文 |许晨渊的书房
编辑 | 许晨渊的书房
可再生能源作为化石燃料的主要替代品之一,近几十年来发展迅速。2019年,可再生能源约占全球一次能源总需求的10%(国际能源署2020).由于受月球的调节,潮汐流几乎是100%可预测的,这使它成为一种可靠的可再生能源。
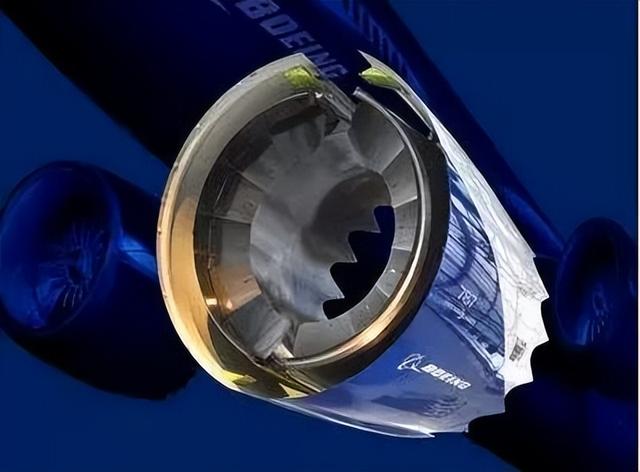
MW(OEE2020).由于潮汐涡轮机通过转子旋转将洋流转化为动能,因此潮汐涡轮机叶片的结构性能是一个关键问题。由于水的密度比空气高835倍,潮汐涡轮机叶片承受复杂的载荷。因此,关于潮汐涡轮机叶片的设计和性能验证存在重大挑战。
本文基于实验测试和数值分析,对世界上最大的潮汐涡轮机之一的1 MW潮汐涡轮机机舱的转子叶片的结构行为进行了研究。
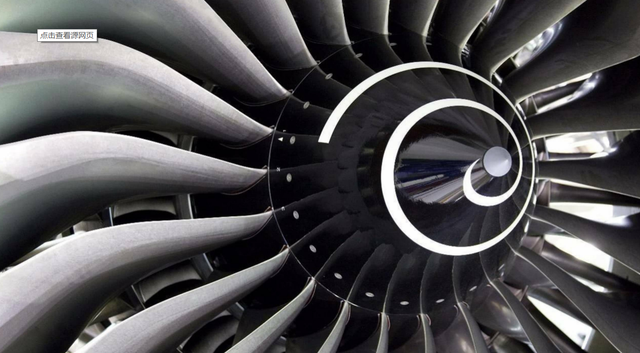
叶片材料的特性通过试片表征,并考虑到运行期间海水浸泡的影响。通过一系列的测试项目,包括固有频率测试和静态测试,获得了8m潮汐涡轮叶片的初步结构性能。
除了物理测试之外,还开发了一个有限元模型形式的数字双胞胎,用于预测叶片的结构响应。通过实验数据验证了有限元模型的准确性。通过进行考虑海水老化效应的数值分析,从刚度、失效风险和疲劳寿命方面研究了1 MW潮汐涡轮机叶片在设计载荷下的结构行为。
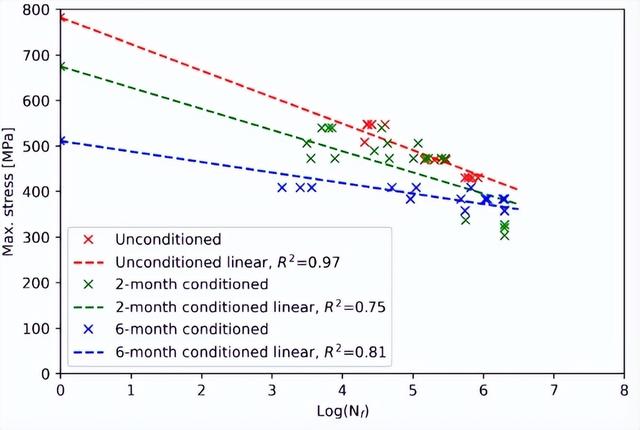
