
文|大核有料
编辑|大核有料
在核电、船舶、石油管道等制造行业中,加工装配误差导致管管相贯焊接件结构不规则,其连接形成的非理想相贯焊缝都属于偏置斜交类型。
这种空间复杂焊缝焊接强度大,焊接周期长且焊接质量不易保证,尤其是需要多层多道焊接时。
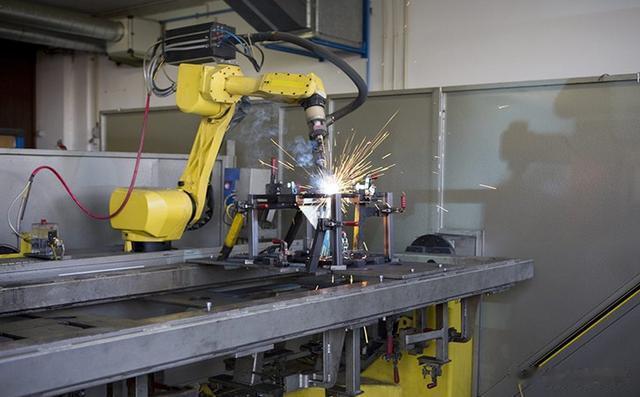
使用机器人进行自动化焊接能够显著提高焊接效率及稳定性,因此开发一种通用的面向相贯焊缝的焊接专机运动控制算法具有重大意义。
在自动焊接过程中根据焊接工艺要求,焊枪除了要求具备平动功能实现位置可达外,还需要对其进行姿态控制来保证接缝的焊接质量,因此焊接专机至少需要4个自由度(x,y,z,α)。
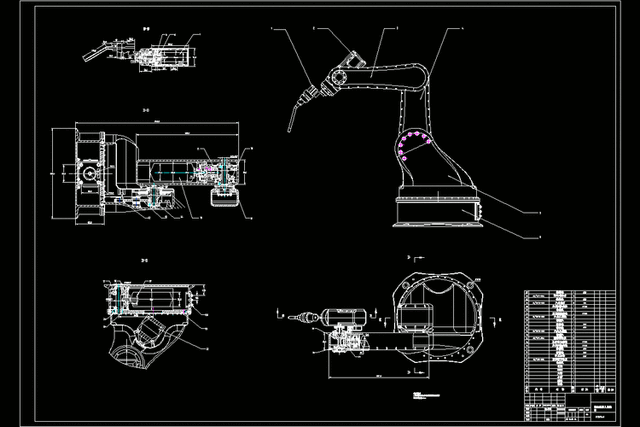
通过相贯焊缝伺服控制系统对焊枪位姿联合控制才能够满足自动化焊接工艺及运动要求,目前针对相贯焊缝的焊接专机伺服运动控制技术的研究较少,很多设备采用通用开关量控制卡控制电机运动,开放性程度低,拓展性较差。
考虑到工程实际应用需求,根据文中设计的管外锚固四自由度焊接专机,建立了通用的管管偏置斜交相贯焊缝数学模型,提出一种连续控制焊枪位置参数及姿态调整值的计算方法。
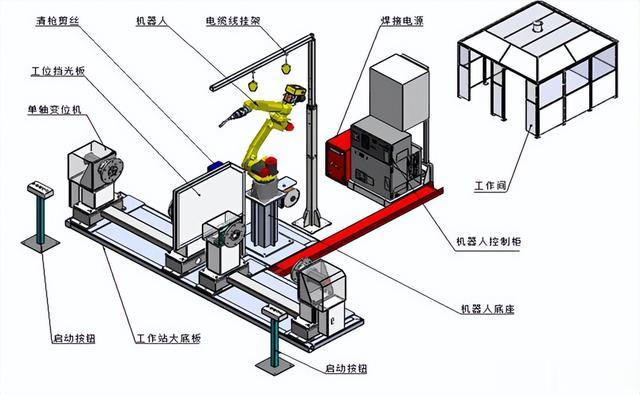
最后采用工控机和运动控制卡构成电机驱动控制系统,这种基于软硬件结合的焊接运动控制算法,具有较大的通用性,能显著提高相贯焊缝的焊接质量、效率及稳定性,可满足工程中自动化焊接需求。
