第三百五十一条 在有瓦斯或者有煤尘爆炸危险的采掘工作面,应当采用毫 秒爆破。在掘进工作面应当全断面一次起爆,不能全断面一次起爆的,必须采取 安全措施。在采煤工作面可分组装药,但一组装药必须一次起爆。
严禁在1个采煤工作面使用2台发爆器同时进行爆破。
【解读】本条是关于采掘工作面起爆方式和爆破方式的规定。
采掘工作面的起爆方式按延期时间不同,有瞬发爆破和毫秒延期爆破。瞬发 爆破是指起爆药包采用煤矿许用瞬发电雷管起爆的爆破方法;毫秒延期爆破是指 起爆药包采用煤矿许用毫秒延期电雷管起爆的爆破方法。瞬发爆破的优点是瞬时 起爆(<13 ms), 能防止瓦斯、煤尘爆炸,缺点是不能全断面一次爆破。毫秒延 期爆破的技术优点为减少了抛掷作用和抛掷距离,防止崩倒支架或其他设备,而 且爆堆集中,提高了装岩效率;减低了爆破震动作用,有效防止爆破对围岩或周 围设施造成的破坏;能够实现全断面一次爆破,提高掘进速度。
当掘进工作面不能全断面一次爆破时,可采用分次爆破。分次起爆时应采取 以下安全技术措施:
(1)加强顶帮和支架管理,坚持敲帮问顶;
(2)加强新自由面局部通风和瓦斯管理,防止瓦斯超限;
(3)应坚持一次打眼、一次装药、一次爆破,二次打眼避开形成贯通裂隙 的地方,新形成自由面与炮眼的距离大于最小抵抗线;
(4)严格执行“一炮三检”制度和“三人连锁爆破”制度;
(5)注意检查每次爆破后有无拒爆。
采煤工作面爆破,应积极研究改进爆破技术,合理安排循环组织,做到分组 装药,一组装药一次起爆。如果在采煤工作面分组装药,一组装药一次起爆确有 困难时,可以打一次眼,间隔分组一次装药,分组起爆。分组装药的距离不得小 于 2m。为了防止间隔区间未装药炮眼被爆破挤压,可以在炮眼中插上炮棍,最 后视分组爆破情况,在装药爆破间隔区内的炮眼,实现一组装药一次起爆的要求。
采煤工作面一组装药分次起爆存在的危害:
(1)在有瓦斯或煤尘爆炸危险的采煤工作面采用一组装药分次起爆时,前 次爆破后,瓦斯超限或煤尘飞扬,很容易被后次爆破产生的空气冲击波、炽热的 固体颗粒、气体爆炸产物及二次火焰所引燃,以致发生瓦斯或煤尘爆炸,具有极 大的危险性。
(2)一组装药分次起爆时,容易把相邻段炮眼的炸药压死,或把电雷管脚 线崩断,或电雷管、炸药随爆破被带出,或将电雷管桥丝震断,造成拒爆或瞎炮。
(3)一组装药分次起爆,不能根据爆破实际情况有效控制或调整炮眼装药 量。
(4)爆破时若崩倒支柱,往往因不能及时扶起,空顶面积大、时间长,连 线和出煤时,容易发生冒顶伤人事故。
(5)爆破时,容易产生炮震裂缝,贯穿相邻炮眼,容易使爆破火焰从裂缝 中喷出,影响爆破安全及爆破效果。
(6)连线和爆破次数多、时间长、劳动强度大,影响循环作业时间。
在一个采煤工作面使用2台发爆器同时进行爆破,由于爆破时间不可能同 步,会造成一台发爆器起爆后,工作面风流中产生大量的浮游煤尘及瓦斯超限, 极易引发瓦斯或煤尘爆炸及炮烟中毒事故。
第三百五十二条 在高瓦斯矿井采掘工作面采用毫秒爆破时,若采用反向起 爆,必须制定安全技术措施。