物理测试是确保潮汐涡轮机叶片在极端载荷情况下安全的有效且可靠的方法。然而,叶片通常在实验室干燥条件下进行测试,这并不代表它们工作的海洋环境。因此,不能考虑海水对叶片材料强度的影响。
刀片描述
潮汐涡轮机装置包含两个1 MW的转子机舱,每个转子机舱的转子直径为20 m。潮汐叶片由主体、后缘整流罩和叶尖组成。数字1显示了潮汐涡轮机叶片的主体。它由ireComposites使用玻璃纤维增强粉末环氧复合材料制造。
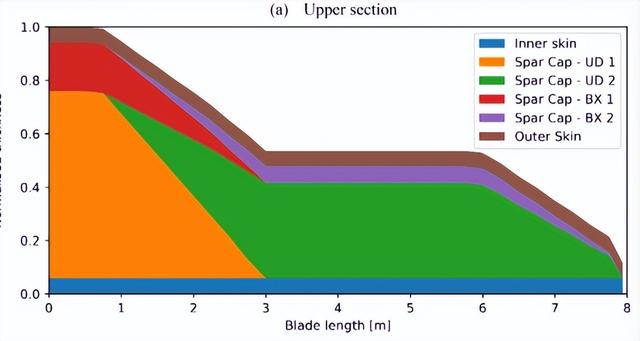
与传统的玻璃纤维增强聚合物(GFRP)相比,基于CPET制造的GFRP具有某些优势,包括较小的全厚度浸湿需求、良好的纤维体积分数控制和固化过程中的低放热。
关于原材料,与传统的环氧树脂不同,粉末环氧树脂可以在环境温度下储存,并且具有长的保存期。
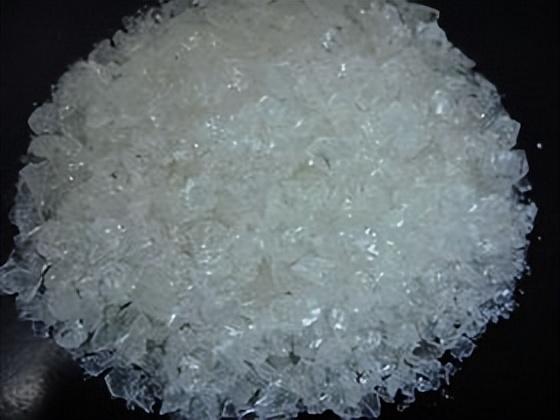
叶片后缘整流罩和叶尖将与主体分开制造。因为这两个部件是为了优化叶片的流体动力形状,所以它们被认为对抵抗主要流体动力载荷没有显著贡献。因此,后缘整流罩和翼尖不包括在性能分析中。
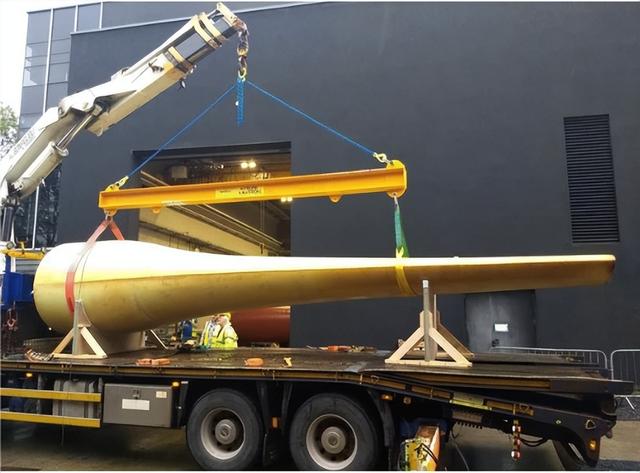
材料属性
用于制造UD层压板的织物具有0°取向的所有纤维,而BX层压板的织物具有分别在0°和90°编织的50%的纤维。TX层压板使用纤维以0°、60°和120°均匀编织的织物制成。
在这项研究中,进行了试样试验来表征这两种复合材料的材料特性。鉴于潮汐涡轮机叶片在其设计寿命期间将在海洋环境中工作,应考虑材料饱和和退化对材料性能的影响。在以下小节中,简要给出了静态拉伸和疲劳试验结果。