«——【·管外锚固机器人结构及工作原理·】——»
管外锚固式焊接机器人结构三维模型如图1所示,其工作原理如图2所示。
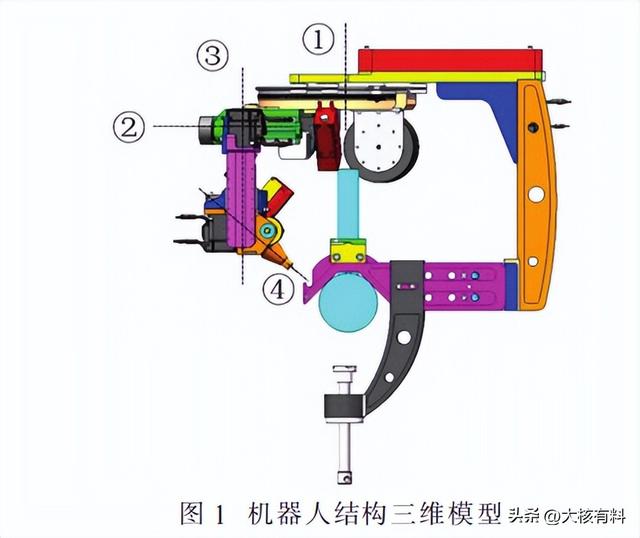
它共有4个自由度:
①号轴为腰部旋转轴,回转机构安装在环形导轨上,带动其余各轴绕其中心旋转,完成相贯焊缝的整周回转;
②号轴为径向移动轴,实现相贯焊缝高度补偿;
③号轴为支管轴向移动轴,完成相贯焊缝轴向进给,三轴联动可保证机器人位置可达;
④号轴为焊枪姿态调整轴,可按照工艺要求调整焊接工作角,焊枪摆动机构采用涡轮蜗杆螺旋式传动结构,传动更为平稳、振动小、噪音低,可提高焊枪摆动的定位精度。
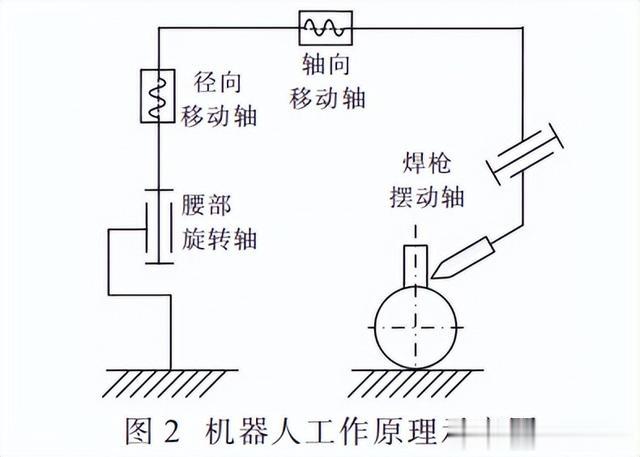
«——【·偏置斜交相贯焊缝数学模型·】——»
母管支管相贯形式有正交、斜交、偏置正交及偏置斜交四种情况。偏置斜交指两圆管的轴线互为异面直线,异面直线间的距离为偏心距,夹角为相贯角,这两参数相当于在描述机器人连杆间关系时所用到的连杆偏距和连杆扭角。
为不失一般性,根据工件实际情况建立了如图3所示的通用焊缝模型。
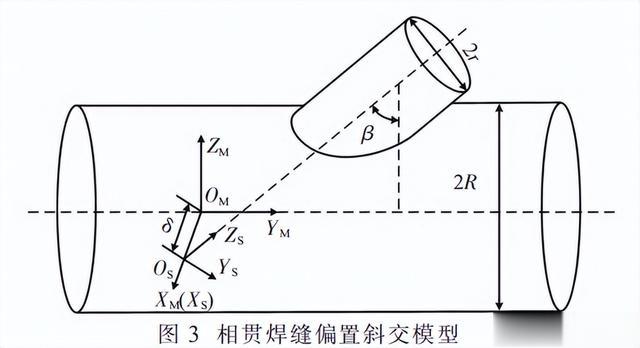
母管半径为R,支管半径为r,在公垂线与轴线的交点处分别建立母管坐标系{M}和支管坐标系{S},分别用OM-XMYMZM和OS-XSYSZS表示。
ZM轴沿母管轴线与支管相贯方向一致,ZS轴沿支管轴线以远离母管方向为正方向,XM轴沿公垂线指向OM方向,XS轴与XM轴保持同向,YM和YS轴可根据右手法则选取。