【解读】本条是关于在高瓦斯矿井的采掘工作面采用毫秒反向起爆时必须制定安全技术措施的规定。
如果起爆点置于装药顶部,靠近眼口的位置,使爆轰波传向眼底,这种起爆 方式为正向起爆。由正向起爆实施的爆破称为正向爆破。反之,起爆点置于装药 底部,爆轰波传向眼口称为反向起爆。
从操作方便上讲,反向爆破比正向爆破好。主要是装药时可一只手拽着脚线 进行操作,一旦炮眼发生堵塞炸药装不到眼底,可利用脚线将炸药退回来,待疏 通炮眼后重新装药。正向爆破则不行,一旦药卷装不到眼底,就难以处理,不能 退回来,爆破时有可能发生“打枪”现象。
从炸药发挥能量与威力看,反向爆破更加合理。这是因为岩石的抵抗是沿着 炮眼的纵深方向从眼底到眼口逐渐增大,炮眼越长,眼底岩石的抵抗与夹制作用 也越大,而炸药的能量和威力在爆轰过程中则是沿爆轰的传播方向逐渐衰减,这 种现象对于低威力炸药表现得更为明显。很多实验证明,反向爆破比正向爆破时 炮眼利用率可提高5%~20%。
从安全性方面看,反向爆破时,爆炸冲击波、火焰、高温的爆生气体是直接 从炮眼里喷出;正向爆破时,爆炸冲击波、火焰、高温的爆生气体是首先冲向眼 底,折回后才从炮眼喷出。对正向起爆和反向起爆的安全性问题一直存在争论, 有许多研究资料证明,反向爆破比正向爆破安全,如德国、法国和波兰等国家规 定,采用毫秒爆破时,一般规定应采取反向爆破,中国对煤矿爆破事故的统计表 明,反向起爆事故占比较高。
正向装药和反向装药示意图如图3-54所示。
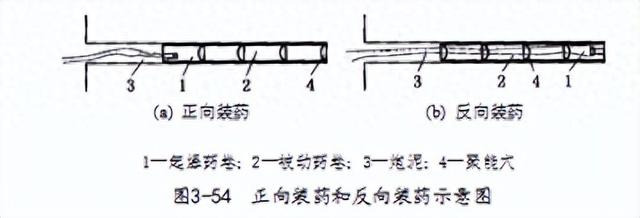
因此,在高瓦斯矿井的采掘工作面采用毫秒延期爆破,若采用反向起爆,必 须制定安全措施。安全技术措施应包括以下内容:
(1)严格执行“一炮三检”制度和“三人连锁爆破”制度。
(2)毫秒雷管不准跳段使用,相邻两段的间隔时间不得大于50 ms。
(3)严格执行炮眼封泥的规定。
(4)炮眼布置方式、炮眼深度、装药量、起爆顺序,必须严格按爆破说明 书进行施工。
(5)煤矿许用毫秒雷管在出库前,必须事先进行导通试验,并逐个测定电 阻,排除断路、短路、电阻特大或特小的电雷管,使同一网路的电雷管电阻差不 得超过0.25~0.3Q。
(6)爆破前,爆破工必须做电爆网路全电阻检查。
第三百五十三条 在高瓦斯、突出矿井的采掘工作面实体煤中,为增加煤体 裂隙、松动煤体而进行的10m 以上的深孔预裂控制爆破,可以使用二级煤矿许 用炸药,并制定安全措施。
【解读】本条是对在高瓦斯、突出矿井进行深孔预裂爆破的规定。
从煤矿爆破安全角度出发,针对防止突出、瓦斯治理,广泛应用并推广深孔 预裂爆破、深孔松动爆破技术等。
深孔预裂爆破技术:它的主要特点是通过控制孔径、孔间距、线装药密度和 堵塞长度使相邻炮孔之间形成裂缝,并通过爆生气体的气楔作用,使初始裂隙和 原生裂隙扩展、张开,最后形成包括压缩粉碎圈、径向裂隙和横向裂隙及次生裂 隙圈在内的立体连通裂隙网。由于预裂爆破作用范围大、工艺简单,在煤矿井下 所有需要裂隙的情况下都可以应用。经过多年攻关,深孔预裂爆破在提高低透气 性煤层的瓦斯抽放率、坚硬顶煤的可放性以及顶板管理方面已经成为成熟的实用 技术。
