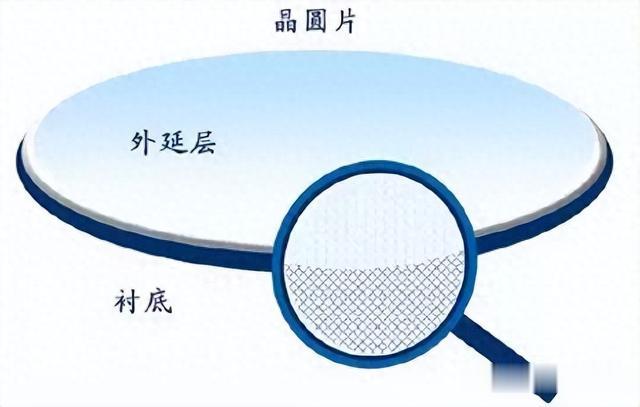
在当今数字化时代,芯片已成为各类电子设备的核心,从智能手机、电脑到汽车、工业控制系统,几乎无处不在。而晶圆制造材料,作为芯片制造的基础,其重要性不言而喻,堪称芯片产业的基石。没有优质的晶圆制造材料,就无法制造出高性能、低功耗、小型化的芯片,整个电子信息产业的发展也将受到严重制约。
晶圆制造材料涵盖了多种关键材料,每种材料在芯片制造过程中都发挥着独特且不可或缺的作用。它们共同协作,支撑着芯片制造这一复杂而精密的过程,从最基础的硅片,到光刻、蚀刻、掺杂等关键工艺中使用的光刻胶、电子特气、湿电子化学品等,每一种材料的性能和质量都直接影响着芯片的最终性能、成品率和成本 。
基础材料:硅片的 “进化之路”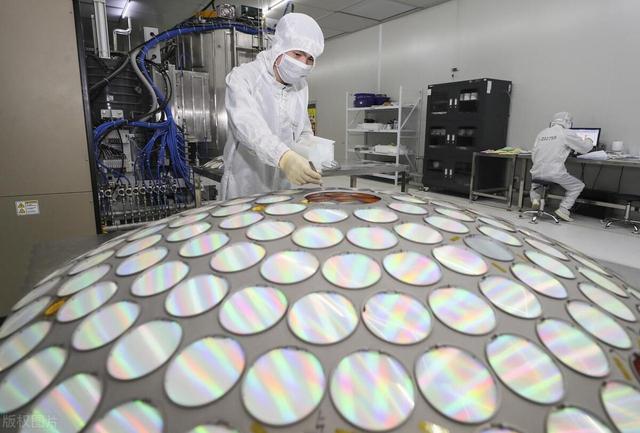
硅片,作为晶圆制造的核心基础材料,其地位举足轻重。从最初的原料提取,到单晶硅生长、晶圆制备等复杂流程,每一步都凝聚着科技的智慧与创新。硅片的主要原材料是石英,也就是我们常见的沙子 ,其提取过程需要经过多道复杂工序,将沙子中的二氧化硅转化为硅金属,再通过化学方法去除杂质,得到高纯度的电子级硅(EGS),电子级硅的平均纯度要求每一百万个硅原子中最多只有一个杂质原子。
获得高纯度的硅材料后,下一步便是单晶硅生长。目前,主要有直拉法(CZ)和区熔法(FZ)两种技术用于单晶硅生长。直拉法由波兰科学家 Czochralski 在 1916 年发明,是目前应用最广泛的方法,半导体工业中超过 90% 的单晶硅都是采用这种方法制备的。在直拉法中,多晶硅被放置到坩埚中,熔炉加热到超过硅的熔点,将一个适当晶向的籽晶放置在籽晶夹具中,悬于坩埚之上,接着将籽晶插入熔融液中,虽然籽晶将会部分熔化,但未熔化的籽晶顶部将会接触熔融液的表面,随后将籽晶慢慢拉起,熔融液在固体 - 液体的表面逐渐冷却,从而产生一个很大的单晶锭,标准的拉晶速率是每分钟数毫米。
区熔法又称悬浮区熔法,该方法不使用坩埚,而是将硅棒局部利用线圈进行熔化,在熔区处设置磁托,因而熔区可以始终处在悬浮状态,将熔硅利用旋转籽晶进行拉制,在熔区下方制备单晶硅。这种方法优势在于,熔区为悬浮态,因而在生长过程中单晶硅不会同任何物质接触,并且蒸发效应以及杂质分凝效应较为显著,因此具有较高的纯度,其单晶硅制品性能相对较好,但由于工艺复杂,对设备以及技术要求较为严格,因此生产成本相对较高。
单晶硅生长完成后,还需进行晶圆制备。首先,将晶锭切除包含籽晶的头部和最后凝固的尾端,接着磨光表面以确定晶圆的直径,然后沿晶锭轴向磨出一个或数个平面,这些平面用来指示晶向和导电类型。随后,晶锭被金刚石刀片切成晶圆,切割决定四个晶圆参数:晶面结晶方向,如<111>或<100>;晶圆厚度,如 0.5 - 0.7mm,由晶圆直径决定;晶面倾斜度,指从晶圆一端到另一端的厚度差异;晶圆弯曲度,指从晶圆中心到晶圆边缘的弯曲程度。切割完成以后,晶圆的两面要用氧化铝(Al2O3)和甘油的混合物来研磨,一般可研磨到 2um 的平坦度,这道研磨操作通常会造成晶圆表面和边缘的损伤和污染,损伤和污染的区域可用化学刻蚀的方法来消除。晶圆成形的最后一道工序是抛光,其目的是为后面的光刻工艺提供具有高度平坦化、高度洁净表面的晶圆。