设公垂线长度为即偏心距,ZM轴和ZS轴的夹角为相贯角,用β表示。
在坐标系OM-XMYMZM和OS-XSYSZS中,两圆管曲面的方程分别为:

坐标系XSOSZS绕XM轴旋转负β角度,沿XM轴正方向移动δ个单位距离得到坐标系OS-XSYSZS,所以两坐标系的转换关系可表示为:

由式(2)可得:
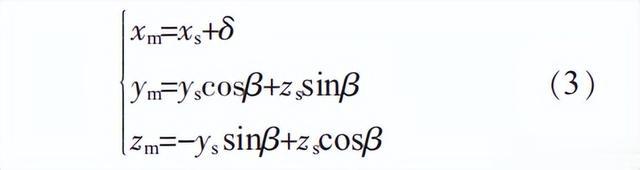
联立式(1)和式(3)可得:

由式(4)描述的焊缝方程难以直接描述每个变量的变化情况,因此将上式转化为以支管旋转变量为参数的函数。
θ的几何意义为t时刻支管轴线剖切面绕Z轴逆时针旋转相对于XSOSZS平面的夹角,其取值范围为[0,2π]。
则支管柱面在坐标系OS-XSYSZS与OM-XMYMZM坐标系中的相贯焊缝曲线方程可分别表示为:
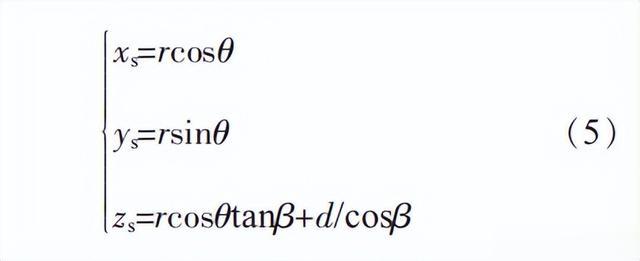
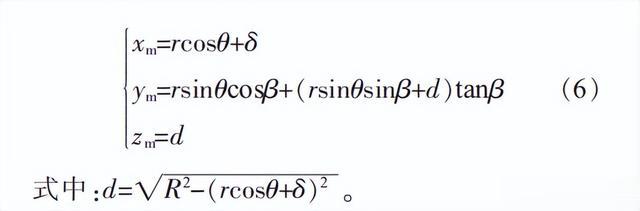
«——【·焊接运动控制算法·】——»
在工程应用中,由于工件具有不一致性,无法通过获取精确3D模型对标准路径进行离散,因此需要采用关键点示教+轨迹拟合来实现机器人连续焊接任务。
示教点的数量,决定了运动轨迹的精度和机器人的工作效率。示教点越多,精度越高,但效率越低。
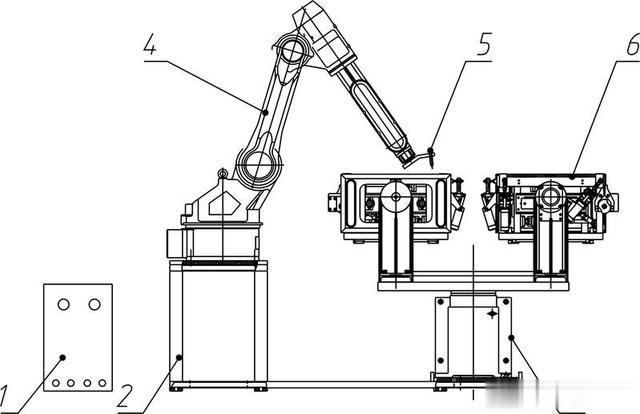
焊枪位置插补:本文给出了一种利用相贯焊缝上三点确定相贯曲线轨迹的焊枪位置连续插补算法。