深孔松动爆破技术作为治理瓦斯的一种手段比较广泛地起到了防治突出的作 用。深孔控制卸压爆破的局部防突措施的实质,是在掘进工作面前方煤体中,打 若干个长钻孔,其中有爆破孔和控制孔,由于控制孔的控制导向作用,所以深孔 控制卸压爆破的结果是在介质内部的炮孔周围产生一柱状的压缩粉碎圈和一沿爆 破孔与控制孔连心线方向的贯穿爆破裂缝面,使集中地应力转移,加速排放高压 瓦斯,降低了瓦斯压力梯度,减少了突出势能,实现了空间上、时间上的超前防 护作用,从而达到防治突出的目的。
由于我国煤矿许用炸药的整体技术水平限制,三级煤矿许用炸药作功能力相 对较小,10m 以上的深孔预裂控制爆破若采用三级煤矿许用炸药很难达到预期 的爆破效果。由于二级煤矿许用炸药同时具有足够的安全性能和作功能力的双重 优点,本条规定10m 以上的深孔预裂控制爆破在采取安全措施的前提下,可以使用煤矿二级许用炸药。
目前我国已有企业研制出水胶炸药瓦斯抽排专用药柱,其主要成分为高威力 三级煤矿许用水胶炸药,安全等级达到三级,其作功能力远远超过普通煤矿许用 三级炸药。建议在深孔爆破时,优先采用水胶炸药瓦斯抽排专用药柱。
若使用二级煤矿许用炸药进行深孔预裂爆破,应采用以下安全措施:
(1)制定科学严谨的爆破方案。
(2)为防止产生爆燃,必须选用含水型的煤矿许用二级炸药,必须严格控 制单孔装药量。
(3)煤矿许用毫秒雷管在出库前,必须事先进行导通试验,并逐个测定电阻。
(4)炮眼布置方式、炮眼深度、装药量、起爆顺序,必须严格按爆破说明 书进行施工。
(5)由于炮孔内有煤渣,同时又受地应力的影响,在炮孔钻杆拔出时,用 探孔管对炮孔进行探孔,并记录炮孔的深度后,确定装药的数量与长度。为了保 证细长药卷间隔装药和连续装药起爆的可靠性,必须在炮孔内沿孔全长敷设煤矿 许用导爆索。
(6)炮眼封泥炮孔封孔长度不低于孔深的1/3。
(7)爆破前,爆破工必须做电爆网路全电阻检查。
(8)炸药严格执行“一炮三检”制度和“三人连锁爆破”制度。
(9)为了防止延期突出,爆破后至少等20 min方可进入工作面,一般在预 裂爆破后,工作面停止作业4~8 h。撤人和爆破距离根据突出危险程度确定,不 得小于200 m, 撤出人员应处于新鲜风流中。
(10)必须有撤人、停电、警戒、远距离爆破、反向风门等安全防护措施。
(11)爆破后应对爆破效果进行检验,并依此调整其爆破参数和布孔方式。 煤矿许用导爆索的结构如图3-55所示。
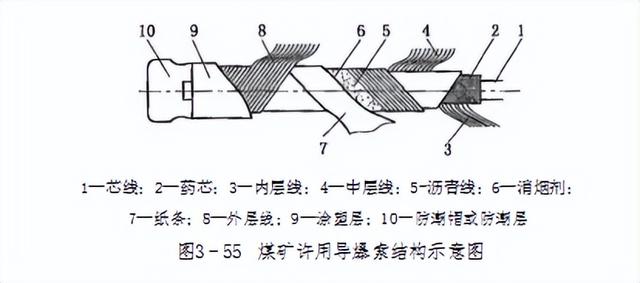
第三百五十四条 爆破工必须把炸药、电雷管分开存放在专用的爆炸物品箱 内,并加锁,严禁乱扔、乱放。爆炸物品箱必须放在顶板完好、支护完整,避开有 机械、电气设备的地点。爆破时必须把爆炸物品箱放置在警戒线以外的安全地点。
【解读】本条是关于在采掘工作面存放爆炸物品的规定。
把雷管与炸药放在一起,雷管爆炸后,可能引起炸药爆炸,使爆炸事故扩 大。
由于井下作业环境复杂及人员较多,为防止踩踏发生意外爆炸,或发生雷管 丢失,造成公共安全事故,爆炸物品箱应加锁并由专业的爆破工负责。
