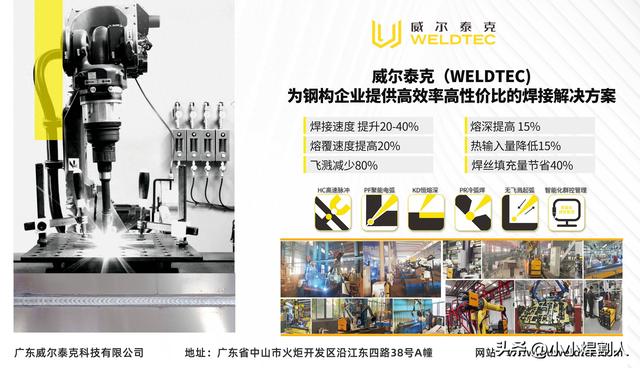
激光焊接是以高能量密度的激光束充当热源的一种高效精密焊接方式。激光焊接属于激光材料加工技术应用的关键方面之一,其运作原理是对激光脉冲的宽度、能量、峰值功率以及重复频率等参数加以控制,促使工件熔化,进而形成特定的熔池。也就是说,激光辐射会对工件表面进行加热,表面热量经由热传导朝内部扩散,通过调控上述参数让工件熔化并构建特定熔池。鉴于激光焊接是一种具备高质量、高精度、低变形、高效率以及高速度等优势的焊接方法,伴随高功率 CO2 与高功率固体 YAG 激光器的出现,还有光纤传输技术的完善以及金属钼焊接聚束物镜等的研制成功,其在机械制造、航空航天、汽车工业、粉末冶金、生物医学、微电子行业等诸多领域的应用越发广泛。
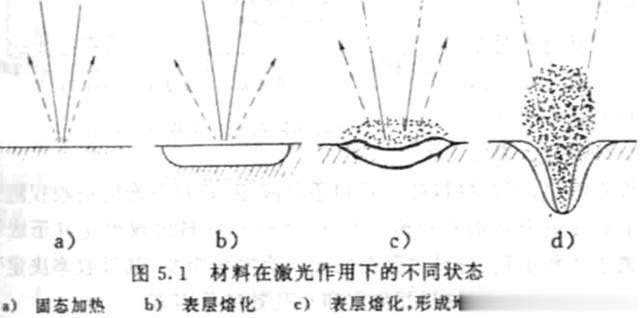
一.激光焊接原理
激光焊接常用的激光光源是气体CO2激光器和固体YAG激光器,按照激光器输出功率的大小和工作状态,激光器工作的方式有连续输出方式和脉冲输出方式。被聚焦的激光光束照射到焊件表面的功率密度,一般在104~107W/cm2。其焊接的机制也因功率密度的大小,区分为激光热传导焊接和激光深熔焊接。
热传导焊接当激光照射在材料表面时,一部分激光被反射,一部分被材料吸收,将光能转化为热能而加热熔化,材料表面层的热以热传导的方式继续向材料深处传递,最后将两焊件熔接在一起。
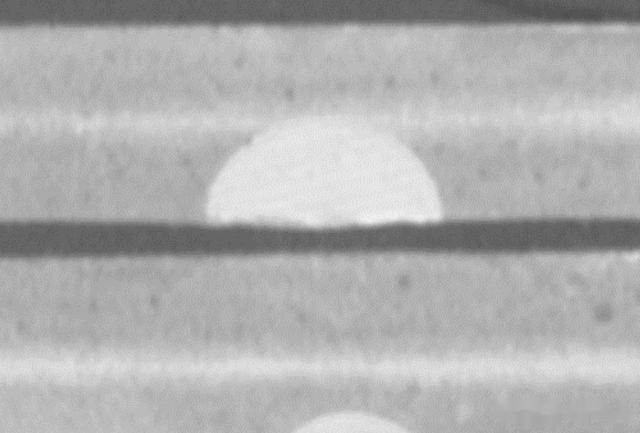
激光深熔焊接依靠小孔效应,使激光光束的光能传向材料深部,激光功率足够大时,小孔深度加大,随着激光光束相对于焊件的移动,金属液体凝固形成焊缝,焊缝窄而深,其深宽比可达到12:1。激光深熔焊接需要足够高的激光功率,但几百瓦的CO2激光器,当激光模式好时,也能产生小孔效应,这是因为基模光束聚焦后能够获得高功率密度。
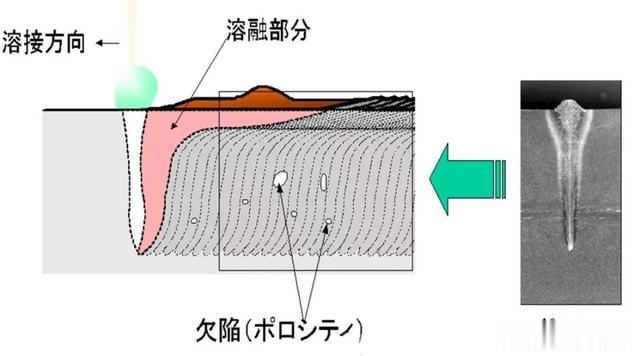