采用该方法仅需示教机器人运动轨迹上的三个目标点,在这三个目标点所确定的平面上根据轨迹特征计算出这些目标点之间需要到达的中间位置插补点,通过插补计算,从而实现高精度焊接的运动轨迹。
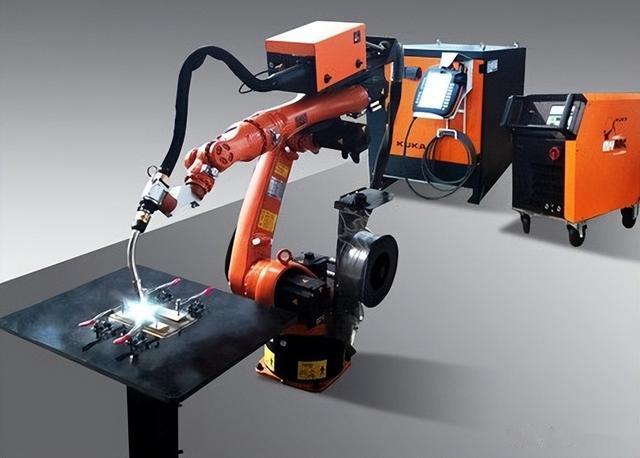
已知相贯焊缝上三个目标点A(xA,yA,zA),B(xB,yB,zB),C(xC,yC,zC)在机器人基坐标系下的值,需要求出目标点所在平面内确定的圆弧半径R,圆心O(x,y,z)以及插补位置递推式。
确定平面上圆弧所在位置根据相贯焊缝上三个目标点可确定平面M上的一圆弧,如图4所示,为了计算插补中间点需要首先确定圆心所在位置及半径。
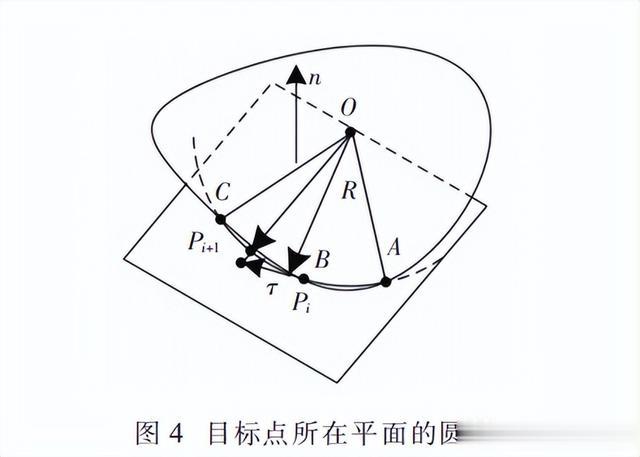
设圆心为O(x,y,z),则根据各目标点到圆心的距离相等可得:
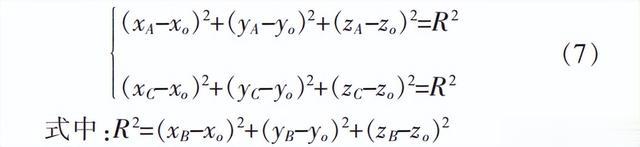
又因为相贯焊缝上三点A,B,C不共线,可得:
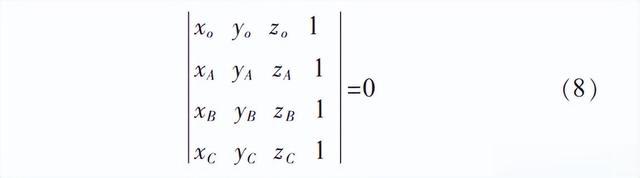
联立式(7)和(8)可求出圆心位置。
计算插补递推式:计算圆弧所在平面的法矢量n(u,v,w)。设n=AB×BC=ui+vj+wk,化简可得:
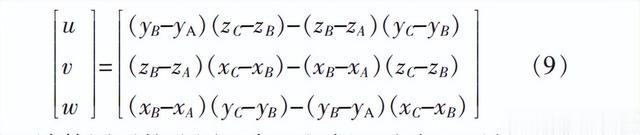
计算圆弧轨迹圆心角。根据正弦定理可得:

化简可得:

计算圆弧轨迹切向量。在所求圆弧上取任意点pi,在该点的切向量为τ,设τ=n×opi=mi+lj+ek,化简可得:
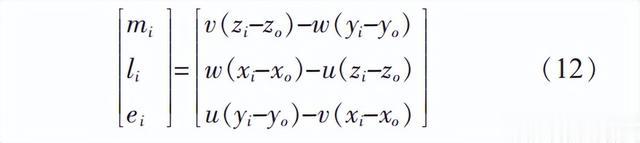
经过一个插补周期后,枪尖位置从点pi沿着圆弧切向到达p'i+1(p'i+1为pi点沿切向量τ方向移动Δs后到达的点),点p'i+1与pi之间位置关系可表示为:
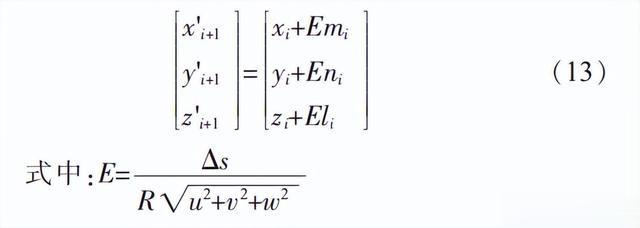
可以发现p'i+1点并没有落在所求圆弧上,误差是ΔR,因此需要对上式进行修正。连接op'i+1交圆弧于点pi+1,在直角三角形opip'i+1中,根据几何关系有R2+ΔS2=(R+ΔR)2,化简后可得:
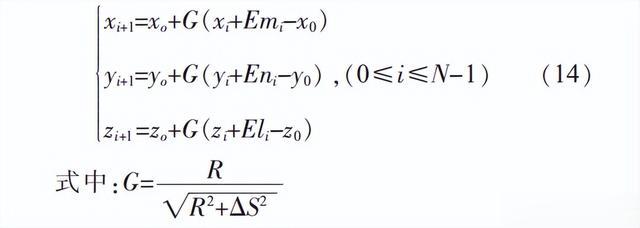
通过式(14)即可求出焊枪运动轨迹上各个目标点的位置。
焊枪姿态调整:在焊接过程中需要焊枪始终处在最佳姿态上,通过主法面二面角法对焊枪姿态进行规划。
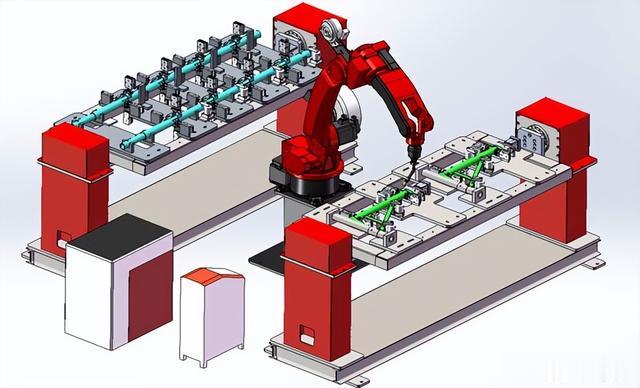
设焊枪末端在点pi处时焊枪工作角为α,其值为二面角的一半,主法面的法向量为相贯线上pi点的切向量,也是焊枪的行走方向。
主法面与母管、支管在该点的切平面各有一条交线,这两条交线的角平分线定义为焊枪轴线的方向,如图5所示。
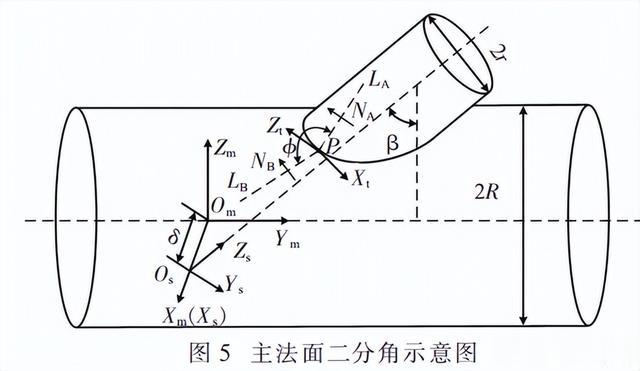
二面角可通过两切平面的法向量求得。
在OM-XMYMZM坐标系中,支管圆柱面的方程为:

其中在点pi处切平面A的法向量NA表示为:

在OM-XMYMZM坐标系中,母管圆柱面方程为:

其中在点pi处切平面B的法向量NB表示为:
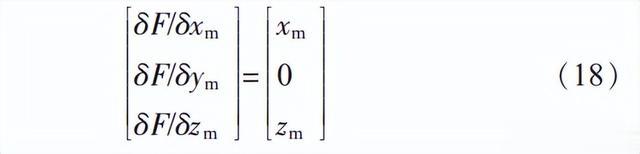
联立式(16)与式(18),将参数θ引入后可得:

以pi为交点的直线LA和LB的夹角就是切平面A和切平面B所形成的二面角,其表达式为:

则焊枪工作角α为:
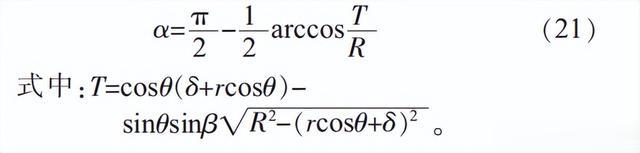
至此,四轴机器人需要的轨迹参数x,y,z,α均已求得。
«——【·伺服运动控制实现·】——»
伺服控制系统是机器人的核心部分,通过控制伺服驱动器来驱动各个关节电机运转,使机器人焊枪工具按照预先规划好的轨迹运动完成焊接工作。
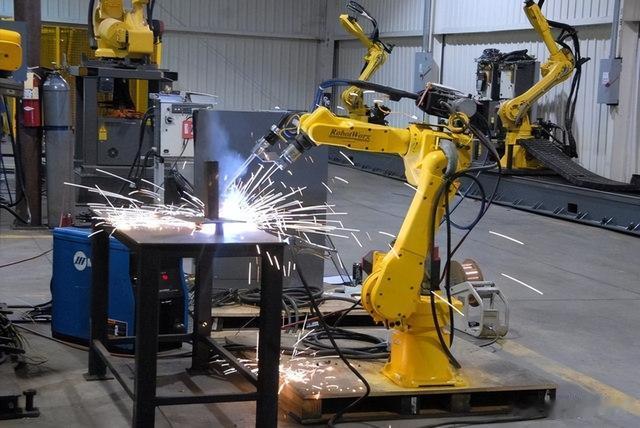
为验证大构件斜交偏置相贯马鞍形焊缝轨迹控制系统的可行性,基于以上介绍的连续焊枪位置参数及姿态调整控制算法,通过建立实验平台进行焊接实验来验证该控制系统的精确性。
控制系统硬件组成:本系统采用分级控制的模式,伺服控制系统如图6所示。
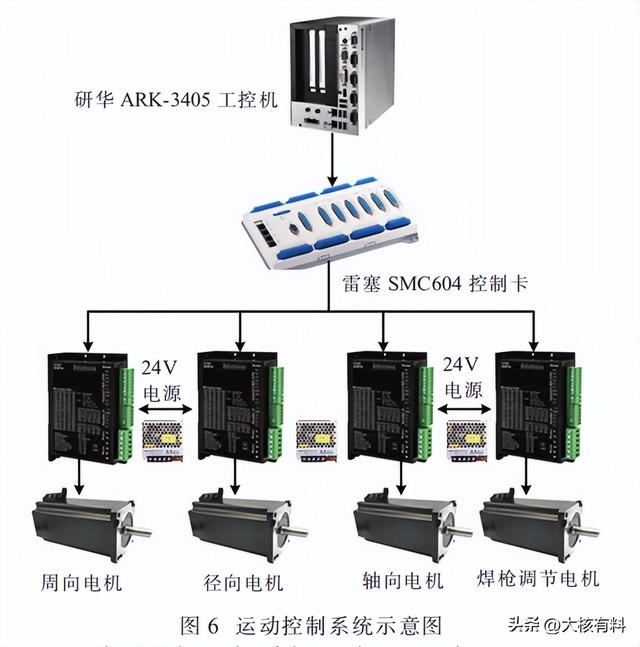
这种基于“工控机+运动控制卡”的开放式控制模式,能够完成对电机的伺服位置控制及I/O逻辑顺序控制,具有拓展性强、可靠性高、信息处理能力强等优点。
工控机选用研华ARK-3405作为上位机,负责人机界面交互、系统参数设置、机器人轨迹规划及工艺参数输入等任务。
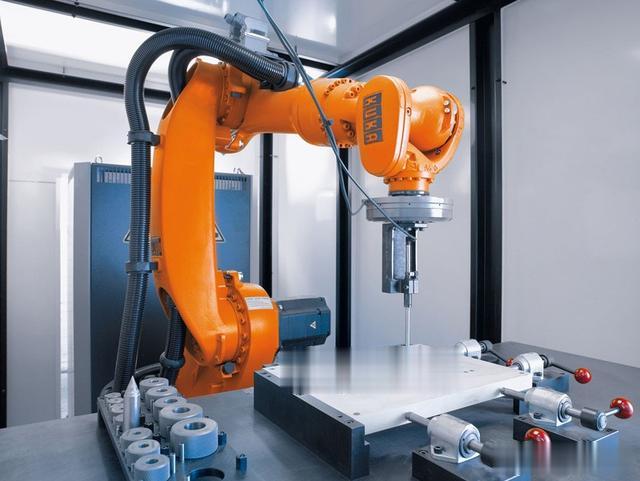
