PEM电解水制氢高成本一直是其商业化应用的一大障碍。如何给PEM电解水制氢降本,是这一技术商业化应用的关键。近来,PEM电解水制氢设备及供应链在降本上频频探索、频传捷报,一个PEM制氢的时代似乎踏马而来。
PEM电解水制氢降本的关键在PEM电解槽,电解槽降本的核心在双极板和膜电极。双极板企业在降本压力下已普遍采用PVD工艺将铂层厚度低至100nm甚至50nm,同时在积极探索规模化下单板价格更低的冲压工艺技术;膜电极方面,则陆续有企业推出让PEM电解槽 “断崖式”降本的新一代高电密、薄PEM膜电极。另有,还有电解槽企业通过提升电流密度、提升国产化率、优化内部结构等方式来降本。
PEM电解水制氢似乎进入“集体”谋降本时代。在这股浪潮下,业界预计明年行业PEM电解槽的成本将降低到一个新的水平。
PEM电解槽材料降本“进行时”
PEM电解水制氢因为能够适应可再生能源的波动性、响应速度快、产氢纯度高等优势显现出巨大发展潜力,但是,因为初始设备投资成本高(大约是碱水制氢的3-5倍),让它在应用上一直未能打开局面。降本,是这一技术路线推广的关键。
PEM电解水制氢降本主要集中在PEM电解槽。PEM电解槽由双极板、膜电极、短板附件、极框、垫片等组成,以1MWPEM电解槽成本构成为例来看(下图),双极板组件、膜电极又是PEM电解槽降本的核心。近期,市场消息显示,国内双极板组件、膜电极供应商已经集体掀起降本的浪潮,助力PEM制氢的规模化应用。下面以这两个维度为例,展开具体介绍。
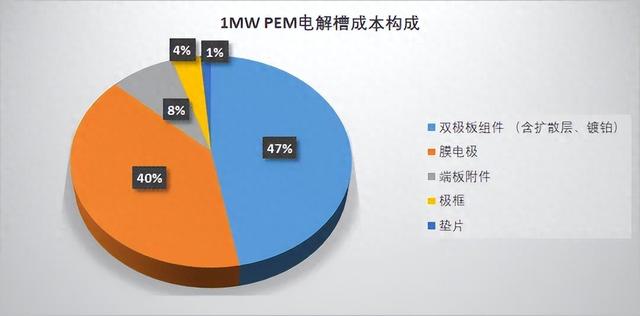
双极板组件方面。双极板组包括双极板和扩散层,两者因为含有较高的铂载量,成为PEM电解槽降本的重头戏。这部分以双极板为代表展开介绍。PEM电解槽双极板一般采用耐腐性更好的钛材,并涂上含铂的涂层。双极板的降本通常是降低双极板涂层的铂载量或寻找非铂涂层。目前,市场多家双极板企业在通过降低涂层的铂载量进行降本,即在保障性能不减弱的情况下,通过减少高价值材料的使用来降本。
比如其中一家开发出低载量铂金属复合涂层,通过采用PVD工艺将铂层厚度低至100nm甚至50nm,这就比电镀铂涂层(500nm)成本可降低一半。
“电镀500 nm铂涂层每平米需要10000元,而且电镀工艺将涂层做不薄,如果在500nm以下,镀膜涂层会不稳定。如果改成PVD镀100nm,每平米就能减到6000元,而且镀层与基材的结合力也不错。“这家企业一位相关负责人告诉高工氢能,并且据透露,目前100nm以上的涂层已经越来越少了。
除此外,从极板生产工艺看,由于蚀刻速度慢、成本高,不利于规模化降本,国内多家双极板供应商已在探索推进冲压工艺规模化量产技术,包括上海治臻、西部材料、博远新能源等。
另外,基于铂涂层在双极板的成本占比最大,(铂目前价格是235元/g,一个250标方电解槽涂层(100nm)价格就要在40万左右),越来越多的企业着手研发非贵金属涂层作为替代材料。这种路线是否走得通目前还没有论证,但如果哪一天真有能够替代贵金属涂层的材料诞生,那么PEM双极板乃至整个PEM电解槽的价格,将发生革命性变化。
膜电极方面。膜电极在PEM电解槽中的成本占比在40%左右,仅次于双极板组件。膜电极降本的方向是薄质子膜、低贵金属载量。今年以来,国内多家PEM膜电极企业推出符合这种特点的新一代膜电极产品,助力PEM电解槽降本。