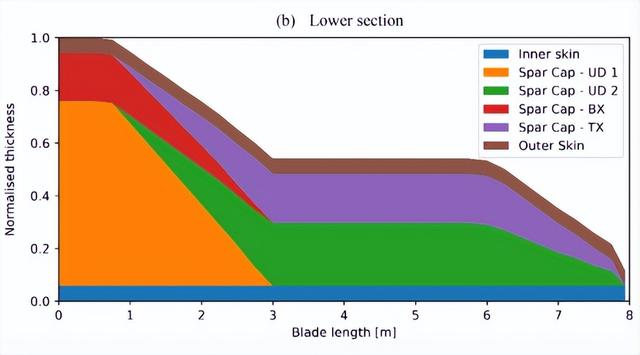
为了代表涡轮叶片的工作环境,通过在人造海水的加热箱中调节样品来进行加速老化过程。人造海水是用来自苏格兰孔雀盐的“Seamix”盐生产的。
安装在隔热木制容器中的200升聚乙烯罐用作调节罐,人造海水保持在50℃以加速试样的老化过程。
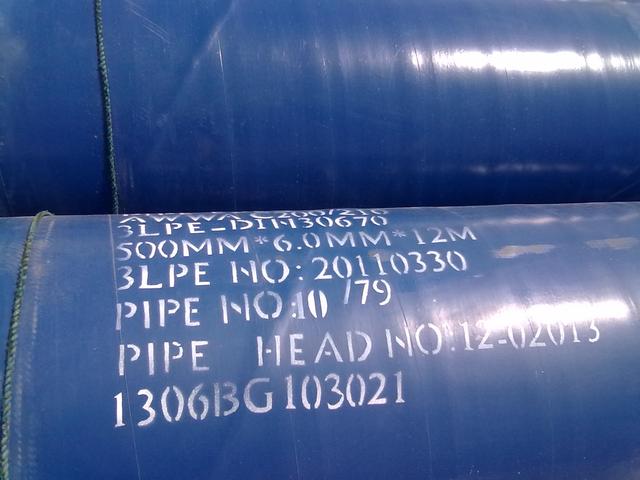
为了确保温度和盐度的均匀性,使用潜水泵以大约2000 l/h的流速对水进行连续再循环。本研究中考虑的等效运行时间为50年。这超过了潮汐涡轮机25年的典型设计寿命。因此,使用条件材料数据进行结构分析将确保结果是安全的。
测试建模
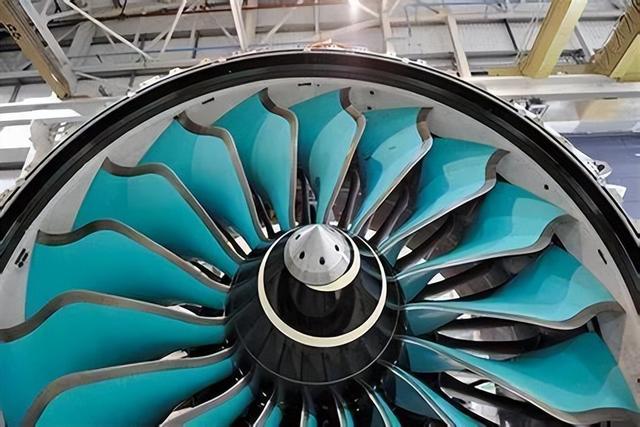
为了获得材料特性,进行了试样测试,包括以下四种类型的测试,包括测试所依据的标准:
根据制造商提供的结构细节,叶片可分为四个部分,即外蒙皮、翼梁缘条、内蒙皮和腹板,如图。3。内外蒙皮从内侧和外侧保护叶片。
两块蒙皮都由16层玻璃纤维BX板制成。翼梁缘条是用玻璃纤维UD和BX粉末环氧树脂层混合制成的。
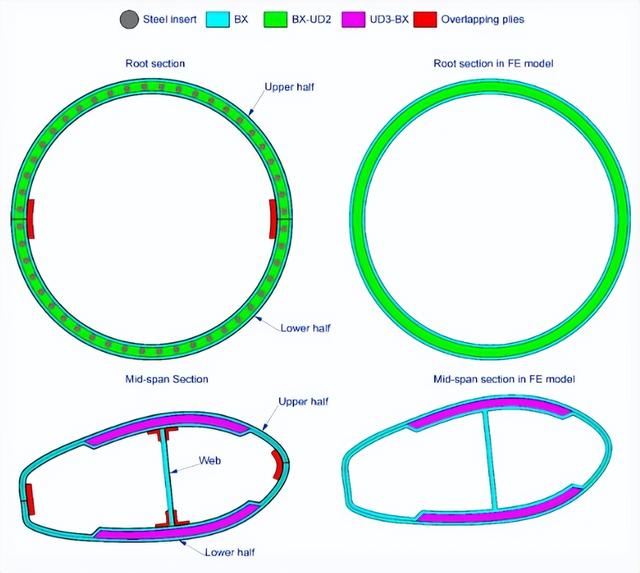
该区域与内层和外层一起形成夹层复合部件,其目的是抵抗由潮流引起的流体动力载荷。数字4显示了主梁帽的材料细节和标准化厚度。叶片根部区域是叶片最厚的部分,因为它应该承受由潮汐流产生的力矩。