随着半导体技术的不断发展,硅片的尺寸规格也在不断发展变化。早期,硅片尺寸较小,1960 年代中期,硅片的直径通常是 25 毫米(1 英寸) 。随着技术进步和对更高效生产的需求增加,硅片的尺寸不断增大,现代半导体制造中,通常使用 150 毫米(6 英寸)、200 毫米(8 英寸)以及 300 毫米(12 英寸)的硅片。较大的硅片允许在同一片硅片上制造更多的芯片,意味着更大的硅片可以显著提升产量,并且硅片面积增大后,产量增加,而制造工艺的一些基本步骤(例如光刻和蚀刻)不随硅片尺寸的变化而变化,这样就可以在不增加工艺步骤的情况下提高生产效率,此外,更大的硅片也使得制造成本能够进一步分摊,从而每个芯片的成本也会降低 。目前,行业对更大尺寸硅片的探索仍在继续,450 毫米硅片的研发工作已经开始,并有望在未来实现商用。
工艺材料:“精雕细琢” 的艺术
光刻胶,作为光刻工艺中的关键材料,堪称光与化学的 “魔法” 结晶。它是一种对光敏感的化学材料,在集成电路的制造过程中,用于将设计好的电路图案转移到硅片等半导体材料上。光刻胶的工作原理基于其在特定波长光线照射下发生的化学反应。当光刻胶被涂布在晶圆表面并经过软烤处理后,形成一层具有特定膜厚和表面特性的薄膜。随后,在曝光过程中,光线透过掩模版上的透明区域照射到光刻胶上,光刻胶中的光敏剂吸收光子能量,引发化学反应,使得曝光区域的光刻胶化学结构发生改变,其溶解性也随之改变。经过显影处理后,光刻胶上就形成了与掩模版图案对应的精确图案,实现了电路图案从掩模版到晶圆的精准转移 。
光刻胶的性能对芯片制程精度有着至关重要的影响。其分辨率、灵敏度、对比度等特性直接决定了光刻工艺能够实现的最小线宽和图案精度。随着芯片制程技术不断向更小尺寸发展,对光刻胶的性能要求也越来越高。
光掩膜版:芯片图案的 “模板”光掩膜版,又称光罩,在光刻过程中扮演着芯片图案 “模板” 的角色,如同传统照相机的 “底片” 一般。它是由制造商通过光刻制版工艺将电路图刻制于基板上制作而成,主要作用是利用已设计好的图案,通过透光与非透光方式进行电路图形复制,从而实现芯片的批量生产。
在光刻过程中,光掩膜版承载的电路图案通过光刻机曝光,将图案精确地转移到光刻胶上,然后经过后续的蚀刻步骤,将图案刻蚀到半导体衬底材料(如硅)上,形成所需的微小结构。随着晶体管尺寸的不断缩小,对光掩膜版的精度要求越来越高,其制造也变得越来越复杂。
电子特气:芯片制造的 “隐形助手”电子特气,作为芯片制造的 “隐形助手”,在蚀刻、沉积、掺杂等多个芯片制造环节中发挥着不可或缺的作用。它是电子半导体行业用的特种气体,广泛应用于前端晶圆制造中的化学气相沉积、光刻、刻蚀、掺杂等诸多环节。电子特气的纯度和洁净度直接影响到光电子、微电子元器件的质量、集成度、特定技术指标和成品率,并从根本上制约着电路和器件的精确性和准确性 。