比如枡水科技推出颠覆性新一代PEM膜电极,该产品采用50微米薄膜膜电极,并配以第四代氧中氢控制技术,让新一代膜电极做到了低成本兼具高性能和稳定性。产品实际测试表现是:电流密度:4A/cm²@1.8V(60度,铱载量1mg/cm²,铂载量0.4mg/cm²);氧中氢:≤0.3%@0.2A/cm² 3MP背压;电流效率:>97%;另外新品的耐久性也在过去的基础上提升了10%,实现有条件1%-150%负载运行。堆叠这款新一代膜电极的测试型PEM电解槽SSTS-4001的成本仅为117.7万/兆瓦。
莒纳科技围绕PEM膜电极降本,推出其量产型PEM制氢膜电极JP系列产品,阴极Pt载量低至0.35mg/cm²,阳极Ir载量低至0.86mg/cm²,降本约20%。另外,针对膜电极中多采用进口质子交换膜、价格高的情形,莒纳科技针对PEM电解水用质子交换膜进行系列测试,根据测试结果,已经有一些国产膜在测试中呈现不错的性能效果,莒纳科技正在加强和这些膜厂家的合作测试和性能改进工作,助力国产质子交换膜国产化替代、PEM电解槽降本。
另外,鸿基创能在去年发布了一款高效全尺寸PEM膜电极,不仅实现了高效能,且已经较市售的膜电极产品贵金属载量从2.5mgPGM/cm²降至1.3mgPGM/cm²,但这依然不是其追求的终点。据鸿基创能PEM电解水项目负责人董准博士透露,今年新一代PEM电解水制氢膜电极已开发设计完成,贵金属载量进一步下降40%,整个膜电极成本下降30%,正在加速验证当中。
明年PEM制氢或迎来价格新水平
除了上述核心材料企业在推动降本,电解槽企业本身也在积极寻找降本空间,包括比如提升电流密度,减少核心材料用量;对各种低载量方案进行测试;提升国产化率;优化内部结构;集成化降本等。
国内最早设计电解槽时,电流密度只能达到1.3 A/cm²,现在PEM电解槽企业的电流密度基本都可达到2-3A/cm²,意味电解槽的成本已经降到一半了。因为同等电压下电流密度提升对应核心材料用量减少,如果电流密度提升一倍,核心材料用量可能减少50%,核心材料成本等于降低一半。
另外,电解槽企业也在通过掺杂非贵金属或者降低贵金属载量等方式降本,比如淳华氢能自主研发了硼化物陶瓷负载氧化铱,有效降低了贵金属的载量,优于学术界的数据;另外其研发的沟槽型膜电极显著强化了气液电传递效率,使得电解反应更加高效;以及独特的Janus气体扩散层有效促进了气泡的快速排离,进一步提高了反应效率和稳定性。淳华氢能在贵金属载量和电流密度这两项关键性能指标上实现创新。
除了上述基于材料的提升来降本外,还有的电解槽在设计结构上进行突破,比如兴燃科技,通过改进机械加工技术,实现更加精确的电极加工与组装。该公司电解槽采用零间距结构,提高组装效率,并保持强密封性,欧姆电阻较低,整体效率从75%提升到86%,极大得降低了电解槽的能耗,进一步降低制氢膜电极的成本。
大型化和集成化也在成部分企业降本的有效路径。10月19日,鹭岛氢发布自主开发的低铱高电流密度单堆500标方PEM电解槽。该产品在额定功率下直流电耗4.4kWh/Nm³,电流密度达3A/cm²,铱载量仅0.4mg/cm²,负荷调节范围5%-130%,适应各种情况下可再生能源波动制氢,此外,新产品采用全新工艺,综合成本较同系列200标方PEM电解槽降幅达30%,各个部件的国产化率超过90%。另外,国产首台兆瓦级PEM电解水制氢设备1000Nm³/hPEM电解槽也已问市,其以集装箱为制氢单元,封装4个单槽进行模块化生产,每个集装箱产氢量为1000Nm³/h。
可以说,整个PEM制氢供应链都在为降本思虑筹划!
基于企业的种种表现和市场竞争的因素,一位PEM电解槽供应链企业表示,“PEM电解水降本远超预期,明年上半年行业内将会陆续看到更多大电流PEM电解水零部件和系统产品,这将会将PEM槽的成本降低到一个新的水平。”