在电池产业链当前激烈的竞争环境下,电池PACK市场已经迎来新阶段。
动力电池领域,过去电芯厂与PACK厂紧密相连,随着汽车品牌开始自研电池,PACK环节也成为了车企和电池企业共同瞄准的板块。
不过汽车电池包PACK看似简单,其实并非如此,因为电芯材料、电池型号、电池集成方案等均会影响到电池包性能,电池厂的PACK依旧采用CMP和CTP两种方式,通过标准化模组或简化模组设计平衡生产效率与成本,但随着车企涌入PACK环节,多种新型的集成方案也随之出现,向着多样化趋势发展,例如比亚迪/小米/吉利CTB方案、零跑/小鹏的CMP方案、零跑MTC/CTC方案等。
储能电池领域,储能企业PACK也因为市场环境变化迎来革新,比亚迪通过刀片电池+魔方储能系统不断优化内部结构,海辰储能也推出∞PACK+全场景大容量储能平台,将PACK直接上升到“集装箱”规模。
随着电池型号的逐渐统一,当圆柱电池主流市场被18系/26系/32系/46系分割后,PACK环节也会迎来“模块化”和“标准化”。
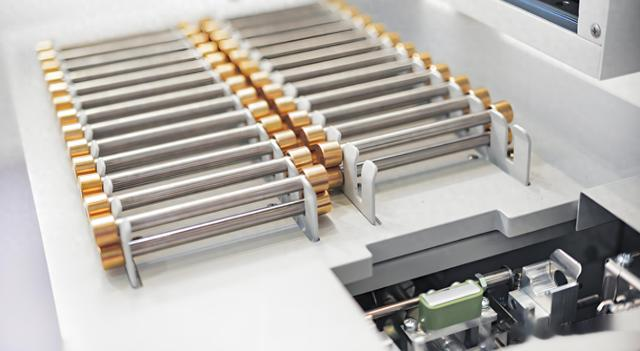
锂电池pack标准化与模块化的难点主要包括以下几个方面:
1.不同客户的定制化需求:需要根据不同车型和应用场景进行高度定制化的生产,产线的灵活性和可扩展性对于设备环节是较大考验。
2.电池型号差异:生产过程中原材料和工艺的选择路径不同,会导致同一批次的电池性能也会不同,精确筛选出性能相近的电池进行组装是一项考验技术的挑战。
3.焊接技术:焊接是连接电芯与电路的关键步骤,焊接过程中所产生的偏差可能导致虚焊、假焊或焊接过度的问题,继而从单体电芯扩展至整个电池包。
4.BMS集成与调试:BMS(电池管理系统)在电池包中责任重大,肩负着检测与管理电池组充放电过程,其设计和集成需要高精度的传感器和复杂的数据采集电路,算法则需要动态调整,在PACK厂调教过程中需要格外注意。
5.电池包检测环节:检测环节需要全方位精细观察,包含外观、电性能、安全性能等各个方面。但依旧有少量缺陷如电芯内部轻微短路,早期容量衰减等问题难以发现。
所以,当电芯型号趋于统一,工艺与能量密度趋于统一时,PACK的模块化与标准化将不再是梦想。
模块化与标准化设计优势在于可复用标准模块,并进行模块预制和预调试等措施,将大大缩短交付周期,还可降低重复开发成本,使得维护和升级更加便捷,技术人员更容易把控其中的关键点,让良率得以提升。
为此多家设备企业正朝着该方向进行不懈努力,起点锂电获悉,科迈罗身先士卒,在电池PACK标准化与模块化领域取得了长足进展。
科迈罗光电在圆柱电池、方壳电池PACK线,铝壳试验线、大圆柱实验线方面布局深厚,熟悉方形电池、圆柱电池、软包电池工艺流程,精通各工序的激光焊接工艺和技术要求,能够给客户提供合理的方案和可实施性建议。与锂电行业上市主体企业保持良好的合作关系,如多氟多、中兴派能、比亚迪、正威国际、兴储世纪、鹏辉、欣旺达、南都电池、蜂巢能源、福建巨电、雄韬等。
科迈罗助力圆柱电池模块化设计在2月28日起点锂电圆柱电池技术论坛暨圆柱电池20强排行榜发布会现场,科迈罗光电 产品经理 李海针对PACK标准化模块设计进行了深入解读。
李海认为,除了新能源汽车和储能,两轮车的发展也会促进电池PACK技术进步,随着电动车需求数量的不断增加,电池的需求也日益增长,将直接带动PACK自动生产线的需求增加。
目前科迈罗在PACK线标准模块化的优势有以下几点:
1.缩短交付周期。传统产线定制交付周期长达4-5个月,采用模块化设计:通过复用标准模块,模块预制,预调试等可将交付周期压缩至2个月,甚至更短。
2.降低综合成本,采用标准模块设计。降低重复开发成本,以及批量采购可节约成本(20%-30%)。
3.质量与效率可控。标准模块经过量产验证,工艺成熟,稳定性高,技术人员对设备关键点,风险点更容易把控,良品率提升至99.9%以上。
4.灵活调整产线。可跟据工艺需求,柔性调节,扩展模块,避免因技术迭代或需求变化导致的产线废弃风险。
但理论变成实践需要一些规划,起点锂电也在李海的演讲中总结了标准化实施的具体方法:
1.将Pack线拆解为标准功能单元(如电芯上料、分选配组、排序、电芯入装支架、极性检查、焊接、物流、MES等),定义每个模块的输入/输出接口、性能参数和兼容性要求。
2.开发通用模块形成基于模块的开发平台。提供一个简单易用、高效率、高质量、易扩展的模块库,“像搭积木一样组合产线”。
3.人员培训流程化,设备关键技术要点与实践获得的经验书面化,记录在标准文件中,以帮助企业积累技术经验,避免因人员的流动而使经验、技术流失。标准化作业文件同时可作为新手学习的文档,使技术人员经过短期培训,快速掌握关键技术要点与工作流程。
由于不同的电池尺寸将会对PACK设备进行较大改动,所以能适应各种电池尺寸的的柔性化设计也是未来PACK设备的发力重点,为此李海针对柔性化也做出了相应解答。
首先是可调节性,Pack线应具备高度的可调节能力。在生产不同规格的产品时,设备的参数能够快速调整。例如,电芯间距、极性排列可以通过可编程的控制系统,根据参数设置完成自动调整。
其次是模块组合扩展灵活,例如柔性布局设计,采用“U型布局”或“直线式布局”,通过输送线连接模块接口,还可以根据生产需求灵活组合不同的功能模块,如果增加新的生产工艺,只需添加相应的模块即可,不需要对整个Pack线进行大规模改造,加之标准化物流接口实现模块间无缝衔接,可减少物料搬运时间30%以上。
标准化和柔性化作为未来趋势,也意味着大部分采取老方法的设备厂需要更换新设备,在追求效率的环境下,如何快速交付设备并投产,也是值得关注的重点。
为此李海也给出了相应的解决方案。
在为客户定制PACK线时需要进行前期规划与设计,在Pack线的规划和设计阶段,需要充分考虑客户的工艺需求和生产流程,采用并行工程的方法,使设计、采购、制造等环节协同进行,缩短项目的整体周期。
并且设备厂商需要自身优化,与上游客户建立紧密的合作关系,确零部件保质保量的及时供应。同时,优化库存管理,减少因物料短缺导致的生产延误。
最后需要制定高效安装调试方案,在工厂内完成模块预组装和功能测试。并且在交付前充分的功能调试,可以提前发现80%以上的潜在问题。确保Pack线到达客户现场后能够快速完成安装,调试,投入生产。