锂,同时降低溶液中硫酸钾和硫酸钠浓度,该溶液再经过冷冻结晶。
冷冻结晶、过滤:蒸发结晶后的母液经预冷后送至冷冻结晶器。硫酸钠和硫酸钾的溶解度随温度降低而变小,冷冻析出硫酸钠钾盐晶体。冷冻出料经泵输送至冷冻稠厚器,经离心机进行固液分离,得到硫酸钠钾盐晶体和硫酸锂溶液。其中硫酸锂溶液返回至净化工序回收硫酸锂,硫酸钠钾盐晶体送至钠钾盐暂存库,而后回用于配料、混料工序,满足生产回用需求后的余下的钠钾盐外售。

四、成品包装工段(包括烘干、粉碎、包装)
成品烘干、除铁:合格湿碳酸锂通过烘干机将水份烘干,调节下料速度和转盘速度,控制碳酸锂水份在0.25%以下,达到电池级碳酸锂标准,烘干机下料口安装除铁器,除去烘干后碳酸锂的磁性物质。
成品粉碎:烘干碳酸锂下料进入到旋振筛,将可能结块料挡在筛网上面,绝大部分物料通过旋振筛,下料到气流粉碎机料斗。运行气流粉碎机,将碳酸锂粉碎至合格粒径范围。
成品包装:粉碎后的碳酸锂用真空输送设备输送至成品混批机混合均匀,混合后用自动包装机进行包装,得到电池级碳酸锂。