作为组装类生产企业的质量经理,分层级拆解最终检验项目是提升质量管控效率的关键。以下是系统化的分层拆解方法和实施建议:
### 一、 **分层级拆解逻辑**
1. **层级划分依据**
- **产品结构层级**:组件(零件)→ 模块(子装配体)→ 整机(成品)
- **过程阶段层级**:来料检验→过程检验→最终检验
- **风险优先级**:高风险(核心功能)→中风险→低风险(外观/包装)
- **管控颗粒度**:全检→抽检→免检(基于历史数据)
2. **拆解原则**
- **前移检验重心**:通过组件/模块层级的早期检验减少最终检验压力
- **防错设计**(Poka-Yoke):在装配过程中嵌入自动化检测(如传感器、视觉检测)
- **数据驱动决策**:基于SPC(统计过程控制)动态调整检验频次
---
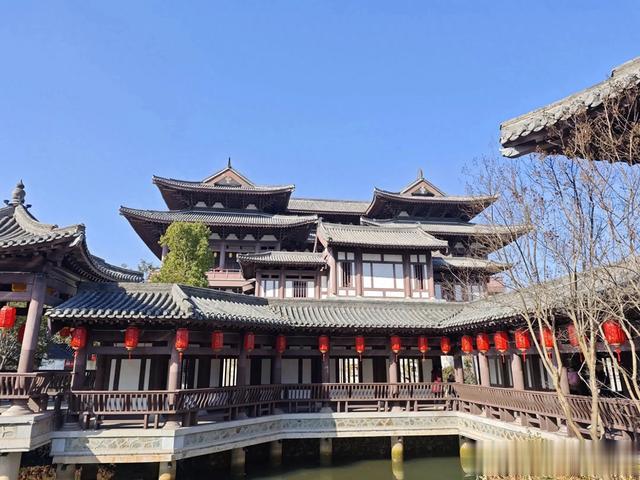
### 二、 **四层检验架构模型**
#### **第一层:组件级检验(微观层)**
- **对象**:关键零部件(如电机、电路板、轴承)
- **方法**:
- 自动化尺寸检测(如三坐标测量机CMM)
- 功能性测试(如电路通断、扭矩测试)
- 供应商质量协议(如PPAP文件审核)
- **工具**:
- 检验工装(Jig)标准化
- 电子化检验记录(与MES系统集成)
#### **第二层:模块级检验(中观层)**
- **对象**:子装配体(如传动系统、控制系统)
- **方法**:
- 模块功能测试(如空载运行、噪音检测)
- 过程能力分析(CPK≥1.33)
- 防呆验证(如错装/漏装检测)
- **工具**:
- FMEA(失效模式分析)识别高风险工序
- 红箱测试(模拟极端工况)
#### **第三层:整机级检验(宏观层)**
- **对象**:完整产品(如机械设备、电子产品)
- **方法**:
- 全功能测试(如负载试验、耐久性测试)
- 客户标准符合性验证(如安规认证、EMC测试)
- 包装与标签防错(二维码追溯系统)
- **工具**:
- OQA(出货质量保证)抽样方案(AQL标准)
- 虚拟现实(VR)模拟用户场景测试
#### **第四层:系统级管控(战略层)**
- **对象**:全流程质量体系
- **方法**:
- 质量成本分析(COPQ,劣质成本优化)
- 跨部门质量联动(SQE+PE+ME协同)
- 大数据预警(如AI预测关键参数偏移)
- **工具**:
- QMS(质量管理系统)集成IoT数据
- 8D报告闭环管理
---

### 三、 **效率提升策略**
1. **检验资源优化**
- **自动化替代**:将重复性检验(如螺丝扭力)替换为智能电批+数据采集
- **检验分级**:对低风险项目(如外观)采用AI视觉抽检,释放人力投入高风险检验
2. **数据流整合**
- 建立质量数据湖(Data Lake),打通ERP-MES-QMS系统
- 实时监控CTQ(关键质量特性)波动,触发自动预警
3. **人员能力建设**
- 分级培训体系:
- 初级检验员→标准作业指导书(SOP)执行
- 高级工程师→SPC分析、GR&R(量具重复性与再现性)评估
4. **持续改进机制**
- 每月质量回顾会:TOP 3问题PDCA循环
- 客户投诉反向追溯(从最终检验倒查过程漏洞)
---
### 四、 **实施路径示例**
**阶段1:基线评估**
- 绘制当前检验流程图,识别冗余环节(如重复检验点)
- 通过PFMEA确定高失效风险项,重新分配检验资源
**阶段2:试点运行**
- 选择一条产线试行模块化检验,对比缺陷逃逸率(Defect Escape Rate)
**阶段3:全面推广**
- 制定分层检验手册,明确各层级输入/输出标准
- 部署数字化看板(Andon系统)实现异常实时响应
**阶段4:持续迭代**
- 每季度更新检验标准(基于客户反馈和制程能力变化)
- 引入机器学习预测潜在质量风险(如关联物料批次与故障模式)
---
### 五、 **关键绩效指标(KPI)**
- 缺陷逃逸率降低30%
- 检验周期时间缩短20%
- 质量成本占比下降15%
- 客户退货率(PPM)达标率提升至99.5%
通过以上结构化分层,企业可构建从微观到宏观的全链路质量防护网,实现检验效率与管控精度的双重提升。