这两种焊接机理根据实际的材料性质和焊接需要来选择,通过调节激光的各焊接工艺参数得到不同的焊接机理。这两种方式最基本的区别在于:前者熔池表面保持封闭,而后者熔池则被激光束穿透成孔。熔池是指因焊弧热而熔化成池状的母材部分。
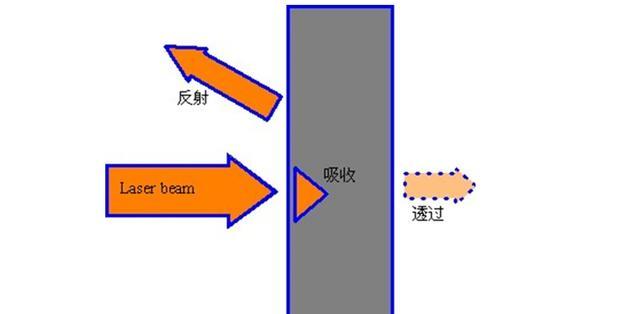
二.激光焊的特点
激光焊接的优点在于其热输入低、焊接变形小、不受电磁场影响,并且非常适合于微型零件和可达性很差的部位的焊接。因此,激光焊接已成功应用于微、小型零件的精密焊接中,焊接质量比传统焊接方法高。
1.优点
(1) 小的加工范围对能量输入可控:小的热应力,小的热影响区,和 小的热变形。
(2) 窄而光滑的焊缝:可以减少或消除焊后处理工序。
(3) 能在室温或特殊条件下进行焊接,焊接设备装置简单。例如,激光通过电磁场,光束不会偏移;激光在真空、空气及某种气体环境中均能施焊,并能通过玻璃或对光束透明的材料进行焊接。
(4)可焊接难熔材料如钛、石英等,并能对异性材料施焊,效果良好。
(5)冷却速度快,焊缝组织微细,故焊接接头性能良好。
(6) 高加工速度,短工作周期。
(7)可进行微型焊接或实现远距离传输,不需要真空装置,利于大批 量自动化生产。
(8) 易于功能集成:激光焊接很容易与其它加工手段,协同生产,例 如折弯,冲床,组装等等,容易实现自动化生产 。
(9)生产过程易于控制:传感系统对加工实时监控,保证焊接质量。
(10)激光焊接不需要与工件接触,避免接触应力。
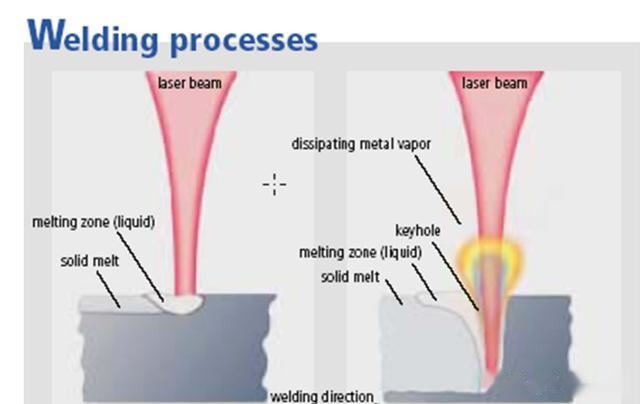
2. 缺点
激光焊虽然是一种新型的焊接方式,具有好的前景,但是也有自身的局限性。
(1)焊接厚度有局限,适合薄材焊接。
(2)工件的夹持要求比较高,间隙尽量小。且要求光束在工件上的位置不能有显著偏移。这是因为激光聚焦后光斑尺寸小,焊缝窄,加填充金属材料。若工件装配精度或光束定位精度达不到要求,很容易造成焊接缺憾。另外精密焊接夹具的成本比较高。
