今年以来,固态电池相关概念股股价水涨船高,其背后固然有资本炒作的成分,但更为重要的是,固态电池产业进程明显提速。
但多位行业内技术大牛对此持保守态度,例如曾毓群表示:“用数字1到9表示成熟度,当前行业最高水平只到了4左右,处于器件样品实验验证阶段。”
这也意味着,固态电池距离大规模产业化还有很长的路要走,因为欧阳明高院士和比亚迪孙华军也没有松口说固态电池何时能大规模量产。
曾毓群认为,研发全固态电池的关键在于对材料和化学体系,其中最难的就是固固界面问题。
全固态电池量产第一大难点:固固界面接触难题由于取消了电解液,固态电池的电解质与界面是直接的固体接触,而固液接触是以浸润形式充分贴合,固体界面接触则很难充分贴合,因为面积小导致界面接触阻抗高,锂离子通道减少和应力堆积问题显现。
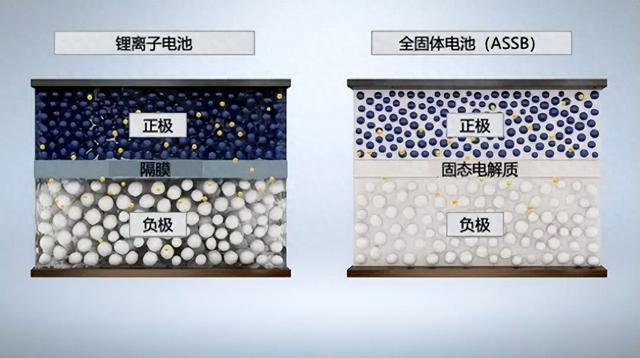
电解液和电极的化学性质不同,导致相互接触后可能会发生化学反应,这在金属锂负极和电解质界面尤为常见。电池充放电过程中,锂离子在负极表面不均匀沉积会形成锂枝晶,随着充放电过程的循环进行,锂枝晶逐渐延伸刺破隔膜导致电池的短路,带来严重的安全隐患。
界面抗阻问题也是固固界面一个需要攻克的点,锂金属负极体积变化和正极颗粒破碎,会导致界面空隙和裂纹形成,阻碍锂离子传输,界面空隙类似气泡,受电流密度和容量影响,逐步扩展成裂纹,形成多孔结构。
研究表明,施加大于等于12 MPa的叠压压力可抑制空隙生成,稳定界面,但过高压力可能引发短路风险。
所以需要无压力对界面孔隙生成进行阻止,优化策略包括高弹性聚合物缓解应力、缓冲层改善接触、表面改性提升锂离子传输,因此优化界面结构并控制叠压压力是提升固态电池稳定性的关键。
当前,改善材料和电池制备工艺,提高界面接触面积是攻克固固界面的重点,例如直接将固态电解质浇筑在正极材料上,得到优异的固-固界面,以及提升电极表面平整度和结晶性等。
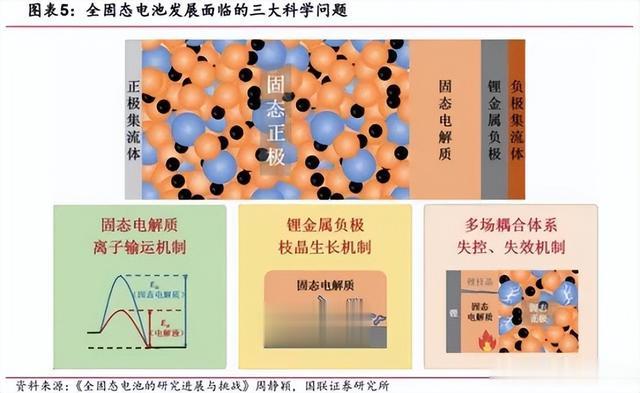
但难点是,全固态电池技术成熟度低,高效的工艺技术路线和固态电池工艺装备都有待于进一步开发。
相关研究表明,锂枝晶从固固界面生长出来,是固态锂金属电池的核心问题,所以需要借助合适的界面修饰技术及其表征、模拟技术,利用分子层(MLD)/原子层(ALD)的沉积技术构筑柔性的改性界面,来提升正极与固体电解质界面的稳定性与电导率,还有一种方式是采用外加动态压力系统,来适应电池内部应力变化,提升循环稳定性。
目前,对于该固-固界面优化研究已取得了明显进步,但依旧有许多关键问题需要解决,例如:正极材料与固态电解质界面润湿性;正极材料中的活性物质比例偏低;缺乏对界面层成分和界面相容性的研究等。
相关企业布局进展,界面问题道阻且长尽管多家电池企业均宣布在全固态电池的研发上取得重大突破,但真正详细披露界面问题解决方案的只有以下几家公司:
01南都电源
南都电源在RE+美国国际太阳能展览会展示了全固态电池产品,主打氧化物电解质技术路线,
氧化物在生产工艺、制造成本、电化学性能等方面较为均衡,但存在材料脆性大、界面电阻高的短板,成为全固态电池产业化进程的壁垒。
