晶圆减薄(Wafer Thinning)是半导体制造中的关键工艺,主要用于将晶圆的厚度从初始的几百微米(如775μm)减薄至几十甚至几微米,以满足先进封装、三维集成(3D IC)、功率器件、MEMS(微机电系统)等应用的需求。以下是晶圆减薄工艺的详细介绍:
一、晶圆减薄的必要性封装需求:薄晶圆更易于堆叠(如3D封装),提升集成密度。器件性能:减薄可降低电阻和寄生电容,提高器件速度(如功率器件)。散热优化:薄晶圆改善热传导,适用于高功率器件。机械柔性:超薄晶圆可用于柔性电子(如可穿戴设备)。二、晶圆减薄工艺步骤背面研磨(Backside Grinding)粗磨(Rough Grinding):使用金刚石砂轮快速去除大部分材料,将晶圆厚度降至约100-200μm。精磨(Fine Grinding):用更细的砂轮抛光表面,减少损伤层,厚度可降至20-50μm。缺点:机械应力可能导致微裂纹或晶圆翘曲。化学机械抛光(CMP, Chemical Mechanical Polishing)结合化学腐蚀和机械研磨,消除研磨后的表面损伤,提升表面平整度。用于高端器件(如CMOS图像传感器),但成本较高。湿法蚀刻(Wet Etching)通过酸性溶液(如HF/HNO₃)腐蚀晶圆背面,进一步减薄并消除应力。优点:均匀性好,无机械应力;缺点:需控制蚀刻速率和选择性。等离子体蚀刻(Dry Etching)使用等离子体(如SF₆、Cl₂)进行各向异性刻蚀,适用于超薄减薄(<10μm)。常用于化合物半导体(如GaN、SiC)。临时键合与解键合(Temporary Bonding/De-bonding)临时键合:将晶圆正面粘附到刚性载体(如玻璃)上,防止超薄晶圆破裂。解键合:减薄后通过激光、热滑移或化学法分离晶圆与载体。关键技术:粘合剂选择(如紫外固化胶)、应力控制。三、减薄技术分类技术
原理
优点
缺点
适用场景
机械研磨
砂轮物理磨削
效率高、成本低
表面损伤、应力残留
常规减薄(50μm以上)
化学机械抛光(CMP)
化学腐蚀+机械抛光
表面质量高
成本高、速度慢
高端器件、超薄晶圆
湿法蚀刻
化学溶液腐蚀
无应力、均匀性好
环保风险、需掩膜保护
特定材料(如硅基)
干法蚀刻(等离子)
等离子体刻蚀
精度高、各向异性
设备复杂、成本高
化合物半导体(GaN、SiC)
临时键合技术
载体支撑减薄
防止超薄晶圆破裂
工艺复杂、解键合风险
3D封装、超薄晶圆(<50μm)
四、技术挑战与解决方案晶圆翘曲与碎片原因:减薄后应力不均。解决:优化研磨参数(如转速、压力)、使用临时键合技术。表面损伤原因:机械研磨导致晶格缺陷。解决:CMP抛光或湿法蚀刻去除损伤层。超薄晶圆处理(<50μm)难点:易碎、难以传输。解决:临时键合、自动化搬运系统(如真空吸盘)。热管理减薄后散热路径变短,需优化封装材料(如导热胶、硅通孔TSV)。五、应用领域3D封装与TSV(硅通孔):薄晶圆堆叠实现高密度互连。功率器件(IGBT、MOSFET):减薄降低导通电阻,提升效率。MEMS传感器:超薄结构提升灵敏度(如压力传感器)。柔性电子:薄晶圆转移至柔性基底(如PI薄膜)。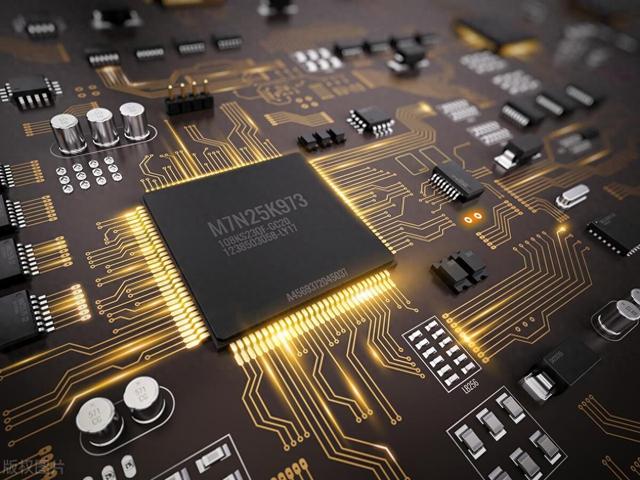
晶圆减薄是半导体制造中连接前道制程与后道封装的核心环节,随着先进封装(如Chiplet、HBM)的兴起,其技术复杂度和重要性将持续提升。
参考文献,见详细文件