根部横截面设计为圆形,并通过48钢嵌件连接至涡轮变桨轴承根部与内外蒙皮一起成为叶片最厚的部分,厚度为127毫米。叶片内部有一个腹板,从根部到叶尖大约1米。该网由80层玻璃纤维BX板制成。它连接梁帽的上下两侧,形成工字梁,增强梁帽的强度。
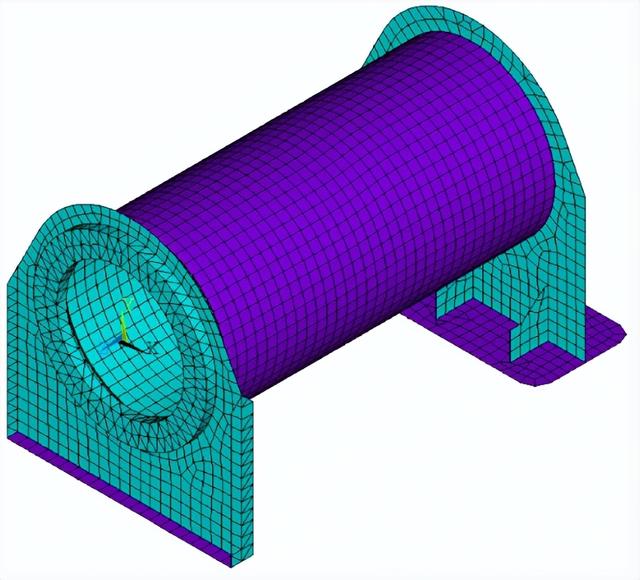
应该注意的是,仅使用GFRP材料,这种潮汐涡轮机叶片的外壳足够厚以避免局部屈曲失效。因此,与典型的风力涡轮机叶片不同,在叶片中没有使用轻质填充材料来增加壳体厚度。
二、实验测试介绍了固有频率试验、静态试验和疲劳试验。从图中可以看出。5设计并制造了一个钢支撑框架,用于在静态测试过程中支撑叶片。叶片以6°至48°的螺旋角安装在支撑框架上,其压力面朝上。支撑框架固定在钢筋混凝土反应层上。
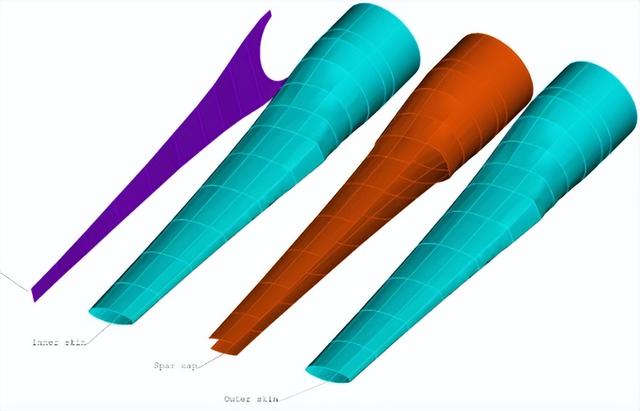
首先进行了固有频率测试,以确定叶片的动态特性。在这些试验中,分别沿压力面和前缘安装了五个和三个单轴加速度计,以记录叶片振动响应。为了激励叶片,用锤子对叶尖进行瞬时冲击。
我感兴趣的是前两种拍打方向和沿边方向的模态,以及第一种扭转模态。为了获得拍打方向和扭转方向的模态,在拍打方向施加瞬时冲击,而对于沿边模态,则施加沿边冲击。基于快速傅立叶变换(FFT)分析获得叶片的固有频率。每种测试重复三次,取平均值。
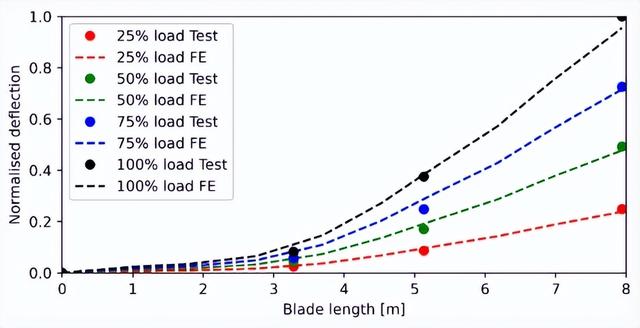