(3)定位要非常准确,对编程的要求比较高。
(4)高反射性及高导热性材料如铝、铜及其合金等,焊接性会有影响;
(5)焊缝快速凝固,不利于气体的排出,可能有气孔及脆化;
(6)设备昂贵,对于小批量的生产或者定位复杂,工序复杂的生产性 价比不高。
三. 激光焊接的分类
1. 激光深熔焊
当功率密度比较大的激光束照射到材料表面时,材料吸收光能转化为热能,材料被加热熔化至汽化,产生大量的金属蒸汽,在蒸汽退出表面时产生的反作用力下,使熔化的金属液体向四周排挤,形成凹坑,随着激光的继续照射,凹坑穿人更深,当激光停止照射后,凹坑周边的熔液回流,冷却凝固后将两焊件焊接在—起。

1. 匙孔 2. 熔融金属 3.焊缝 4. 激光光束 5. 焊接方向 6.金属蒸汽 7. 工件
激光焊缝窄而细,深宽比甚至可以达到10:1。
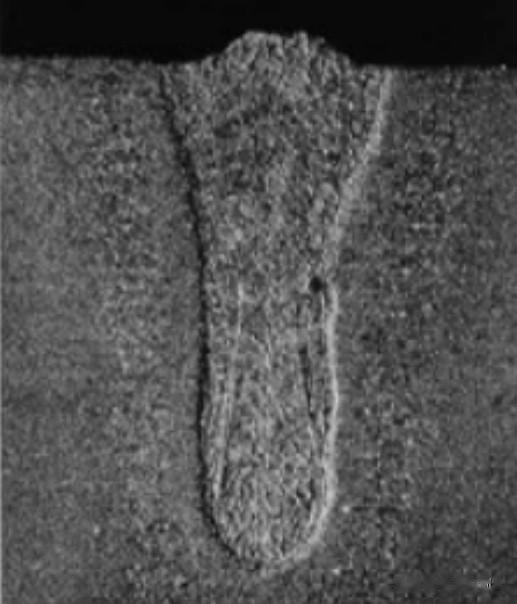
2. 激光热传导焊
激光光束沿着材料边缘,熔融的材料互相熔合后凝固形成焊缝。焊缝深度从接近于零到一毫米。材料的厚度不会超过3mm,通常在2mm以下。
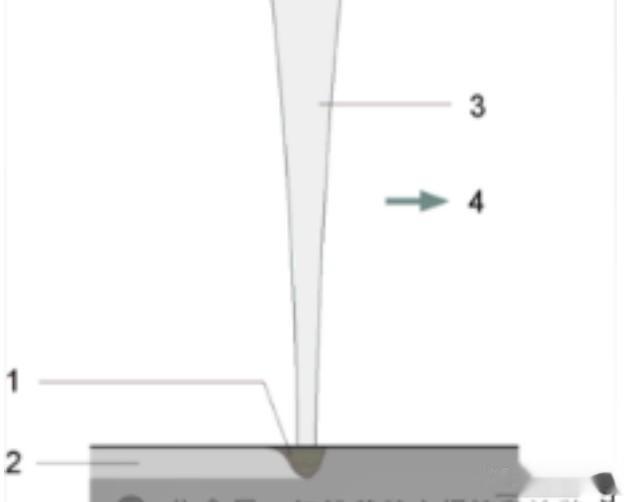
1.熔化材料 2.焊缝 3.激光光束 4.焊接方向 5.工件
固体激光的热传导焊接主要用于薄板角接,例如电池外壳,心脏起搏器的外壳和一些机床的覆盖件。热传导焊接能够产生一个光滑,洁净的圆角焊缝,无需后续加工。
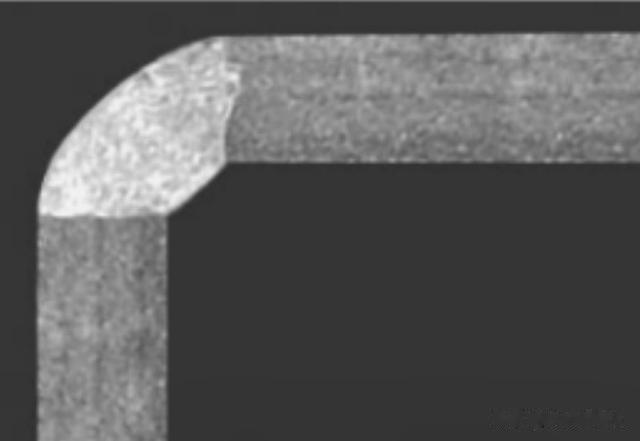
焊接的接头形式:
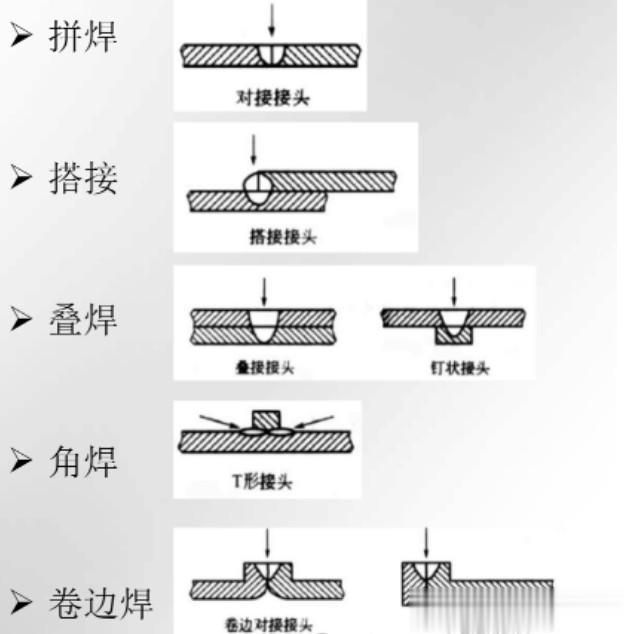
四. 激光焊接的工艺参数
1、功率密度P
激光功率的大小是激光焊接技术的首选参数,只有保证了足够的激光功率,才能得到好的焊接效果。