为此南都电源在固态电解质中引入增韧材料,增强固态电解质机械强度,降低发生内短路可能性。通过电解质三明治结构设计以及电极表面原位成膜技术,改善界面接触性能,降低电芯内阻。
除此之外,南都电源开发的致密电极干法工艺,有效降低电极孔隙率,致密度达80%,保证了电极活性材料与电解质间的紧密接触。
02当升科技
当升科技投资者互动平台表示,已系统布局氧化物、硫化物等固态电解质和双相复合正极材料路线,其双相复合正极材料搭配电解质产品,解决了正极与电解质固固界面难题。
双相复合固态锂电正极材料是由传统锂电池正极材料和固态电解质材料复合而成的电池材料,由锂电池正极材料、固态电解质材料、导电剂组成。
其中,正极材料负责储存和释放锂离子,固态电解质负责离子传输和隔离,导电剂则起到电子传导的作用。
双相复合固态锂电正极材料的性能优势有以下两种:
1.高能量密度:复合两种材料充分发挥各自优势,使电池在相同体积或重量下能储存更多电能。
2.长循环寿命:双相复合材料优化电极与电解质的固固界面,降低阻抗,提高循环寿命和放电性能。
03中科固能
中科固能吴凡表示,中科固能面临的主要挑战是如何克服锂金属与硫化物电解质之间的界面问题,为此团队对锂金属表面进行界面保护层处理,选择软碳材料作为负极核心,在软碳材料中引入氮化锂,成功实现了锂金属界面保护。
软碳材料具有较高的层间颗粒和孔隙率,吸引锂离子并引导其在氮化锂颗粒周围沉积形成原子层,提升了电池的电化学性能。吴凡还指出,通过软碳氮化锂的界面保护层,团队成功抑制了锂枝晶的生成,极大提升了电池的循环稳定性。
不仅如此,团队还开发出软碳与氮化硅的复合界面保护层,氮化硅在沉积过程中会与锂金属形成锂硅合金,锂硅合金和软碳复合以后,可以显著提升硅材料本身在固态电池中的电化学性能和循环性能。
04宁德时代
据吴凯介绍,针对正极的界面问题,宁德时代研发了单晶正极多层级全包覆技术,第一层无机氧化物包覆层可以抑制界面副反应,第二层固体电解质包覆层,提升界面离子扩散。多层设计可提升界面结构稳定性,还研发了多功能复合粘结剂,帮助稳定极片导电网络。
05长安汽车&太蓝新能源
太蓝新能源自身有研发出高性能氧化物-聚合物混合固态电解质,通过优化离子导电性和机械强度,降低界面阻抗并抑制锂枝晶生长,并引入柔性聚合物涂层包覆电极/电解质界面,缓解循环过程中的体积膨胀应力,提升界面稳定性。
除此之外,太蓝新能源还和长安汽车联合研发出无隔膜技术,采用极片复合固态电解质层替代传统隔膜,直接集成固态电解质于电极表面,简化界面结构并提升安全性。
除了以上公司,以下科研机构也针对固固界面问题发表研究成果。
首先是华中科技大学黄云辉教授和同济大学罗巍教授,二人采用超声成像技术对固态软包电池进行研究,得益于超声波高灵敏度,原位超声成像可有效探测软包电池在长期循环过程中内部的气体释放和界面降解。跟踪正极界面处逐渐氧化的过程,可以很好地区分增加的界面电阻是接触损失还是钝化层生长。
其次是上海交通大学张希教授团队,张希教授团队提出了一系列适用于全固态电池体系负极固固界面改善策略,具体包括三个方面:
1.多层固态电解质:提出设计多层固态电解质结构,同时承受负极还原反应和正极氧化反应。垂直异质结构设计为界面工程研究提供参考。
2.嵌入SEI中间层:在锂负极与固态电解质之间嵌入SEI中间层,采用具有优异离子和电子输运性能的三维多孔支架材料。
3.高容量锂合金负极:相比于金属锂负极,锂合金负极在固态电解质中的稳定性更高,可将Li-Si合金作为全固态电池负极的有效候选者。
最后是哈尔滨工业大学王家钧教授团队,该团队提出自上而下设计法,通过降低富镍阴极材料的内应力变化,使固固界面得以更好地接触。
为此研究人员开发了一种功能性Al/Zr修饰的单晶LiNi0.8Mn0.1Co0.1O2阴极,能在高压下表现出优异的机械相容性和快速的离子/电子传输。这种设计思想可以克服固态电池在低外部压力下的缺陷,还可以有效解决电极应力累积问题,有助于改善固固界面、创造出快速离子通道。
起点固态电池经过总结认为,固固界面突破需要从以下几点做起:
1,界面材料的优化,用体积变化更小的锂金属负极搭配包覆复合正极材料(如高镍三元正极),减少体积膨胀效应,维持界面稳定。
2,开发超薄固态电解质层,厚度控制在微米级,提升界面润湿性及离子导通效率。
3,界面压力优化,在电芯制造过程中施加更高压力,消除电极与电解质层间的孔隙,强制实现面接触。
4,固态电解质层替代传统隔膜集成于电极表面简化界面结构。
退而求其次瞄准半/准固态过渡方案完全解决固固界面问题还需要时间,为了快速量产,半固态/准固态电池依旧是最佳解决方案。
全固态电池相比,半/准固态电池仍保留少量电解质,目前的加注比例约10%,可逐渐降低至5%以下,值得一提的是半/准固态电池也可采用高镍正极和硅碳负极,提升能量密度。
当前环境下,市场选择与技术进步各退一步,半固态电池过渡至准固态乃至全固态依旧是最为稳妥的方案,这一点在新兴的固态电池企业中不乏支持者。
例如根据清陶能源规划,量产半固态过程中可实现全固态工艺成熟化、设备稳定运行,以及关键材料的量产。
该公司在生产第一代半固态电池的产线上就有诸多全固态相关的设备和技术投入运行,随着生产经验变多,全固态电池的制造痛点被逐渐摸清,就可找到过渡路线。
卫蓝新能源也如出一辙,从半固态电池上车逐渐摸索,公司创始人俞会根称卫蓝新能源搭载于蔚来,对于公司在半固态电池领域从0到1的过程中起到了关键作用。该公司的原位固化技术,通过液态聚合物前驱体或熔融锂金属渗透并固化,提高界面接触。低熔点锂金属使固固界面转变为兼容的液-固界面,促进锂离子跨界面迁移。
软包电池为主的孚能科技则表示,针对市场需求来看,半固态电池可以满足当前的需要,其工艺设备与液态电池差别较小,可沿用并逐渐进行过渡,达到全固态标准。
头部企业宁德时代也半固态电池表示支持,认为半固态电池是液态锂电池向全固态电池的过渡方案,但现有半固态技术尚未完全发挥固态电解质的潜力。
其余的二线电池厂尽管没有过多表示,但基本用行动证明该方案可行,有图表为例。
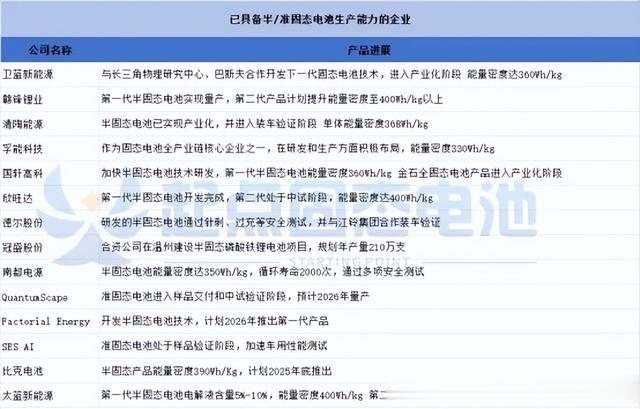