运动控制卡选用雷塞SMC604型号作为下位机,实现四轴电机控制,执行运动控制算法,实现各轴电机的脉冲比例分配,完成焊接任务。
步进电机驱动器给电机提供的信号主要包括步进脉冲数信号及方向电平信号。步进电机的驱动方式采用与其配套的电机驱动器来完成,所有驱动器的供电电源电压均为DC24V直流电。
雷塞SMC604运动控制卡与电机驱动器的连接方式如图7所示。
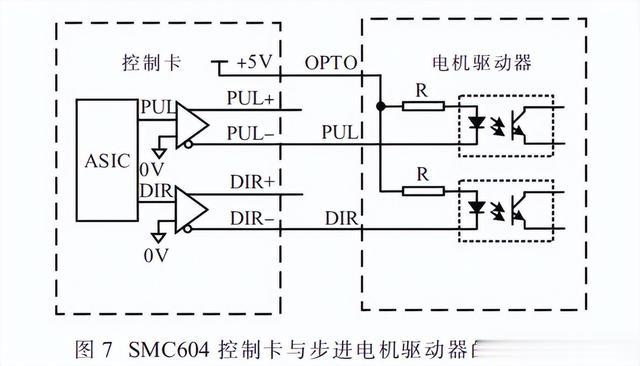
控制系统程序设计:SMC604控制卡提供了动态链接库,用户可选择调用动态链接库提供的API函数来执行相关运动功能。
本文基于VisualC++程序开发软件及SMC604型号运动控制卡的专用运动指令函数对控制系统程序进行设计。
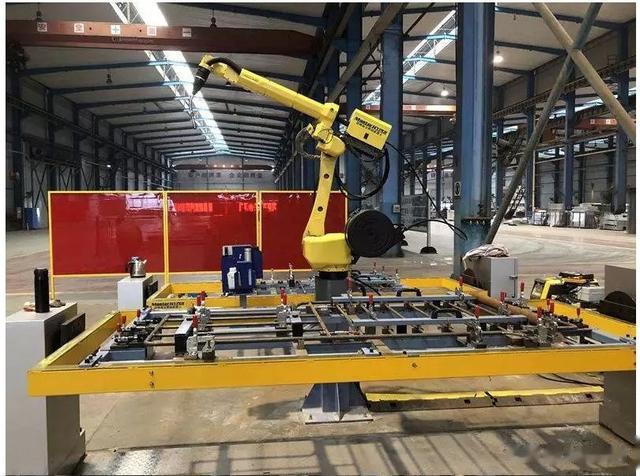
为便于用户与控制系统进行数据交互,利用MFC搭建的界面框架开发了参数交互对话框。
用户可通过示教机器人到达焊缝3个位置或更多,软件会首先根据输入的三点机器人轴坐标调用机器人正运动学算法将其转化成位姿表述,接着通过式(14)与式(21)的运动表达式计算出焊接路径上的其他目标点,其界面如图8所示。
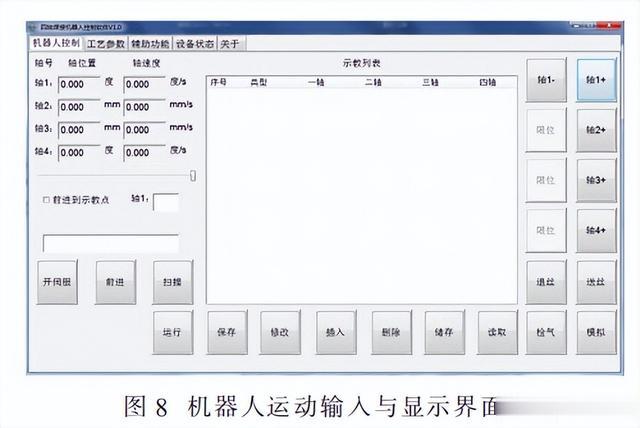
用户可通过点击模拟按钮在不起弧的情况下来验证焊接路径是否正确,在进行焊接任务前需要输入工艺参数,界面如图9所示,用户可手动输入也可通过读取文件来获取。
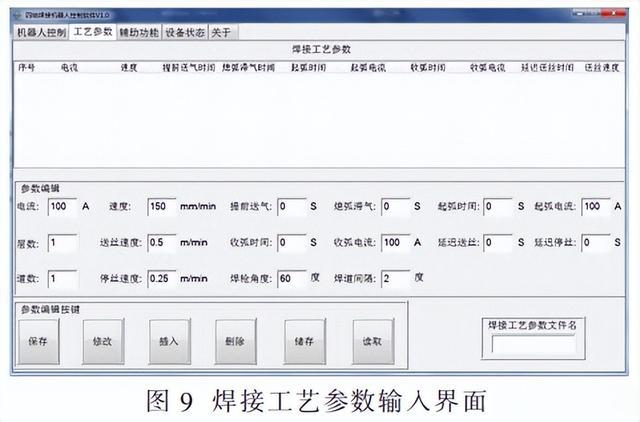