激光功率较小时,虽然也能产生小孔效应,但有时焊接效果不好,焊缝内有气孔,激光功率加大时,焊缝内气孔消失,因此激光深熔焊接时,不要采用勉强能够产生小孔效应的最小功率。适当加大激光功率,可以提高焊接速度和熔深,只有在功率过大时,才会引起材料过分吸收,使小孔内气体喷溅,或焊缝产生疤痕,甚至使工件焊穿。
功率密度是激光加工中最关键的参数之一。采用较高的功率密度,在微秒时间范围内,表层即可加热至沸点,产生大量汽化。因此,高功率密度对于材料去除加工,如打孔、切割、雕刻有利。对于较低功率密度,表层温度达到沸点需要经历数毫秒,在表层汽化前,底层达到熔点,易形成良好的熔融焊接。焊接熔深(h)随激光功率(P)的增加而增加。
因此,在传导型激光焊接中,功率密度在范围在104~106W/CM2。
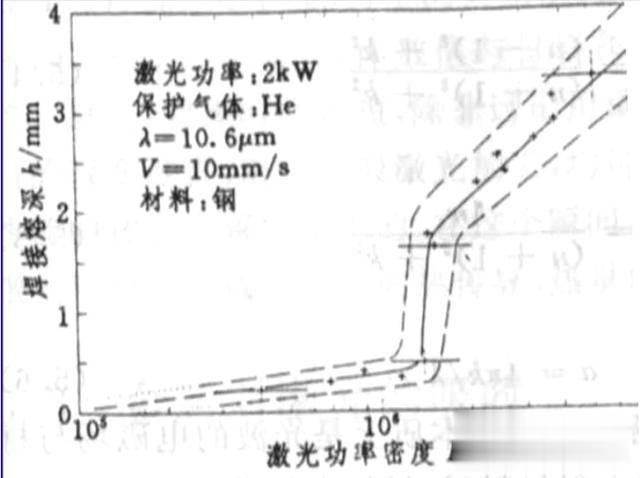
2、激光脉冲波形
激光脉冲波形在激光焊接中是一个重要问题,尤其对于薄片焊接更为重要。当高强度激光束射至材料表面,金属表面将会有60~98%的激光能量反射而损失掉,且反射率随表面温度变化。在一个激光脉冲作用期间内,金属反射率的变化很大。
借用电子电路技术中仿真线的概念,由电感电容网络组成仿真线,通过仿真线放电形成特定形状的激光脉冲,一般通过L-C仿真线网络可以将脉冲展宽,得到一个平顶宽脉冲。根据需要可以使脉宽在3~5ms,最大可做到30ms。
3、激光脉冲宽度
脉宽是脉冲激光焊接的重要参数之一,它既是区别于材料去除和材料熔化的重要参数,也是决定加工设备造价及体积的关键参数。
激光热传导焊接中,激光脉冲宽度与焊缝深度有直接关系,也就是说脉冲宽度决定了材料熔化的深度和焊缝的宽度。据文献记载,熔深的大小随脉宽的1/2次方增加。
如果单纯增加脉冲宽度,只会使焊缝变宽、过熔,引起焊缝附近的金属氧化、变色甚至变形。因此,特殊要求较大熔深时,可使聚焦镜的焦点深入材料内部,使焊缝处发生轻微打孔,部分熔化金属有汽化飞溅现象,焊缝深度变大,此时焊缝表面平整度可能稍差。必要时,改变离焦量重复焊接一遍,可使焊缝表面光滑美观。
4.激光脉冲重复频率