在刻蚀环节,硅片刻蚀气体主要是指氟基气体,包括 CF4、SF6、C2F6、NF3 ,以及氯基 (Cl2) 和溴基 (Br2、HBr) 气体等,它们通过与硅片表面材料发生化学反应,有选择地去除不需要的材料,实现图案的精确复制;在掺杂工艺中,常用的掺杂气体包括砷烷、磷烷、三氟化磷、五氟化磷、三氟化砷、五氟化砷、三氟化硼、乙硼烷等,将这些杂质掺入半导体材料内,可使材料具有所需要的导电类型和一定的电阻率,以制造电阻、PN 结、埋层等;在外延沉积过程中,常用的硅外延气体有 SiH2Cl2、SiCl4 和 SiCl4 等,通过化学气相沉积法,在衬底晶圆上镀上一层薄膜作为缓冲层,阻止有害杂质进入硅衬底 。
湿电子化学品:芯片的 “清洁卫士”湿电子化学品,堪称芯片的 “清洁卫士”,在芯片清洗、蚀刻等湿法工艺中发挥着关键作用。它是微电子、光电子湿法工艺制程中使用的各种液体化工材料,按用途可分为通用化学品(又称超净高纯试剂)和功能性化学品(以光刻胶配套试剂为代表) 。
在芯片制造过程中,湿电子化学品的主要作用是确保芯片制造过程的洁净和精准。例如,在清洗环节,使用超净高纯试剂,如硫酸、双氧水、氨水、氢氟酸、异丙醇等,能够有效去除晶圆表面的颗粒、有机物、金属杂质等污染物,保证晶圆表面的洁净度,为后续的工艺步骤提供良好的基础;在蚀刻工艺中,功能性湿电子化学品,如半导体用显影液、刻蚀液、面板用显影液、剥离液以及缓冲刻蚀液等,能够精确地去除不需要的材料,实现电路图案的转移和精细加工 。湿电子化学品的纯度和洁净度直接影响电子元器件的成品率、电性能和可靠性。
CMP 抛光材料:让晶圆 “光滑如镜”CMP 抛光材料,通过化学和物理作用的协同配合,实现晶圆表面的平坦化,让晶圆 “光滑如镜”,在芯片制造中具有举足轻重的地位。CMP(Chemical Mechanical Polishing)即化学机械抛光,其基本原理是在一定压力下及抛光液的存在下,晶圆与抛光垫做相对运动,借助纳米磨料的机械研磨作用与氧化剂、催化剂等的化学腐蚀作用之间的有机结合,将物质从晶圆表面逐层剥离,从而达到高度平坦化的效果 。
在芯片制造过程中,随着集成电路的不断发展,对晶圆表面平整度的要求越来越高。CMP 抛光材料能够对整个晶圆表面进行全局性的平坦化处理,实现高达纳米级的表面平整度,满足现代集成电路对基片表面要求极高的需求。它不仅用于硅晶圆片的平坦化,还可以处理有机物等低介电常数物质,并且在浅沟槽隔离(STI)、多晶硅平坦化(Poly CMP)、层间介质平坦化(ILD CMP)、金属间介质平坦化(IMD CMP)、铜互连平坦化(Cu CMP)等多个关键工艺环节中发挥重要作用 。
溅射靶材:为芯片 “镀膜”溅射靶材,在芯片镀膜和掺杂工艺中发挥着关键作用,如同为芯片 “镀膜” 的工匠。它是高速荷能粒子轰击的目标材料,在溅射过程中,靶材原子被溅射出来,沉积在晶圆表面,形成一层薄膜,实现芯片的镀膜和掺杂 。
溅射靶材的材料特性和纯度对芯片性能的稳定性和可靠性至关重要。例如,在芯片制造中,常用的溅射靶材有铜靶、铝靶、钛靶等,不同的靶材适用于不同的工艺需求。高纯度的靶材能够减少杂质的引入,保证镀膜的质量和性能。在先进制程的芯片制造中,溅射靶材的尺寸精度、表面平整度等指标都需要严格控制,以确保能够实现高质量的镀膜和掺杂,提高芯片的性能和成品率 。