但行业对于半固态电池安全性和市场定位存在诸多怀疑,因为只要有电解液即会有安全风险,因此虽然添加少量电解液能解决固固界面问题,但半固态电池依旧不是大家理想中的固态电池,且价格偏高,十分鸡肋。
既要实现固固界面通畅,又不能使用电解液,这一矛盾点让固态电池成为一个难以解开的节,并且还将长期持续,制约着产业发展。
更值得注意的是,此前在实验室阶段,行业内普遍认为半固态电池与全固态电池存在能量密度的差异,例如半固态电池能量密度普遍在275-350Wh/kg,全固态电池能量密度则达到400Wh/kg以上,但从以上表格的产品参数来看,二者相差并不会太多。
写在最后固固界面还有很多问题悬而未决,全固体电池短时间内走不出实验室。
除了界面问题外,生产工艺、成本和质量管控也是不小的难题。
全固态电池诞生时间并不短,但一直没有大规模流行,原因就是生产成本和技术痛点,起点固态电池认为商业原因大于技术原因,制造全固态电池,大部分的锂电生产设备和工艺环节都需要改造,基本相当于重新建立。
大规模替换设备对于任何锂电池企业来说都是一笔重大开销,重新建立生产线打造的全固态电池成本不会低,加之集成难度、开发难度、技术能力,一步登天是难上加难。
因此起点固态电池赞同欧阳明高院士的看法,固态电池需要逐一解决痛点,而不是一口吃成胖子,产业化需要循序渐进。
另外,材料的成本以及选择,都将决定固固界面的成功与否,如果两种材料互相排斥产能化学反应,就需要更复杂的技术手段来稳定化学性质。
固态电解质本身也有很大问题需要克服,例如轻薄化难度较大,部分稀有金属原材料价格较高,例如氧化物电解质里面的锆元素、硫化物电解质里面的锗元素等。
这并不仅仅是中国企业的难题,更是全世界的难题,例如丰田一再跳票、QuantumScape研发受阻等,均说明该电池技术难度超群。
保留少量的液态电解质是目前唯一的方式,半固态电池随着放量增多,价格会逐渐平稳,准固态电池也会逐渐走向成熟。
技术的不突破,也反向刺激市场,资本环节对其失去信心,相关数据显示,2023年固态电池公司的全球风险投资是近5年来的最低值,不过2024年热度忽然回升,持续多久还是未知。
政策对于固态电池也提出了一些要求,例如《锂电池行业规范条件(2024年本)》中新增了固态电池性能要求:单体能量密度≥300Wh/kg,电池组能量密度≥260Wh/kg,循环寿命≥1000次,容量保持率≥80%。
其实,以上要求半固态电池也能做到。
半固态电池当前需要解决的不仅是技术问题,更是要获得消费者的肯定。当前在产业链的驱动以及市场驱动下,液态电池能量密度超过极限,未来储能电池将会大规模使用500Ah+的大容量电芯,半固态电池将会在新能源汽车上获得应用,其降本速度也会随着量产增多而加快。
当前,清陶/赣锋/卫蓝/孚能/南都/亿纬等企业正在不断进行努力,力求先将半固态电池用于车载,电解液、隔膜、设备相关企业也在随着下游客户的转变而进行改进,但事实是任何东西不能十全十美,半固态电池先上车、持续攻关全固态电池是大部分企业同时行走的路线,“既要又要”是人类发展的根本动力,也是会适得其反的毒药,只有不断在技术探索中进行权衡,才会有适合商业化的产品出现。