静态测试旨在确保潮汐涡轮机转子叶片能够承受由叶片设计者提供的设计载荷情况。叶片设计载荷通过使用DNV软件“潮汐叶片”进行的时间序列模拟计算得出脚注1加上1.35的负载安全系数。
模拟包括双转子操作、浮动平台、转子腿、传动系统和涡轮机控制系统的影响。叶片的最大设计载荷通常是在接近涡轮机切断波高的条件下,在额定功率(2.5米/秒当前速度)附近“正常运行”产生的。
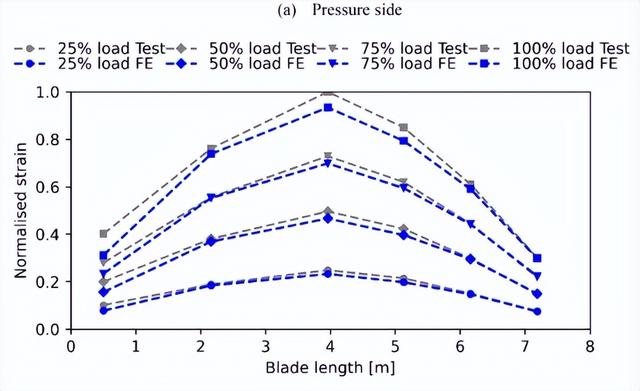
当将产生的剪切力和弯矩剖面与使用设计力所经历的剖面相匹配时,五个加载点提高了测试精度,确保准确代表潮汐载荷。接触垫使用高密度聚氨酯泡沫制造,其尺寸适合叶片表面的几何形状。
每个接触垫的面积约为3000 cm2。在测试期间,在加载区域周围没有观察到局部损坏或局部变形,证明接触垫尺寸足以分配负载。
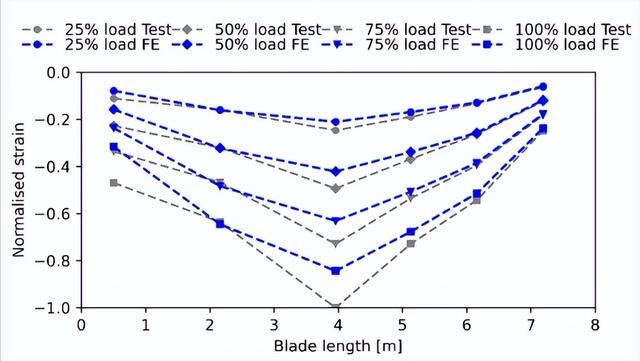
应该注意的是,在对潮汐涡轮机叶片建模时,进行了两个主要的简化。图的左边。7显示了制造叶片的横截面,而右侧显示了有限元模型的简化横截面。叶片由三部分组成,即上半部、下半部和腹板。
这是因为刀片分两个阶段制造。在第一阶段,叶片的上半部分、下半部分和腹板分别用CPET制造。在这个阶段,三种组分没有完全固化。在第二阶段,将三个组件组装在一起,并添加额外的未固化重叠层,以确保连续纤维在所有接合线之间延伸。
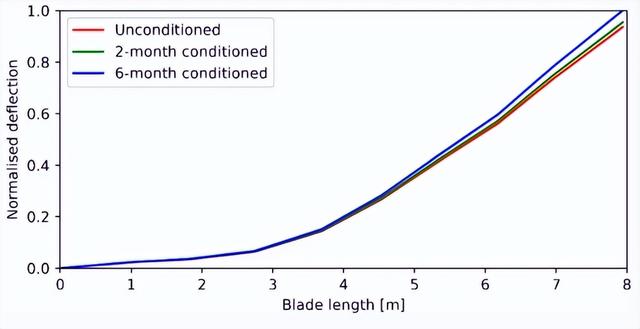