新型材料:探索无限可能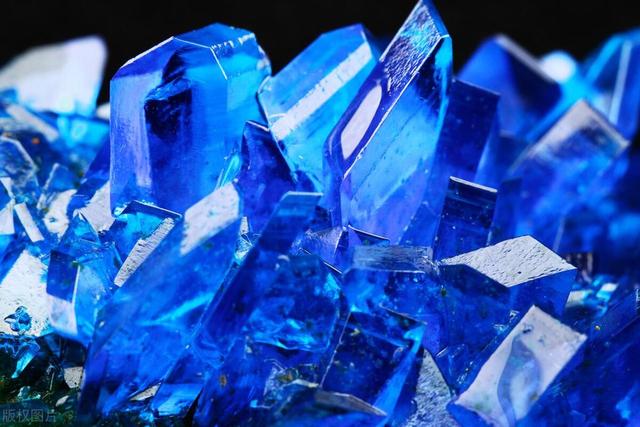
随着电子设备不断小型化和性能要求的提升,芯片中的晶体管数量持续增加,尺寸日益缩小,对介质材料提出了更高要求。传统的介质材料在厚度减小到纳米级别时,绝缘性能会显著下降,导致电流泄漏,这不仅增加了芯片的能耗,还导致发热量上升,影响了设备的稳定性和使用寿命 。
为了解决这一难题,我国科学家经过多年研究攻关,成功研制出一种人造蓝宝石作为绝缘介质的晶圆,为开发低功耗芯片提供了重要的技术支撑。该成果于 2024 年 8 月 7 日在国际学术期刊《自然》发表。科研团队开发了一种创新的金属插层氧化技术,通过插层氧化的技术对单晶铝进行氧化,实现了单晶氧化铝作为介质材料,它在 1 纳米下能够实现非常低的泄漏电流 。这种人造蓝宝石介质晶圆虽然是人工合成的,但其晶体结构、介电特性、绝缘特性都跟现实生活中的宝石性能一样。科研团队已成功制备出低功耗芯片器件,续航能力和运行效率得到大幅提升,这一成果不仅对智能手机的电池续航具有重要意义,还为人工智能、物联网等领域的低功耗芯片发展提供了有力支持 。
“光学硅” 芯片材料:光与电的融合随着全球集成电路产业发展进入 “后摩尔时代”,集成电路芯片性能提升的难度和成本越来越高,人们迫切需要寻找新的技术方案。以硅光技术和薄膜铌酸锂光子技术为代表的集成光电技术是应对此瓶颈问题的颠覆性技术 。
其中,铌酸锂有 “光学硅” 之称,因其自身机械性能稳定、易加工、耐高温、抗腐蚀、原材料来源丰富、价格低廉、易生长成大晶体的优点,被广泛应用于高性能滤波器、电光器件、全息存储、3D 全息显示、非线性光学器件、光量子通信等领域,哈佛大学等国外研究机构甚至提出了仿照 “硅谷” 模式来建设新一代 “铌酸锂谷” 的方案 。
中国科学院上海微系统与信息技术研究所研究员欧欣团队与瑞士洛桑联邦理工学院 Tobias Kippenberg 团队另辟蹊径,选择可批量制造的钽酸锂薄膜作为研究对象。他们研究证明,与铌酸锂类似,单晶钽酸锂薄膜同样具有优异的电光转换特性,且在双折射、透明窗口范围、抗光折变、频率梳产生等方面相比铌酸锂更具优势 。此外,硅基钽酸锂异质晶圆(LTOI)的制备工艺与绝缘体上的硅(SOI)更加接近,因此钽酸锂薄膜可实现低成本和规模化制造,具有极高的应用价值 。
在这项研究中,团队基于 “万能离子刀” 异质集成技术,通过氢离子注入结合晶圆键合的方法,制备了高质量硅基钽酸锂单晶薄膜异质晶圆 。试验显示,这种钽酸锂光芯片展现出与铌酸锂薄膜接近的电光调制效率,同时,团队还基于该钽酸锂光芯片首次在 X 切型电光平台中成功产生了孤子光学频率梳,结合其电光可调谐性质,有望在激光雷达、精密测量等方面实现应用 。欧欣团队孵化的上海新硅聚合半导体有限公司已经具备薄膜钽酸锂异质晶圆量产能力,并成功攻关 8 英寸晶圆制备技术,为国产光电集成芯片和移动终端射频滤波器芯片更大规模的发展奠定了核心材料基础 。