爆炸物品箱若放在顶板、支护不完好的地点,或没有避开机械、电气设备的 地点,一是冒落的石块撞击爆炸物品会引起爆炸;二是距离机械电气设备过近, 漏电和杂散电流有可能引起雷管意外爆炸。另外爆炸物品箱特别是存放雷管的爆 炸物品箱,还要避开通信基站,以免射频电引起雷管意外爆炸。
正常爆破时,在炸药起爆后会形成爆炸冲击波,并且会夹带飞石;同时有时电雷管
还会因爆炸物品本身的问题或装药质量等问题出现爆 燃、喷出灼热颗粒等异常情况,如果将爆炸物品箱放 在警戒线以内,即小于避炮安全距离,就有可能受爆 炸冲击波的冲击,被爆破飞出的碎石击中而发生意外爆炸。
第三百五十五条 从成束的电雷管中抽取单个电 雷管时,不得手拉脚线硬拽管体,也不得手拉管体硬 拽脚线,应当将成束的电雷管顺好,拉住前端脚线将 电雷管抽出。抽出单个电雷管后,必须将其脚线扭结 成短路。
【解读】本条是关于从成束的电雷管中抽取单个电 雷管的操作规定。
我国目前生产的煤矿许用电雷管,其结构是借助 一段材质为聚乙烯的塑料封口塞将引火元件(由脚线、 桥丝、药头组成)和装了药的基础雷管连接起来,如 图3-56所示,电雷管引火元件与装了起爆药的管体 接在一起。这种固接方式能承受的拉力有限,如果抓住管体硬拽脚线或是抓住脚线硬拽管体,都很容易造成封口塞松动,两根脚线错 位,致使桥丝崩断,或引火药头脱落,最终导致雷管拒爆,更为严重的是起爆药 和引火药头都是摩擦感度很高的物质,一旦拉动引火元件,容易造成这些敏感的 药剂和管体内壁的强烈摩擦而发火,雷管在手中爆炸,造成人身伤亡事故。因 此,在有关雷管的操作中,都要禁止硬拽脚线和管体。
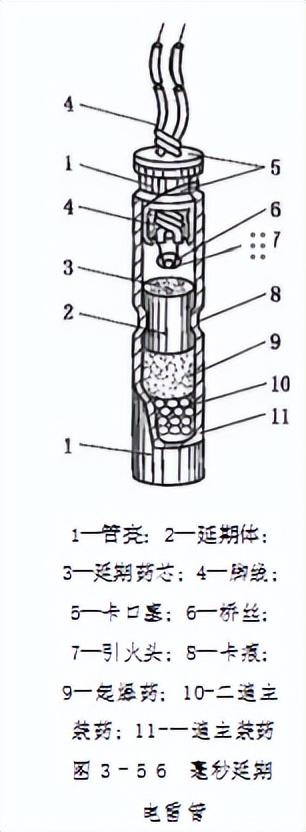
从成束的电雷管中抽取单个雷管,正确的做法是:把整束的雷管脚线顺好, 若无其他有效工具,应用脚轻轻踩住脚线末端,拉住管体前端脚线,缓缓用力将 其抽出。抽出单个雷管后,将其脚线扭结成短路,防止脚线接触导电体或杂散电 而被意外引爆。
第三百五十六条 装配起爆药卷时,必须遵守下列规定
(一)必须在顶板完好、支护完整、避开电气设备和导电体的爆破工作地点 附近进行。严禁坐在爆炸物品箱上装配起爆药卷。装配起爆药卷数量,以当时爆 破作业需要的数量为限。
(二)装配起爆药卷必须防止电雷管受震动、冲击,折断电雷管脚线和损坏 脚线绝缘层。
(三)电雷管必须由药卷的顶部装入,严禁用电雷管代替竹、木棍扎眼。 电雷管必须全部插入药卷内。严禁将电雷管斜插在药卷的中部或者捆在药卷上。
(四)电雷管插入药卷后,必须用脚线将药卷缠住,并将电雷管脚线扭结成 短路。
【解读】本条是对装配起爆药卷的有关规定。
装配起爆药卷的地点必须在顶板完好、支架完整处,以防止局部冒顶或落石 撞击起爆药卷,同时也要避开电气设备和导电体,以防止电气设备失爆、漏电以 及杂散电源通过导电体与起爆药卷接触,引发爆炸事故。在装配过程中不与潮湿 的煤岩壁或导电体接触,以防漏电或杂散电流引爆电雷管。