最后,整个叶片仅在高温下在真空袋下原位完全固化。因此,在粘合表面,纤维是不连续的。这种纤维的不连续性很难用壳单元来表示。
考虑到数值模型是为预测全尺寸叶片的行为而开发的,这些局部结构细节可以简化,假设在粘接界面没有观察到损坏。
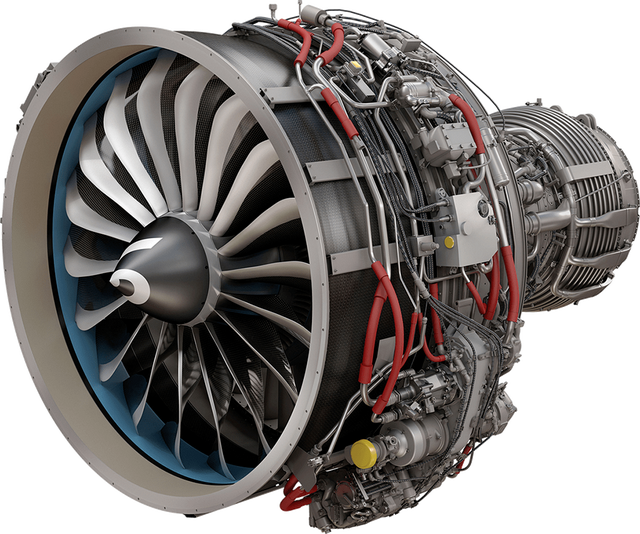
因此,这些重叠层在数字孪生中被忽略。假设纤维在叶片的不同部分是连续的,除此之外,腹板上的单元通过共享相同的节点直接连接到叶片表面的单元。第二个简化是在第一个制造阶段嵌入根部的钢嵌件上进行的。
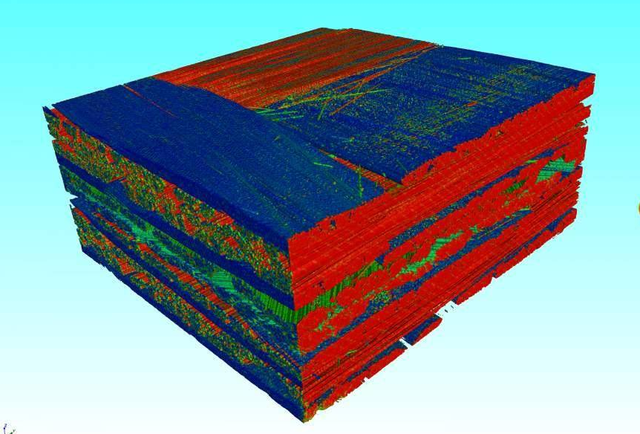
通过简化有限元模型,在忽略重叠层和钢嵌件的情况下,有限元模型预测的质量(3.82吨)低于实验值(超过4吨)。这种质量变化会影响固有频率分析的结果。此外,忽略钢嵌件也会影响根部的应力/应变分布。
从试样试验中获得的机械性能被用作有限元模型的材料输入数据。然而,应该注意的是,尽管使用了相同的制造方法,试样测试结果可能并不完全代表叶片结构的材料性能。这主要是由于试样和实际叶片之间的厚度(或层数)不同。
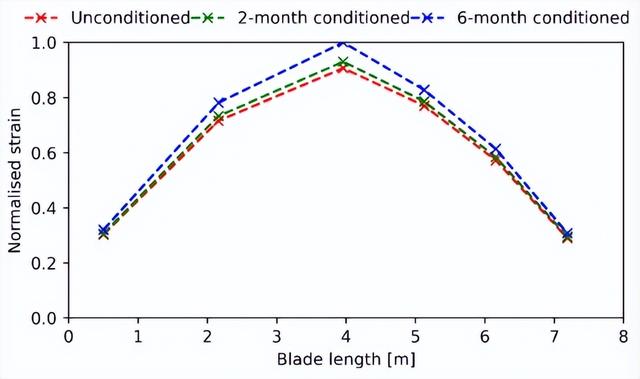
不同的厚度可能导致不同的纤维体积分数和固化状态,导致机械性能的不确定性。除此之外,其他因素,如模具形状和制造缺陷,也会影响材料的性能。
然而,受试验机能力的限制,试样厚度不能与实际叶片结构的厚度一样厚。因此,假设叶片材料的材料特性与本研究中的试样试验结果相同。