热传导焊接中,激光器发出重复频率激光脉冲,每个激光脉冲形成一个熔斑,焊件与激光光束相对移动速度决定了熔斑的重叠率,一系列的熔斑形成鱼鳞纹似的漂亮焊缝。如仪器、仪表、电池、继电器外壳的密封,板材、管件或需要连接的电子零件、机械零件的焊接等大都使用这种方法。

5、焊接速度
一定条件下,降低速度v,线能量提高,焊接熔深增大。但是速度过低,熔深不会无限增加,反而使熔宽增大。
金属熔化过多,金属蒸汽压力不够;金属蒸汽增加导致等离子体浓度增加。
6、离焦量对焊接质量的影响。
激光焊接通常需要一定的离焦,因为激光焦点处光斑中心的功率密度过高,容易蒸发成孔。离开激光焦点的各平面上,功率密度分布相对均匀。
对于能够正常焊接的激光功率(或是脉冲能量),在焦平面处的激光功率密度往往已经超过激光焊接所需的功率密度,在焦点位置焊接,可能会出现金属汽化、熔渣飞溅或是打孔现象。正确焊接技术是使焦平面离开工件表面一小段距离,这个距离称为离焦量。如下图所示,以工件表面为准,焦平面深入工件内部称为负离焦,焦平面在工件之外称为正离焦。
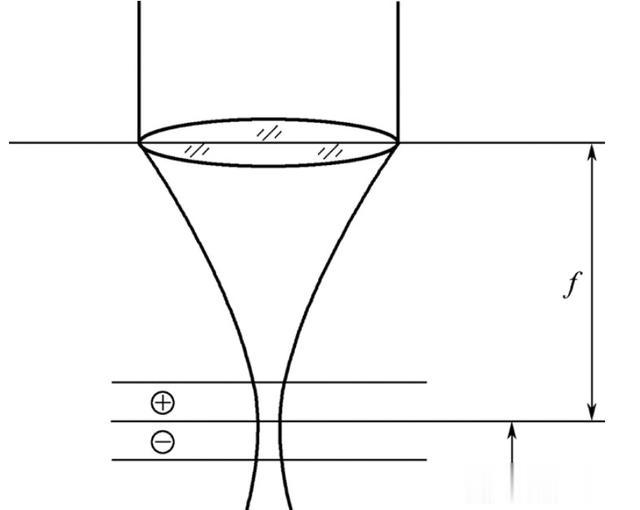
一般对熔深要求不高时最好用正离焦,这样很容易获得牢固美观的焊缝。实际焊接过程中经常是激光器各项参数设置完毕后,最后经由微调离焦量,来达到完美的焊接效果。
7.气体保护
作用是保护熔池,抑制等离子体。保护气体种类:Ar,He,混合气体气体保护方式:同轴顶吹;偏轴侧吹;拖罩+同轴。
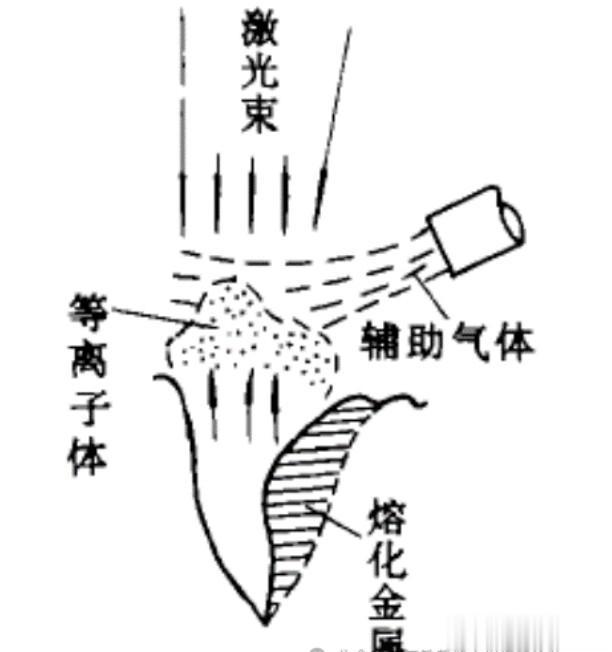
五. 激光焊接适用材料
1. 碳钢及普通合金钢 总的说,碳钢激光焊接效果良好,其焊接质量取决于杂质含量。
材料中硫和磷是产生焊接裂纹的敏感因素如果硫、磷的含量高,不适 合激光焊接。中、高碳钢和普通合金钢都可以进行良好的激光焊接, 但需要预热和焊后处理,以消除应力,避免裂纹形成。
2. 不锈钢的激光焊接 一般的情况下,不锈钢激光焊接比常规焊接更易于获得优质接头。