装配时,严禁坐在爆炸物品箱上,如果爆炸物品箱不结实,轻则造成药卷变 形,包装破损,导致产品不能使用,严重的可能会发生爆炸。因为起爆药已装配 雷管,危险性大大增加。装配起爆药卷数量,用多少就装配多少,以当时需要的 数量为限,不可多装。
电雷管必须从药卷的顶部(平头)装入,否则使雷管和起爆药卷的爆炸能 量不能全部向被动药卷传递,导致下一个药卷拒爆或爆燃。
煤矿许用电雷管是起爆药卷中最敏感的部分,装配起爆药卷时必须防止电雷 管受震动、冲击而引起意外爆炸。同时要保护好雷管的脚线和绝缘层,避免操作 的过程折断电雷管脚线和损坏脚线绝缘层,否则会导致爆破网路漏电,发生丢漏 炮现象。
装配起爆药包宜采用的方法:将电雷管脚线扭结成短路,用炮锥在药卷平头 一端扎一个比雷管略长的小孔,将雷管正向全部置于小孔内,然后用雷管脚线在 药卷上缠绕固定,以免雷管从药卷中松脱出来。
第三百五十七条 装药前,必须首先清除炮眼内的煤粉或者岩粉,再用木质 或者竹质炮棍将药卷轻轻推入,不得冲撞或者捣实。炮眼内的各药卷必须彼此密 接。
有水的炮眼,应当使用抗水型炸药。
装药后,必须把电雷管脚线悬空,严禁电雷管脚线、爆破母线与机械电气设 备等导电体相接触。
【解读】本条是对装药过程中操作方法的有关规定。
装药前,炮眼内的煤粉或岩粉必须清除掉。炮眼内存有煤岩粉,一是会造成 药卷之间连接不实,药卷之间不能正常殉爆,或者发生爆燃,进而引起瓦斯、煤 尘爆炸事故;二是煤粉是可燃物,极易被爆炸火焰燃烧,喷出孔外,有点燃瓦 斯、煤尘的危险;三是若煤粉参与炸药的爆炸反应,就会改变原有炸药的氧平 衡,使爆生气体中的有毒气体含量增高,影响人身健康。
装药时,若用炮棍冲撞或捣实药卷,一是会使药卷变形、膨胀,一旦把药卷 的包装捣破,影响炸药的爆破性能;二是改变装药密度,严重的可能导致半爆、 拒爆;三是用炮棍捣实药卷,有可能捣破电雷管的脚线包皮或捣断脚线,采用正 向装药时,起爆雷管是在最外一卷炸药内,如用力捣炸药卷就可能捣爆雷管,因 此装药时要用木质或竹质炮棍将药卷轻轻推入,不得冲撞或捣实。
有水的炮眼,应使用抗水型炸药。煤矿许用水胶炸药和煤矿许用乳化炸药呈 凝胶状,抗水性能强,一般在水中浸泡24h 不影响爆被性能,使用方便简单。
由于井下电机车牵引网路引起的杂散电流和电气照明设备、采掘机械设备等 漏电引起的杂散电流,都可以通过沿井巷的导体(如管路和轨道)形成电路。 杂散电流与潮湿的煤、岩壁接触,可使煤、岩壁导电。漏电电源一相与另一漏电 电源一相,经爆破母线或脚线与之接触,就可能发生意外爆炸事故,造成人员伤亡。因此,在装药后,必须把雷管脚线扭成短路并悬空,严禁雷管脚线、爆破母 线与机械电气设备等导体接触,以防发生爆炸事故。
杂散电流对爆炸物品贮存、运输和使用过程具有较大危害,当杂散电流超过 电雷管最小准爆电流时,可能引起电雷管爆炸。所以,在工作场所及附近,要定 期检测杂散电流,其值一般不应超过50 mA,同时,要掌握工作场所杂散电流分 布规律,并采取针对性措施,防止杂散电流产生,消除其危害。另外还应防止静 电的产生,将有可能产生静电的设备、器材接地,使其产生的静电向大地泄漏, 不至于积聚;加强洒水防尘、增加空气湿度,使静电难以产生;爆破工及接触爆 炸物品的有关人员,必须穿纯棉布或抗静电服,以避免人体产生静电和积聚静电。