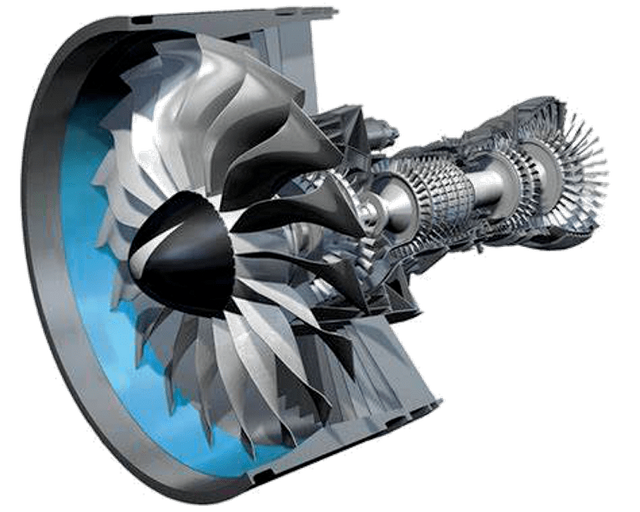
静态测试
随着八种载荷情况下载荷的增加,观察到叶片在整个静态试验中表现一致。因此,选择了四种荷载工况,即设计荷载工况的25%、50%、75%和100%进行有限元模型验证,以减少显示结果时的拥挤。
在物理测试中,在最大设计载荷(100%载荷情况)下没有观察到故障或裂纹,表明叶片具有承受设计载荷的结构完整性。在静载荷下,叶根在较大的根部力矩(5714 kN·m)作用下轻微转动。通过安装在支撑框架上的一对LVDTs的位移数据获得了根部旋转。
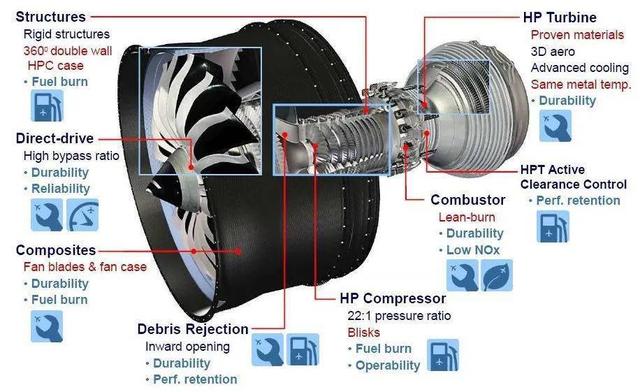
在100%负载情况下,观察到0.17°的根部旋转。考虑到叶片约8米长,这种旋转导致叶尖额外偏转约23毫米。
因此,由三个位移传感器记录的偏转值用根部旋转角度进行了修正。修正根部旋转后,在静态有限元分析中可以忽略支撑框架。
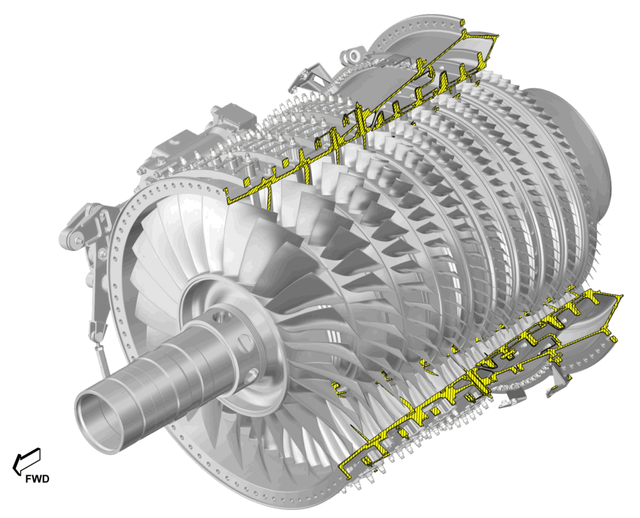
数字9总结了四种载荷情况下的叶片挠度,其中挠度根据图中的极限值进行了归一化。最大叶尖偏转约为叶片长度的1.3%,表明在极端条件下叶片不会撞击潮汐涡轮机的其他部件。
此外,考虑到潮汐力与极端载荷情况相比较小,叶片在运行期间可以保持良好的形状,确保涡轮机正常捕获能量。
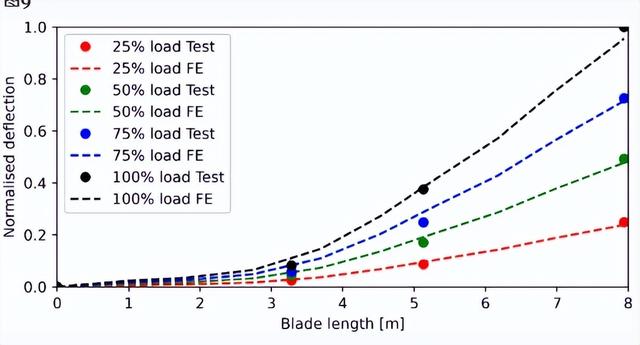