不锈钢低的热导系数更易于获得深熔窄焊缝。不锈钢又主要分为铁素体不锈钢(接头脆化),奥氏体不锈钢(热裂纹),马氏体不锈钢(焊接性较差),双相不锈钢(焊接影响区容易脆化)。
3.模具钢
S136,SKD-11,NAK80,8407,718,738,H13,P20,W302,2344等。
4. 铝合金的激光焊接
由于铝合金表面的高反射性和高导热性,激光焊接铝合金具有一 定的难度。对于高反材料的激光焊接,能量阀值的表现更明显。
不同系的铝合金,不同的牌号,焊接性能也不一样。
铝的强氧化能力:铝在空气中及焊接时极易氧化,生成的氧化铝熔点高、非 常稳定,不易去除氧化膜的比重大,不易浮出表面,易生成夹渣、未熔合、 未焊透等缺欠。铝材的表面氧化膜和吸附大量的水分,易使焊缝产生气孔。故对工件的清洁度有很高的要求。
较大的热导率和比热容。应当尽量采用能量集中、功率大的能源,有时也可采用预热等工艺措施。一般要求的激光功率比较大。
较大的线膨胀系数,铝凝固时的体积收缩率较大,焊件的变形和应力较大, 铝焊接熔池凝固时容易产生缩孔、缩松、热裂纹及较高的内应力。
铝对光、热的反射能力较强,固、液转态时,没有明显的色泽变化,焊接操作时判断难。高温铝强度很低,支撑熔池困难,容易焊穿。
容易形成气孔:铝及铝合金在液态能溶解大量的氢,固态几乎不溶解氢。在焊接熔池凝固和快速冷却的过程中,氢来不及溢出,极易形成氢气孔。
对工件的清洁度有很高的要求,包括工件及周围环境的干燥。
合金元素易蒸发、烧损,使焊缝性能下降。
5. 铜合金的焊接
类似于铝合金的焊接,但是镜面的铜的反射性能更强。工业最常用的牌号是T1、T2和T3,外观呈紫红色,故又称为紫铜。容易产生的焊接缺陷:未熔合与未焊透(高能量密度的激光束)、焊接变形 、 热裂纹(在结晶过程中,由于低熔点共晶体分布在枝晶间或晶界处,使铜和铜合金具有明显的热脆性,加上焊接应力的作用,极易产生热裂纹)、 气孔(紫铜焊缝中的气孔主要是氢气孔)。
6.不同钢材之间的激光焊接