«——【·样机试验·】——»
为了验证上述算法的正确性,制作了如图10所示的样机并进行了实际的管管相贯焊缝焊接试验。
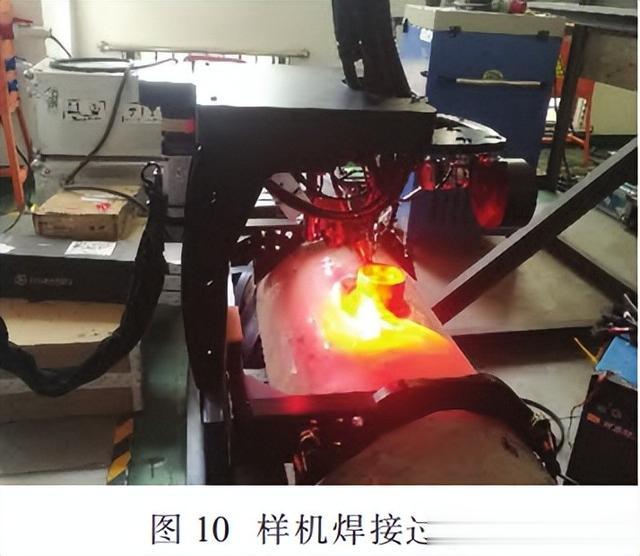
其中主管直径为320mm,支管直径为80mm,两管中心轴线偏置距离10mm,倾斜角度为5°,每道焊缝示教点间隔22.5°,第一层第一道示教数据见表1。
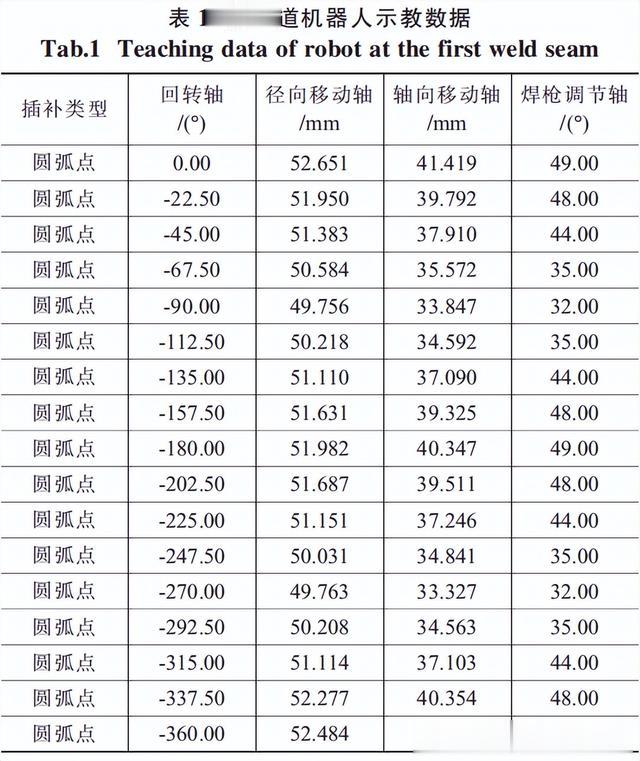
焊接工艺参数见表2。
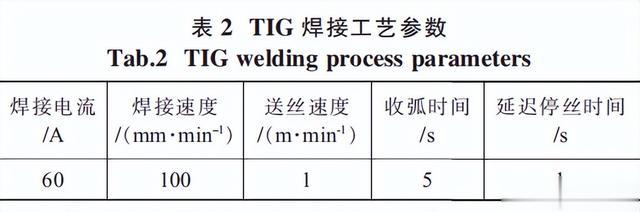
按照第一道焊接方法进行多层多道焊接,焊接完成后的工件如图11所示。
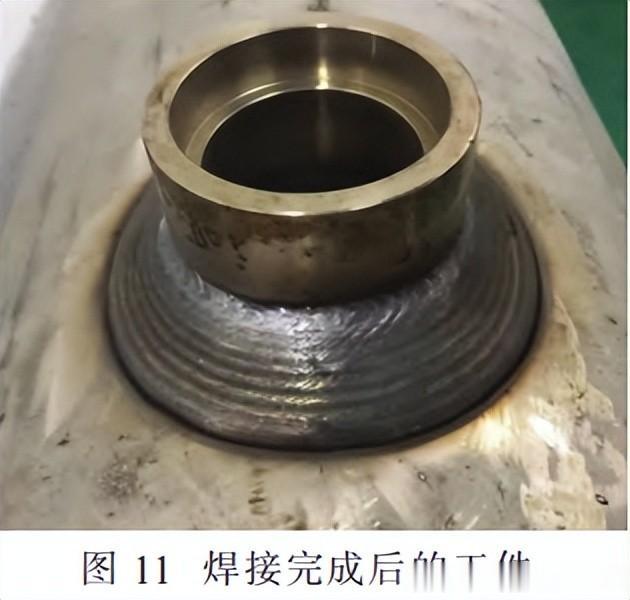
从图11中可以看出焊件成形良好,焊缝致密美观,说明了管管斜交偏置相贯焊缝轨迹运动控制系统稳定可靠,能满足焊接需求。
对于工程应用过程中存在加工及装配偏差的各种相贯件,都可以运用此系统来进行焊接。
«——【·结语·】——»
通过坐标变化构建了大构件偏置斜交相贯焊缝通用数学模型,利用三点分段圆弧拟合焊缝曲线求取了各离散点位置坐标,通过主法面二分角法确定了机器人焊枪姿态调整值。
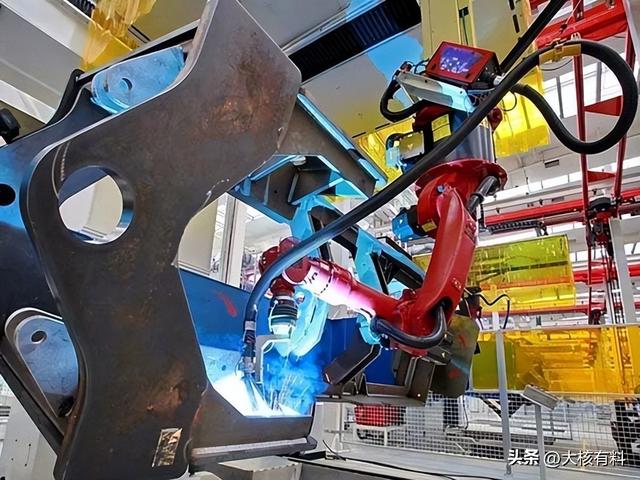
采用工控机+运动控制卡组成伺服控制系统,开发了友好的人机交互界面,通过制作样机搭建实验平台进行相贯焊缝焊接试验。
焊缝致密成形美观,验证了焊枪位姿规划算法的正确性及伺服控制系统的稳定性、可靠性。