在测试载荷下,观察到压力侧和吸力侧分别承受最大的拉伸应变和压缩应变。所选四种载荷情况下沿压力侧和吸力侧的标准化纵向应变。纵向被定义为在制造过程中用于铺设复合材料的参考方向,即从根部到尖端。
在100%载荷情况下,最大绝对应变0.002出现在翼梁缘条的压力侧。涡轮机设计者提供的应变极限约为0.025,这也符合DNVGL-ST-0164(2015),说明叶片符合设计预期。由有限元分析预测的应变数据绘制成图,并与试验数据进行比较。
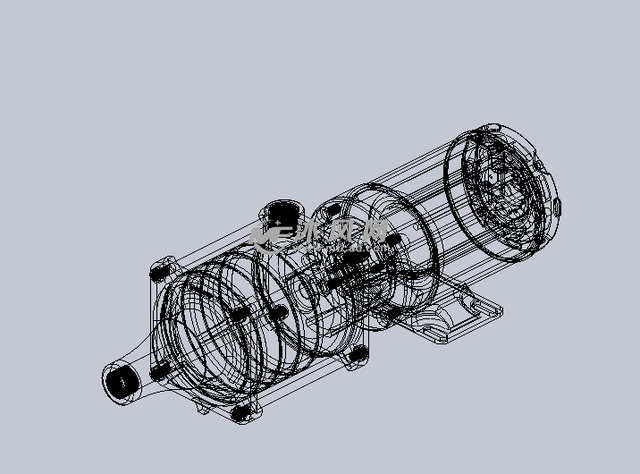
叶根周围的预测应变值低于试验结果。这与挠度比较中的观察结果相矛盾,在挠度比较中,有限元模型低估了根部区域周围叶片的刚度。
然而,考虑到应变片仅测量叶片表面单个位置的应变值,两个应变片的应变记录不能指示根部区域的应变分布。
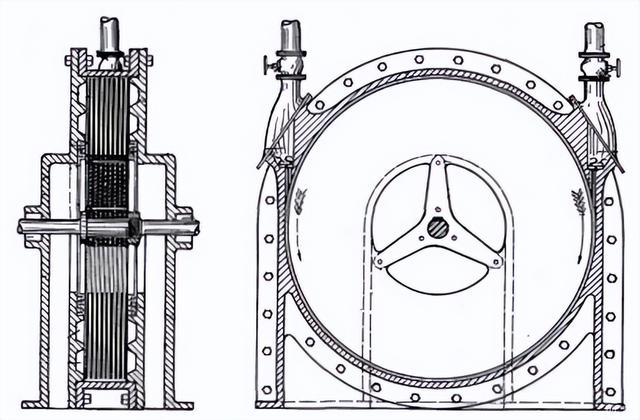
因此,很难根据测得的少量应变值确定根部区域周围的刚度是否被低估。可能导致不匹配的另一个潜在原因是生成有限元模型时所做的简化。忽略嵌入根部的钢筋,根部周围的应力和应变分布会受到影响。这表明有限元模型略微高估了叶片刚度,这与叶尖偏转比较的观察结果一致。
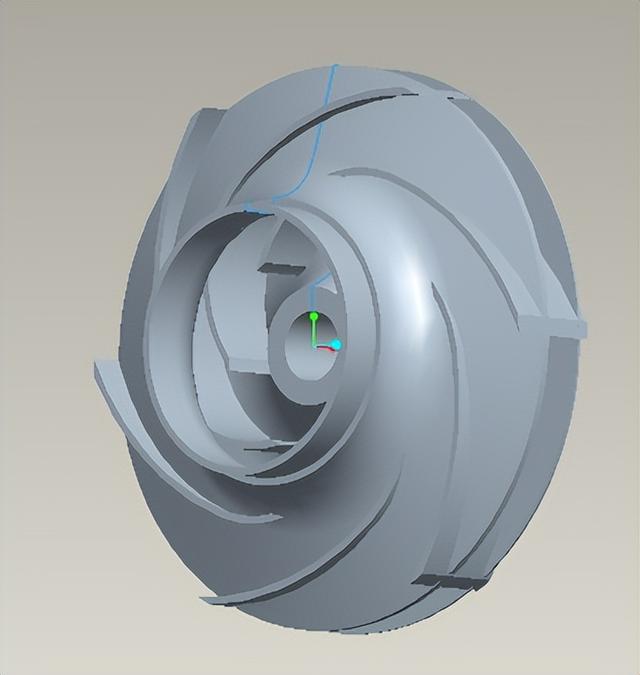
根据疲劳试验后进行的固有频率试验和剩余强度试验,没有观察到刚度退化和固有频率变化。因此,即使材料在海水冲击下耐疲劳性降低,叶片的疲劳寿命也不会受到影响。这得益于叶片的高强度,表明叶片可能是保守设计的。