激光焊接极高的冷却速度和很小的热影响区,为许多不同金属焊接融化后有不同结构的材料相容创造了有利条件。以下金属可以顺利进行激光深熔焊接:不锈钢~低碳钢,416不锈钢~310不锈钢,347不锈钢~HASTALLY镍合金,镍电极~冷锻钢,不同镍含量的双金属带。
7.钛、镍、锡、铜、铝、铬、铌、金、银等多种金属及其合金,及钢、柯伐合金等合金的同种材料间的焊接。有色金属相对难焊,其紫铜合金、银合金最难焊。
8.应用于铜-镍、镍-钛、铜-钛、钛-钼、黄铜-铜、低碳钢-铜等多种异种金属间的焊接。
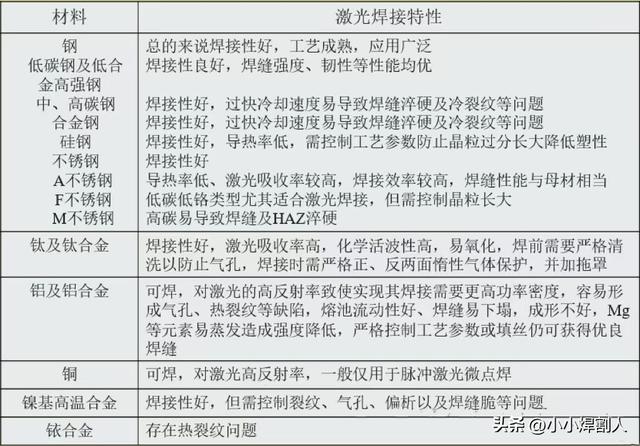
六. 激光焊接要求
焊接之前要求明确客户的焊接要求,一般是对焊缝的强度(熔深要求,气孔控制要求,裂纹控制要求等等),外观(焊缝的平整度, 被氧化程度,深宽比等等)气密性(承载的气压)。
1. 焊缝几何形貌
任何质量检测的目的都是要确认工件的性能是否能够达到使用的 要求。对于焊接来说,激光焊接的质量标准主要集中在焊缝处和焊接热影响区处。
2. 基础要求
焊缝需要满足两个最基本的质量要求:
焊缝宽度和深度必须要满足焊接规范要求,以来满足焊接强度的要求。焊缝金相质量:焊缝内部组织要尽量均匀,晶粒细小均匀。
七.常见焊接缺陷
焊接工艺规范中还包含一些其它的焊接标准和焊接缺陷, 下图展示了不同的焊接缺陷:
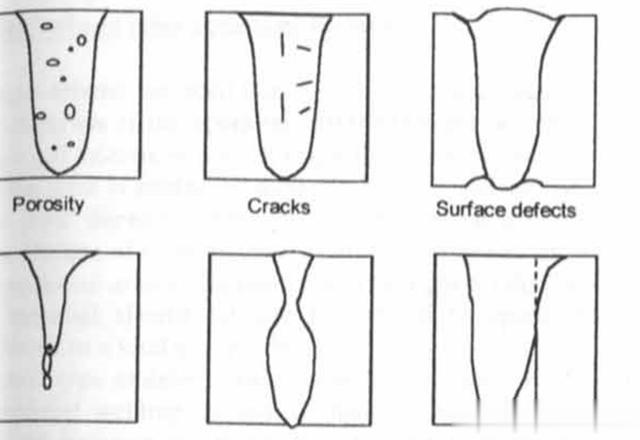
1)气孔 2)裂纹 3)表面缺陷 4)焊钉 5)成型不规则 6)未熔合
3. 焊缝内部缺陷:
典型的焊缝内部缺陷:
1)未熔合:焊缝间隙过大
2) 气孔:两类气孔:
–冶金气孔
H气孔,与弧焊等常规焊接方法类似
–孔洞
激光深熔焊本身小孔失稳密切相关
机理仍然不十分清楚
3) 裂纹:在焊缝的表面或内部,焊缝完全凝固之前,由于焊缝的冷却凝固过程中在高温阶段晶间塑性变形能力不足以承受当时所发生的塑性应变量而产生的,裂纹较多产生于焊缝中心线及热影响区,因而那些具有宽的结晶温度范围、高的C、S、P含量的材料容易产生裂纹,如铝合金的激光焊接过程中容易产生此类裂纹。