第三百五十八条 炮眼封泥必须使用水炮泥,水炮泥外剩余的炮眼部分应当 用黏土炮泥或者用不燃性、可塑性松散材料制成的炮泥封实。严禁用煤粉、块状 材料或者其他可燃性材料作炮眼封泥。
无封泥、封泥不足或者不实的炮眼,严禁爆破。 严禁裸露爆破。
【解读】本条是对炮泥和装填炮泥的有关规定。
用来封闭炮眼的材料统称为炮泥。炮泥的作用主要有:
(1)保证炸药反应充分,使之放出最大热量并减少有毒气体生成量;
(2)降低爆炸气体逸出自由面的温度和压力,提高炸药的热效率,使更多 的热能转化为机械功;
(3)在有瓦斯的工作面,炮泥不但降低了爆生气体逸出自由面的温度和压 力,还起着阻止灼热固体颗粒从炮眼内飞出的作用;
(4)炮泥影响爆炸应力波的参数,从而影响岩石的破碎过程和炸药能量的有效利用。
使用炮泥的目的是防止爆炸产生的高温、高压气态产物从炮眼口逸出,从而 使药包的后爆炸药爆炸分解得更安全,提高整个柱状药包的爆炸有用功,提高爆 破效果;同时起到阻止爆炸火焰喷出的作用,以免火焰直接与井下沼气、煤尘接 触,诱使沼气、煤尘爆炸;还有降低爆破后产生粉尘的作用。虽然固体炮泥能起 到充分发挥炸药能量的作用,但是不能减少由于爆炸产生粉尘的危害及有害气体 的影响,而且当炮泥长度不够时,爆炸时仍会有火焰喷射,容易引燃瓦斯、煤 尘,如果炮泥充填过长、捣得过实时,常常容易出现拒爆、残爆现象。固体炮泥的堵塞作用,主要取决于炮泥本身质量的大小及炮泥与孔壁的摩擦情况。
水炮泥属于不可压缩材料,与孔壁的摩擦远不如固体炮泥。水炮泥与固体炮 泥结合使用,可以解决单用固体炮泥存在的问题。炸药爆炸后,水炮泥的水由于 爆生气体的冲击作用形成水雾,起到了降低爆温、缩短爆炸火焰延续时间的作 用,从而降低了引爆瓦斯、煤尘的可能性。水炮泥形成的水幕,有降尘和吸收爆 炸气体中有害气体的作用。若在水炮泥中加上适当的辅助剂,将会更好地起到降 尘和减少有毒气体的作用。
对于炮泥材料,在有瓦斯的工作面,必须采用聚乙烯塑料袋装的碱性水炮 泥,同时必须采用声阻抗比水大的其他不燃性材料封堵眼口,一般采用黏土炮 泥。试验表明,采用这种结构的堵塞方式时,装药爆炸,在水炮泥一端激起的冲 击波和从另端反射的冲击波相撞时,可产生很高的阻力,减缓水炮泥的运动。
裸露爆破就是把炸药放在被爆破的煤、岩块的表面上,用黄泥等把炸药盖上 进行爆破,又叫放糊炮。由于放糊炮是在煤和岩石表面上爆炸,爆炸火焰直接与 井下空气相接触,最容易引起瓦斯、煤尘燃烧或爆炸;同时由于放糊炮的爆破方 向和爆破能量难以控制,往往带来其他不安全因素,例如放糊炮容易崩倒和崩坏 支架,造成冒顶,容易崩坏机电设备,造成生产事故。另外,裸露爆破还会在空 气中引起强烈震动,容易把顶帮的浮石崩松或崩落,使离层面和围岩裂隙面扩 大;容易把煤尘震起,使煤尘到处飞扬,既不利于工人健康,也容易引起煤尘爆 炸事故。因此,严禁裸露爆破。
【案例】2004年2月8日,某煤矿43下04综放工作面实施裸露爆破引起煤 尘爆炸,死亡2人、受伤16人,直接经济损失29.4万元。