市场现状与未来趋势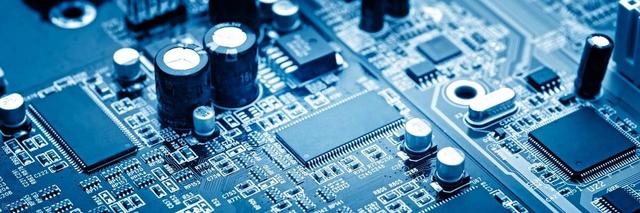
全球晶圆制造材料市场呈现出多元化且高度集中的竞争格局。在硅片领域,市场集中度极高,日本的信越化学(Shin-Etsu)和胜高(SUMCO)、中国台湾的环球晶圆(GlobalWafers)、德国的世创(Siltronic)、韩国的 LG Siltron 等五大厂商垄断了全球 90% 以上的市场份额 。信越化学凭借其先进的技术和庞大的产能,在全球硅片市场中占据着主导地位,市场份额约为 27%,其产品涵盖了多种尺寸和规格的硅片,广泛应用于各类芯片制造领域;胜高的市场份额约为 24%,同样以高品质的硅片产品和强大的研发能力著称,在高端硅片市场具有较强的竞争力 。
在光刻胶市场,尤其是高端半导体光刻胶领域,核心厂商主要来自日本、美国和韩国。东京应化(TOK)、JSR、信越化学、DuPont、富士胶片(Fujifilm)、住友化学和韩国东进世美肯等企业占据了全球约 86% 的市场份额 。其中,东京应化在半导体光刻胶领域技术领先,产品种类丰富,能够满足不同制程工艺的需求,在全球高端光刻胶市场拥有较高的市场份额;JSR 也是光刻胶领域的重要企业,其研发的光刻胶在分辨率、灵敏度等关键性能指标上表现出色,在先进制程的芯片制造中得到广泛应用 。
相比之下,我国企业在全球晶圆制造材料市场中整体处于追赶阶段,但在部分领域已取得显著进展。在硅片方面,沪硅产业是国内第一家生产出 300mm(12 寸)晶圆的厂商,打破了国外大硅片的垄断,目前在国内市场占据一定份额,并逐步向国际市场拓展;在光刻胶领域,南大光电自主研发的 ArF 光刻胶产品已成功通过客户的使用认证,标志着我国在高端光刻胶领域取得了重要突破;彤程新材(子公司北京科华微电子)、晶瑞电材、徐州博康信息化学品有限公司等企业也在光刻胶研发和生产方面不断投入,产品涵盖了 g 线、i 线、KrF 等多种类型的光刻胶,在国内市场逐步扩大份额 。
未来趋势:技术创新引领变革随着半导体技术向更先进制程迈进,晶圆制造材料在性能提升、成本降低、新型材料研发等方面呈现出一系列重要的未来发展趋势。在性能提升方面,对硅片的纯度、平整度、缺陷密度等指标要求将更加严格,以满足 7 纳米及以下制程的高精度需求。
在成本降低方面,随着技术的成熟和规模化生产的推进,晶圆制造材料的成本有望逐步降低。一方面,通过优化生产工艺,提高生产效率,减少原材料浪费,降低生产成本;另一方面,随着市场竞争的加剧,企业为了争夺市场份额,也会通过各种方式降低产品价格 。
新型材料研发将是未来晶圆制造材料发展的重要方向。随着芯片制程技术逐渐逼近物理极限,传统材料的性能难以满足进一步发展的需求,新型材料的研发成为必然趋势。除了前文提到的人造蓝宝石介质晶圆和 “光学硅” 芯片材料,还有如碳纳米管、石墨烯等新型材料也在研究之中,这些材料具有独特的物理性质,有望在未来的芯片制造中发挥重要作用。例如,碳纳米管具有优异的电学性能和机械性能,理论上可以用于制造更小尺寸、更高性能的晶体管,有望成为下一代芯片制造的关键材料 。