对于高C钢或某些高高合金钢而言,冷裂纹也是其激光焊接过程中容易产生的缺陷。由于激光焊接的冷却速度很快,这类钢材由于含C量较高,焊缝中容易得到淬硬组织,较易产生冷裂纹。
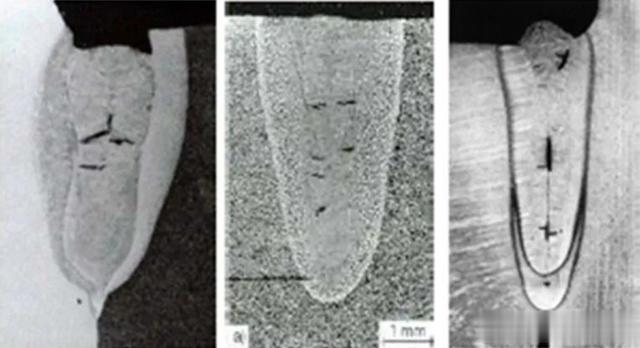
4. 外部焊接缺陷:
a.焊缝形状不均匀:例如焊缝塌陷部位的导致的微裂纹。
b.熔融金属飞溅:由于熔融金属“炸飞”在焊缝表面形成凹坑,降低焊
缝强度甚至形成气孔 。
c.焊缝表面塌陷,及焊缝底部凹陷:降低焊缝的有效受力面积,降低焊
缝强度 。
d.错边:在对接焊缝中,错边导致有效焊缝面积减少。
e.收弧弧坑:减少焊缝有效受力面积 。
f.氧化:降低不锈钢的抗氧化能力。
g.飞溅:飞溅物体落在焊缝或工件表面降低表面质量,增加后续处理工
作。
h.热输入导致焊接变形,在焊接过程中,焊缝内部的热量会传导到焊缝周围的工件导致少量变形。
八.激光焊接的发展趋势
激光器件不断改进
–铝合金等材料激光焊接难题得到解决
–深宽比更大、更厚、速度更快
数控系统
–一维焊缝→二维焊缝→三维焊缝
激光复合焊接技术的发展
–激光电弧、激光等离子体、激光感应、双光束
完整的质量监控
–焊前、焊中、焊后
总之,尽管激光焊接拥有诸多优点,然而,因激光器价格高昂、电光转换效率偏低等因素,激光焊接技术的应用尚未实现广泛普及。不过,中国的激光焊接技术已然处于世界先进水准,具备了运用激光成形超过 12 平方米的复杂钛合金构件的技术实力与能力,且已投入到多个国产航空科研项目的原型及产品制造之中。在 21 世纪,对于半导体晶片和各类积体电路的需求将会达到惊人的数量。作为连接积体电路与硅晶片的纽带,激光焊接在晶片封装技术里得到应用。为了契合集成电路日益小型化、高速化、高密度、多接脚、长寿命等众多需求,激光焊接技术必定会凭借其卓越的优越性发挥关键作用。